Introduction As a result of new environmental regulations to reduce the amount of sulfur in vehicle transportation fuels, the need to study the catalytic hydrodesulphurization process is steadily increasing [1, 2]. Therefore, great interest has been focused on the research of new routes to obtain catalysts for hydrodesulphurization (HDS). In spite of the great variety of routes used, mechanical alloying (MA) routes have not been explored satisfactorily. By using MA it has been possible to synthesize novel materials with special physical and chemical properties [3, 4]. Elaboration of Raney-type catalyst combines powder metallurgy routes with chemical treatments to obtain a highly porous final product. Unsupported catalysts called NEBULA (New Bulk Activity) based on Ni-Mo-W, are four times more active than typical catalysts and two times more than advanced formulations [5]. These types of catalysts opened the way to new bulk catalysts with improved catalytic activity in HDS. In this work, quaternary alloys of Ni-Mo-W-Al were prepared by MA. In addition, a process of chemical extraction by alkaline leaching was applied to remove aluminum in order to increase the specific surface area (SSA) and to generate porous materials which were tested in the HDS of dibenzothiophene (DBT) to determine their catalytic activity and the selectivity. Experimental Nickel (99.8% purity, -300 mesh), molybdenum (99.9% purity, -200 mesh), tungsten (99.9% purity, -325 mesh), and aluminum (99.5% purity, -325 mesh), crystalline metal powders were used as raw materials. Nominal composition was set to (Ni50Mo25W25)50Al50 mol%. The MA experimental runs were performed at room temperature in a commercial high-energy ball mill (Spex 8000). The milling time intervals were 0, 3, 6 and 9 h. Methanol was used as process control agent. The milling media to powder mass ratio was maintained constant at 5 : 1 for all experiments. Argon atmosphere was selected during the milling process. In order to increase the SSA the as-milled products were leached in an alkaline potassium hydroxide solution (KOH 20 mass% and pH = 12) at room temperature for 1 h. Catalysts Characterization SSA was measured using a Quantachrome Nova 1000 series by nitrogen adsorption at 77 K, using the BET method. Samples were degassed under vacuum at 473 K before nitrogen adsorption. X-Ray diffraction (XRD) studies were performed using a Philips XPert MPD Diffractometer equipped with a curve graphite monochromator, using a Cu Kα radiation (λ =1.54056 Å) and operated at 43 kV and 30 mA. Catalyst morphology was studied using a JEOL JSM-5800 LV scanning electron microscope analyzing several fields at different magnifications. Trasmission electron micrographs were obtained in a Philips CM200 trasmission electron microscope operated at 200 kV with an LaB6 filament as a source of electrons. Catalytic Activity and Selectivity The HDS of DBT has been extensively studied as a model reaction HDS of petroleum feedstock [6]. Laboratory-scale studies have been performed in pressurized flow [7] and batch reactors [8-12]. By using batch reactors, useful information such as reaction rate constants (k) and selectivity (HYD/DDS) can be obtained by following the composition of the reaction mixture as a function of time. In this work, the HDS of DBT was carried out in a Parr model 4560 high-pressure batch reactor. One gram of catalyst was placed in the reactor with the reagents (5 vol% of DBT in decaline). The reactor was then pressurized to 3.1 MPa with hydrogen and heated up till 623 K. After the working temperature was reached, sampling for chromatographic analysis was performed during the course of each run to determine conversion versus time dependence. The reaction time averaged was 5 hours. The