Ceramic materials suitable for additive manufacturing (AM) methods often lack essential material properties such as density or mechanical strength, which hinders the wider industrial application of 3D-printable technical ceramics. Recently, Fortify, a Boston-based 3D printing company, partnered with Tethon 3D, a company specialized in ceramics-based additive manufacturing, to advance the adoption of technical ceramics in various additive manufacturing applications.
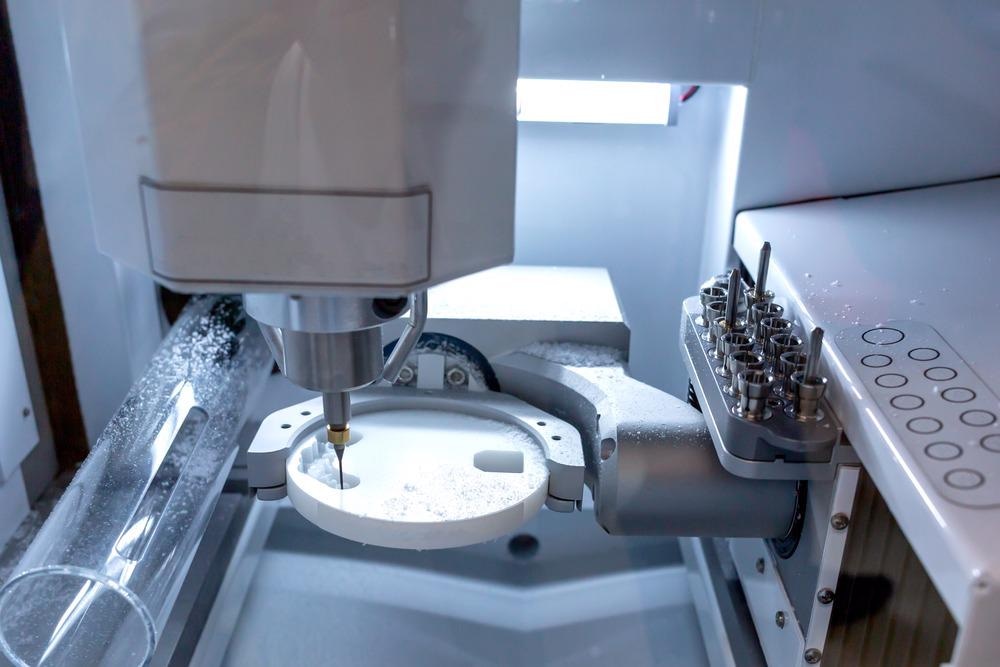
Image Credit: ANDRIY B/Shutterstock.com
Technical ceramics exhibit outstanding performance due to their high hardness and strength, good high-temperature performance, excellent thermal shock resistance, and high chemical stability in harsh conditions.
These unique properties make ceramics relevant for a wide range of applications in the chemical and aerospace industry, construction, electronics, transportation, and biomedical engineering.
However, manufacturing and processing ceramic parts has always been a challenge because of the material's inherent hardness and brittleness.
Conventional processing methods, such as dry pressing, casting, injection molding, and powder sintering prove costly and unsuitable when highly complex structures with detailed features are required. Besides, most of these methods require prefabricated molds for each particular design, while sintered components typically require mechanical processing to obtain a finished product.
These additional steps slow down the whole production cycle and make small-scale manufacturing expensive and unsustainable.
Additive Manufacturing Cuts Cost, Time, and Waste
While additive manufacturing technologies are already well-established in plastics processing or metalworking, the ceramic industry lags in implementing such manufacturing methods.
Additive manufacturing offers new pathways to overcome the disadvantages of conventional fabrication methods and create highly complex ceramic components.
First introduced more than 30 years ago, additive manufacturing, also known as 3D printing, was initially developed as a rapid prototyping method for manufacturing complex 3D parts without molds and in a short time.
The intense development of a range of additive processes for 3D manufacturing, such as selective laser sintering, direct ink writing, and stereolithography, led to vastly improved accuracy and significant cost reductions of the manufacturing hardware (3D printers) and source materials.
These techniques use the same process, where a component is assembled from thin two-dimensional layers of the starting material stacked on top of each other.
Each layer corresponds to a cross-section of the component's digital model. The process allows for the design and manufacture of complex objects in a short time and without waste material.
Besides, ongoing material science innovations expand the range of printable materials, meaning that designers and manufacturers are no longer limited to printing only plastics or metals.
