Increased use of low-density materials such as polymers and polymer composites is one way of developing the lightweight vehicles of the future, to achieve the forthcoming strict legislation on emissions and recyclability. Of the commodity polymers, polypropylene is by far the most attractive for the automotive industry. It not only fulfils these requirements but it is also inexpensive. Additionally, polypropylene can be used as a glass or mineral filled composite, which may be used for semi-structural applications. Fixing Polypropylene Panels Automotive manufacturers who wish to pursue this attractive material must consider appropriate methods of joining panels. Mechanical fastening is the traditional technique employed. However, not only do the fixings add weight to the assembly, they can also be damaging, especially for composites given that stress concentrations can promote premature failure. Therefore, adhesive bonding has become the most practical alternative. Altering the Surface Chemistry of Polypropylene A major problem is that polypropylene (along with other polyolefins) has a non-polar surface chemistry, which means the wetting characteristics of components made from this material are poor. Ultimately, this will result in poor adhesion of paints, coatings or adhesive bonding products. This problem has been overcome in the majority of instances by treating the surface of the substrate in order to alter the surface chemistry. Numerous methods have been used to increase the number of oxygen groups on the surface, including chemical treatment, corona discharge and plasma techniques. These techniques produce a variety of changes at the surface, including cleaning, removal of low molecular weight fractions, cross-linking and oxidation. Owing to polypropylene’s extensive use in films and flat sheets, certain techniques such as flame and corona have been favoured, despite both having problems of heterogeneous or patchy treatment across a surface. However, for complex 3-D automotive shapes such as bumpers, these methods are less useful, although flame treatment can be easily automated. Plasma Pre-Treatment Although widely used, flame treatment has several disadvantages in a commercial volume production environment. Parts have the potential to undergo overtreatment, incipient melting or melting during machine stops etc, as well as the hazards associated with combustible gas. An alternative method is plasma pre-treatment, which has been used in the electronic and medical industries for a few decades now and more recently in the automotive sector by Audi and BMW. Types of Plasma Pre-Treatment There are two types of plasma treatment available: • Vacuum • Atmospheric Vacuum Plasma Processing The vacuum plasma process requires the parts to be treated under low vacuum pressure in a chamber. A bleed gas is then introduced and ionised. These inert gas ions bombard the surface of the component causing chemical and topographical changes in the near surface region. The chemical changes are complex but involve removing atoms or breaking bonds, which results in free radical evolution and cross-linking. This method is limited by the size of the chamber and because it is a batch process it makes it unacceptable for continuous production methods. Atmospheric Plasma Processing As a result, the atmospheric plasma pre-treatment technique is highly attractive because it treats the parts in-situ rather than in a chamber. Additionally, the process works by ionisation of atmospheric gases rather than a bleed gas, which drastically reduces the cost of the procedure. For these reasons, an industrial consortium consisting of Linpac Automotive, Hamilton Machinery Sales, Solvay Engineered Polymers and Gurit-Essex (now Dow Automotive), led by researchers at Warwick Manufacturing Group and the University of Bristol, developed a pre-treatment and adhesive system that uses air plasma to solve the problem of joining a complex auto bumper to the frame of a vehicle by pretreating and bonding the bumper assembly. Friction Welding Until now, one of the most effective ways of joining a bumper assembly has been using friction welding, but despite it being a rapid process (~50 seconds) it can leave unacceptable amounts of unsightly weld swarf marks on the surface. This then becomes included at the painting plant as surface specific aesthetic defects, causing the part to be scrapped. Put simply, scrap or re-work costs money, therefore an alternative method was needed. The Lectro-Treat Air Plasma System The team solved the problem by tailoring the pretreatment parameters to the material blend and the adhesive to form a strong and durable bond as good as the original technique. The Lectro-Treat blown air plasma system (designated LTIII) lends itself well to automation and has been widely used for many years in the USA to apply paints and labels to plastic products. How It Works? Two wire electrodes are connected to the secondary winding of a high-voltage (12-15 kV) transformer. As power is applied an electric arc sparks between the electrodes. A constant flow of air is blown through the electric arc causing it to deflect or spread and because 50-60 arcs are produced per second the process supplies a virtually constant forced air plasma loaded with highly energetic ions. The plasma temperature is low, so doesn’t create a fire hazard or deformation/melting problems to the component. Area of Effect As shown in figure 1, the plasma head was attached to a robotic arm, making it highly suitable for use in continuous production environments and treating complex surfaces. The treatment width is ultimately limited by the distance between the electrodes. However, by placing two or more discharge heads next to each other, the effective treatment width from a single power supply is up to 225mm, which is greater than flame treatment, for example. 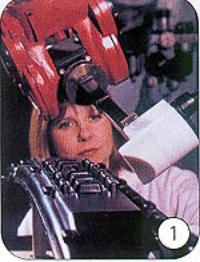 | Figure 1. The Lectro-Heat blown air plasma system mounted on a robotic arm. | Increased Adhesion Due to Lectro-Heat Increased adhesion is achieved by stripping the hydrogen from the polypropylene-carbon spine and replacing it with functional groups - for Lectro-Treat the hydroxyl (OH) group is used. XPS spectra taken before and after pre-treatment, clearly shows the increase in surface specific oxygen after pre-treatment. Benefits of the Lectro-Heat Process Parts pre-treated and bonded using this material successfully passed all the required standard automotive impact tests. The open time for the pre-treatment was two to four weeks depending on storage conditions. Crucially, the treated surface remained consistent during this period unlike flame and corona treated surfaces, which tend to become patchy across the treated surface after only a day or two. Therefore, this process allows greater flexibility in the potential uses of the parts, meaning bonding and/or painting don’t necessarily have be undertaken at the same site or on the same day. Treated parts can be transported or placed in stillage until required, which allows greater flexibility in the manufacturing process. Summary Currently, this technology is being applied in the UK electrical and packaging industries as well as some automotive applications, although there is significant scope to extend its use in the automotive industry. The process is relevant to any assembly line involving polypropylene and in particular such pre-treatment and bonding technologies will be key to future developments in lightweight vehicles. |