Cutting cement carbon dioxide (CO2) emissions has remained a challenge, despite widespread efforts to cut CO2 and save the planet from the worst-case-scenario outcomes of climate change predicted by the scientific community. New research has highlighted a potential path to effective carbon capture and utilization with an innovative approach utilizing carbon mineralization.
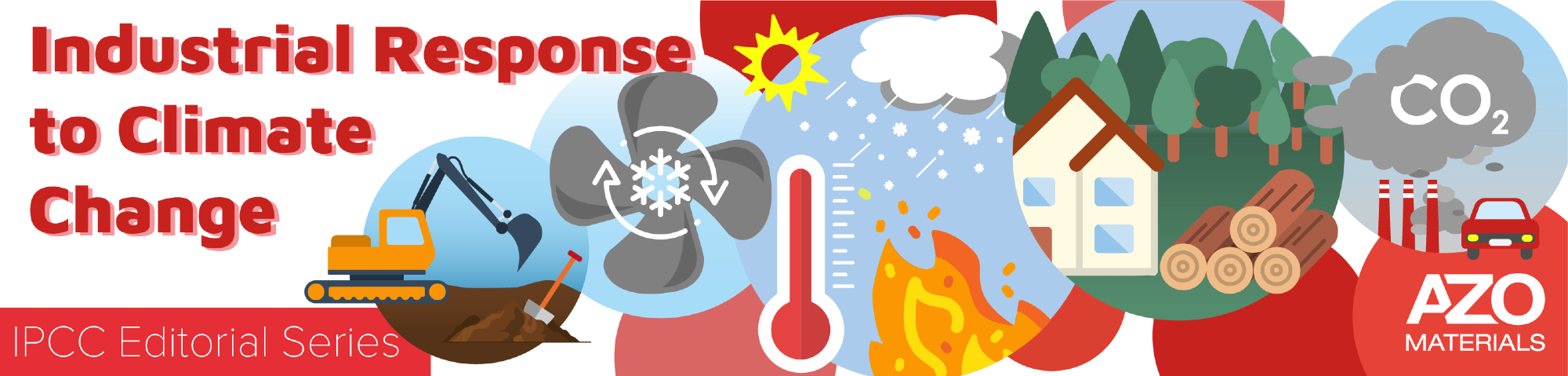
Why Is Cutting Cement CO2 Emissions Important?
There continues to be a rising demand for new buildings and infrastructure around the world, and therefore for concrete. While the ubiquitous building material causes relatively low emissions by mass (under 150 kg CO2 per ton of concrete), the sheer amount that we use means that it is responsible for up to 8% of human-induced CO2 emissions.
The latest Intergovernmental Panel for Climate Change (IPCC) report warns that we need to reach net-zero CO2 emissions by 2050 – at a minimum – to avoid the worst-case-scenario outcomes of climate change. Tackling the major problem of concrete and CO2 emissions is therefore extremely important.
First and foremost, developers, planners, and citizens have to question whether new buildings and infrastructure are necessary. Reusing and restoring old buildings, maintaining and repairing buildings, and recycling building materials can all contribute to reductions in concrete’s total environmental harm by reducing the amount of new concrete produced.
Carbon Mineralization for Reducing Concrete’s CO2 Emissions
The CO2 emissions from concrete are primarily a result of cement manufacturing processes, with clinker production cited as the leading cause.
To combat this, many researchers and cement producers have focussed on reducing the amount of clinker needed for cement. Supplementary cementitious materials (SCMs) are used to reduce the amount of clinker in cement’s content. However, almost all SCMs that are suitable for meeting the growing demand for concrete are already in use.
