In an article recently published in the journal Additive Manufacturing, authors proposed a path planning algorithm for the printhead of fused deposition modeling (FDM) 3D printer to generate a single-stroke path and continuously print the shape without the need for repetitive filament cutting for every layer. The fabricated samples were also characterized by the authors using X-ray computed tomography (CT).
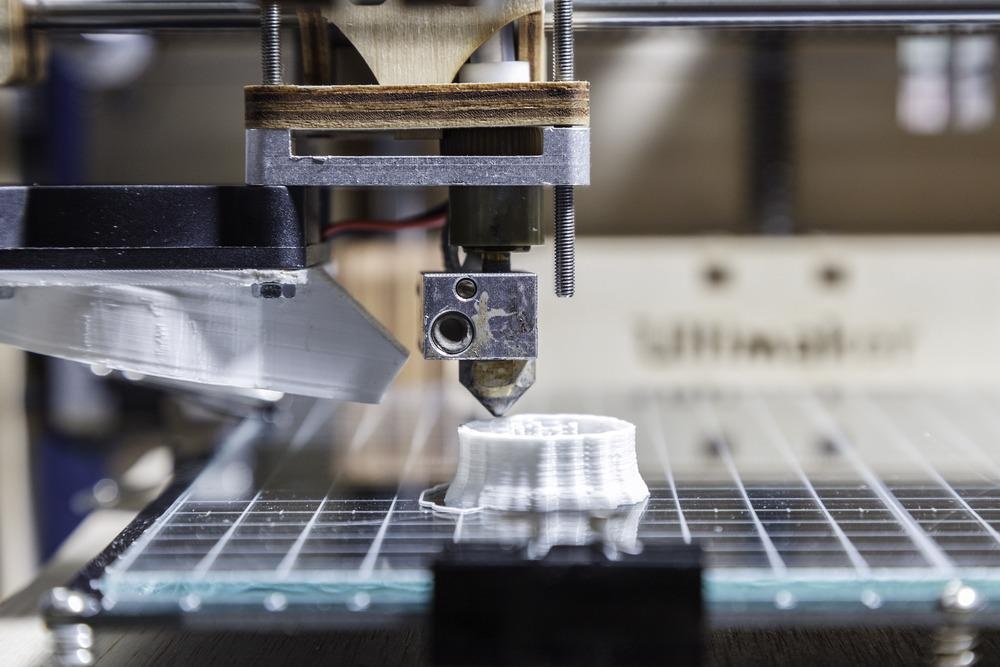
Study: A novel single-stroke path planning algorithm for 3D printers using continuous carbon fiber reinforced thermoplastics. Image Credit: Sergi Lopez Roig/Shutterstock.com
Three-dimensional (3D) printers applying continuous carbon fiber received considerable attention from researchers and were used to construct complex shapes. However, using carbon fiber filament in a 3D printer remains unexplored due to the requirement of additional steps to cut the carbon fiber filament multiple times.
Background
The excellent mechanical properties of continuous fiber composites enabled their application in 3D printer material. The conventional method of using them involves their fabrication as an intermediate.
The working of FDM 3D printers using resins or short fibers as the material is different from 3D printers using continuous fibers. However, the major drawback of using continuous fibers is that an intersection point in the same layer can break the fiber bundle due to excess material deposition in those areas, thus restricting the nozzle movement. In this context, limiting the fiber distribution at the intersections without altering the printing of the remaining parts can conditionally resolve the problem.
Limiting fiber distribution can be done either by using the in-nozzle impregnation method or by creating a path using slicing software and performing multiple cuts at the intersections or other points. However, the in-nozzle impregnation method limits the maximum fiber volume fraction, and the application of slicing software causes discontinuity in fibers and weakens the bundle strength.
About the Study
In the present study, the authors proposed an algorithm to print the target geometry in a single stroke. They created an Eulerian graph based on target structures and generated a path using Hierholzer’s algorithm with constraints.
The algorithm generated a single-stroke path inside the contour, which was subsequently transformed into an undirected graph further into an Eulerian graph to form the single stroke path. Calculating the Eulerian circuit from the Eulerian graph can determine the closure of the stroke. Finally, this path was adjusted at all intersections and transformed into a Geometric Code (G-code).
Research Findings
In the present study, the authors used honeycomb and triangular patterns as inputs, and the constructed samples were observed in the central upper part using ScanXmate-L080TT, an X-ray CT.
The results revealed that small gaps generated at the folded part of vertices were due to discontinuity in fibers and non-attachment to the resin. These gaps drastically reduced the stiffness and strength of the sample. Further, constructing the same complexes with PLA helped compare the reproducibility of the shapes. The results did not show gap generation with PCA, and reproducibility at the corners of vertices was very high.
The gaps formed were due to three shape reproducibility problems. The first problem is due to the stiffness of the filaments containing continuous carbon fibers and the inability to bend at the curvatures resulting in poor reproducibility. Moreover, the moment of inertia of the filament significantly affected the reproducibility in printing curves at severe curvatures.
The second problem was twisting at curvatures of lattice that can cause errors in the printing path. Although accurate prediction of torsions is possible, it cannot be zero practically. The third reproducibility problem is the continuity of the filament in the newly printed path. The difference between the direction of the previous print and the direction of the nozzle at curvatures caused misalignment. This misalignment was compensated by adjusting parameters.
Conclusion
In this study, the authors used continuous carbon fibers as material in FDM-based 3D printers and proposed a path planning method for the printer’s print head. The proposed method generated a single-stroked printing path for each layer. Each algorithm step was a single-stroke path.
The proposed method applies to infill the periodic patterns (with variable thickness) and complex patterns without periodicity. Although the present study discusses the application of the algorithm to lattice geometry, it can also be applied to generate single-stroke paths for other geometries.
The proposed algorithms work best for complex geometric pattern printing. Thus, the authors anticipate the combination of the proposed algorithm with the patterns obtained from topology optimization. Further, there are two challenges to the practical implementation of these algorithms to print complex 3D structures. The first is to develop a technology that considers the characteristics of continuous fibers to print target geometries with 3D intersections. The second challenge is to alter the algorithm’s constraints based on the inherited limitations from the 3D geometry of the complex structure and produce a suitable path to print the target geometry.
More from AZoM: How Can Valve Diagnostics Reduce Emissions in the Chemical Industry?
Disclaimer: The views expressed here are those of the author expressed in their private capacity and do not necessarily represent the views of AZoM.com Limited T/A AZoNetwork the owner and operator of this website. This disclaimer forms part of the Terms and conditions of use of this website.
Source:
Yamamoto, K., Luces, J. V. S., Shirasu, K., Hoshikawa et.al. A novel single-stroke path planning algorithm for 3D printers using continuous carbon fiber reinforced thermoplastics. Additive Manufacturing (2022). https://www.sciencedirect.com/science/article/pii/S2214860422002160