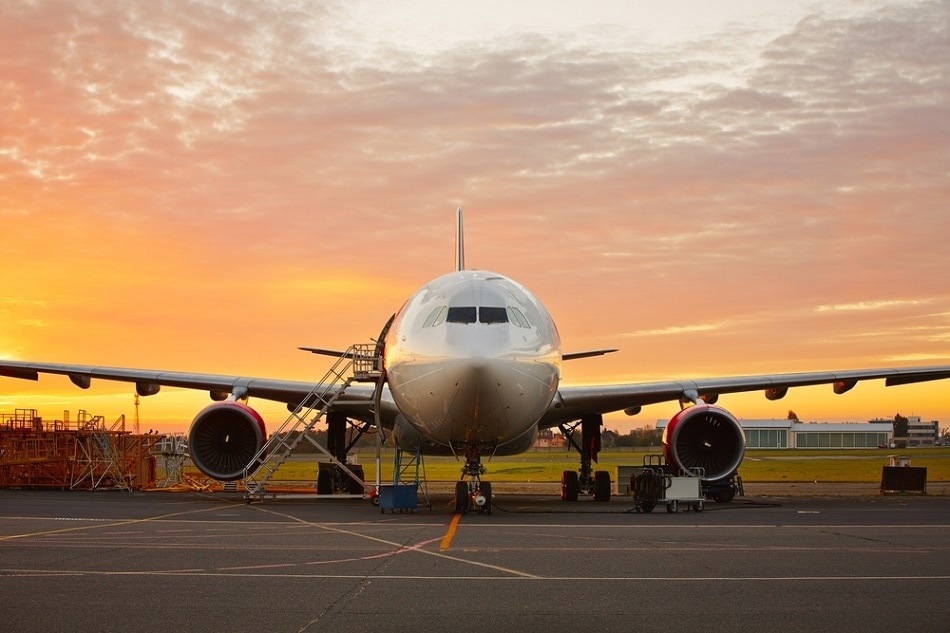
The consistent inspection of aircraft components and machinery is imperative to maintain prior to the assembly of the aircraft, as well as throughout the lifetime of its use.
Aircrafts are cycled, meaning that parts of the aircraft are loaded and unloaded during their flight and landing periods, therefore, they are generally designed to be light despite their responsibility in performing various different functions when in use. To ensure the safety of aircrafts when in orbit, technicians must be able to precisely locate, quantify and repair damage found on the aircraft.
To do this, aerospace professionals utilize certain nondestructive testing (NDT) techniques including Eddy currents and electromagnetic acoustic transmission1 (EMAT).
Eddy Currents
Eddy currents, which are also referred to as Foucault currents, are swirled loops of electrical currents found that are induced by a time-varying magnetic flux within the conductor. The interaction between the eddy current and the changing magnetic field results in a force that acts radially, as well as in three different spatial directions.
Eddy currents are found in a variety of applications such as braking systems that use drag force generated by the currents as a means to stop or slow down moving objects, repulsion effects and levitation, metal identification, structural testing and much more.
Eddy current inspection testing within the aerospace industry, as well as its other manufacturing and service applications, is capable of detecting cracks present within metal sheets and tubing, metal and nonconductive coating thickness measurements, conductivity measurements and corrosion identification2.
Established in 2009, Eddyfi is a technological company that is committed towards further developing the eddy current array (ECA) technology for its ability to inspect oil & gas, heavy industries, nuclear and power generation, aircrafts and spacecrafts. Eddyfi has developed a successfully electromagnetic testing solution that connects Aircraft Operators, Component Manufacturers and Inspection Companies with the possible defects found in aerospace parts.
Eddyfi utilizes their ECA surface probes, test instruments and acquisition/analysis software to connect these various personnel to evaluate defects present in difficult to reach places present within commercial and military aircrafts. Such locations on the aircraft include components within the turbine and jet engines, multilayered aluminum structures, paint coatings and fasteners3.
Electromagnetic Acoustic Transmission (EMAT)
The EMAT transducers for this type of nondestructive ultrasonic testing utilize a magnetostrictive effect to transmit and receive ultrasonic waves. These transducers are comprised of a case with a socket, induction coil, protective cover, magnetic flux concentrator and permanent magnet. To induce currents on the surface of the test object, alternate current feeds within the induction coil oscillate.
These initiated currents then interfere with the permanent magnetic field, thereby creating ultrasonic waves to propagate onto the surface of the test object. A final picture illustrating potential flaws present on the material, as well as characterization of the material’s properties, is created by the reflection of the waves to and from the walls of the induction coil4.
Applus+, a leading producer of inspection, certification and testing technologies around the world, provides a number of services to power, automotive, oil & gas, aerospace and several other industries. The Applus+ EMAT devices to be used for aerospace inspection purposes including the detection of flaws within steel materials of the aircraft, detection of the lamination in bonded composites and plates, inspection of welds and wall-thickness, as well as material characterization5.
Similarly, Victor Aviation equips their aircrafts with EMAT sensors to examine material defects present with the aerospace parts by using the beams of the mechanical waves, which are both short in wavelength and high in frequency, to measure the reflected pulse that represents the size, distance and reflectivity of flaws that are found upon inspection6.
Image Credit:
JaromirChalabala/ Shutterstock.com
References:
- “Nondestructive Testing in the Aerospace Industry” – NDT Resource Center
- “Introduction to Eddy Current Testing” – Olympus
- “Propelled by Eddyfi’s Eddy Current Array Technology” – Eddyfi
- “EMAT (Electro-Magnetic Acoustic Transducer” – Nordinkraft
- “Electromagnetic Acoustic Transducer EMAT” – Applus+
- “Ultrasonic EMAT Inspection” – Victor Aviation
Disclaimer: The views expressed here are those of the author expressed in their private capacity and do not necessarily represent the views of AZoM.com Limited T/A AZoNetwork the owner and operator of this website. This disclaimer forms part of the Terms and conditions of use of this website.