3D Printing Process for Technical Ceramics
To answer the growing demand for large-volume manufacturing of high-precision components made of technical ceramics, Tethon 3D and Fortify joined their expertise to offer a wide variety of 3D printed technical ceramics applications.
In a typical ceramics 3D printing process, a liquid photo-curable polymer is mixed with fine ceramic particles (called filler).
3D-Printed Ceramics | PopMech
Credit: Popular Mechanics/Youtube.com
The 3D printer solidifies the liquid polymer layer-by-layer using UV light, thus shaping the printed object.
Next, the ceramic 3D prints are treated using heat and/or chemicals to remove the polymer and leave only the ceramic material in the shape of the 3D print. The process of polymer removal causes a slight shrink in the object's dimensions.
The final step is to sinter the 3D object, which fuses the ceramic particles and gives the final product its desired mechanical and chemical properties.
Partnership for Advanced Additive Manufacturing
The primary know-how of Tethon 3D, a material science company based in Omaha in the USA, is in 3D-printable ceramic formulations.
The company offers a comprehensive portfolio of ceramic- and metal-based photocurable resins for use in an in-house developed desktop 3D printer for technical ceramics.
The system is based on Digital Light Processing (DLP) technology and offers superior control of the photopolymerization process.
Recently, Tethon 3D and Fortify developed two new ceramics-based resins, called Low Shrink Aluminum Silicate and Fortify High Purity Alumina, that are suitable for use with Fortify's Flux series of 3D printers.
The 3D printing hardware uses the company's Digital Composite Manufacturing (DCM) platform and is designed to have unmatched print quality when using filled photocurable resins.
During the 3D printing process, DCM continuously recirculates the resin in a process called continuous kinetic mixing and blends the filler, thus minimizing the sedimentation of the filler particles.
The uniformly distributed ceramic filler enhances the strength, stiffness, and wear resistance of the material.
High Performing Ceramic Resin Formulations for Manufacturing-Oriented Solutions
Most importantly, the novel 3D printable ceramics, developed by Tethon and Fortify, address the material shrinkage problem during the sintering step. The treatment to remove the cured polymer reduces the final volume of the printed object by 20%–30% (depending on the filler content in the resin).
Tethon's scientists used ceramic particles with different shapes and sizes that permitted them to achieve a very high filler content in the resin while maintaining optimal porosity to facilitate the sintering process. The High Purity Alumina material sinters to a final purity of 99.8% alumina with only 12% shrinkage, while the Low Shrink Aluminum Silicate achieves a record-breaking 5% shrinkage.
Both materials are suitable for applications that require high dielectric strength, corrosion resistance, and thermal conductivity, and can operate at temperatures above 1450 °C.
The overall performance of the newly developed technical ceramics, together with the capabilities of Tethon's and Fortify's 3D printing systems, can satisfy key demands from industrial customers for high purity materials, low shrinkage, and faster processing throughput.
References and Further Reading
K. Sertoglu (2021) Fortify and Tethon 3D partner to develop ceramics for additive manufacturing. [Online] www.3dprintingindustry.com Available at: https://3dprintingindustry.com/news/fortify-and-tethon-3d-partner-to-develop-new-ceramics-for-additive-manufacturing-195693 (Accessed on 21 September 2021).
S. Davies (2021) Fortify & Tethon 3D partner to develop 3D printing ceramic materials. [Online] www.tctmagazine.com Available at: https://www.tctmagazine.com/additive-manufacturing-3d-printing-news/ceramic-and-exotic-additive-manufacturing-news/fortify-tethon-3d-partner-to-develop-3d-printing-ceramic-mat (Accessed on 21 September 2021).
Lakhdar, Y., et al. (2021) Additive manufacturing of advanced ceramic materials. Prog. Mater. Sci. 116, 100736. Available at: https://doi.org/10.1016/j.pmatsci.2020.100736
Zakeri, S., et al. (2020) A comprehensive review of the photopolymerization of ceramic resins used in stereolithography. Additive Manufacturing 35, 101177. Available at: https://doi.org/10.1016/j.jeurceramsoc.2018.11.013
Chen, Z., et al. (2019) 3D printing of ceramics: A review. J. Eur. Ceram. Soc. 39, 4, 661-687. Available at: https://doi.org/10.1016/j.jeurceramsoc.2018.11.01
Disclaimer: The views expressed here are those of the author expressed in their private capacity and do not necessarily represent the views of AZoM.com Limited T/A AZoNetwork the owner and operator of this website. This disclaimer forms part of the Terms and conditions of use of this website.