A group of researchers recently published a paper in the journal Polymers that demonstrated the feasibility of using natural fibers, specifically pineapple leaf fiber (PALF), for the fabrication of polymer composites.
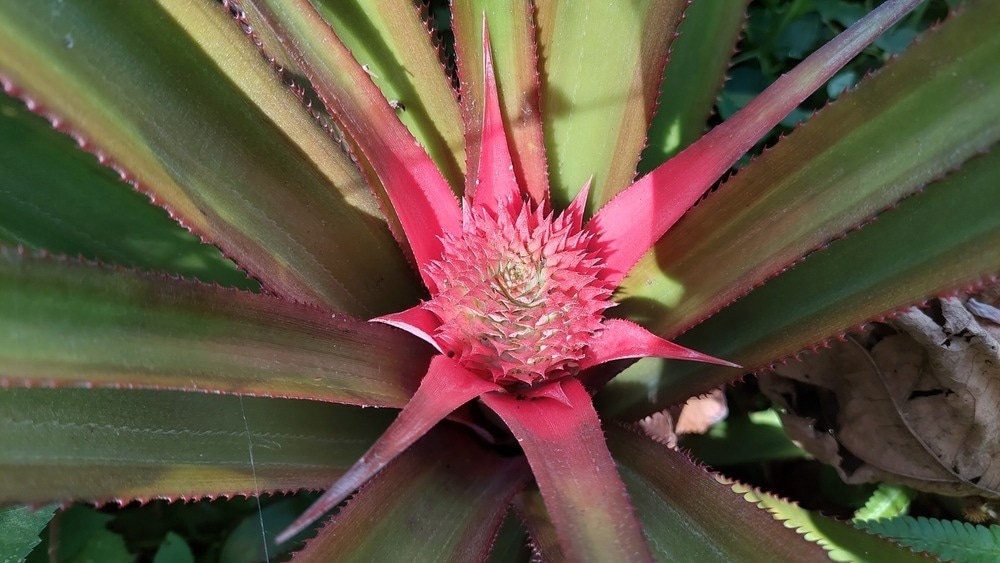
Study: Potentiality of Utilizing Woven Pineapple Leaf Fibre for Polymer Composites. Image Credit: Ekky Ilham/Shutterstock.com
Background
Natural fiber-reinforced polymer composites (NFRPCs) are considered an eco-friendly alternative to synthetic fiber-reinforced composite materials. These composites also possess several other advantages, such as superior mechanical properties, lower density, and affordability.
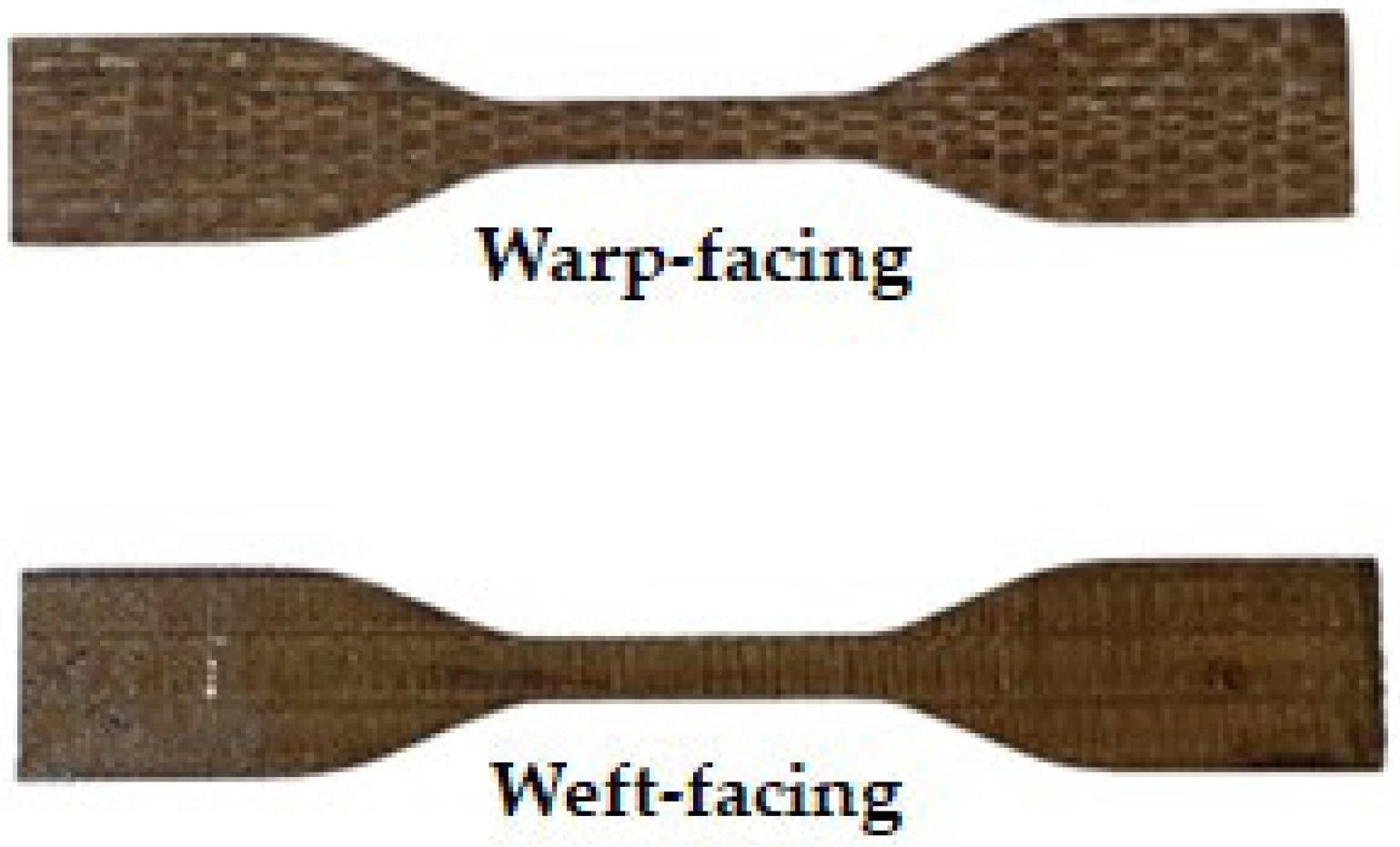
Warp and weft direction of woven PALF-reinforced epoxy composites. Image Credit: Hadi, A.E. et al., Polymers
Moreover, the use of natural fibers to prepare composite materials can enhance sustainability by decreasing energy consumption, owing to the low density of such fibers. The mechanical and physical properties of natural fiber woven composites are determined by the polymer type, fiber orientation, layering sequences, and woven structure.
PALF is a natural fiber with the highest cellulose content and tensile strength (TS). It is also one of the most eco-friendly types of natural fiber. PALF is used most extensively in the textile industry to reinforce polymer composites owing to its good acoustic and thermal insulation, extensive availability, and lower cost.
Although several studies were performed to investigate the feasibility of using unidirectional, random, long, and short PALF mats as reinforcement agents in composites, studies evaluating the properties of woven PALF and its mechanical performance when used as a composite reinforcement have been limited.
The Study
In this study, researchers evaluated the potential of woven PALF in reinforcing epoxy resin (ER) composite by fabricating a woven PALF-reinforced ER composite. Specifically, the effect of warp (0o) and weft (90o) fiber orientations and layering numbers on the PALF-reinforced ER composite mechanical properties were investigated. PALF-reinforced ER composites with four-layer (4L), three-layer (3L), and two-layer (2L) of woven PALF were synthesized to assess the effect of different layering numbers.
