By Taha KhanReviewed by Frances BriggsJul 17 2025
New monitoring technologies, such as electromagnetic sensors and high-speed X-ray diffraction, are helping to track alloy phase changes in real time. These technologies can improve heat treatment control and boost material performance across industries.
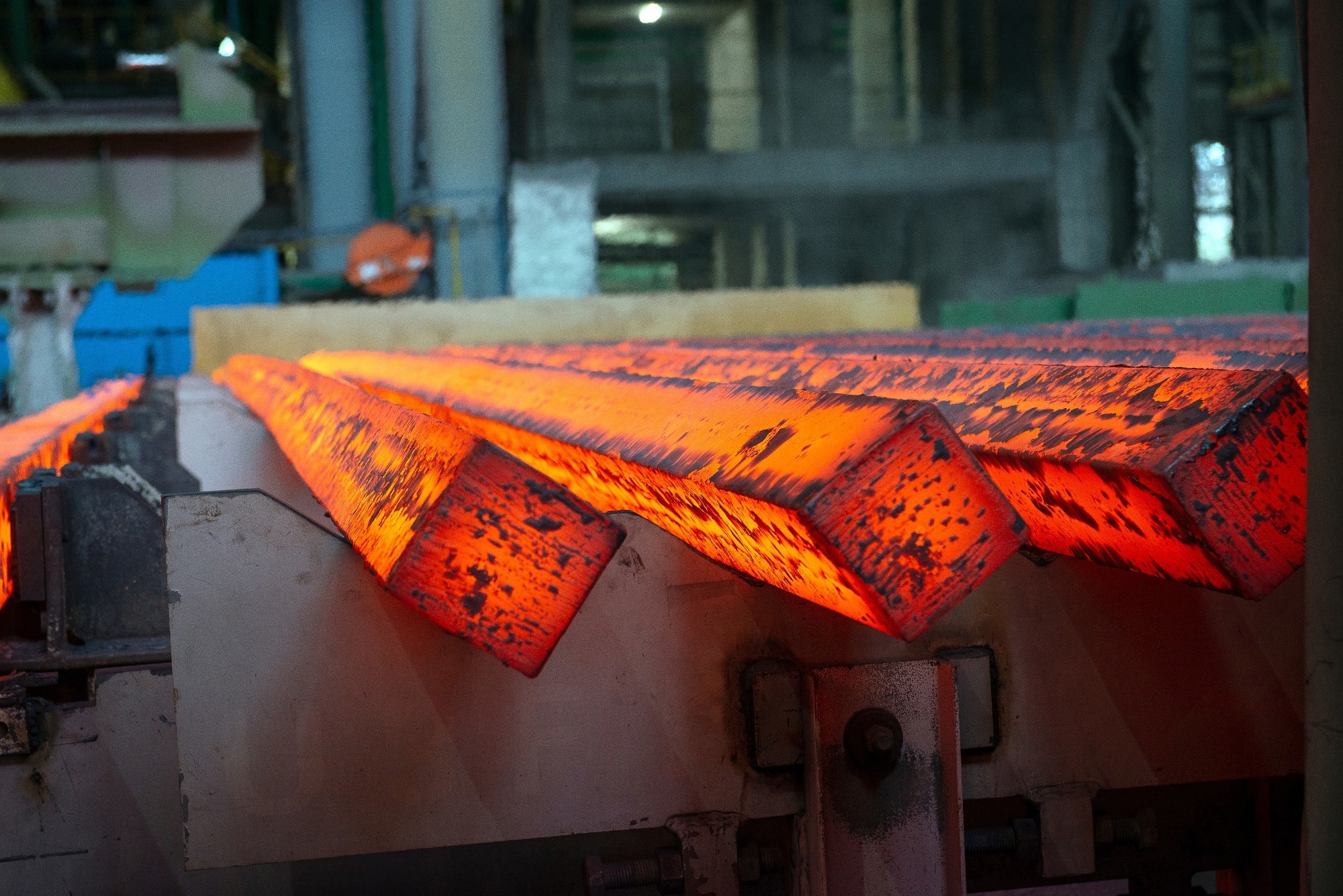
Image Credit: kaband/Shutterstock.com
Importance of Real-Time Monitoring in Heat Treatment
The toughness, ductility, and wear resistance of metallic alloys are dictated by the phases present in their microstructure and how these phases are distributed. During heat treatments such as annealing, quenching, or tempering, the microstructure can shift dramatically as phases evolve in response to temperature changes.
In steel, for instance, the austenitic phase can give way to martensite or bainite, each imparting distinct mechanical properties. If these transitions are not properly controlled, the resulting material can fail to meet performance specifications and often lead to product failure.1
Traditional post-process characterization methods are only able to provide a retrospective understanding material changes. This can lead to inefficiencies and variability in product quality.
However, real-time monitoring allows for dynamic adjustment of heat treatment parameters, ensuring that the microstructure is consistently assessed. This real-time monitoring allows engineers to detect the exact onset and completion of phase transitions, enabling adjustments mid-process to ensure optimal outcomes.
Advanced In-Line Monitoring Techniques
Electromagnetic Sensors
Electromagnetic sensors can pick up subtle shifts in the electrical and magnetic properties of alloys, which serve as indicators of phase transformations. In steel, for example, the process of austenitization or the formation of martensite alters both magnetic permeability and electrical resistivity.
