Traditionally, ceramics have been fired using gas burners or electric resistance elements. However, as ceramics are thermal insulators, the heat transfer is not particularly effective and temperature profiles are generated in the material, with the surface being hotter than the centre. Microwave heating offers a potential novel solution to this problem by depositing the energy directly within the component. Using microwave energy alone creates problems due to surface heat loss, leading to inverse temperature profiles, and the impression of heating from the inside out.
Microwave Assisted Gas Firing
The key to rapid successful processing is to combine traditional radiant (gas or electric) energy with volumetric heating (microwave) simultaneously, in the same kiln. In microwave-assisted firing, the microwave energy is used to heat the product, while the radiant heat sources act primarily to prevent heat loss from the surface. This then in turn minimises, and indeed can prevent, the generation of temperature profiles within the product, allowing it to be fired faster in the most effective manner. The benefits of simultaneously combining radiant gas firing with volumetric heating have already been proven conclusively in a smaller experimental kiln which has been used to fire a wide range of ceramics for end users in the multinational consortium backing the research at EA Technology.
Benefits of Microwave Assisted Gas Firing
The results of the research have met, or exceeded, all of the advantages of the system envisaged at the start of the project, and have included increased firing rates (by at least a factor of four), quality improvements, energy cost savings of over 50%, and enhanced binder removal.
The First Pilot Production Kiln
Experience from the initial kiln has been incorporated into the design of the first pilot production kiln. The kiln, built by Drayton Kilns of Stoke-on-Trent, is capable of firing up to 1000kg of ceramic products per cycle and is presently undergoing trials on a range of products, figure 1. The main challenges were to make compatible the conventional gas engineering design, provided by Drayton, with the microwave engineering requirements of electric field distribution and safety, together with the advanced control requirements for the dual fuel processing. These design aspects were supplied by EA Technology. Both companies focused on obtaining cost effective solutions to the novel design, and were successful in doing so as the kiln was designed, built and commissioned within budget.
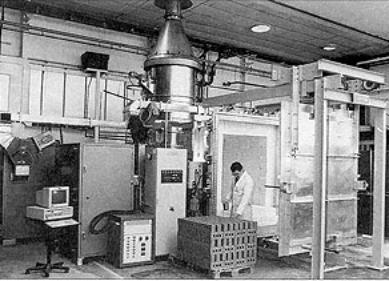
|
Figure 1. The pilot production microwave assisted gas fired kiln.
|
Results from the Pilot Production Kiln
The results of the trials carried out since May 1995 have again met or exceeded all of the advantages demonstrated in the smaller experimental kiln, including increased firing rates, quality improvements, energy cost savings and binder removal.
The Final Microwave Assisted Gas Fired Kiln
The final kiln to be built at EA Technology is a 15 metre long tunnel kiln, designed to operate to 1600°C, and is capable of being operated in either an intermittent or continuous push mode, satisfying the requirements of the ceramic companies in the consortium. The design has been finalised and the site construction commenced in December 1995 with an anticipated commissioning date of April or May 1996.
Control Systems
Again, the design undertaken by EA Technology focused on the microwave engineering requirements, but more importantly extensive work has been carried out since January 1995 to develop a control strategy to enable a temperature profile to be established in the microwave-assisted tunnel kiln. This brought together fundamental research underpinning most of the development work being carried out, which is focused on understanding how microwaves interact with ceramic materials throughout the firing cycle, with engineering design and control work.
The Future of the Project
Several of the ceramic companies taking part in the development have indicated that following their next series of trials on the pilot production kiln, which are part of the entry fee to the consortium, they will take up the option of a royalty-free license to transfer the technology to their production sites.
Industry Involvement
The consortium now has ceramic companies involved from the UK, Germany, and the USA. It is supported by sponsoring electricity companies, the Energy Efficiency Office, equipment manufacturers and ceramic companies. The support from the ceramic industry is extensive, making this the most exciting programme in this field in recent years, covering all generic types of ceramic.
|