Introduction Barium strontium titanate, often abbreviated as Ba1-xSrxTiO3 to clearly define its composition, is a ferroelectric material which has a perovskite structure (ABO3 structure). It has a high dielectric constant, low dissipation factor, a compositional-dependent Curie temperature (Tc) [1] and is proven to show good thermal as well as mechanical stabilities [2-3]. From a material point of view, Ba1-xSrxTiO3 is composed of mixed titanates of barium titanate (BaTiO3) and strontium titanate (SrTiO3) [4-5]; or in other words, the strontium (Sr) atoms are introduced into the A site in the perovskite BaTiO3 matrix to replace barium (Ba) atoms; thus it is also known as Sr-doped BaTiO3 [6]. There are several ways to synthesize Ba1-xSrxTiO3 powder, in general, by either dry synthesis or wet chemical synthesis [7]. The former, based on solid state reaction, is the most commonly used method to produce Ba1-xSrxTiO3; whereas the latter, which include methods such as co-precipitation, sol-gel and hydrothermal, has been developed to overcome certain limitations in the solid state reaction method. Each of these methods has its merits and drawbacks. For example, the solid state reaction by conventional ball milling requires high processing temperature but it is relatively simple and cost effective. Wet chemical synthesis solve the problem of high processing temperature but often results in low yield and the starting chemicals are costly [8-10]. Regardless of the method by which they are synthesized, however, the process must be economical and the resultant powder must exhibit high purity, controlled stoichiometry and excellent electrical properties. In this paper, we investigated the calcination temperature required to form single phase Ba0.70Sr0.30TiO3 powder by mechanically activation of BaCO3-SrCO3-TiO2 starting materials. Dielectric properties as well as microstructure development were also investigated as a function of sintering temperature. Experimental Procedure Ba0.70Sr0.30TiO3 formation by mixed oxide route through solid state reaction was studied. High-purity raw materials of BaCO3 (Merck, 99+% purity), SrCO3 (Merck, 99+% purity) and TiO2 (Merck, 99+% purity) were weighed out in stoichiometric proportion to form the desired composition. These starting materials were mixed by a mechanical activation process for 60 minutes with an automated mortar grinder (Retsch, RM 100), shown in Figure 1. The grinder uses pressure and friction that involved a rotating mortar bowl at a speed of 90 rev/min. The pestle is situated slightly off the centre of the mortar and affects the mixtures by its own weight. The presence of the scrapper makes sure the mixtures is scrapped off from the inside wall of the mortar to prevent “caking”. This method of forcing the powder ensures that the entire input volume is mixed well and that each particle is fed back repeatedly into the milling and mixing process. 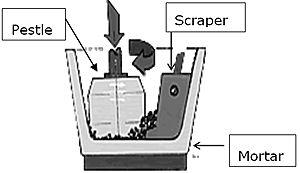 Figure 1. Milling mechanism of mortar grinder. The mixtures were calcined at 750oC, 800oC, 850oC and 900oC for 3 hours. The crystalline phases of the calcined powders were identified by XRD using X-Ray diffractometer (Philips, PW1710 with Cu-Kα radiation). Pellets were formed by pressing approximately 0.8g of the calcined powder in a 13mm diameter harden steel die at the load force of 40 kN. For dielectric properties measurement, Ba0.70Sr0.30TiO3 samples were sintered at 1250oC, 1300oC and 1350oC for 3 hours. The heating rate was set at 10oC/min. Electrical contact to the pellet-shaped samples was made by applying a gold paste to the two faces of each sample and firing at 800oC. Measurements of the dielectric constant and dissipation factor at room temperature were carried out using an impedance phase gain analyzer (Sclumberger S112600) by applying 1V RMS at 1kHz. The polished and etched microstructures of sintered samples were examined by scanning electron microscope, SEM (Cambridge Stereoscan S200). Results and Discussion The XRD patterns of the mechanically activated mixtures calcined at various temperatures are shown in Figure 2; the soaking time at each temperature was kept constant at 3 hours. In the XRD pattern of powder calcined at 750oC, the peaks located at about 24o, 34o, 42o and 47o