Electromagnetic sensors can measure these changes in real-time during heat treatment, providing rapid, non-destructive indications of phase changes, enabling immediate process control.2
High-Speed X-Ray Diffraction (XRD)
Advanced high-speed X-ray diffraction techniques use synchrotron radiation to offer high resolution and sensitivity, detecting atomic-scale structural changes in real-time. These techniques capture diffraction patterns that reveal phase composition, lattice parameters, and strain states during heating and cooling cycles. 3
Case Studies
Dilatometry and Acoustic Emission Monitoring in Ti-6Al-4V Alloy
A 2024 study paired a modified dilatometer with acoustic emission (AE) sensors to monitor phase changes in the titanium alloy Ti-6Al-4V during heating. The dilatometer pinpointed the onset and completion of transformations across a range of heating rates, while the AE sensors picked up real-time acoustic signals confirming these changes, all without causing any damage to the material.
The results showed that the α to β phase transformation began above 900 °C, with AE signal frequencies matching each stage of the process. This technique provides a practical way to monitor phase changes continuously during industrial heat treatments, helping to fine-tune thermal cycles for aerospace-grade titanium alloys. 4
EBSD-Based Analysis of High-Entropy Alloys During Heat Treatment
A 2022 case study took a closer look at AlMo0.5NbTa0.5TiZr refractory high-entropy alloys under heat treatment. Using electron backscatter diffraction (EBSD), researchers tracked phase decomposition and transformation kinetics in real time, capturing subtle shifts as Zr-rich and Ti-rich regions emerged and evolved within the microstructure, a process that unfolded differently across heating regimes. These new phases hardened the alloy.
The EBSD technique enabled the quantification of phase fractions and provided a comprehensive mechanism for phase decomposition. This study highlighted the importance of precise control of microstructures in industrial applications. 5
In Situ Scanning Electron Microscopy (SEM) with EBSD and Secondary Electron Imaging
High-temperature in situ SEM combined with EBSD enables direct observation of microstructural changes and phase transformations in real-time during heat treatment. Another 2022 study used a novel heat stage within a Zeiss SEM to observe phase changes in iron alloys at temperatures up to 800 °C.
Their method combined secondary electron imaging with EBSD for real-time visualization of grain and phase transformations during commercial heat treatment. This allowed over 100 different grains to be tracked and identified as the carbon steel samples transformed from ferrite/pearlite to austenite.6
In Situ Synchrotron X-ray Diffraction (SXRD) for Continuous Cooling Transformation (CCT) Monitoring
A further project monitored CCT data in situ for 40 steel samples using time-resolved SXRD during real heat treatments. Six steel grades from three suppliers were tested, with the SXRD data allowing for real-time monitoring of ferrite, martensite, and precipitate phase evolution.
The high-frequency detector enabled tracking of volume fraction changes and carbon diffusion by analyzing peak shifts in the fcc and bcc phases. The results were used to validate and improve machine learning models for simulating CCT data, enhancing predictive accuracy, and process optimization. 7
Benefits and Future Directions
Building real-time monitoring into alloy heat treatment workflows offers clear advantages. Operators can adjust heating or cooling parameters on the fly to fine-tune the phase composition and achieve desired microstructures.
This live feedback cuts batch-to-batch variability and helps ensure the final properties meet strict design criteria. It also enables quick detection of process deviations, allowing immediate corrections and reducing material scrap.
Looking ahead, combining real-time monitoring with artificial intelligence and machine learning could make predictive control of phase transformations and fully automated heat treatment a reality.
Extending these approaches to a wider range of alloys and complex processes, including additive manufacturing, will provide even greater precision in material design and production.
References
- Mathews, J. A., Sietsma, J., Petrov, R. H., & Santofimia, M. J. (2023). Austenite formation from a steel microstructure containing martensite/austenite and bainite bands. journal of materials research and technology. https://doi.org/10.1016/j.jmrt.2023.06.270
- Zhou, L., Wu, F., Hall, R., & Davis, C. (2022). Electromagnetic sensors for in-situ dynamic microstructure monitoring of recovery and recrystallisation in interstitial free steels. Journal of Magnetism and Magnetic Materials. https://doi.org/10.1016/j.jmmm.2022.169187
- Xiong, L. et al., (2024). Revealing in-situ phase transition during laser additive manufacturing via high-speed synchrotron X-ray diffraction and imaging. Materials Research Letters. https://doi.org/10.1080/21663831.2024.2404539
- Łazarska, M., Musiał, J., Tański, T., & Ranachowski, Z. (2024). Transformations in the Ti-6Al-4V alloy studied using dilatometry supported by acoustic emission. Materials. https://doi.org/10.3390/ma17246260
- Zarei, Z., Zohrevand, M., Momeni, A., Sadeghpour, S., & Somani, M. (2023). Effect of heat treatment regime on microstructure and phase evolution of AlMo0. 5NbTa0. 5TiZr refractory high entropy alloy. Journal of Alloys and Compounds. https://dx.doi.org/10.2139/ssrn.4307867
- Heard, R., Siviour, C. R., & Dragnevski, K. (2022). Investigating Iron Alloy Phase Changes Using High Temperature In Situ SEM Techniques. Materials. https://doi.org/10.3390/ma15113921
- Vinnova. (2022). In situ X-ray diffraction during heat treatments to guide AI-modelling of phase transitions in steels (Project No. 2020-03800). Ferritico AB. https://www.vinnova.se/en/p/in-situ-x-ray-diffraction-during-heat-treatments-to-guide-ai-modelling-of-phase-transitions-in-steels/
Disclaimer: The views expressed here are those of the author expressed in their private capacity and do not necessarily represent the views of AZoM.com Limited T/A AZoNetwork the owner and operator of this website. This disclaimer forms part of the Terms and conditions of use of this website.