Repairing subsea pipes is a difficult, expensive, and time-consuming effort. Depending on the severity of the damage, a compromised subsea pipe may need to be shut off entirely, “stopping its flow and the revenue it generates” (Charalambides, 2016). To reduce the inconveniences caused by these repairs, Norwegian company Kongsberg Ferrotech is making use of recent 3D printing developments to optimize the process with its new, award-winning Nautilus.
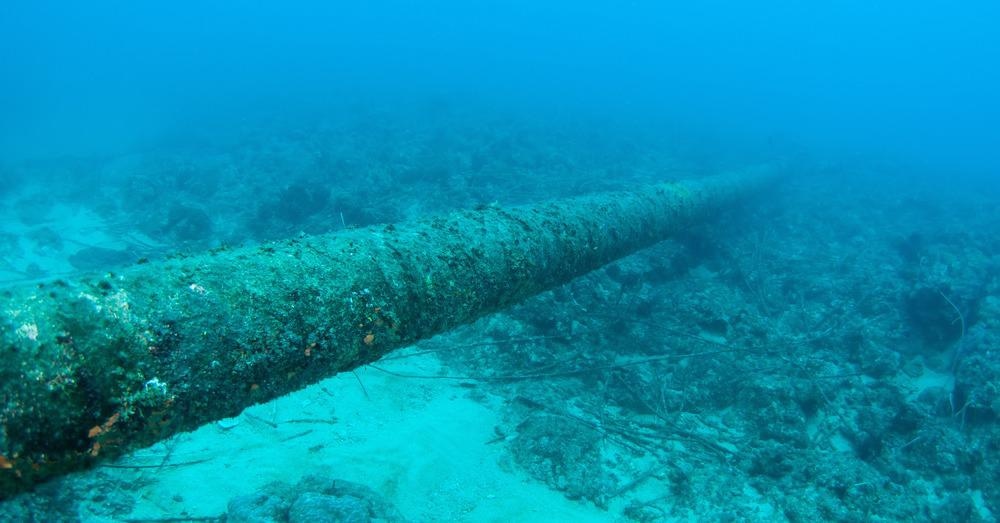
Kongsberg Ferrotech has developed a robotic 3D printing solution for seabed pipeline repairs. Image Credit: Jung Hsuan/Shutterstock.com
Conventional Subsea Repair Methods
Even in cases of minor damage, a compromised pipe will need to be assessed by a remotely operated underwater vehicle (ROV). The seabed around the damage must be dredged by divers, the surface of the pipe must be prepared (which may include milling down welded surfaces) by divers, and a clamp must be lowered in and secured, typically done manually by the divers.
Even this example assumes the best-case scenario for the damaged pipe. If the length of the damaged pipe is longer, this process will become even more arduous and intensive. If the damage of the pipe has progressed past minor, the compromised length of the pipe may need to be removed and replaced entirely.
Though the issue of damaged subsea structures is difficult, this conventional solution has many downfalls. The process uses different components for assessment and repair, increasing the time of the process and reducing its cost-effectiveness. Furthermore, the conventional method relies heavily on manual aid from divers which can be problematic in deep-sea conditions as divers need to spend hours after the repair to avoid decompression sickness. Dredging and digging on the seabed can also be considered an environmental disruption.
Underwater 3D Printing Solutions with Kongsberg Ferrotech
Kongsberg Ferrotech, a Norwegian company that specializes in subsea robotics, has designed a product, due for release in 2022, to simplify and improve this repair method.
The company’s product will be able to assess pipeline integrity, perform maintenance, and repair damage using a single robot. This innovation, a first in the industry, is made possible using underwater 3D printers.
The Nautilus robot is a tool that houses, drains, inspects, and repairs sections of defective pipelines. The device is connected to a control center onboard the ship that deploys it. This method of transferring data from the robot to a team above the surface minimizes the number of divers needed throughout the inspection and repair process.
The robot is lowered onto the compromised section of the pipe via a crane. The machine uses pigging inspection to minimize the seabed’s excavation. This reduces manual labor required, preparation time, and environmental damage to the seabed.