resulting products were analyzed using a Perkin-Elmer Clarus 500 gas chromatograph provided with an autosampler and equipped with a 2.736 m long packed column containing 3% OV-17 (phenyl methyl dimethyl silicone, 10% phenyl) as separating phase on Chromosorb WAW 80/100. After catalytic evaluation, the samples were separated from the reaction mixture by filtration, then washed with 2-propanol to remove residual reaction products and dried at room temperature. The main reaction products from the HDS of DBT were biphenyl (BP), cyclohexylbenzene (CHB) and tetrahydrodibenzothiophene (THDBT). Results and Discussion Figure 1 shows the XRD patterns obtained from powders produced by MA. For the samples at 3 and 6 h, peaks corresponding to nickel and aluminum are broad and short, indicating the presence of nanocrystalline structure. As we can observe at 9 h, apparently almost all aluminum was dissolved into nickel and molybdenum or tungsten matrix; however, there is no evidence of formation of a new phase during milling. For Mo and W an effect of crystallization was observed. This behaviour can be related with a process called “mechanically driven crystallization” since it has been reported that severe mechanical deformation also induces crystallization in some alloys [13]. Remaining aluminum is not detected by XRD, probably because it is still in solution within Ni, Mo and W cell, in accordance with the typical peaks reflections shifting. On the other hand, there is no evidence of change in crystalline structure after leaching (Figure 2), as it was reported several years ago by Ivanov [3]. 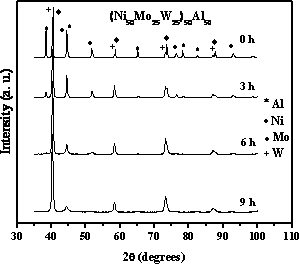 Figure 1. XRD patterns of milled samples. 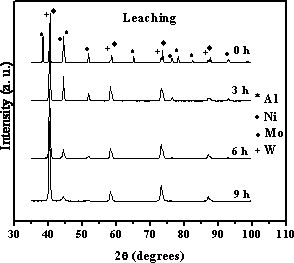 Figure 2. XRD patterns of leached samples (with exception of 0 h sample). In our samples Ni and Mo(W) retained their FCC and BCC structures after the milling process and leaching treatment since the chemical dissolution by using alkaline solution is selective for aluminum [14]. Difractograms for samples at 3 and 6 h reveal the remotion of aluminum during the chemical treatment since it was not possible to detect its typical peak reflections. However, an EDS analysis confirmed that aluminum was not completely removed in the leaching process (see Table 1). Furthermore, we detected the presence of oxygen which could be present in the form of oxide but by using these characterization techniques we can not clarify this and it represents a highest ongoing characterization challenge in this field. Molar ratios for the catalysts show variations depending on the milling time and are smaller than those expected. This behaviour could be attributed to the synthesis method. Table 1. EDS analysis for samples at 3, 6 and 9h before and after leaching process (mol%). | Before leaching | | | | | | | 3 h | 21.72 | 23.29 | 6.89 | 3.78 | 44.32 | | 6 h | 24.48 | 24.81 | 8.16 | 5.75 | 36.80 | | 9 h | 27.21 | 24.44 | 7.26 | 3.61 | 37.48 | | After leaching | | | | | | | 3 h | 24.46 | 44.34 | 19.39 | 8.13 | 3.41 | 0.27 | 6 h | 35.21 | 39.74 | 12.21 | 5.84 | 6.63 | 0.39 | 9 h | 35.03 | 39.26 | 11.90 | 6.65 | 7.02 | 0.16 | Figure 3 shows SEM images of milled samples at 3 and 9 h (before leaching and after leaching). Samples in the as-milled condition (Figures 3a and c) reveals an irregular morphology, typical of milled products. Upon increasing the milling time (9 h), the particles broke down and show a more uniform shape. Figure 3(b) presents a SEM micrograph of a leached specimen originally produced at 3 h. The size and the shape of the particles before (Figure 3(a)) and after leaching (Figure 3(b)) were almost unchanged. On the other hand, a different behaviour was observed for sample at 9 h wherein the presence of porosity was evident after the alkaline leaching process. Figure 3(d) shows a particle containing small porosity ranging from 1 to 3 μm. 