corresponded to BaCO3; the 47o peak could also belong to SrCO3. The appearance of the most intense peak at 2θ 31.795o is attributed to the formation of the Ba0.70Sr0.30TiO3 phase. It thus indicates that at 750oC, the calcined temperature was insufficient to form a single phase Ba0.70Sr0.30TiO3. For the activated mixture calcined at 800oC, the appearance of new peaks at 2θ 22.100o and 51.180o provide further evidence of the existence of the Ba0.70Sr0.30TiO3 phase. The minor peak at 2θ 23.995o is attributed to remnant BaCO3; peaks which corresponded to the other starting materials are no longer detected. Further increasing of the calcination temperature to 850oC resulted in the formation of the single phase Ba0.70Sr0.30TiO3. There was no significance difference in the XRD pattern for the activated sample calcined at 900oC compared to 850oC. 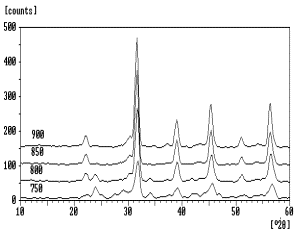 Figure 2. XRD patterns of BaCO3-SrCO3-TiO2 mixtures calcined at various temperatures. The formation of single phase Ba0.70Sr0.30TiO3 at 850oC is at a significantly lower temperature than required by conventional solid state reaction via ball milling, namely at 1050-1150oC [11-12], and is almost comparable with wet chemical methods that temperatures of 700-800oC [13]. However, the processing sequences employed by our mechanical activation method are similar to the conventional solid state reaction method and much simpler compared to the wet chemical methods. The low formation temperature for Ba0.70Sr0.30TiO3 that we achieved obviously results from the refined powder produced by the mechanical activation process. One of the common problems faced in ball milling is the “caking” effect where the powder strongly adhered to the wall of the milling jar as well as the milling balls. This will cause some level of inhomogeneity of the mixture. By comparing the efficiency of conventional ball milling and the automated mortar grinding, it is obvious that the latter equipment has advantages. For the automated mortar grinder as illustrated in Figure 1, the feed powder is conveyed into the grinding gap between the mortar and the pestle by the rotating mortar and the scraper. The scraper will ensure whole mixed powder quantity is repeatedly subjected to the milling process and is homogenously mixed as well. Furthermore, “caking” effect was avoided as the scraper would scrap off powder that adhered on the mortar. The ability to reduce the calcination temperature by 200oC is believed to be able to overcome the particle coarsening effect induced by high temperature calcination and at the same time, it shorten the calcination process. The single phase Ba0.70Sr0.30TiO3 powder formed at 850oC was compacted and sintered at 1250oC, 1300oC and 1350oC for 3 hours. Microstructure analysis was carried out and the results are shown in Figure 3(a)-(c). Highly uniform grains of about 3.8μm in size are observed in pellets derived from 60 mins mechanical activation which sintered at 1250oC, shown in Figure 3(a). Pores appeared to be very small and located at the grain boundary. In Figure 3(b), larger grains averaging 5.8μm were developed in pellet sintered at 1300oC. However, the spread of grain size is relatively high as some grains grew larger than others. As the sintering temperature was increased to 1350oC, the pellet showed formation of larger grains. In Figure 3(c), the grain size was not uniform due to abnormal grain growth, the average grain size obtained being about 9.8μm; with some individual grains as large as 30μm. Overall, the grain size of pellets derived from 60 mins mechanical activation increased with increase in sintering temperature. 