Magnesium has attributes that make it a very desirable manufacturing material. It has the lowest density of all structural metals, making it ideal for applications in which weight saving is a priority, yet it offers great strength, rigidity and dimensional stability. Additional advantages include a high degree of EMI/RFI shielding, durability, heat dissipation and full recyclabllity. Recently Dynacast has introduced an unique magnesium multi-slide die casting technology capable of producing complex, robust, yet lightweight components. Based on the company’s zinc multi-slide casting technology, the magnesium process is designed to produce small components with complex geometries to extremely high levels of accuracy, part-to-part consistency and repeatability, but the very properties of magnesium that make it an attractive material for finished products meant that the company had to overcome considerable difficulties in adapting the technology for the new material.
Multi-Slide Diecasting vs Conventional Diecasting
Dynacast’s existing zinc-multi-slide die casting technology was originally invented in 1936. What differentiates multi-slide diecasting from traditional hot-chamber diecasting is the construction and operation of the tooling, and the diecasting machine required to operate it. Traditional hot-chamber diecasting uses a two-part tool, making it difficult and expensive to produce parts with complex geometries. In contrast, multi-slide tooling is designed to use four perpendicular slides in the tool, enabling complex and accurate castings to be produced. In some cases, up to six slides can be added, which may be at angles other than 90°.
The Multi-Slide Tool
The multi-slide tool is made up of the die block, slide, crosshead and cover plate. Each die block has either a cavity and/or cores on its face, which together form the complete cavity and runner profile into which the molten metal is injected. These die blocks are mounted onto sliders, which fit precisely into a crosshead, ensuring repeatable opening and closing operations. A cover plate, bolted onto the top of the tool, holds all the components together.
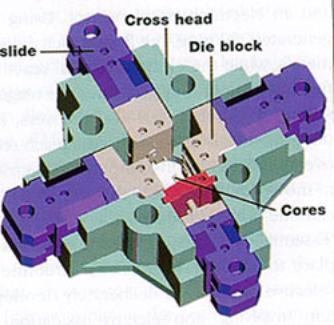
|
Figure 1. The four-slide mechanism enabling production of complex shapes in a single casting.
|
Differences between Magnesium and Zinc Four-Slide Diecasting
There are some subtle differences between the four-slide zinc casting and four-slide magnesium casting machines, which are mainly due to the differences in the metals themselves. Magnesium is flammable, so at the melting stage it is kept under a blanket of gas. It also needs to be kept fluxed, the agent for which is sulphur hexafluoride, which is itself corrosive and needs to be safely contained. To meet these needs is not difficult, but it means that the diecasting furnace is completely enclosed, making melt level measurements difficult. In addition, the surface of the molten magnesium forms a crust of magnesium oxide making melt measurements harder still.
Equipment Configurations
Once melted, the magnesium is injected into the core via a plunger and goose-neck system, as in the zinc casting process. One major difference is that, as disturbance to the melted magnesium needs to be avoided (because movement increases oxide formation), rather than move the gooseneck up to the die and inject metal, the die is moved to the gooseneck. This entails having the entire die, multi-slide tools, crosshead and coverplate assembly on a moving plate. This in turn requires pneumatic actuators to move it, shock absorbers to cushion the movement and gears to control the motion. Obviously, accuracy and timing is critical to avoid damage to the gooseneck nozzle where it meets the die. To prevent spit outs at the die/nozzle interface, a force of about 1.25 tonnes is required, compared to about 0.7 tonnes for zinc. When they do occur, spit outs can increase the temperature of the nozzle and so reduce its hardness, requiring that the nozzle be changed. A further complication is that the low heat of fusion of magnesium, together with its conductivity and density, can cause freezing within the nozzle, also requiring remedial action.
Die Temperature
The other major difference between four-slide zinc casting and four-slide magnesium casting is in the temperature of the die. While for large, non-precision magnesium castings the temperature for the magnesium process can be the same as that for the zinc process, for the small high precision magnesium castings that Dynacast produces the die temperature needs to be considerably higher - 140°C as opposed to 40-70°C. This in turn leads to greater expansion, and the design of die, crossheads, slides and so on needs to take account of this. Also, because of the greater viscosity of molten magnesium, the clamping force of the process needs to be higher than that for zinc.
Shrinkage and Cores
Within the die itself, shrinkage of the cast part onto the cores can be a problem. This is due to the low mass and good thermal conductivity of magnesium parts and results in drag and damage during ejection. Drag can be reduced by polishing the cores and, if drag marks do start occurring, regular cleaning of the cores.
Dimensional Limitations
The dimensions of components made in this way have a maximum size of 100mm x 120mm x 40mm and a maximum shot weight of 40g. Cycle speeds depend on the shot weight - 40g components can be produced at eight shots per minute, while 5g components can be run at 20 shots per minute.
Summary
The result is a high-speed, tightly temperature controlled process yielding thin-walled components so complex that they would need to be assembled from two or more pieces if alternative methods to diecasting were used. Consequently, the process can eliminate an entire assembly stage from production, reduce inventory requirements and achieve higher quality in the finished component. Such characteristics are likely to be attractive in a broad range of volume applications, from cases and shields for handheld electronic devices, such as mobile phones and PDAs, to optical pickup units in CD-ROM drives and DVD players.
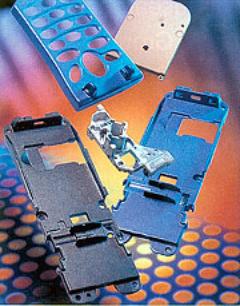
|
Figure 2. Intricate casings made using four-slide technology.
|
|