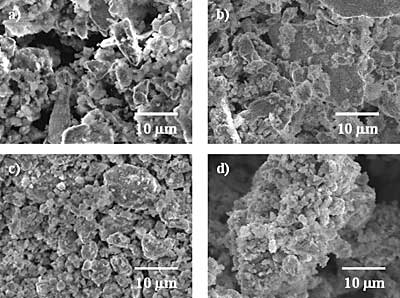 Figure 3. SEM micrographs of (Ni50Mo25W25)50Al50 alloys prepared by MA: a) 3 h before leaching, b) 3 h after leaching, c)9 h before leaching, and d) 9 h after leaching. Figure 4 presents the SSA before and after alkaline leaching process. Figures 5 and 6 show the reaction rate constants (k) and the selectivity (HYD/DDS) of Ni-Mo-W catalysts (respectively). The alkaline leaching process increase the SSA. This variation in SSA has an important effect in the catalytic properties. 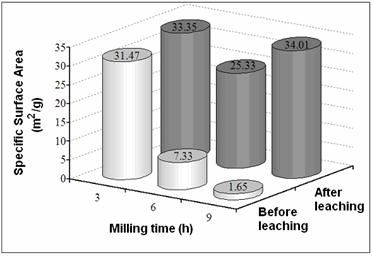 Figure 4. Specific Surface Area before and after leaching. 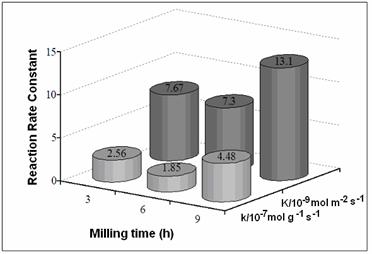 Figure 5. Reaction Rate Constants (k) of Ni-Mo-W catalysts. 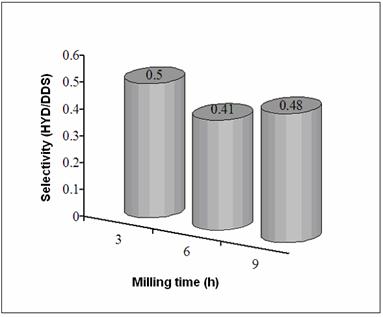 Figure 6. Selectivity (HYD/DDS) of Ni-Mo-W catalysts. Figures 7(a) and (b) show low magnification TEM images of a particle of the starting alloy and of final Ni-Mo-W catalyst prepared at 9 h of milling time. The difference in morphology is easily observed: the starting morphology (Figure 7a) is transferred into an aglomerate of particles of spongy form (Figure 7b). On the other hand, Figure 7c shows a typical dark field image from as-leached particle at 9 h of milling time. This particle presents small crystal size (40-100 nm) and in some cases lower (10-30 nm). Note the presence of porous (20-180 nm) produced by chemical dissolution of aluminum.  Figure 7. TEM images from (Ni50Mo25W25)50Al50 alloys prepared by MA at 9 h, a) before leaching, b) after leaching, c) dark field image after leaching. Sample at 6 h exhibits lower catalytic activity since a lower surface area value was obtained for this sample compared to their 3 and 9 h counterparts. On the other hand, the catalytic activity of the sample at 9 h was enhanced as a result of a great increase in SSA and a more evident presence of porosity. This kind of morphology could favor the catalytic activity since in nanocrystalline alloys, the enormous quantity of available grain borders and the presence of intergrain disorder can be important sources of active sites [4]. The HDS of DBT yields biphenyl (BP) through the so-called direct desulphurization pathway (DDS) and cyclohexilbenzene (CHB) and tetrahydrodibenzothiophene (THDBT) through the hydrogenative pathway (HYD). Since these two pathways are parallel [15], the selectivity (HYD/DDS) can be approximately calculated by: (HYD)/(DDS) = ([CHB]+[THDBT])/[BP] All catalysts present a preference for the DDS pathway, in accordance with previous studies [14]. Conclusions Raney-type Ni-Mo-W-based catalysts were produced by combining mechanical alloying and an alkaline leaching process. An increase in specific surface area was obtained after leaching treatment. The nanocrystalline state, the synergized effect of small particles and presence of porous and nanoporous affect the catalytic activity of this kind of catalysts. These catalysts show a moderate catalytic activity in the HDS of DBT. Acknowledgements The authors thank to W. Antúnez, E. Torres, H. Esparza and A. Medina for their valuable technical assistance with SEM/TEM and XRD analysis. References 1. J. Vakros and C. Kordulis, “On the synergy between tungsten and molybdenum in the W-incorporated CoMo/Al2O3 hydrodesulfurization catalysts”, Appl. Catal., A 217 (2001) 287-293. 2. Ch. Song and X. Ma, “New Design Approaches to Ultra Clean Diesel Fuels by Deep Desulfurization and Deep Dearomatization”, Appl. Catal., B 41 (2003) 207-238. 3. E. Ivanov, A.A. Makhlouf, K. Sumiyama, H. Yamauchi and K. Suzuki, “ Structural and magnetic properties of non-equilibrium b.c.c. nickel prepared by leaching of mechanically alloyed Ni35Al65”, J. of Alloys and Compounds, 185 (1992) 25-34. 