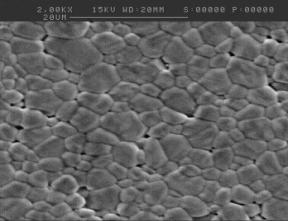 (a) 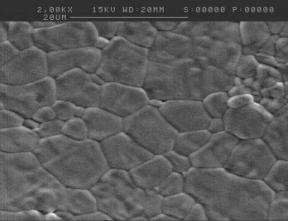 (b) 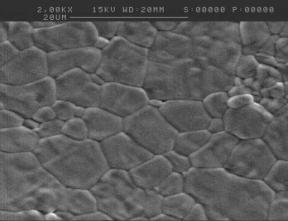 (c) Figure 3. SEM micrograph of Ba0.70Sr0.30TiO3 pellets derived from 60mins mechanical activation which sintered at: (a) 1250oC, (b) 1300oC and (c) 1350oC. Figure 4 shows the Ba0.70Sr0.30TiO3 dielectric constant and dissipation factor as a function of sintering temperature. The highest dielectric constant was achieved at a sintering temperature of 1250oC. The dielectric constant value decreased as the sintering temperature increased, whereas the dissipation factor showed an increase in value as the sintering temperature increased. The degradation of the dielectric constant value at higher sintering temperature was probably due to formation of non-uniform grain size as well as the large grains shown in Figure 3. However, the dielectric constant of Ba0.70Sr0.30TiO3 derived from the mechanical activation process is higher compared to the samples which were formed by conventional ball milling process. In our previous studies [14], we reported a dielectric constant of about 10,000 for Ba0.70Sr0.30TiO3 synthesized by conventional ball milling. By comparing the dielectric constant values, the mechanical activation process is shown to be a more value added process compared to conventional ball mill. 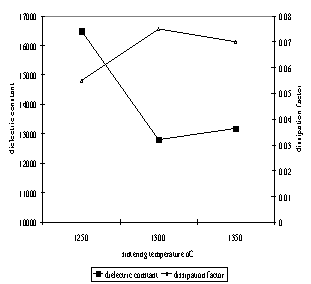 Figure 4. Dielectric constant and dissipation factor of Ba0.70Sr0.30TiO3 as a function of sintering temperature. Conclusions The mechanical activation process is proven to be a value added process in solid state synthesis of Ba0.70Sr0.30TiO3. Moreover, due to more intimate mixing, the starting materials are able to produce single phase Ba0.70Sr0.30TiO3 at lower calcination temperature. A higher dielectric constant is also achieved by mechanical activation method as compared to the conventional ball milling. Acknowledgements The author is grateful to Ministry of Science, Technology and Environment for the financial support. Special thanks Dr. Mat Johar, Mr. Rashid, Mr. Shahrul, Mr. Razak and Madam Fong Lee Lee for their technical support and useful discussions. References 1. M. Nayak, S. Y. Lee and T. Y. Tseng, “Electrical and dielectric properties of (Ba0.5Sr0.5)TiO3 thin films prepared by a hydroxide-alkoxide precursor-based sol-gel method”, Mater. Chem. & Phys., 77, 34-42, 2002. 2. L. Goux, M. Gervais, F. Gervais, A. Catherinot, C. Champeaux and F. Sabary, “Characterization of pulsed laser deposited Ba0.6Sr0.4TiO3 on Pt-coated silicon substrates”, Materials Science in Semiconductor Processing, 5, 189-194, 2003. 3. A. Ries, A. Z. Simoes, M. Cilense, M. A. Zagheteand and J. A. Varela, “Barium Stronitum titanate powder obtained by polymeric precursor method”, Mater. Charac., 50, 217-221, 2003. 4. D. H. Bao, Z. H. Wang, W. Ren, L.Y. Zhang and X. Yao, “Crystallization kinetics of Ba0.8Sr0.2TiO3 sols and sol-gel synthesis of Ba0.8Sr0.2TiO3 thin films”, Ceram. Int., 25, 261-265, 1999. 5. X. Y. Wei and X. Yao, “Nonlinear dielectric properties of Barium Strontium Titanate ceramics”, Mater. Sci. Eng. B, 99. 74-48, 2003. 6. G. Yang, H. S. Gu, J. Zhu and Y. Q. Wang, “The fabrication and characteristics of (Ba0.5Sr0.5)TiO3 thin films prepared by pulsed laser deposition”, J. Crys. Growth, 242, 172-176, 2002. 7. S. Suasmoro, S. Pratapa, D. Hartanto, D. Setyoko and U. M. Dani, “The characterization of mixed titanate Ba1-xSrxTiO3 phase formation from oxalate coprecipitated precursors”, J. Euro. Ceram. Soc., 20, 309-314, 2000. 8. S. E. Lee, J. M. Xue, D. M. Wan and J. Wang, “Effects of mechanical activation on the sintering and dielectric properties of oxide-derived PZT”, Acta Mater., 47, (9) 2633-2639, 1999. 9. Q. W. Zhang, T. Nakagawa and F. Saito, “Mechanochemical synthesis of La0.7Sr0.3MnO3 by grinding constituent oxides”, J. Alloys and Comp., 308, 121-125, 2000. 10. V. Berbenni, A. Marini and G. Bruni, “Effect of mechanical milling on solid state formation of BaTiO3 from BaCO3-TiO2 (rutile) mixtures”, Thermochim. Acta., 374, 151-158, 2001. 11. O. P. Thakur, C. Prakash and D. K. Agrawal, “Dielectric behaviour of Ba0.95Sr0.05TiO3 ceramics sintered by microwave”, Mater. Sci. Eng., 96, (3), 221-225, 2002. 12. B. Su and T. W. Button, “The processing and properties of Barium Strontium Titanate thick films for use in frequency agile microwave circuit applications”, J. Eur. Ceram. Soc., 21, 2641-2645, 2001 13. Y. B. Khollam, S. V. Bhoraskar, S. B. Deshpande, H. S. Potdar and N. R. Pavaskar, “Simple chemical route for the quantitative precipitation of barium-strontium titanyl oxalate precursor leading to Ba1-xSrxTiO3 powders”, Mater. Lett., 4079, 1-9, 2002 14. W. T. Teoh, A. Mat Johar, A. A. Zainal and M. N. Ahmad Fauzi, “Microstructure development and dielectric properties of Ba1-xSrxTiO3”, The 4th International Materials Technology Conference & Exhibition (IMTCE) 2004. Contact Details |