Semiconductor activities from wafer growth and passivation to packaging and testing are now housed under one roof in Sheaumann Laser’s brand-new 18,000 sq ft cleanroom.
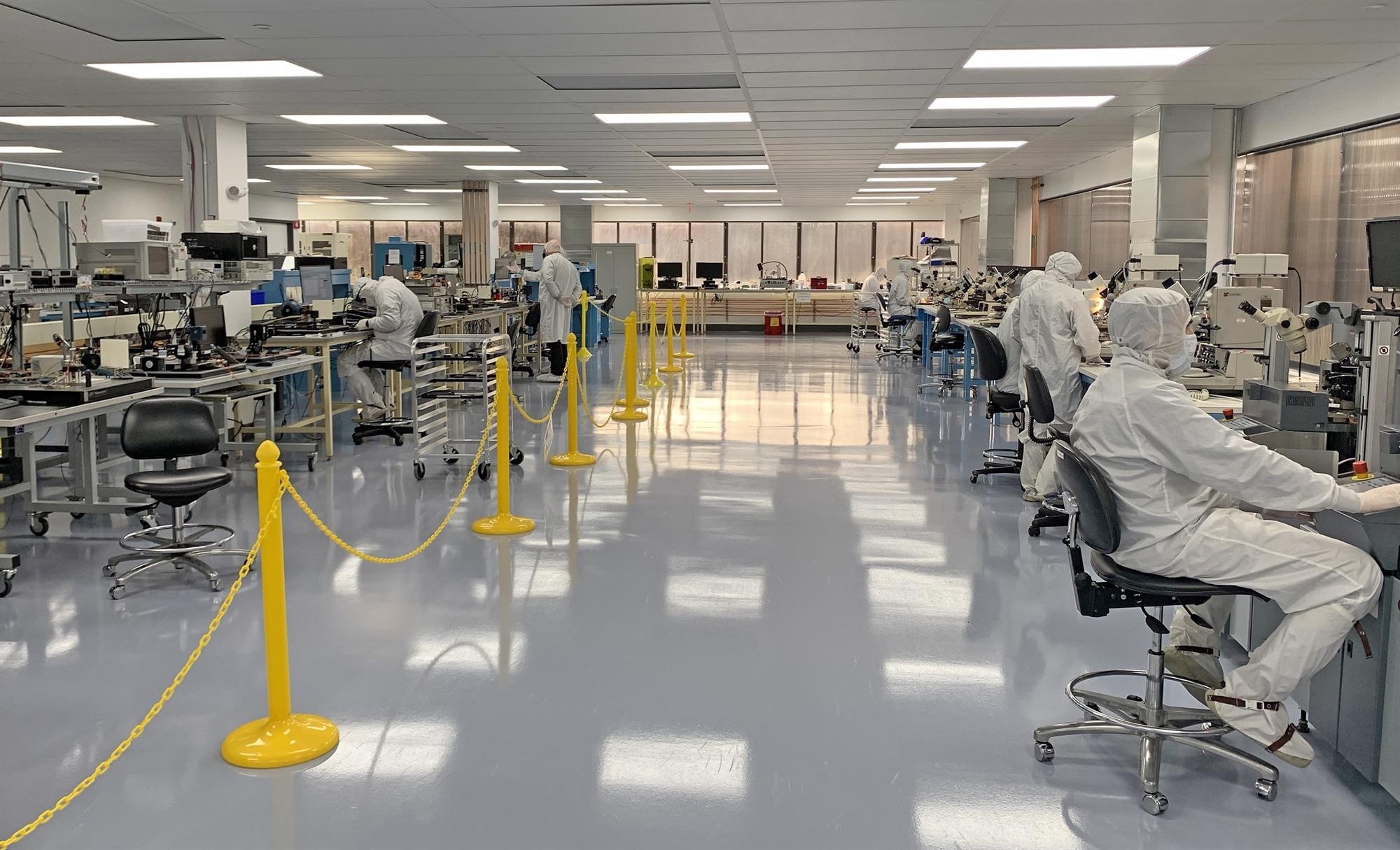
Sheaumann Laser won the Massachusetts Manufacturing Innovation Initiative (M212) grant in 2018, a catalyst for the company. The multi-million dollar grant supported significant equipment upgrades, including the purchase of a new reactor.
The purchase allowed Sheaumann to expand their emissions offerings into the InP
wavelengths, opening a whole new level of business to the company. The applications of this new offering range from 3D sensing to laser illumination.
However, the facility the company was leasing at the time posed both logistical and spatial challenges. The combination of expanded capabilities, the need to increase the workforce and new equipment meant that it was time for Sheaumann to find a new space.
There were many questions to consider, including who could manage the massive buildout and where to build the expanded cleanroom and new headquarters.
Most of the vertically integrated semiconductor laser diode manufacturing industry has largely moved its production to Asia. This means that Sheaumann’s presence in the United States is rare for the industry.
Sheaumann’s ethos towards growing its business is based on being sized with innovation in mind, not on using the lowest prices for the mass production of standard parts.
