Jun 16 2011
Pulse Electronics Corporation (NYSE: PULS), a leading provider of electronic components, introduces its new laser direct structuring (LDS) antenna lasering process for antenna parts which are too long or large to fit well in conventional laser machines.
Pulse Electronic's lasering process saves as much as 30% over manufacturing done with previous LDS lasering machines, making LDS antennas cost competitive alternatives for laptop computers, tablets, and notebooks while providing superior RF quality and freedom of design.
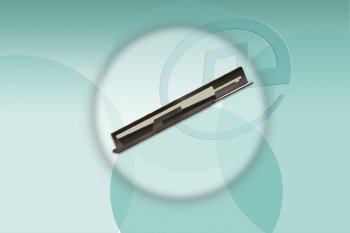
"In Pulse, the development of manufacturing technology has always been of major importance in enabling new designs and solutions which materialize into attractive and high performing products," explained Esa Kalistaja, engineering manager, Pulse Electronics Mobile Division. "High RF performance 3D-shaped antennas are increasingly needed to gain ever smaller and thinner mobile devices, especially in the desired round shapes. Pulse's efforts in manufacturing technology reinforce the translation of in-house RF and design expertise to cost-effective LDS antennas, which offer many benefits over other antenna solutions."
Development of Pulse Electronics' new lasering concept is based on LPKF Laser & Electronics' new Fusion 3D 1100 laser machine, which is adapted with a Pulse-designed and manufactured part handling system. This newly developed system is more capable of lasering long, large, or complex parts. The process has less design and dimensional limitations, yet still meets production efficiency.
LDS is the most capable 3D antenna manufacturing technology on the market and produces a high-performing 3D antenna. The laser beam transfers the antenna design directly onto a molded 3D surface, making prototyping and production faster. It enables design freedom and flexibility with quick versioning during the project phase, design freezing in the late project phase, and the ability to fine-tune the design during production to meet stringent carrier requirements. The production process is fast and easy to implement with low customer-specific tooling costs.
Pulse also manufactures cable assemblies that can be directly connected to all solderable materials, which is more cost effective than using connectors. With the RF performance benefits of LDS, this new process makes LDS antennas viable for the tablet and laptop market.
Pulse's LDS process enables fast product ramp-ups and seamless transfer between R&D and manufacturing sites. Pulse will install this state-of-art LDS machinery in many of its global locations to enhance R&D services in each continent. Pulse has been using LDS technology to manufacture antennas for handsets and laptops for several years. The new systems make laser processing for volume manufacturing of antennas for larger wireless devices such as laptops and tablets a practical option.