Pigging, a method originally used to clean pipes without turning them off, consists of inserting devices called ‘pigs’ through a pipe. As the pigs travel through the pipe, they “[scrape] the sides of the pipe as it travels, removing dirt and debris” (Inspectioneering, n.d.). If the pigs have data-collection capabilities, known as ‘smart pigs’, pigging can travel through the pipe and detect imperfections in the pipe, accurately pinpointing areas of damage.
Using this inspection method, the area that the Nautilus needs to be applied to is narrowed down to very specific locations. This inspection method is why the amount of dredging required is minimal. This also means that the size of the robot’s interior does not limit the minor defects that it can fix.
Once the Nautilus has been lowered onto the observed defect, the robot automatically clamps around the pipe and drains the water in its interior. This gives the machine and the inspectors performing the repairs from the ship a dry workspace, allowing the 3D printing repair to take place.
Once the water has been drained from the internal environment, the Nautilus removes the coating of the pipe section. During this process, the vacuum mechanism is still on, so that the debris caused during the removal process is sent to the deck of the ship for collection by the team.
After this removal process, the surface is prepared to adhere to a new coating. This coating is applied by a circular 3D printer, encapsulating the pipe. The 3D printer travels along the length of the pipe, coating it completely. Cameras inside the robot allow the control room attendants to observe and control this process.
Once the new coating is applied, a scanner on the 3D printer accurately pinpoints the exact area of damage, using data from the pigging inspection. This area is then coated with a solution to prevent further leakage, again using the 3D printer. A carbon fiber composite is then wrapped around the leak, completing the repair. The Nautilus releases the seal and returns to the surface.
Nautilus revolutionizes subsea service work by re-imagining pipeline maintenance by ARV
Video Credit: PTTEP Official/YouTube.com
The Innovation of 3D Printing in Subsea Repair
The use of additive manufacturing to repair subsea pipes is a new idea, with the Kongsberg Ferrotech’s Nautilus being the first of its kind. The technology is only made possible using the vacuum, supplying a dry workplace for the printer to carry out the repairs.
This innovation optimizes the time, money, and resources used in the short term for subsea pipe repairs, and also improves the cost-effectiveness of inspection and repair in the long term. Using this device can “significantly extend the lifetime” (Hanaphy, 2021) of a subsea pipe, meaning costs incurred by replacing old pipes are reduced dramatically.
This technological advance won Kongsberg Ferrotech the Award for Breakthrough Technological Project of the Year from the Oil exhibition ADIPEC. According to Brede Lærum, the head of Additive Manufacturing at collaborator Equinor, Kongsberg Ferrotech “plan to offer service and maintenance based on 3D printing as early as 2022” (OEDigital, 2021).
References and Further Reading
Charalambides (2016). Getting to the bottom of subsea repairs. [online] Available at: https://www.controleng.com/articles/getting-to-the-bottom-of-subsea-repairs/ (Accessed 11 June 2021)
Hanaphy, P. (2021). Underwater 3D Printing to be rolled-out in 2022? [online] Available at: https://3dprintingindustry.com/news/underwater-3d-printing-to-be-rolled-out-in-2022-191146/ (Accessed 12 June 2021)
Kongsberg Ferrotech (2021). Kongsberg Ferrotech [online] Available at: https://www.kferrotech.no/ (Accessed 11 June 2021)
OEDigital (2021). Subsea 3D Printing Tech Targeted for 2022 [online] Available at: https://www.oedigital.com/news/488085-subsea-3d-printing-tech-targeted-for-2022 (Accessed 12 June 2021)
Inspectioneering (n.d.). Overview of Pigging [online] Available at: https://inspectioneering.com/tag/pigging (Accessed 12 June 2021)
Disclaimer: The views expressed here are those of the author expressed in their private capacity and do not necessarily represent the views of AZoM.com Limited T/A AZoNetwork the owner and operator of this website. This disclaimer forms part of the Terms and conditions of use of this website.