Sheaumann aims to equip its facility with skilled technicians, a team of engineers, and equipment that can aid in building partnerships to address complex problems, not just creating off the shelf, standard parts. This involves working alongside companies forging new frontiers in space, government think tanks, and medical device start-ups.
Sheaumann aims to scale up with its partnering companies by starting with designing custom component solutions for big-idea projects. Sheaumann has centered its engineering capabilities, foundry and cleanroom in every planning stage as it begins its next chapter.
Jim Hsieh, the Owner, and CEO of Sheaumann, believes in this plan for growth. His previous company, Lasertron, was founded on the same principles and made major breakthroughs in the telecom industry in the 90s while being guided by the same principles of engineering innovation.
When moving to a bigger space from the company’s previous location in Marlborough. Let’s do this right, from the ground up. Let’s buy a building and shape the place to our needs.”
Jim Hsieh, Owner and CEO, Sheaumann
Sheaumann’s CTO and President, John ‘Gary’ Sousa, also brings expertise to this endeavor thanks to his previous work building laser manufacturing plants.
He has first-hand experience of refitting a building to ensure it is meeting the company’s needs as best as possible, as can be demonstrated by his previous work doing just that when his company, Axcel Photonics, merged with Sheaumann in 2015.
His previous experience means he can anticipate any hurdles that might arise and knows how to quickly jump over them.
Location, Location, Location
Constructing a new facility inside the US is more expensive than building it elsewhere, and Massachusetts is a particularly expensive place to do this project.
However, the state is home to some of the world’s best engineering programs, and Sheaumann’s new location in Billerica, MA, provides the opportunity to recruit graduates from WPI, UMass Lowell, BU Photonics, Harvard and MIT, all of which are within 40 minutes of the new campus.
The Process Defines the Fab
Designing the cleanroom was the next step after identifying the location and building for the company’s move. The new flow was tailored by Sousa to better fit Sheaumann’s manufacturing process.
The flow of the new space has the growth area moving into a process area; the process area begins with photolithography in yellow rooms with a dedicated space for both solvent hoods and acid hoods.
The next step of the process is for the product to get moved to a different specialized area for the depositing of metals and dielectrics. Major considerations for Sousa as he laid out the facility included the production process path of the epitaxial wafers grown by the company.
The process is nuanced and involves multiple steps and the specific challenges in laying out a facility to manage it would likely be beyond the scope of many independent architects, even the most adept.
Sousa was able to solve this puzzle thanks to decades of direct participation in the process and an ability to med operational knowledge with the town’s planning codes and the existing bones of the building.
Consideration for major systems had to be done before any other part of the building design could even be started. There had to be space for the weaving pipes, ducts, and lines of the water, air filtration, gas, and electricity systems.
Mechanical space is the heart of the cleanroom floorplan. This is where the solvents and acids are taken care of and the DI and RO water is filtered and removed.
The room, with its water and drainage lines being fed from the center out like spokes, began to be conceptualized as a bicycle wheel by Sousa. In order to minimize the impact on the labs, each laboratory was assigned its own lines.
This meant if there was a malfunction in one area, the rest would still be able to continue working. Each of the different areas is fed from a central power node. The coolant and chilled water systems use gravity to their advantage by being placed on the roof.
Semiconductor manufacturing requires hazardous gases, and so their safe handling was another key part of infrastructure design. The custom-built toxic gas containment building was constructed to meet international and state gas and fire codes.
Many complex processes and machines being set up to operate at maximum efficiency in a single cleanroom facility is only one part of the company’s strategic puzzle.
Other important considerations were visitors being able to have maximum visibility and the cleanroom technicians having a working environment that enables them to do their best work. Instead of using harsh fluorescent lights, LED overhead lighting was installed to mimic natural daylight and to bring a bright and airy feel to space.
Clean, Cleaner, Cleanest
Technicians arriving at Sheaumann in their street clothes first enter a HEPA-filtered breakroom space that is cleaned 60 times an hour. The technicians then clean their shoes using a motorized boot cleaner before entering a large gowning room and getting into a full cleanroom suit.
They then pass through an airlock shower with an 1150 CFM fan before they enter the workspace. This process means that there is a class 1000 space that tests to a class 100 and a class 10,000 space that almost tests to a class 1000 in certified particle count readings that are taken at multiple points in the rooms three times a day.
The ceiling features several 650 CFM fan-blown HEPA, each with its own motor that is tunable to control flow. Dust is prevented from falling into the workspace by gasketed trays underneath the insulated, state-of-the-art cleanroom solid panel ceiling. The LED overhead lighting lends the space a bright and airy feel.
Seeing is Believing
A viewing corridor with windows was created out of what would have otherwise just have been a mechanical chase by Sousa. Facility tours can use this “viewing corridor” when customers come to view the clean space.
Customers being able to more easily view the equipment means they can gain a better understanding of the facility and the steps used in the manufacturing of their product. It also means they can be first-hand witnesses to the dedication of the technicians and the quality of the cleanroom.
A cleanroom walk through at Sheaumann Laser, Billerica, Mass.
Video Credit: Sheaumann Laser, Inc.

This information has been sourced, reviewed and adapted from materials provided by Sheaumann Laser, Inc.
For more information on this source, please visit Sheaumann Laser, Inc.