By Surbhi JainReviewed by Susha Cheriyedath, M.Sc.Sep 28 2022
In an article recently published in the journal Additive Manufacturing, researchers discussed the laser powder bed fusion (L-PBF) microstructural engineering of a dual-phase Ti-Al-V-Fe alloy using in situ alloying.
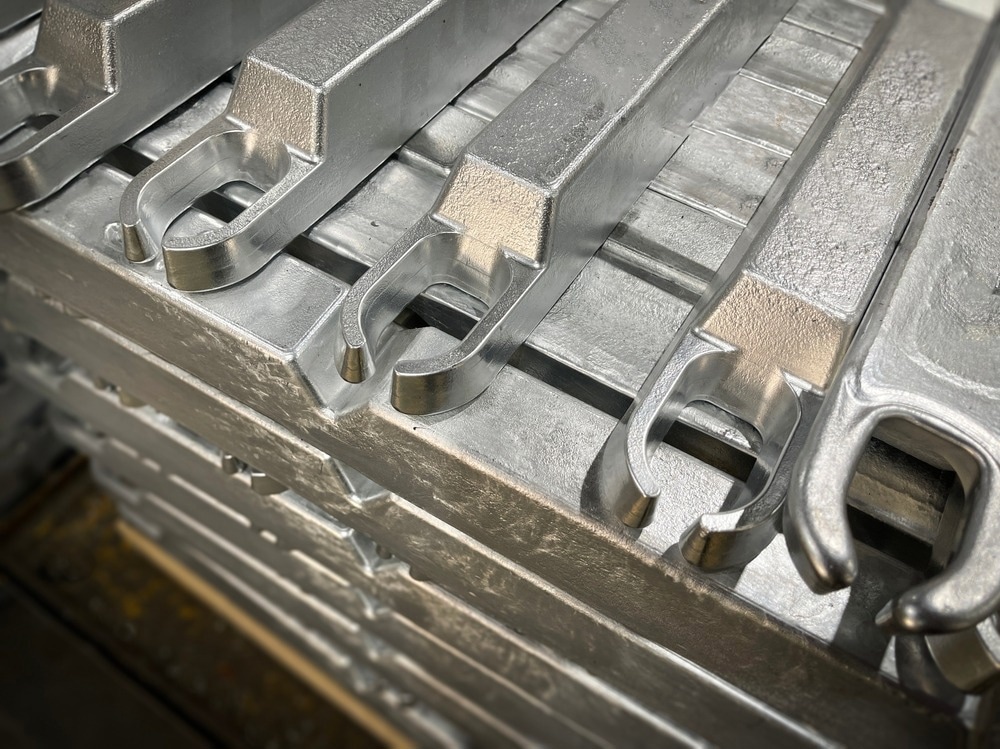
Study: Microstructural engineering of a dual-phase Ti-Al-V-Fe alloy via in situ alloying during laser powder bed fusion. Image Credit: Javier Ruiz/Shutterstock.com
Background
The use of metallic powders in additive manufacturing (AM) to create components with complicated structures close to net shapes has improved significantly during the past ten years. Due to their remarkable weldability, titanium (Ti) alloys made via L-PBF, especially Ti-6Al-4V (Ti64), have attracted a lot of interest for use in the aerospace and bio-medical industries.
The Ti64 produced by L-PBF exhibits hierarchical structure formation. Engineering microstructures and phase fractions have received a lot of attention to enhance mechanical characteristics. In the meantime, a substitute technique for producing Ti alloys with varied microstructures and phase fractions during the L-PBF process is emerging, using blended powders, including β-stabilizers instead of pre-alloyed powders.
For a variety of applications, the printed parts display a wide range of mechanical characteristics. Utilizing L-PBF as a feedstock for blended powders provides enough flexibility to build innovative Ti alloys with a wide range of possible compositions. The fatigue resistance is negatively impacted by the presence of retained hard Mo particles. Cu particles enhance the printed Ti alloy's antibacterial characteristics for use in hard tissue implants, but they can also result in unfavorable intermetallic CuTi2. The majority of publications in the literature concentrate on the powder combination chemical makeup and how it affects the phase fractions.