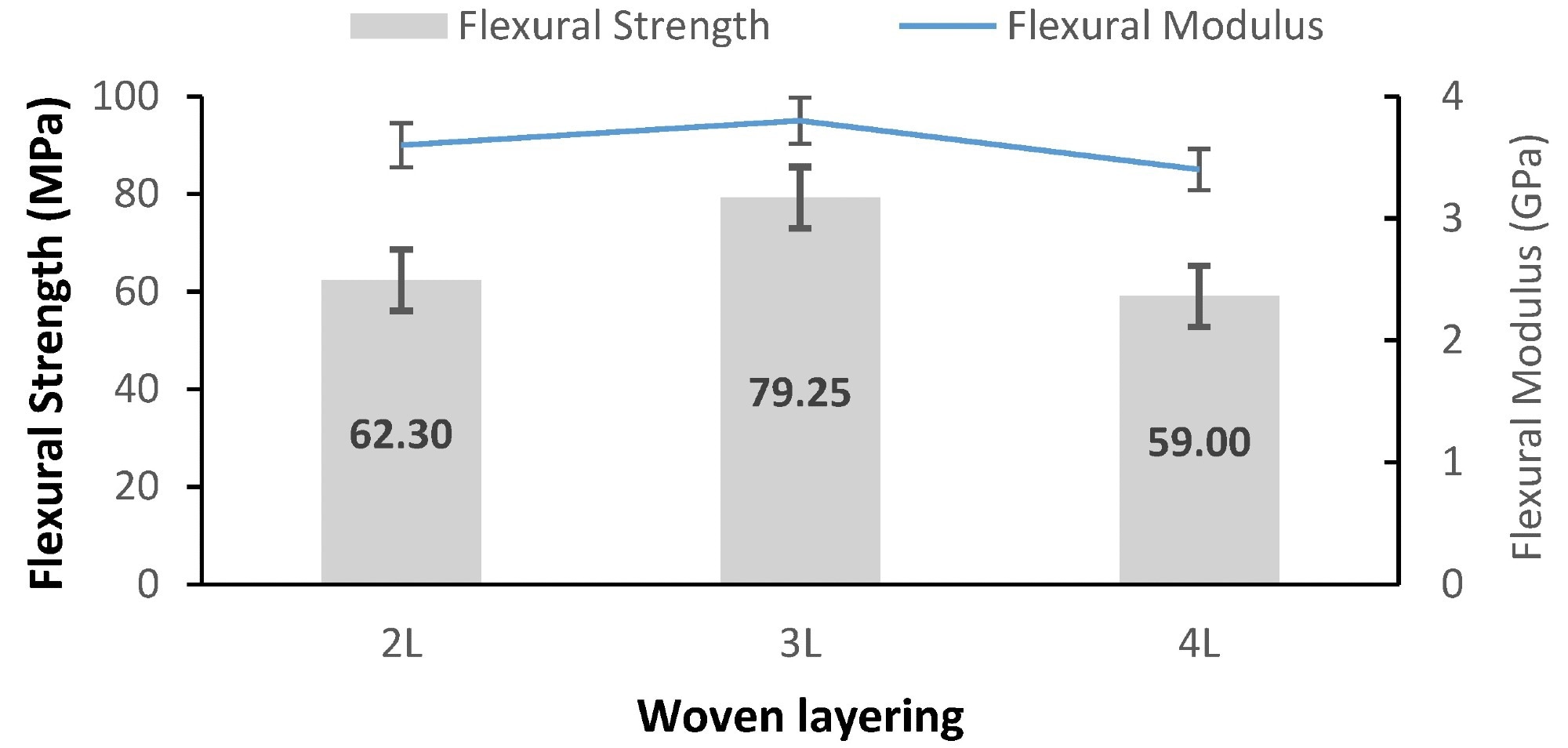
Flexural properties of woven PALF-reinforced epoxy composite at different layering numbers. Image Credit: Hadi, A.E. et al., Polymers
A plain type of woven PALF was used to prepare the woven PALF-reinforced ER composites with three woven PALF layer numbers using the hand layup technique. The woven PALF was cut into 300 × 300 mm pieces, which were then arranged in layers in an aluminum mold. A releasing agent was dispersed on the inner mold surfaces before the initiation of the lamination process to avoid the sticking of the composite to the mold and produce a sample with a smooth surface.
The hardener matrix and the ER were mixed and stirred uniformly and slowly for five min. Subsequently, the mixture was poured into the aluminum mold, and a scraper was used to spread the mixture throughout the surface of the layered woven PALFs.
