Several hindrances to the recycling of synthetic polymers, including material separation and post-treatment degradation of the macromolecular polymer chains, negatively affect the cost-efficiency and properties of recycled materials. Chemically recycle polymers, which can be polymerized into monomers for reuse, can offer a solution for material recycling for better plastic sustainability, without loss in properties. A chemically recyclable polymer created by Dr. Junpeng Wang and his colleagues at the University of Akron, USA, can pave the way towards more sustainable polymer materials.

Image Credit: Sanit Fuangnakhon/Shutterstock.com
Synthetic polymers have become ubiquitous in modern industrial society with various applications, including packaging, construction, transportation, consumer products, textiles, medicine, and electronics. These materials are strong, durable, lightweight, low in cost, and have good chemical resistance.
Primarily made from fossil-based feedstock, synthetic polymers are organic macromolecules consisting of many repeating subunits called monomers. The polymers' exceptional durability and remarkable mechanical properties are achieved through high-strength covalent bonds that form dense macromolecular networks.
Large-scale use of polymers began in the 1940s. The use of nylon for parachutes and ropes, Plexiglas (or polymethyl methacrylate, PMMA) for aircraft windows, and polybutadiene-polystyrene co-polymers as a rubber replacement in car tires were all commonplace.
Since then, global plastics production has grown to more than 400 million tons per year, with more than 8 billion tons produced in the past 50 years. The average annual production has increased by 36% in the past decade and is projected to reach 700 million tons per year by 2030.
The Importance of Recyclable Polymers for Plastic Sustainability
On average, only 20% of all discarded polymer materials are recycled globally, with less than 10% in the United States and ~30% in the EU. The primary industrial recycling process involves mechanical grinding.
Polyethylene terephthalate (PET) and high-density polyethylene (HDPE) dominate due to their widespread use, facilitating collection and sorting at recycling facilities.
More than half of total waste polymer materials are deposited into landfills or released into the environment; approximately 25% of plastic waste is incinerated for energy recovery, releasing greenhouse gases.
New regulations are boosting the demand for recyclable and sustainable polymers. These include minimum recycled content requirements for flexible packaging in the EU and UK and restrictive policies by some of the largest global importers of plastic waste, like China and Turkey.
In the last decade, an increasing number of industrial and academic research and development ventures aim at producing novel cost- and energy-efficient polymer recycling processes that can be commercially competitive with polymer production from a virgin feedstock.
What are the Challenges in Developing Chemically Recyclable Polymers?
A growing number of applications, such as automotive parts, wind turbines, and aircraft components, rely on high-strength carbon-fiber reinforced polymer composites. The increasing use of flexible films and laminated plastics in the packaging industry generates significant post-consumer waste, emphasizing the need to develop innovative recycling methods.
Designing a polymer capable of undergoing an indefinite number of degradation (depolymerization) and formation (polymerization) cycles would allow valuable resources to be fed back into the economy in a high-value form, rather than downgrading them as fuel for power generation.
The next grand challenge for polymer science is to develop a chemical recycling process permitting depolymerization (into the material's constituent monomers) and re-polymerization of polymers. Doing so would reduce the demand for finite raw materials and minimize plastics' negative impact on the environment.
Currently, chemical recycling to monomer (CRM) processes involve hydrolysis for carbonyl-containing polymers, such as Polyethylene terephthalate, PET, or pyrolysis - heating in the absence of oxygen. Historically, both techniques have been too energetically demanding for commercial use. Only in the last few years, the increasing demand for sustainable polymers made them economically viable.
Traditionally, the polymer properties depend on the material's intended use. Polyolefins occupy the largest polymer market segment, making up more than half of the global polymer production and waste. The development of CRM-compatible polyolefin-based materials would guarantee positive economic and environmental impact.
The design of such chemically recyclable polymers, however, can be very challenging.
Physical properties of new materials need to match or exceed those of the materials being replaced. At the same time, a cost-effective depolymerization process that can cleave the carbon-carbon bonds along the polyolefin backbone chains is necessary.
