Capacitance sensing has been in existence for more than 50 years. This article looks at the characteristics of capacitive sensing, the performance features, and fixturing of capacitive sensors.
Characteristics of Capacitive Sensors
Non-contact displacement measurements can be made rapidly and with high precision using capacitive sensors over a modest range.
The main features are:
- Capacitive sensing is a non-contact measurement method. As the system does not make contact with the part, there are no witness marks, parts distortion, or probe wear. Since there is no sensor cycle time, high volume measurements are achievable.
- Capacitive sensors measure quickly. They are ideal for high-bandwidth measurements applications and high-volume sorting applications.
- The capacitive sensor offers a very high resolution, matched only by the laser interferometer. Common resolutions range from 0.1 nm (0.004 pin) to 50 nm (2 pin) Operating ranges are generally less than 3 mm (1/8”).
Principle of Operation
When two parallel conductive plates are brought close to one another and a charge is supplied to one of the plates, a capacitor is formed. The current is conveyed through the gap between the plates. The amount of current that passes through the gap is established by the area of the plates, the material that divides the plates, the voltage, and the distance between the plates.
Q is defined as: Q = C*V
Where:
Q = Current (amps), C = Capacitance (farads), and V = Voltage
Capacitance (C) is given as:
C = K* E0 * A/D
Where:
C = Capacitance (farads)
K = The Dielectric Constant of the material between the plates
A capacitive sensor can be defined as a device that establishes the displacement of two parallel plates, one of which is a sensor and the other is the object that is being measured by the sensor.
.jpg)
Figure 1. Simple capacitive sensor (side view)
Figure 2 illustrates a standard sensor configuration, and Figure 3 illustrates the sensor side view.
.jpg)
Figure 2. A typical sensor configuration
.jpg)
Figure 3. Sensor side view — guard ring protects sensor
Types of Capacitive Sensors
There are two types of capacitive sensors:
Active systems are not subject to cable length constraints. They work at higher output bandwidths and higher frequencies. They are suited for applications which may contain stray electrical noise on the target such as spindle run out analysis. The drawbacks of active systems include less configuration flexibility and higher costs.
Passive systems possess certain advantages. They deliver higher flexibility in terms of stability, probe configuration, and lower cost. Their drawbacks are lower bandwidth, cable length limitations, and lower drive frequency, which make them unsuitable for certain applications.
Sensor Size
The larger the sensor size, the better the resolution. The choice of sensor size depends upon the size of the target. The size of the sensor has to be as large as is practically possible.
As a basic rule, the RMS noise will be halved when the sensor area is doubled. The sensor size also affects the range. The larger the sensor the larger its practical range. As a standard rule for round sensors, the sensor’s diameter should be no less than four times the maximum range.
.jpg)
Figure 4. Determining sensor size based upon target shape
Spatial Resolution
A key drawback of larger sensors is decreased spatial resolution. The capacitive sensors capture an average reading of the surface under the sensor. Smaller sensors can distinguish smaller features on a component.
.jpg)
Figure 5. Sensor size determines spatial resolution
Range and Standoff
The distance from the face of the probe to the center of the range is referred to as standoff. This is an estimated distance. Range is the measuring range of the probe. Usual ranges for the capacitive measurement systems are from +/– 10 µm (+/- 0.0004”) to +/– 1000 µm (+/– 0.040”). Ranges beyond 25 mm (1”) are possible in special cases.
.jpg)
Figure 6. Range and Standoff
Resolution
Resolution is the smallest increment of displacement that can be measured at a specific bandwidth. Resolution, according to MicroSense, is an RMS value, as it is measured with a true RMS meter which delivers a clear-cut result.
Bandwidth
An important advantage of non-contact capacitive measurement is its ability to measure highly rapid motions. Applications such as spindle analysis, servo control, and vibration analysis often need the ability to measure extremely small and very rapid motions. Active systems such as the MicroSense 5810 and MicroSense 6810 are built to handle extremely challenging applications having filter bandwidths to 100 kHz. Passive systems such as the MicroSense 8810 and MicroSense 4810 also work well at bandwidths up to 20 kHz. However, the system resolution is relative to the square root of the bandwidth.
Both Butterworth and Bessel filters are provided in MicroSense Active systems, and Butterworth filters are provided in MicroSense Passive systems. Filters are selected in software or by jumpers on the boards.
Linearity
Since the arrival of economical computers and analog/digital cards, linearity has become less of a concern in the last decade. It is possible that a system has integral non-linearity and this relationship is repeatable within resolution parameters and can be compensated with basic software adjustments. For all its systems, MicroSense provides linearity compensation data.
Stability
Stability of the sensor is a function of numerous factors. These can be categorized as external and internal factors. Relative measurement stability is not a problem for numerous measurements such as servo control, spindle analysis, or other short duration relative measurement stability. For measurements where accuracy is necessary over long periods of time, meticulous selection of sensing systems and external factors are very important.
As a standard rule, passive systems such as the MicroSense 8810 and MicroSense 4810 have better long-term stability features than active systems such as the MicroSense 6810 and MicroSense 5810. Standard probes are built using stainless steel and possess a thermal coefficient of around 200 ppm/°C.
Target Characteristics
In the conventional capacitive sensing model, the target grounded and the sensor is driven. For ideal performance, a conductive path from the target to the sensing electronics is vital. The target can be capacitively grounded. Capacitances of 1000 pF or more are ideal.
Environmental Considerations
The main environmental consideration for a capacitive sensor is that there is a uniform, nonconductive material between the target and the sensor. In most applications, this material is air. However, capacitive sensors operate extremely well in vacuum environments, including UHV. The probes will have to be clean. Capacitive Sensors do not function well in on line cutting and grinding environments where there is a constant stream of cutting fluids and grinding waste. It is also easy to fix capacitive sensors.
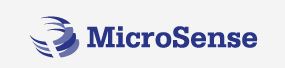
This information has been sourced, reviewed and adapted from materials provided by MicroSense, LLC.
For more information on this source, please visit MicroSense, LLC.