Smart coatings are structured coating systems that provide an optimum response to some external stimulus. They react to outside conditions, such as temperature, stress, strain or the environment, in a selective way. Smart Windows Smart windows are an excellent example of a smart coating behaviour. The panes of glass in the window are coated with a thermochromic material, whose heat reflectivity changes with the temperature of the glass. Thus the window can switch from heat adsorption to heat reflection depending on the ambient temperature. Coating glass with a compound such as V1-xNbx02 permits the metal insulator transition to be varied from 64°C down to -4°C by adding up to 7at% niobium, figure 1. Above this transition temperature, the coating is able to reflect infrared radiation from the sun, thus ensuring that the inside of a commercial building does not overheat in the summer, as an application example. In winter however, the coating transmits infrared, ensuring good thermal efficiency. 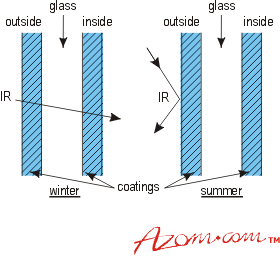 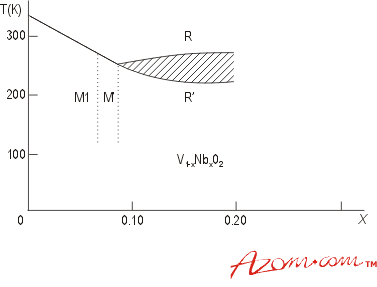 | Figure 1. Thermochromic coatings can be used to design smart windows (top) due to the variation of metal-insulator transition temperature with x in V1-xNbx02 (bottom). | Heat Mirrors Another example of smart coatings is a family of wavelength selective coatings that have been used to manufacture ‘heat mirrors’ (figure 1, bottom). A transparent coverplate is coated with either indium-tin-oxide (ITO) or a multilayer TiO2-Ag-TiO2 coating. Both coatings have a high transmission for the predominant wavelengths in sunlight. A 0.3µm ITO coating on glass provides in excess of 80% transmission for wavelengths of 0.4-1.1 µm. An 18nm layer thickness Ti02-Ag-TiO2 multilayer coating has a narrow transmission band of 0.3-0.65µm, but is more efficient at reflecting longer wavelength infrared radiation. Greater than 95% of wavelengths are reflected, compared with 70% at a 2µm wavelength for the ITO coating. By combining such a coated cover plate with a heat absorber it is possible to retain the heat, limiting re-radiation at higher wavelengths. It should be possible through a combination of these two concepts to produce smart windows that would reflect solar energy in summer, but transmit solar energy in winter, whilst limiting the re-radiation of low grade, long wavelength heat. For a double glazed window this would be possible by coating the outer pane with the vanadium niobate coating, whilst coating the inner pane with indium-tin oxide or the multilayer Ti02-Ag-Ti02 coating. These two examples illustrate some of the basic concepts of smart coatings. The coatings are not smart in themselves, and they have no built in intelligence as is possible when designing active smart systems consisting of microsensors, a microprocessor and a microactuator, which provide a preprogrammed response. Their smart behaviour results from the scientific combination of intrinsic coating properties. Smartness, as a property, rests with the coating designer. It is through clever coating design that ‘smart coatings’ can adapt to the requirements of their surroundings. Functionally Graded Materials In the areas of corrosion and wear resistance, functionally graded materials can be used to fabricate smart, environmentally tolerant coatings. Functionally graded materials acknowledge that different properties are often required at component surfaces or interfaces to those required in the bulk of the component. This can only ideally be achieved through the selection of alternative surfacing or interface materials. However, the choice of a new surface alloy adds further interfaces that again can be optimised. The net result is a multilayered, or continuously graded surface treatment that offers optimised performance. This use of functionally graded structures to provide smart coating concepts is best illustrated by example. There are many applications where materials are exposed to a combination of corrosion and wear. Due to changes in the local environmental conditions, different degradation mechanisms may occur across the surface of the component and as a function of time. Therefore, no single coating of uniform composition and structure can offer an optimum solution. There will inevitably have to be compromise to resist the range of environmental conditions. The coating of a twin screw extruder barrel used in the food processing industry is an excellent example of variable wear/corrosion conditions because the degradation mechanisms operating on the extruder barrel are invariably dependent on the product, ingredients and relevant process parameters being used. Degradation mechanisms may include corrosion, surface fatigue, abrasive and adhesive wear, with the magnitude of these processes changing both along the length and around the barrel profile, figure 2. To combat this complex attack, a structured coating has been designed, through collaboration between Cranfield University and APV Baker. The coating has been produced by powder metallurgy and HIP, with the structure and composition varying both through the coating thickness and laterally, to accommodate the localised environmental conditions. The outer layer contains tungsten carbide and various chromium carbides in a nickel-chromium alloy matrix. By varying the proportions of tungsten carbide, chromium carbide and the local composition of the nickel-chromium matrix, it is possible to engineer the desired wear and corrosion resistance. The graded inner zone ensures compatibility with the steel substrate. 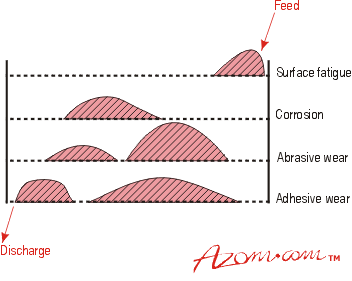 | Figure 2. Typical degradation mechanisms within a twin-screw extruder. | Smart Overlay Coatings A final example examines the manufacture of smart overlay coatings for industrial gas turbines. This is a newly funded programme under the Link surface engineering initiative, involving Cranfield University, Birmingham University and a consortium of British industry led by Diffusion Alloy Ltd. The concept is the development of functionally graded coatings, using a combination of plasma spraying and chemical vapour deposition (CVD), that can adaptively respond to the mode of corrosion attack within the industrial gas turbine. This is achieved by designing a graded coating system that forms alumina scales for high temperature protection (900-1200°C), but chromia and/or silica scales to combat type II hot corrosion at lower temperatures (650-800°C). It is the mode of corrosion attack, plus the graded coating structure, that permits this adaptive response. A corrosion map constructed at 750°C, showed that the optimal design required that the coating composition profiles vary through the coating to provide alloys that grow stable alumina scales at the coating surface. Beneath these the composition changes to alloys more resistant to type II corrosion. It is the mode of type 11 corrosion attack that permits this functionally graded coating to exhibit smart concepts. Summary The use of smart coating concepts in three industrial sectors, as diverse as architectural windows, food processing and industrial gas turbines, has been illustrated. These are not the only examples. The intelligent combination of materials and novel coating processing technologies is being used to manufacture numerous coating systems that embody smart concepts. Multilayer metal-ceramic structures can be devised to provide optimum wear and erosion resistance. The layer thicknesses are engineered such that the ceramic layers do not fracture and the metal layers provide enhanced toughness. New thermal barrier coatings are under development with nano-engineered structures that provide well controlled thermal conductivities, plus strain tolerance. Active and passive sensors and actuators are being manufactured using nano-engineering in conjunction with coating technology. In the scientific literature there are many materials that offer ‘smart properties’. Such materials require a change in property that can be easily stimulated by changes in the local environment, such as temperature, stress, strain or chemical potential. A few examples include metal-insulator transitions, thermochromic materials, non-linear dielectrics, piezoelectric materials, ferroelectric materials, martensitic phase transition, shape memory alloys, and the use of reversible hydride formation for heat/energy storage. These are but a few examples. Their use in smart coatings requires that only a social or commercial need be identified. |