However, the distribution of elements has a significant impact on the mechanical characteristics of linked microstructures. For Fe-modified Ti64 alloys, the relationship between the laser production parameters and the as-built microstructures is still seldom ever investigated.
About the Study
In this study, the authors showed how to tailor the phase fraction of a Ti alloy produced by LPBF using a blend of powders made of Ti-6Al-4V and 3 wt% Fe particles. By changing the laser parameters, the as-built microstructures transition from α’-dominated microstructure to a nearly full β-dominant microstructure.
The team inferred that the spatial distribution of the β-stabilizer Fe under the high cooling rates typical of L-PBF processing could be related to microstructure using X-ray fluorescence, high-speed operando X-ray diffraction, and electron backscatter diffraction (EBSD) analysis. Without the need for post-processing heat treatments, the as-built microstructure with significant amounts of β phase achieved high strength and improved ductility.
The researchers explored how the L-PBF laser process parameters affect the final microstructures and mechanical characteristics of a blended powder made up of Ti64 and 3 wt% Fe particles. The as-built microstructures transitioned from β dominant to virtually complete α’ microstructures as volume energy densities increased. The Ti-alloy with the predominant β-atom achieved superior mechanical characteristics.
This showed how laser manufacturing parameters could be used to construct certain microstructures and open the path for producing functionally gradient characteristics in Ti alloys made additively.
Observations
The effective influence of Fe addition on the stability of the metastable β phase under rapid cooling circumstances was revealed by using the temperatures as a function of time to determine cooling rates and diffusion lengths. Using blended powders composed of Ti-6Al-4V combined with 3 wt% Fe particles, the metastable β-Ti phase could be stabilized to room temperature under a rapid cooling rate in the range from 5.8 x 105 to 1.1 x 106 K/s during the L-PBF procedure.
Compared to samples printed with low energy density, those printed with higher energy density displayed stronger thermal cycling with more cycles exhibiting peak temperatures that were greater than the β transus temperature. By increasing the energy input, the as-built microstructures could be changed from β dominant to practically complete α’. This was related to the distribution and density of Fe, which was connected to the process variables. Fe was distributed unevenly in the microstructure at low energy densities. However, increased energy density caused more Fe to be lost and better Fe atom mixing in the Ti64 matrix, which resulted in a substantially smaller stabilized β-fraction after printing.
High strength and ductility were both concurrently achieved by the printed microstructures containing a significant β proportion. When the α’ phase was dominant, the strength was increased, but the ductility declined.
Conclusions
In conclusion, this study showed an efficient way to tailor the microstructures of Ti6Al4V-Fe alloys produced additively by changing the laser parameters throughout the L-PBF process while employing blended powders. Phase evolution and temperature profiles were measured using high-speed operando X-ray diffraction during printing. To demonstrate how energy input affects the elemental distribution and phase fractions, the specimens' microstructures were examined. The representative samples' mechanical characteristics were evaluated.
The authors demonstrated a paradigm for designing Ti alloy microstructures via additive manufacturing. They mentioned that the proposed paradigm made it possible to produce customized microstructures and opened the door to designing specified qualities with functionally gradient properties.
The team believes that the proposed approach could be extended by several alloy systems for the production of L-PBF by controlling the processing parameters and designing the powder composition.
More from AZoM: What is Glow Discharge Optical Emission Spectrometry
Reference
Chen, M., Petegem, S. V., Zou, Z., et al. Microstructural engineering of a dual-phase Ti-Al-V-Fe alloy via in situ alloying during laser powder bed fusion. Additive Manufacturing, 103173 (2022). https://www.sciencedirect.com/science/article/pii/S2214860422005620
Disclaimer: The views expressed here are those of the author expressed in their private capacity and do not necessarily represent the views of AZoM.com Limited T/A AZoNetwork the owner and operator of this website. This disclaimer forms part of the Terms and conditions of use of this website.