Mechanical engineering is dependent on multiple small components acting together in a system. How these many small parts behave in relation to each other is integral to the functionality of the whole system. For thousands of years, it has been known that surfaces colliding and sliding against each other causes damage to the components. This damage may be imperceptible at first but can eventually lead to mechanical failure. Tribology is the science of why this damage occurs and how mechanical engineers can mitigate it.
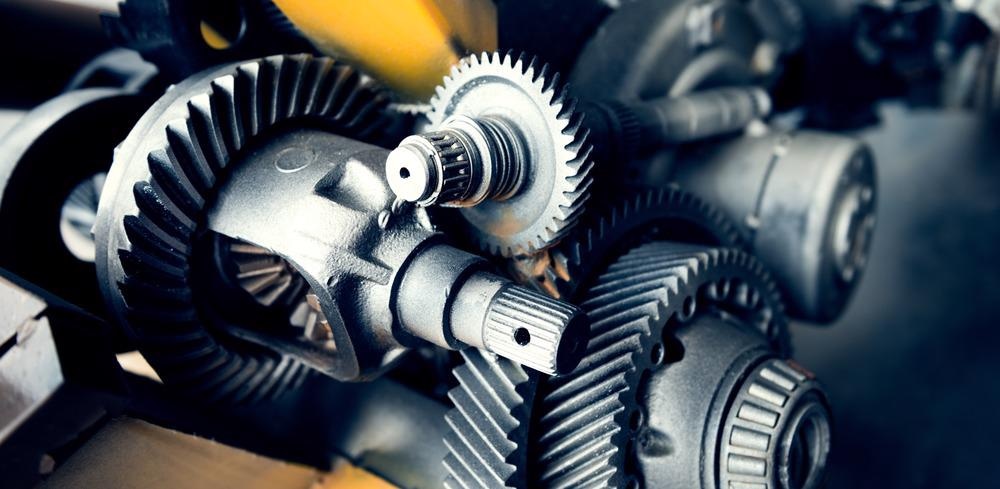
Image Credit: fuyu liu/Shutterstock.com
Tribology refers to the scientific analysis of surface behavior when interacting with each other. The word itself is derived from the Greek word “tribos”, meaning “to rub”. The study is generally divided into three main areas: friction, wear, and lubrication.
Friction
Friction is the resistive force that occurs when surfaces move along each other. Friction will always oppose the direction of the initial force that causes it. Different surfaces have different coefficients of friction (between 0 and 1), written as μ. Smooth, well-lubricated surfaces have a small μ, whereas rough surfaces will have a μ closer to 1.
Though friction is an inevitability in a system with moving parts interacting with each other, it is beneficial to keep friction as low as possible. Even in the best-case scenario, the friction causes a loss of energy in the system in the form of heat. Large amounts of friction can cause significant shear stress on a component and even lead to a component failure, leading to the next area of tribology: wear.
Wear
Wear refers to the loss of material of one or more components as they slide against each other. The two main types of wear are abrasive wear and adhesive wear. Abrasive wear occurs when the harder of the two surfaces removes material from the softer counterpart it slides against. Adhesive wear, however, occurs when the surfaces stick together during sliding, causing one surface to lose material.
A third failure method of wear occurs after, even in circumstances of low stress. If a system undergoes multiple cycles of the same load enough times it can eventually fail, even if the stress it is withstanding is lower than its ultimate tensile strength.
This is caused by minuscule imperfections in the component which leads to imperceptible, microscopic cracks. Though these cracks are not initially a problem, multiple cycles of this stress will cause the cracks to propagate and grow. Fatigue failure refers to the point at which these cracks become large enough to cause the entire system to fail.
As wear can lead to mechanical failure, it is desirable to avoid wear at all costs. In some instances, the failure of a system can be life-threatening. For example, in 1954 a ‘de Havilland’ airliner cabin suddenly decompressed in midair, killing everyone on board. An investigation found that this accident was caused by wear: a seal on a cabin window succumbed to fatigue after multiple stress cycles and failed, leading to decompression.
To avoid wear as much as possible, it is beneficial to ensure that the components of a system can slide across each other and interact with little (or ideally, no) resistance. To ensure the risk of wear is minimized, it is best to ensure that the surfaces of each component do not directly come into contact at all during sliding. This leads to the third topic of tribology: lubrication.