A compression molding machine was employed to cure the as-prepared composites at room temperature for 24 h to eliminate the air bubbles. 50 bars of compression pressure were applied with dead weights on top of the mold. Eventually, the samples were retrieved from the aluminum mold and cut into desired sizes according to American Society for Testing and Materials (ASTM) standards using a laser cutter for further experiments.
Researchers performed flexural tests and tensile tests on the fabricated samples to determine flexural modulus (FM) and flexural strength (FS) and TS and tensile modulus (TM), respectively, using the INSTRON 3369 universal testing machine (UTM) with a 2 mm/min crosshead speed at room temperature.
Rectangular-shaped three-point bending (3PB) tests were performed for the flexural tests. The Zeiss Evo50 scanning electron microscope (SEM) was employed to characterize the woven PALF-reinforced ER composites.
Observations
Woven PALF-reinforced ER composites were fabricated successfully. The percentage of woven PALF in the 2L, 3L, and 4L woven PALF-reinforced epoxy composites were 20, 25, and 29.4 wt.%, respectively.
Composites with warp fiber orientation displayed a higher TS compared to the composites with weft fiber orientation. For instance, the TS of 3L-warp and 2L-warp samples were considerably higher than that of 3L-weft and 2L-weft samples.
The fiber orientation values were increased by 20% from 2L-warp to 3L-warp, and by 22% from the 2L-weft to 3L-weft. However, decohesion was observed in the composites between the fiber and the matrix with the increasing number of woven PALF layers for both warp and weft orientations due to the zone stress.
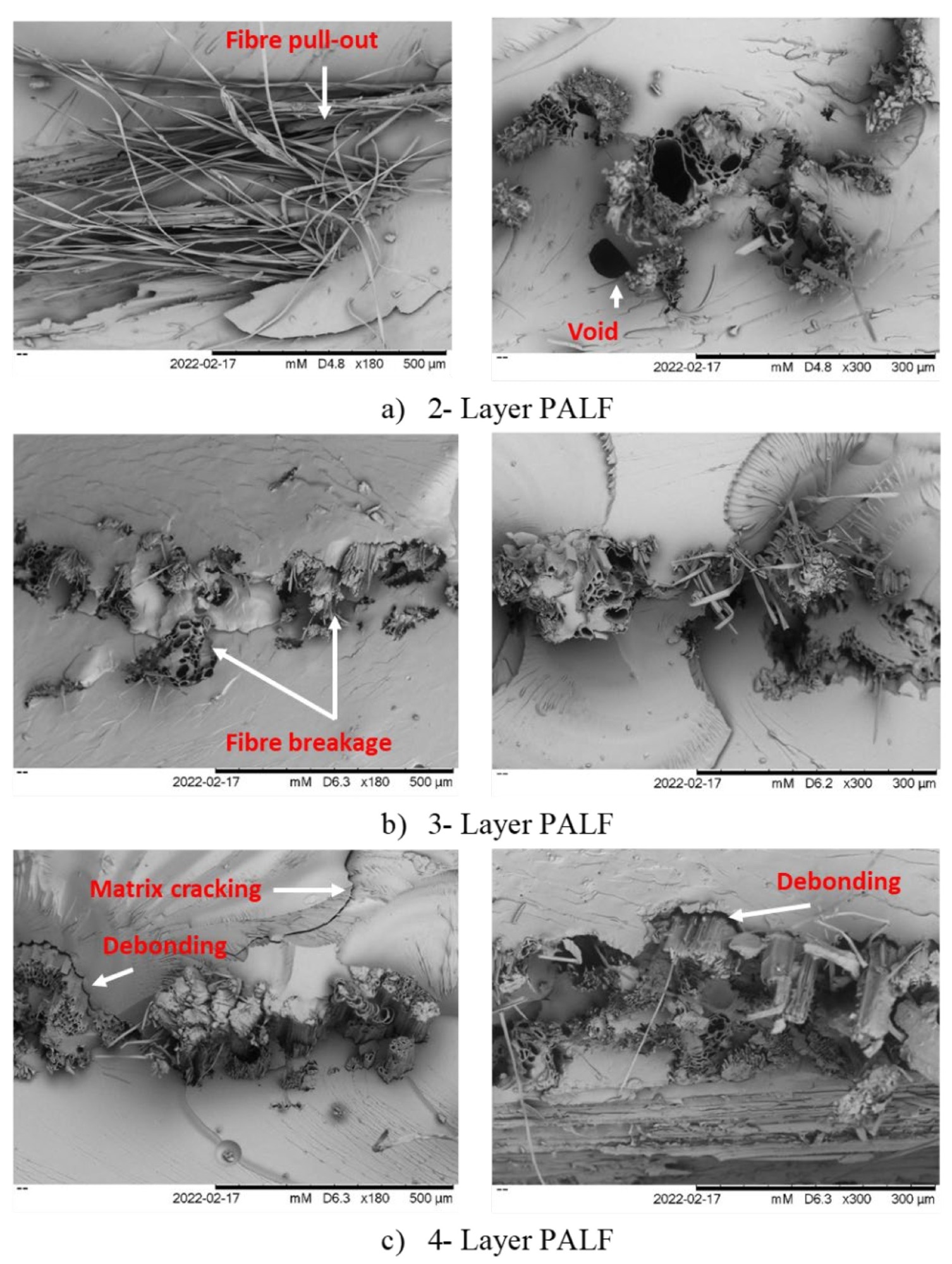
Tensile fracture of woven PALF/epoxy composites; (a) 2-layer, (b) 3-layer, (c) 4-layer. Image Credit: Hadi, A.E. et al., Polymers
Thus, the TS of the composites decreased when the number of woven PALF layers increased beyond three layers as the composite materials failed to hold the polymer matrix reinforcement after three PALF layers/critical fiber composition, leading to a minimal stress transfer between the matrix and fiber. The TS from 3L-warp to 4L-warp samples was reduced by 16%, while the TS from 3L-weft to 4L-weft fiber orientation was reduced by 9% owing to the poor arrangement of fibers in 4L woven PALF-reinforced composites.
