.jpg)
Image Credits: create jobs 51/shutterstock.com
3D printing is no longer tomorrow’s promise; it is available for manufacture today. But with much competition in the investment sphere of technological innovations, from Artificial Intelligence to Augmented Reality, how do you make the business case for 3D?
Down the road, 3D printing will bring about a radical new era of total supply chain transformation, with local, print on demand solutions dramatically reducing both costs and time to market. But this will take time and, as Paul Croft, Director, Ultimaker GB explains; any business dealing with additive manufacture can explore 3D printing to achieve incremental gains today.
Complementary Model
The goal of 3D printing was never to replace traditional manufacturing processes – contrary to what a small number of hype-mongers may have insisted. 3D is a complementary technology that is built to work alongside current manufacturing methods to develop new efficiencies at every stage of the process.
The ability to print spare parts on-demand, for example, can transform uptime – especially for areas with limited access to the rest of the supply network; while the inherent customization allowed via iterative design unlocks improvements in both ergonomic manufacturing equipment and in employee well-being. Companies can drive down transport and warehouse costs, slash production downtime, and optimize processes.
Accessibility is now a compelling factor in the uptake of the complete 3D print solution model. While there is a real opportunity for end-to-end supply chain transformation, the combination of hardware, software and materials maturity is now letting even the smallest organizations evaluate the potential use of 3D within a blended manufacturing model with only a small, up-front investment.
The crucial question for these organizations, therefore, is what are the areas where 3D printing could be explored to support essential business objectives?
Uptime and Time to Markets
Minimizing production line downtime is a critical Key Performance Indicator in any manufacturing organization. Maintaining high uptime reduces costs, improves time to market and keeps customer relationships strong. While many companies have incredibly slick procedures for managing production, such as highly efficient component sourcing, it takes only the failure of a simple piece of equipment that can throw uptime KPIs into jeopardy.
In the case of global brewer Heineken, a decision taken by its Seville operation to integrate 3D printing with its operation has unleashed a huge range of benefits, not least in the newfound ability to locally print difficult to source spare parts. Sourcing, often importing, discontinued parts can cause significant downtime and associated costs, but 3D printing these parts saved the brewer’s team both time and money. They also demonstrated that the 3D printed plastic parts could effectively function as replacements for metal parts.
For manufacturer Volkswagen Autoeuropa, 3D printing has enabled unprecedented levels of control over the supply chain. The vehicle company, which builds models such as the Scirocco and Sharan, is 3D printing manufacturing aids that are used daily on an assembly line that constructs 100,000 vehicles a year. The company has cut costs and reduced lead times from several weeks to just a few days, by simply removing the dependence on external suppliers for tools, jigs and fixtures.
Enhancing Operations
Using 3D printing, these companies have been able to bring highly complex designs to life and quickly make revisions and alterations, without impacting costs or lead times. Custom tools are available in the time it takes to design and print, matching exact requirements, and making function and performance the main drivers of design rather than cost or time. At VW, for example, a new tool can be left to print overnight and then tested on the assembly line by the operators the next morning. Their feedback can be incorporated into consecutive design iterations until the perfect tool is made.
This iterative approach is also used at Heineken and has resulted in the replacement and optimization of various redesigned parts. For example, a metal part used with a quality sensor on a conveyor belt would often knock bottles over, creating a blockage, or ejecting good bottles onto the ground. This problem was overcome using redesigned 3D-printed parts, saving bottles, money, and time. Furthermore, by adjusting the design of functional machine parts, Heineken has increased line efficiency.
Employee Well-Being
3D printing can also result in significant health and safety benefits. For example, the workforce will find 3D-printed plastic tools or guides are much easier to handle than traditional rough metal tools. Plastic parts and tools are usually lighter, which introduces the opportunity to redesign ergonomic aspects. Indeed, the iterative nature of Additive Manufacturing enables organizations to constantly improve the usability of such equipment, transforming worker experience, positively impacting worker morale and wellbeing.
Heineken has gone one step further, taking advantage of the ability to use color to improve safety. On top of designing the improved safety latches, which are used to prevent machines being accidentally started during the maintenance process, the company made it so these latches are printed in bright red for increased visibility. This application was not only useful, but the extra safety feature created awareness and appreciation of 3D printing among employees.
Another important aspect of these innovations is the speed with which they can be expanded across these multinational businesses is also important. Designs and solutions can be easily shared online, accelerating the global deployment of new applications. Instead of physically transporting parts, they can instead be sent digitally, providing vital solutions in areas that struggle with poor transport links.
Heineken, for example, is using this technology to localize part of the production process in Africa, where importing parts can prove to be a challenge for lead times. Printing these parts in or close to the breweries lets the company remove the need for global shipping – hence reducing international freight costs – while also improving control and uptime and ensuring safety features are also deployed globally.
Conclusion
The ease with which these benefits can be achieved, which is a compelling reason for any business considering the role of 3D printing within a blended model. After a brief validation exercise, Volkswagen Autoeuropa has transformed a comparatively small investment of seven 3D printers into a very significant business benefit: 93% of all externally manufactured tools are now fabricated in-house, resulting in a 91% saving in tool development costs and a development time reduction of 95%.
Heineken has found it to be an average of 80% faster to deliver the required parts than sourcing them externally. The costs of a printed part versus a historically sourced part are also on average 80% lower.
The key to successfully integrating 3D printing is to focus on specific business objectives. Whether improving health and safety, transforming uptime or reducing reliance on third-party suppliers to minimize risk, by concentrating the printing on these core business objectives an organization can quickly build a strong business case. The remaining challenge for organizations is that while awareness is undoubtedly on the rise, it can be perplexing as to how to move forward.
Skills and understanding are very important, but confidence must also be considered, and confidence can only be derived from experience. Some tips to get started; explore inexpensive desktop 3D printers and look for good local support. Seek help from the amazingly collaborative 3D community – from instant access to a raft of materials to a willingness to share experiences. The 3D business case is there; and confidence will come from picking the right piece of kit with a low technical threshold, accessing the right materials, exploring the right software interfaces from design to preparation and, critically, getting involved with the right people who are willing to share their knowledge and support as and when it is required.
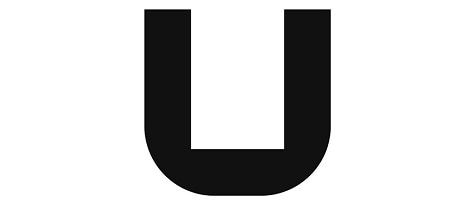
This information has been sourced, reviewed and adapted from materials provided by Ultimaker B.V.
For more information on this source, please visit Ultimaker B.V.