It is thought that one or more catalysts are involved in 95% of all commercially created chemical products at some stage in their manufacturing process. This has an estimated global economic impact of around $15 trillion each year.1
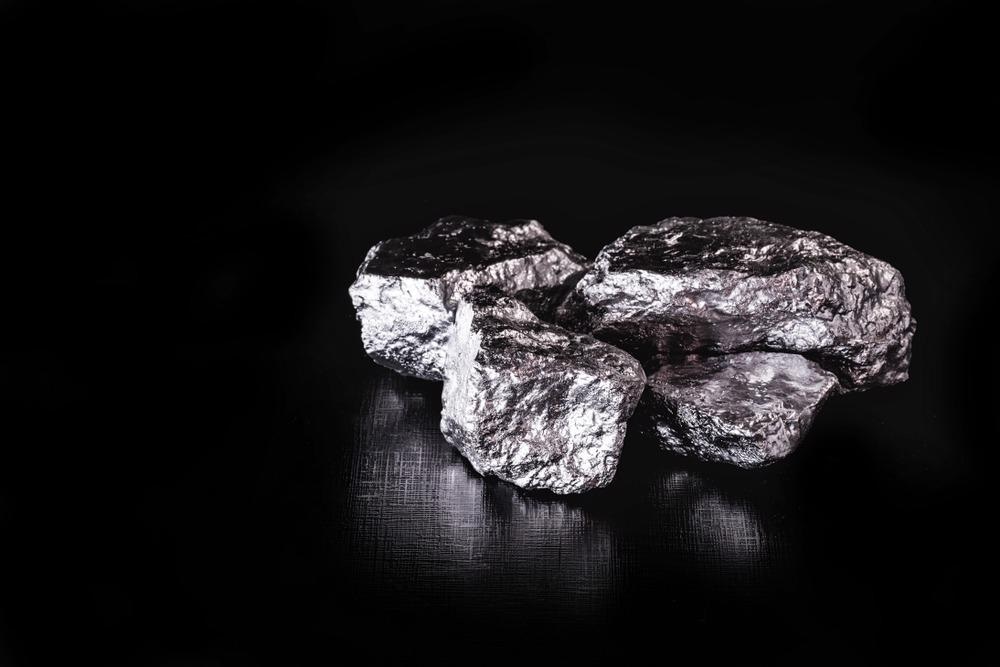
Image Credit: Shutterstick/RHJPhtotoandilustration
For plastics manufacturing, petroleum refining, food and biofuel production and numerous other core chemical manufacturing processes, heterogeneous catalysts are crucial. Thermal degradation or sintering of the active material leads to catalyst performance decreasing and deactivating over time, which is a huge cost driver for chemical manufacturing.
Catalyst deactivation associated with decreased product yields and higher energy usage associated with regenerating or replacing spent catalysts costs billions in lost revenue each year.
Atomic-level control over the catalyst composition and structure will produce high-performance catalysts that cannot be acquired using conventional synthesis techniques. ALD supplies an opportunity for surface engineer active catalyst sites to supply inherent stability, selectivity and performance.5
Atomic layer deposition (ALD) has been shown to be as cost-effective and improve catalyst performance dramatically in a large range of applications.
ALD Improves Catalyst Materials
ALD coatings supply lifetime and selectivity enhancements to catalysts, which in turn supplies better performance. The stabilizing nature of ALD coatings decreases metal catalyst leaching or sintering that would otherwise lower the reaction surface area and performance.
ALD on catalysts benefits are as follows:
- Reduced metal nanoparticle leaching1
- Better catalytic activity overall2
- Lower active site sintering3
- Less thermal degradation3
- Better selectivity between chemical reactions4
- More than 100% better catalyst lifetime because of decreased deactivation4
There are three ALD techniques that are frequently employed in catalyst applications:
1) ALD of the active catalyst on high-surface area supports
2) ALD of an undercoat for increased lifetime and catalyst selectivity and
3) ALD of an overcoat to increase selectivity and limit thermal degradation
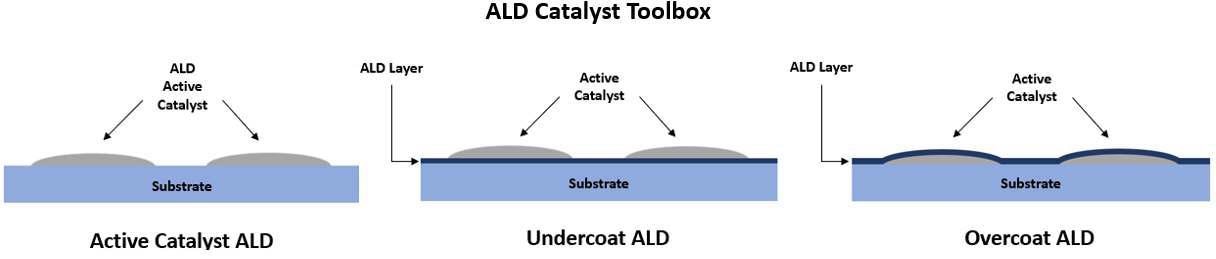
Image Credit: Forge Nano
Active Catalyst ALD
ALD has been discovered to be helpful in depositing catalyst materials like Rh, Fe, Ir, Pt, Pd, Ni and Ru onto ultra-high surface area base supports. The high surface energy of the catalyst materials enables small ‘islands’ to form on the base support and create a high dispersion of active material while maintaining ultra-low loading for lower material costs.
