The use of thermal fluids has been shown to be extremely safe in a variety of industries, but despite this fact, it is very difficult to prevent fires from occurring in these systems. This is because air, fuel, and an ignition source, which are essential ingredients for a fire, are present by design. However, through sound design, set up, and maintenance processes, the risks posed by fire can be reduced considerably.
Causes of Fires
Insulation fires generally occur when thermal fluid enters into porous insulating materials like mineral wool, glass fiber, or calcite. The porous material enables the fluid to move away from the leak source and disperse across the insulation. Through the use of aluminum cladding, fresh air is prevented from reacting with the hot degrading oil; however, if an opening is accidentally cut into the cladding or if it is removed for maintenance purposes, then the drenched insulation can ignite spontaneously.
Leaks occur due to catastrophic failures of rotary unions, pump seals, expansion joints, and flex hoses. Ignition sources can potentially include an electrical panel box left open; bearings that turn red hot as they seize up; and an open motor kept a few floors under the leak.
Heat Transfer Fluid and Hot-Oil Systems
Following are the User’s Guide Series:
- Preventing fires in heat transfer systems
- Examining the fluid
- Cleaning, draining, flushing and charging
- Water in thermal fluid systems
- Fouling in heat transfer systems
- Oxidation in heat transfer fluids
- Leakage of thermal fluid system
- Proposed high-temp system components and suppliers
- Importance of flash and fire points in heat transfer fluids
- A comparison: Thermal fluid vs. steam
- Causes and cures of fluid degradation
- How to easily track the performance of heat transfer system
Undetected Loss of Flow
Safety interlocks integrated into thermal-fluid heaters are specifically made to shut down the heat source, if there is a low flow via the heater and/or if there is an extreme outlet temperature.
Fires, though rare, can occur due to flow loss caused by a malfunctioning back-pressure control valve, pump or pump-coupling failure, or a plugged Y-strainer; and failure of the safety interlocks due to deliberate bypassing or lack of maintenance. During these situations, while the heater is energized, the temperature of the shell, heater tubing, or connecting piping will quickly increase and may break due to thermal stress. Once the leaking fluid is exposed to air, it will ignite, and if the system remains undamaged, the vaporized fluid will come out through the relief valve and/or back up via the expansion tank.
Cracked Tubes in Fired Heaters
Hot spots causing inconsistent thermal expansion of the tube or localized overheating can lead to cracks. Isolated hot spots can occur when there are carbon deposits or flame impingement within the tubes that insulate a small region. While the heater is running, thermal fluid entering into the combustion chamber via the ensuing cracks will burn as fuel. However, when the burner is turned off, the leaking fluid can collect in the combustion chamber. In serious situations, the fluid, which gets accumulated, creates a huge pool within the heater during an extended shutdown period. During start-up, the pool catches fire, destroying the heater.
Design, Installation and Maintenance Tips
Buildings: In order to prevent the accumulation of ignitable vapors (such as vapors from a fuel tank), areas that have the potential for leakage should be sufficiently ventilated. Smoke around a leak is generally considered to be a good sign, as it indicates that vapors are not building up. Hydraulic lines and systems should not be set up close to a heater because they can probably spray fluid at long distances. To contain any major spills, the floor area around skids, pumps, and heaters should be diked.
Piping: Valves should be set up in such a way that stems are kept slightly below horizontal. This will enable the leaked fluid to drip off from the valve body. Expansion joints should be set up such that they shift axially and not in sideways.
Insulation: Foamed glass can prevent the leaked fluid from dispersing out, and hence can be used. This impermeable material must be installed around components such as pressure taps, strainers, valves and so on that have the potential for leaks.
Porous insulation like calcite, fiberglass, and mineral wool should be carefully utilized in hot-oil systems if required. It can be utilized on straight pipe runs; however, care must be taken to leave 18” on both sides of a prospective leak point. Insulated flanges should not be used. Instead, metal covers can be installed for personnel protection, if required.
Overflow Tank: This should be a vented, closed-head type with a drain valve and should be installed away from the heater control panel and exit doors. The overflow tank should never be vented within the heater room.
Pump Seals: These should be substituted as soon as they begin to leak, particularly when the leaking fluid may enter into the bearing housing. Drip pans should remain free of fluid, and noise or vibration should be checked out instantly.
Paratherm | Heat Transfer Fluids | Hot-Oil Technology Made Easy
Fluid Maintenance
Keeping the thermal fluid in good condition can considerably reduce fire risks. A thermal fluid, which is poorly degraded, poses less margin of error for system issues and upsets. For instance, system pressure can be increased by growing levels of low boilers and this, in turn, can make the relief valves to lift at a lower fluid temperature. Low boilers can also create more amounts of vapors around a leak. Oxidation can build up carbon sludge, which brings down the working volume of the expansion tank. While some level of degradation is to be expected, this could be reduced.
Low boilers are basically lower-boiling-point fluid components, which are created when fluid molecules break up as a result of extreme temperatures. Low flow via the heater can lead to fluid cracking and this, in turn, reduces the energy conveyed to the fluid and leads to increased tube temperature. Flame impingement on the heater coil is another leading cause of fluid cracking.
Oxidization of fluid is indicated by carbon sludge, and this oxidized fluid generates carbon as it travels via the heater even at standard operating temperatures. Subsequently, the carbon can plate out within the coil (fouling), causing hot spots. A large part of the carbon continues to be suspended in the fluid, forming sediment in low-flow areas, like the expansion tank.
These conditions can be identified by simply analyzing the fluid for degradation; however, if issues are already present in the system then it is too late for testing. So, the best time would be to test the fluid even before the issues start. Alternatively, the fluid can be tested each year beginning with year one. A useful troubleshooting tool can be obtained through trend analysis of the test results which could help identify and rectify system issues that contribute to premature degradation. If symptoms already exist, a fluid test will simply specify that the fluid is poorly degraded and hence should be substituted.
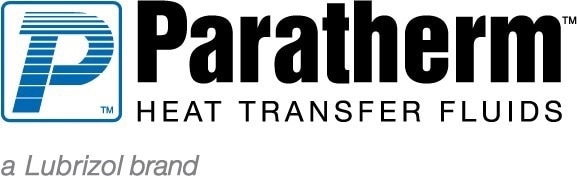
This information has been sourced, reviewed and adapted from materials provided by Paratherm.
For more information on this source, please visit Paratherm.