4. R. Schulz, J.Y. Huot, M.L. Trudeau, L. Dignard-Bailey and Z.H. Yan, “Nanocrystalline Ni-Mo alloys and their application in electrocatalysis”, J. Mater. Res., 9 (11) (1994) 2998-3008. 5. S. L. Soled, S. Miseo, R. Krikak, H. Vroman, T. H. Ho and K. L. Riley, “Nickel Molybodtungstate Hydrotreating Catalysts”, US Patent No. 6, 299, 760 B1 (Oct. 9, 2001). 6. H TopsØe., B. S. Clausen and F. E. Massoth, “Hydrotreating Catalysis-Catalysis, Catalysis Science and Technology”, J. R. Anderson and M. Boudarts, Eds., Vol. 11 Springer-Verlag, Berlin (1996) 111. 7. H. Ishihara, T. Itoh, T. Hino, M. Nomura, P. Qi and T. Kabe, “Effects of Solvents on Deep Hydrodesulfurization of Benzothiophene and Dibenzothiophene”, J. Catal., 140 (1993) 184-189. 8. A. J. Jacobson, R. R Chianelli and T. A Pecoraro, “Transition metal sulfide promoted molybdenum or tungsten sulfide catalysts and their uses for hydroprocessing”, U.S. Patent No. 4,650,563 (March 17, 1987). 9. A. W. Naumann and A. S. Behan, “Molybdenum disulfide catalyst and the preparation thereof”, U.S. Patent No. 4,243,554 (January 6, 1981). 10. R. R. Chianelli, and T. A. Pecoraro, “Carbon-containing molybdenum and tungsten sulfide catalysts”, U.S. Patent No. 4,508,847 (April 2, 1985). 11. T. A Pecoraro and R. R. Chianelli, “Hydrogenation processes using carbon-containing molybdenum and tungsten sulfide catalysts”, U.S. Patent No. 4,528,089 (July 9, 1985). 12. D. J. Sajkowski and S. T. Oyama, “Catalytic hydrotreating by molybdenum carbide and nitride: unsupported Mo2N and Mo2C/Al2O3”, Appl. Catal., A 134 (1996) 339. 13. K. Aoki, M. Sherif El-Eskandaran, K. Sumiyama and K. Susuki. “Cyclic Crystalline-Amorphous Transformations by Mechanical Alloying”, Trans Tech Publications, Switzerland, Material Science Forum, 269-272 (1998) 119-126. 14. M. Sosa, I. Estrada-Guel, G. Alonso, C. Ornelas, S. D. De la Torre and R. Martínez-Sánchez, “Ni-Mo Catalyst Synthesized by Mechanical Alloying”, Journal of Metastable and Nanocrystalline Materials, 15-16 (2003) 745-750. 15. D.D. Whitehurst, T. Isoda and I. Mochida, “Present State of the Art and Future Challenges in the Hydrodesulfurization of PolyaromaticSulfur Compounds”. Adv. Catal., 42 (1998) 345. Contact Details R. Huirache-Acuna Centro de Investigación en Materiales Avanzados, CIMAV Miguel de Cervantes 120, Complejo Industrial Chihuahua, Chih. 31136, México Universidad Michoacana de San Nicolás de Hidalgo Ciudad Universitaria Morelia, Mich. México E-mail: [email protected] | M. I. Flores Z Universidad Michoacana de San Nicolás de Hidalgo Ciudad Universitaria Morelia, Mich. México | M. A. Albiter Centro de Investigación en Materiales Avanzados, CIMAV Miguel de Cervantes 120, Complejo Industrial Chihuahua, Chih. 31136, México Universidad Michoacana de San Nicolás de Hidalgo Ciudad Universitaria Morelia, Mich. México | I. Estrada-Guel Universidad Michoacana de San Nicolás de Hidalgo Ciudad Universitaria Morelia, Mich. México | C. Ornelas Universidad Michoacana de San Nicolás de Hidalgo Ciudad Universitaria Morelia, Mich. México | F. Paraguay-Delgado Universidad Michoacana de San Nicolás de Hidalgo Ciudad Universitaria Morelia, Mich. México | J.L. Rico Universidad Michoacana de San Nicolás de Hidalgo Ciudad Universitaria Morelia, Mich. México | L. Bejar-Gomez Universidad Michoacana de San Nicolás de Hidalgo Ciudad Universitaria Morelia, Mich. México | G. Alonso-Nunez Centro de Investigación en Materiales Avanzados, CIMAV Miguel de Cervantes 120, Complejo Industrial Chihuahua, Chih. 31136, México | R. Martinez-Sanchez, Centro de Investigación en Materiales Avanzados, CIMAV Miguel de Cervantes 120, Complejo Industrial Chihuahua, Chih. 31136, México | |