ALD is able to penetrate ultra-high aspect ratio pores in catalyst supports and obtain uniform deposition, unlike wet chemical synthesis methods.6 ALD can also be controlled for near surface deposition for the creation of eggshell structured catalysts.
Undercoat ALD
Utilizing ALD to produce an interface layer underneath the active catalyst will also help sustain thermal stability and increased lifetime. ALD can be employed to alter surface acidity/basicity and stop the dissolution of the active catalyst into the substrate material by depositing a thin film onto a high surface area substrate without adversely influencing morphology or pore size.5
ALD altered substrates showed better catalytic activity, lifetime and selectivity for oxidative dehydrogenation of propane compared to alumina substrates or bulk silica in one instance.7
Overcoat ALD
ALD is also useful for depositing uniform films as a protective overcoat onto the catalyst while also enhancing the catalytic performance. Depositing thin oxide films like ZrO2, Al2O3, NbOx, TiO2, NiO, or Co3O4 protects catalyst integrity throughout high temperature reaction conditions while stopping metal sintering, degradation and leaching.1,4,5
In one instance, alumina ALD overcoat layers enhanced and preserved the catalytic activity of Pd nanoparticles while stopping sintering up to temperatures of 500 oC.8
References
- O’Neill, Brandon J., et al. “Catalyst Design with Atomic Layer Deposition.” ACS Catalysis, vol. 5, no. 3, 2015, pp. 1804–1825., doi:10.1021/cs501862h.
- Shekhar, Mayank, et al. “Size and Support Effects for the Water–Gas Shift Catalysis over Gold Nanoparticles Supported on Model Al2O3 and TiO2.” Journal of the American Chemical Society, vol. 134, no. 10, 2012, pp. 4700–4708., doi:10.1021/ja210083d.
- Zhang, Xingguang, et al. “Heterogeneously Catalyzed Hydrothermal Processing of C5–C6 Sugars.” Chemical Reviews, vol. 116, no. 19, 2016, pp. 12328–12368., doi:10.1021/acs.chemrev.6b00311.
- Marshall, Chris. “Improved Catalyst Selectivity and Longevity Using Atomic Layer Deposition.” U.S. DOE Advanced Manufacturing Office Program Review Meeting, Argonne National Lab, 2019
- Singh, Joseph A., et al. “Nanoengineering Heterogeneous Catalysts by Atomic Layer Deposition.” Annual Review of Chemical and Biomolecular Engineering, vol. 8, no. 1, 2017, pp. 41–62., doi:10.1146/annurev-chembioeng-060816-101547.
- George, Steven M. “Atomic Layer Deposition: An Overview.” Chemical Reviews, vol. 110, no. 1, 2010, pp. 111–131., doi:10.1021/cr900056b.
- Sereda, Grigoriy, et al. “Effect of Atomic Layer Deposition Support Thickness on Structural Properties and Oxidative Dehydrogenation of Propane on Alumina- and TitaniaSupported Vanadia.” Catalysis Letters, vol. 142, no. 4, 2012, pp. 399–407., doi:10.1007/s10562-012-0780-x.
- Feng, Hao, et al. “Alumina Over-Coating on Pd Nanoparticle Catalysts by Atomic Layer Deposition: Enhanced Stability and Reactivity.” Catalysis Lette
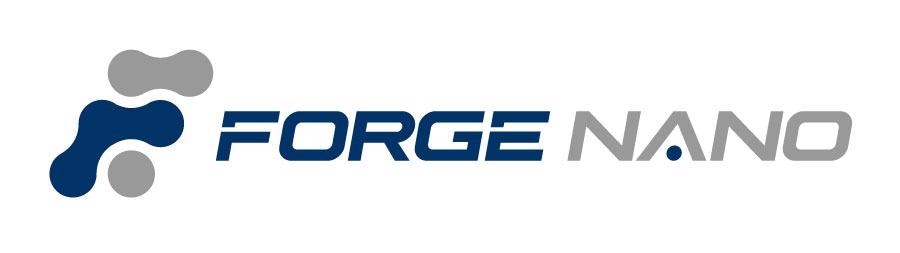
This information has been sourced, reviewed and adapted from materials provided by Forge Nano.
For more information on this source, please visit Forge Nano.