A revolutionary shift from naphtha and petroleum feedstock to natural gas driven supply chain is occurring in the global chemicals market. Huge natural gas reserves have been unearthed, thanks to the hydraulic fracturing technology. Market share is often captured by chemical manufacturers who are able to successfully capitalize these reserves.
Natural gas is commonly used to generate process heat and electricity, which are low-value products. However, it can be utilized in the production of low-cost, high value chemicals when energy-efficient and more active catalysts are utilized. Reformance-SMR™ catalysts developed by Nexceris increase the process efficiency of natural gas by controlling the composition, surface area, and the dispersion of catalytic sites. These catalysts enable process designers to effectively reduce the size of a reactor and/or decrease the operating temperatures, enlarging the scope for designing low-cost reforming systems. This technology enables the capture of the methane value in the vicinity of point-of-use applications and natural gas point-of-extraction gas to liquid systems.
During the steam methane reforming (SMR) reaction, methane reacts with steam to form syngas, i.e. a mixture of H2O, CO2, H2, and CO. This syngas is further decomposed to ammonia, H2, liquid fuels, and methanol. To reduce pressure drop during the process, traditional SMR catalysts such as Ni/Al2O3 promoted with MgO and/or CaO are formed in the shapes of pellets, large rings, and cylinders with holes. Due to the low thermal conductivity of the ceramic forms, the heat transfer in the pellet or ring beds becomes very low. Cold spots are formed in the catalyst beds at higher gas flow rates as SMR is highly endothermic (ΔH° = 206 kJ/mol). This leads to poor conversion.
The use of these catalysts in packed-bed reactors greatly increases the size of the reactors, as the reactors consist of arrays of multi-story packed bed tubular reactors, including huge direct-fire burners that provide process heat. The high aspect tubular reactor designs and tremendous energy input required to reduce cold spots arise from the catalysts’ poor thermal conductivity. The resulting need for high-temperature operation drives the use of costly high-nickel alloy materials. To make these processes affordable, economies of scale result in large-scale centralized plants.
New structured catalysts to convert methane into syngas have been developed by Nexceris to improve SMR efficiency. A unique method is employed to synthesize the catalysts, and they are washcoated on metallic substrates with exceptional thermal conductivity. Unlike the traditional synthesis methods, the Nexceris’ method enables synthesizing unique and high-performance catalysts. The metallic substrates are selected to ensure high mechanical strength, low pressure drop, and increased heat transfer. This notably increases the productivity of syngas, remarkably downsizing the reactor and reducing the materials requirement.
These characteristics enable the formation of novel system designs, such as decentralized syngas production near stranded gases or portable power systems in a cost-efficient manner.
Reformance-SMR™ Performance
For the purpose of comparing the performance of the catalyst, a mixture containing Reformance-SMR™ and traditional catalyst granules with a mesh size of 35 to 60 and α-Al2O3at a weight ratio of 1:20 was loaded in a tubular reactor. The catalyst performance testing conditions were set as GHSV = 200,000 - 1,200,000 h-1, pressure = 1 atm, and H2O/CH4 = 3/1. A gas chromatograph was used to analyze the gas compositions.
To perform the SMR test, two different types of metal foams with a pore size of 1.2 mm, 4.3 m2/L geometric surface area, and 90% porosity were washcoated with the Reformance-SMR™ catalyst. The AlumiLok™ aluminization process developed by Nexceris was used to aluminize the foams. Ball-milling of the catalyst powders was carried out to washcoat the catalyst powders on the foams through a dip-coating process. The dip-coated foams were dried and calcined at high temperatures. The SMR testing conditions were GHSV = 30,000 h-1, pressure = 1 atm, and H2O/CH4 = 3/1.
The testing results indicated that the SMR reactivity of the Reformance-SMR™ catalyst was very high compared to a commercially available Ni catalyst under similar testing conditions. At a GHSV 400,000 h-1, 88-98 percent methane conversions were obtained at 650-750°C on Reformance-SMRT. It was only 10 to 33% in the case of the commercial catalyst (Figure 1). In addition, CO selectivity for the Reformance-SMR™ catalyst was greater compared to the commercial catalyst.
.jpg)
Figure 1. SMR performances of Nexceris granular catalyst and a commercial Ni catalyst under similar testing conditions of GHSV = 400,000h-1, pressure = 1atm, H2O/CH4 = 3/1, and temperature = 750°C.