The TM demonstrated a similar trend as the TS, with the average TM increasing from 2L to 3L samples and then decreasing from 3L to 4L samples for both warp and weft fiber orientations. 4L samples demonstrated the lowest TM values for both orientations. The decrease in TM from 3L to 4L samples was attributed to the incorporation of defects, such as pores, during the layered fabrication process and improper matrix-to-fiber bonding.
Samples with the warp fiber orientation displayed the highest TM value. The observations indicated that the 3L composite is more ductile compared to 2L and 3L composites in both fiber orientations. Fiber orientations, woven fibers, layering numbers, and weave designs primarily influenced the tensile properties of the composites.
Both FM and FS values of the woven-PALF reinforced ER composites were increased from 2L to 3L samples and then reduced from 3L to 4L, with 3L specimens highest FM and FS of 3.8 GPa and 79.25 MPa, respectively. The FM and the FS of the samples were influenced by the fiber-matrix adhesion strength and the number of woven PALF layers in the fabricated composites.
Matrix cracking, debonding, voids, and fiber pull-out primarily influenced the interfacial adhesion between the fiber and matrix. Moreover, the internal bonding of the matrix and fiber was critical to the NFRPC properties owing to its significance in the stress transfer between fiber and matrix.
To summarize, the findings of this study demonstrated the feasibility of using PALF for the fabrication of polymer composites, with the 3L woven PALF-reinforced ER composites displaying superior flexural and tensile properties due to matrix and fiber compatibility.
Disclaimer: The views expressed here are those of the author expressed in their private capacity and do not necessarily represent the views of AZoM.com Limited T/A AZoNetwork the owner and operator of this website. This disclaimer forms part of the Terms and conditions of use of this website.
Source:
Hadi, A.E., Siregar, J.P., Cionita, T. et al. Potentiality of Utilizing Woven Pineapple Leaf Fibre for Polymer Composites. Polymers 2022. https://www.mdpi.com/2073-4360/14/13/2744