Founded in 1607, the Weisses Bräuhaus in Kelheim has been brewing Weissbier since 16 April 1608, and was owned by the Schneider family since 1927. The brewery has built a new heating station to deliver hot water and high temperature water to the brewery and the administration building. This boiler produces approximately 5400KW of heat output.
The core of the system includes a wood chip furnace equipped with a high temperature boiler. Besides the basic load, a 4000KW peak load boiler which runs on heating oil has been integrated to control energy peaks. For better efficiency, a waste-gas heat exchanger was also set up to produce the low temperature, hot water.
Measurement Requirements
When invoicing the wood chips utilized in firing the boiler, it is the amount of heat generated which is used rather than the quantity of wood chips. The heat energy thus produced at the boiler outlet is the basis for calculation. Given that it is a custody transfer measurement, an approved heat volume system was used. Apart from the water’s flow rate, the temperature in the return and supply line should be determined in both heating circuits in order to ascertain the heat energy (Figure 1).
.jpg)
Figure 1. Measuring the produced heat quantity in a heating circuit
- Supply line
- Flowmeter
- Supply line temperature sensor
- Heat consuming unit
- Return temperature sensor
- Return
- Separate heat quantity calculator
KROHNE Solution
In order to determine the quantity of heat generated, two calibrated temperature sensors and KROHNE’s UFM 3030 ultrasonic flowmeter were utilized in each circuit. The UFM 3030 devices were also equipped with separate signal converters to facilitate better instrument read-out. The flowmeters, together with the temperature sensors, were joined to individual "CALEC" energy calculators having the required approval as per EN 1434.
These calculators show the present heat quantity obtained for each heating circuit and also the collective kilojoule value, which is later transmitted to the overriding control system.
Customer Benefits
The Schneider brewery can easily determine and invoice the required wood chips for firing, depending on the amount of heat generated. The following factors were important in the process:
- Available heat quantity in the circuits can be measured any time
- Absolute custody transfer hot water energy balancing was accomplished for both circuits with minimum amount of effort
- The technology installed required only minimum maintenance
- The system conforms to EN 1434 standards
Instruments Used
UFM 3030
- Universal 3-beam in-line ultrasonic flowmeter for liquids
- No pressure loss, no moving or intruding parts
- Independent of pressure, density, temperature, viscosity, and conductivity
OPTITEMP TRA S12 temperature sensor
- Paired design
- High measuring precision
.jpg)
Figure 2. UFM 3030 ultrasonic flowmeter
.jpg)
Figure 3. OPTITEMP TRA S12 temperature sensor
Figures 2 and 3 show the UFM 3030 ultrasonic flowmeter and the OPTITEMP TRA S12 temperature sensor, respectively.
Large Dynamic Range
With a large dynamic range of 250:1, the UFM 3030 provides excellent flexibility. The flowmeter’s diameter can be selected to match the line size to promote optimum performance at low flow rates with minimum pressure loss. Also, in order to cut down the installation space and cost, a compact flow meter can be selected to facilitate reduced up and downstream pipe sections. Approval has been arranged to support this so that excellent flexibility is provided with free selection of measuring range (10, 25, 50, 100, 250) and nominal flowrate (Qp).
Low Minimum Flowrate, Large Temperature Range
The UFM 3030 has a low minimum flowrate (Qi) of 4cm/s for precise measurement at times of low energy need when low flows may occur. For cooling and heating purposes, the UFM 3030 has a wide temperature range from 0 to 180°C. However, the technical limitation is -25 to 220°C. The flowmeter operates safely and efficiently within its limits for a long period of time.
Fully Welded Construction
The UFM 3030 flowmeter tube is a fully welded construction. No sealing, gaskets, or o-rings were utilized to fit the acoustic transducers which mean there is no risk of leakage. Thanks to the direct acoustic path without reflectors, development of conductive, non conductive, magnetite or other scaling does not affect the performance of the flowmeter. Also, no recalibration is required.
The UFM 3030 is lightweight and easy to handle, without any cables or other components protruding beyond the flanges. It has a rugged all metal construction, which eliminates damage to the device during installation. It is supplied ready to measure. Once the flowmeter is electrically and mechanically joined, it does not require any specific handling such as making cable connections and fitting transducer parts. For remote installation, a cable with pre-fitted connectors is supplied. This way, signal connections can be easily made without the necessity for special handling.
Standard Three Acoustic Paths
Additionally, standard three acoustic paths (Figure 4) have been installed to calculate the flow at three different levels within the flow sensor tube. This gives a high level of independence from flow profile distortions induced by upstream disturbances. In case one path fails, the flowmeter will continue operation with the remaining paths, delivering the same performance. Moreover, the sophisticated DSP technology makes the flowmeter operation independent from gas bubbles. This feature along with its self- diagnostic abilities, operation within specification is ensured.
.jpg)
.jpg)
Figure 4. Standard 3 paths provide optimal performance, redundancy and reliability.
Conclusion
KROHNE’s UFM 3030 ultrasonic flowmeters, along with the OPTITEMP TRA S12 temperature sensor, can be effectively used for measuring the amount of heat produced in the heating system. The UFM 3030 is easy-to- use, lightweight, maintenance free and does not require recalibration. In addition, the rugged, all metal construction eliminates risk of damage during the installation process.
About KROHNE Messtechnik
KROHNE is a world-leading manufacturer and supplier of solutions in industrial process instrumentation.
KROHNE offers supporting products and services for one-stop-shopping and in industries as widespread as oil & gas, water & wastewater, chemical & petrochemical, food & beverage, power, minerals & mining and marine.
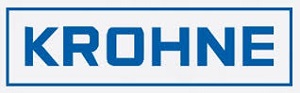
This information has been sourced, reviewed and adapted from materials provided by KROHNE Messtechnik GmbH.
For more information on this source, please visit KROHNE Messtechnik GmbH.