As the methane conversions for the Reformance-SMR™ catalyst were nearer to the thermal equilibrium at a GHSV of 400,000 h-1, the gas flow rate was increased to GHSV = 1,200,000 h-1. Consequently, a 69% methane conversion was observed for the Reformance-SMR™ catalyst (Figure 2). Initially, there was a marginal decrease in the methane conversion to 68% in 6 hours, but then the conversion stabilized. The initial methane conversion observed for the commercial catalyst was 15%, which decreased to 9% in a span of 14 hours (Figure 2). These results imply that the Reformance-SMR™ catalyst is seven times more reactive, and also highly stable compared to the conventional Ni catalyst under similar testing conditions.
.jpg)
Figure 2. SMR performances of the Nexceris granular catalyst and a commercial Ni catalyst under similar testing conditions of GHSV = 1,200,000h-1, pressure = 1atm, H2O/CH4 = 3/1, and temperature = 750°C.
A preliminary lifetime testing revealed that there was no deactivation in 500 hours on stream. Apart from the high stability and exceptional SMR activity, the Reformance-SMR™ catalyst was also resistant to coke formation under drastic testing conditions, with a very low steam to carbon ratio of H2O/CH4 = 1.2/1.
When the Reformance-SMR™ catalyst was washcoated on two metal foams to analyze the mass and heat transfer effects, the metallic substrates provided low pressure drop, high thermal conductivity, high mechanical robustness, and high geometric surface area. The AlumiLok™ aluminization process employed to form a porous Al2O3 layer on the external surfaces improved catalyst adhesion at high loading. Figure 3 depicts a photographic view of a representative foam structure and a micrograph of the support before application of the catalyst.
.jpg)
.jpg)
Figure 3. Photo (top) and SEM micrograph (bottom) of AlumiLok™ coated alloy foams.
The resulting structured catalyst samples also displayed exceptional SMR performance. Equilibrium methane conversion was observed for the catalyst coated foams at GHSV = 30,000 h-1 (Figure 4), which is 10 times that of commercial operation conditions of GHSV = 3,000 h-1. This indicates the possibility of a 10-fold reduction in the reactor volume for the same syngas production by utilizing the Reformance-SMR™ catalyst.
.jpg)
Figure 4. SMR performance on aluminized metal foams coated with Nexceris catalyst under the testing conditions of GHSV = 30,000h-1, pressure = 1atm, and H2O/CH4 = 3/1.
Download the White Paper for More Information
Commercial Implications
Reformance-SMR™ catalysts can be used for any application that requires synthesis of hydrogen and syngas from methane. To increase the production volume of existing reactors, conventional Al2O3/Ni rings/pellets can be replaced with the Reformance- SMR™ structured catalysts. Another possibility is to modify the system to decrease the number of active tubes and to reduce the required heat input to achieve the preferred production levels. In retrofitting situations, the substrate can be customized to accommodate the existing reactor. This improves packing uniformity and reduces pressure drop, a key area of concern in the performance and lifetime of the SMR system.
These factors enable newly built reactors to develop compact reformers to correct flow rates, which could be expensive for traditional SMR catalysts. The compact size and higher efficiency of the Reformance-SMR™ catalysts considerably reduce the investment and the operating costs either for generation of syngas from stranded natural gas in remote areas, or to provide reformate at point-of-use hydrogen generators.
Conclusion
The high intrinsic catalyst activity, combined with the exceptional thermal conductivity of the substrate provides an advanced SMR catalyst, which remarkably enhances syngas productivity. Compared to conventional Ni rings/pellets, the enhanced syngas productivity provided by Nexceris’ catalyst technology reduces the reactor system size, with similar syngas output or increases syngas output at the same reactor size. Both characteristics significantly reduce the investment and energy inputs for an equal amount of syngas production. The use of Nexceris catalyst technology can reduce the cost of transforming natural gas to valuable chemicals via syngas, enhance the cost-effectiveness of current systems, and allow the use of advanced distributed reforming technology.
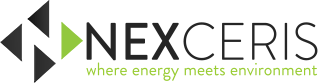
This information has been sourced, reviewed and adapted from materials provided by Nexceris, LLC.
For more information on this source, please visit Nexceris, LLC.