Lubrication
Proper lubrication solves more than just the problem of wear and friction. Besides these two issues, lubrication is also used to regulate heat, as high temperatures can also lead to plastic deformation of machine components. Types of lubrication will also protect surfaces from rust and other forms of corrosion.
Though the concept of lubricating sliding surfaces may seem trivial at first, there are more factors to consider when doing so. Different kind of lubrication films must be applied depending on the conditions. The three main kinds of lubrication, known as ‘regimes’, are boundary, mixed, and hydrodynamic lubrication.
Boundary lubrication is the lubrication film with the smallest thickness. When used, there is extremely little separation between the two sliding parts. To prevent friction and wear, boundary lubrication instead uses additives “such extreme pressure (EP) or anti-wear (AW)” (Machinery Lubrication, n.d.) rather than separation. This regime is used when separation is not possible, typically at slow speeds, with expected “shock-loading conditions” (Machinery Lubrication, n.d.) and many short stress cycles.
Hydrodynamic lubrication occurs at the other end of the spectrum. This regime occurs in conditions where the sliding is occurring at very high speed, and the machine is expected to run continuously with little stopping and starting. Here, the thickness is at a maximum; in fact, in this regime, the two sliding surfaces do not come into contact at all. This leaves extremely low friction yet has the consequence of poor response to shock-loading.
Mixed lubrication is the mixture of the two, where the two sliding surfaces occasionally touch. This occurs “during the transition from low to high-speed operation when boundary and hydrodynamic conditions coincide” (NYE Lubricants, n.d.). It is best for machinery that is required to maintain high speeds but also bear stress cycles from continuous stopping and starting.
Knowing which lubrication regime is most suited for the machinery in question can be complicated. Not only is situational knowledge required, but in machines with high precision, dense and difficult mathematics in fields such as fluid dynamics will become more of an issue to be solved. In terms of practicality, being able to negotiate these issues is the most important area of tribology.
The field of tribology is a combination of mechanical and material science, requiring the researcher to look at systems both wholly and on a microscopic level. Without tribology, mechanical engineers would be unable to mitigate seemingly insignificant issues before they develop. Occasional abrasions and microscopic cracks can eventually lead to complete system failure over time.
Knowing how to properly remedy these issues caused by a motion as inconspicuous as, say, gears sliding across each other, is answered by tribology. In doing so, less energy is lost, less components will wear and need replacing, and the system will be able to function more efficiently and for longer.
References and Further Reading
Tribonet.org (n.d.) . Tribology History. [online] Available at: https://www.tribonet.org/tribology-history/ (Accessed 1 June 2021).
Tribonet.org (2016). Tribology. [online] Available at: https://www.tribonet.org/wiki/tribology/ (Accessed 2 June 2021).
Stle.org (n.d). Tribology Wear. [online] Available at: https://www.stle.org/files/What_is_tribology/Tribology_Wear.aspx (Accessed 27 May 2021)
Wmtr.co.uk (n.d). History of Fatigue Testing. [online] Available at: https://www.wmtr.co.uk/ (Accessed 4 June 2021).
Kardomateas, G.A. and Geubelle, P.H. (2010). Fatigue and Fracture Mechanics in Aerospace Structures. In Encyclopedia of Aerospace Engineering (eds R. Blockley and W. Shyy). https://doi.org/10.1002/9780470686652.eae142
Element (2016). 5 Disasters Caused by Material Fatigue and What We Learned From Them. [online] Available at: https://www.element.com/nucleus/2016/5-disasters-caused-by-material-fatigue-and-what-we-learned-from-them
Machinerylubrication.com (n.d). Tribology Explained. [online] Available at: https://www.machinerylubrication.com/tribology-31340 (Accessed 5 June 2021).
Nyelubricants.com (n.d). What are Lubrication Regimes? [online] Available at: https://www.nyelubricants.com/what-are-lubrication-regimes (Accessed 3 June 2021).
Disclaimer: The views expressed here are those of the author expressed in their private capacity and do not necessarily represent the views of AZoM.com Limited T/A AZoNetwork the owner and operator of this website. This disclaimer forms part of the Terms and conditions of use of this website.