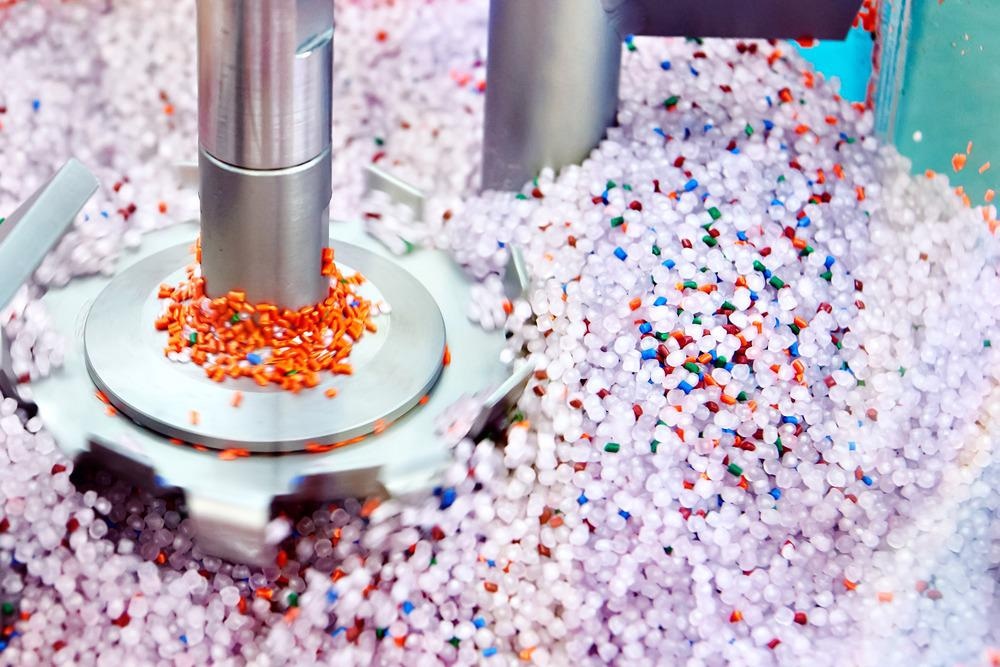
Image Credit: Sergey Ryzhov/Shutterstock.com
Chemical Recycling in the Context of Polymerization Energetics
Wang and colleagues have discovered monomer compounds exhibiting high polymerization and depolymerization activity that can deliver properties comparable to existing industrial polymers. Their research was published in Nature Chemistry on July 22nd, 2021.
Here, the researchers studied the energy landscapes of cyclooctene, an 8-membered unsaturated cyclic alkene, polymerization through computer modeling. Cyclic alkenes can be subjected to a ring-opening metathesis polymerization (ROMP) reaction where a chain-growth mechanism converts them into polymers.
The driving force behind the polymerization reaction is the relief of the bond-energy difference between the cyclic monomer and the polymerized chain, where the energy difference determines whether the polymerization reaction is reversible or not. The idea behind the theoretical research was to design a monomer compound that can undergo catalytic polymerization-depolymerization efficiently.
According to the team's modeling, a specially designed monomer, which consisted of cyclooctene fused with a four-membered cyclobutane ring, might be an excellent candidate for these reverse polymerization reactions. Based on the theoretical models, the cyclooctene-derived monomer was synthesized and subjected to ROMP reaction in an organic solvent in the presence of a ruthenium-based catalyst.
When polymerized at room temperature, the reaction yield was 67%. Since both the monomer and polymer have comparable bond-energies, the polymerization reaction should be reversible. Reversing the reaction at 50°C while still using the same catalyst resulted in depolymerization with nearly 90% of the monomers recovered.
Tunable Monomers for Circular Polymer Economy
According to Dr. Wang, the reaction is controlled by the monomer's concentration. Higher monomer concentration favors the polymerization process, while lower concentration shifts the reaction equilibrium towards the monomers. Besides, the reaction takes place without producing or consuming additional materials.
Further experiments proved that, due to its very high thermal decomposition temperature (370°C), the novel chemically recyclable polymer could be processed into products by a conventional high-temperature injection molding. The process would enable industrial fabrication of chemically recyclable polymer materials using biobased olefins as feedstock.
The recyclable polymer is highly stable and can withstand heat, corrosion, and mechanical stress. Its properties can also be modified for different applications by substituting functional side groups on the polymer backbone. An imide-functionalized monomer synthesized in Dr. Wang's group, when polymerized, exhibited similar mechanical properties to polystyrene.
These remarkable properties make the chemically recyclable polymer not only an elegantly designed CRM system, but a viable route for innovation in the circular polymer economy.
References and Further Reading
D. Sathe, et al., (2021) Olefin metathesis-based chemically recyclable polymers enabled by fused-ring monomers. Nat. Chem, 13, 743–750. Available at: https://doi.org/10.1038/s41557-021-00748-5 [Accessed on 31 August 2021].
Y. Getzler, (2021) Low strain, more gain. Nat. Chem, 13, 719–721. Available at: https://doi.org/10.1038/s41557-021-00759-2 [Accessed on 31 August 2021].
Coates, G.W., et al., (2020) Chemical recycling to monomer for an ideal, circular polymer economy. Nat Rev Mater, 5, 501–516. Available at: https://doi.org/10.1038/s41578-020-0190-4 [Accessed on 31 August 2021].
W. d'Ambrières (2019) Plastics recycling worldwide: current overview and desirable changes. Field Actions Science Reports, 19, 12-21. Available at: https://journals.openedition.org/factsreports/5102 [Accessed on 31 August 2021].
University of Akron (2021) New method developed to solve plastics sustainability problem [Online], Science Daily. Available at: https://www.sciencedaily.com/releases/2021/08/210817193022.htm [Accessed on 31 August 2021].
Disclaimer: The views expressed here are those of the author expressed in their private capacity and do not necessarily represent the views of AZoM.com Limited T/A AZoNetwork the owner and operator of this website. This disclaimer forms part of the Terms and conditions of use of this website.