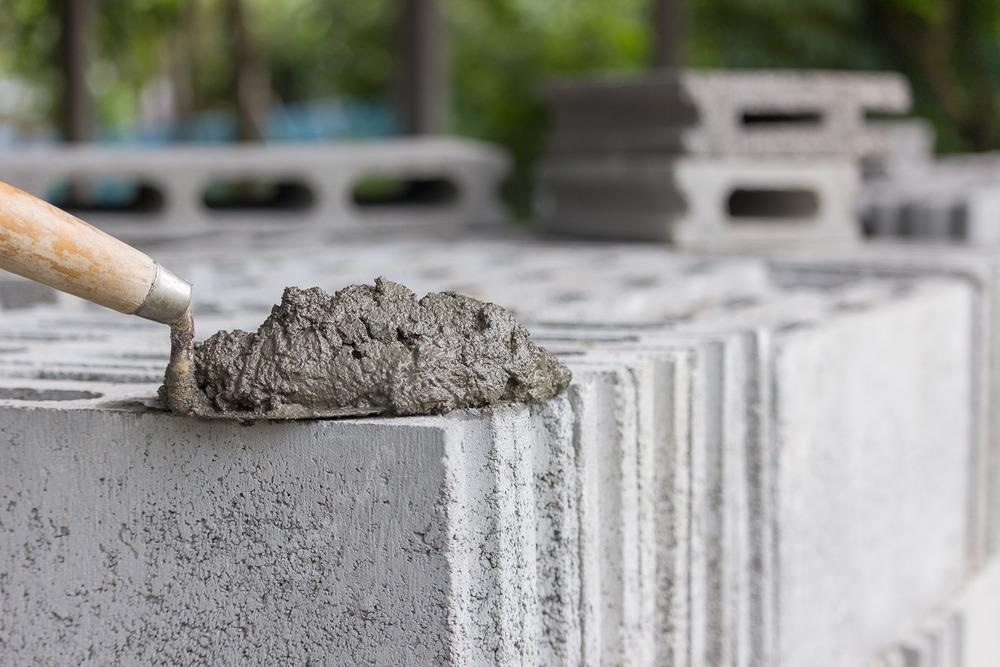
Image Credit: okcm/Shutterstock.com
Further, concrete made with SCMs has limited applicability due to a reduction in mechanical strength. Specific applications like precast concrete and high-quality clay still need a high clinker content to be used safely.
Lowering clinker content also increases the risk of neutralization of the concrete pore solution. This, in turn, can lead to reinforcement corrosion due to carbonation.
Making clinker production more energy-efficient is another method that has been pursued to reduce the amount of clinker being manufactured. However, further energy efficiency improvements can only be marginal as technology reaches the theoretical efficiency limit of clinker production.
In light of this, the only way to make cement less harmful is to capture CO2 before it is emitted in clinker production. Carbon capture and utilization methods have the best potential for improving concrete’s impact on the environment. To effectively capture carbon emissions at the source, carbon mineralization techniques need to be perfected and scaled for industrial use.
Research on Supplementary Cementitious Materials, Carbon Capture and Utilization
A literature review recently criticized the construction industry’s reliance on SCMs for reducing CO2 emissions. It found several unanswered questions regarding the carbonation of concrete made with SCMs and critiqued the extensive and almost exclusive use of SCMs in infrastructure development
A recent research paper has proposed a new carbon capture and utilization approach that could overcome these problems. Carbon mineralization of fines derived from recycled concrete led to the production of new carbonatable materials and reduction of net CO2 emissions. This paper was published in the journal Scientific Reports on March 27th, 2020.
The researchers stored captured CO2 in calcium and magnesium carbonates. These do not readily dissolve in water, so stored carbon will not be quickly returned to the hydrosphere. In fact, researchers argued these carbonates provide a permanent storage solution for CO2.
CO2 reacts with calcium or magnesium in rocks rich in alkaline earth silicates. In the natural world, silicate rocks like these react with CO2 over a geological time period. Weathering effects from calcium and magnesium carbonates as well as silicon dioxide (SiO2).
Converting this process into an industrial carbon capture and utilization technique is challenging as the reaction has to be accelerated with mechanical, thermal, or chemical treatments and conducted under extremely high pressure. Furthermore, large quantities of carbonatable materials must be mined and transported to the CO2 carbonation plant.
When CO2 has been captured, it must be used or disposed of effectively. Separating calcium and magnesium carbonates improves the usability of carbonatable materials produced from carbon capture and utilization methods.
Researchers found that these challenges are effectively met by using concrete fines – byproducts of concrete recycling – as carbonatable materials. Researchers created a hydrated paste from concrete fines that could be carbonated with much less energy than silicate rocks.
The paste is mainly made up of calcite and alumina silica gels, which are highly reactive. This means that carbon mineralization can take place within 28 days of hydration. Used as an SCM, carbonated paste saves up to 114.5 g of CO2 per 100g of paste, more than a third more savings than can be achieved with a limestone SCM.
How Can the Cement Industry Make Use of This Research and Cut CO2 Emissions?
Concrete fines are the residual material left over by concrete recycling that cannot as yet be put to use. The method proposed in this research could be applied in the concrete industry to make use of this waste while at the same time moving towards net-zero CO2 through carbon capture and utilization.
For this technology to be widely adopted, advances in concrete recycling need to come forward. Current technology does not allow for proper separation of coarse aggregates, sand, and hydrate cement paste from recycled concrete.
Finally, if this method is to reach its full potential, all of the CO2 emitted in concrete production has to be captured at the source of pollution. It will only work if it is fully adopted and supported by the industry.
--
Industrial Response to Climate Change
This article is a part of the IPCC Editorial Series: Industrial Response to Climate Change, a collection of content exploring how different sectors are responding to issues highlighted within the IPCC 2018 and 2021 reports. Here, Materials showcases the research institutions, industrial organizations, and innovative technologies driving adaptive solutions to mitigate climate change.
References and Further Reading
IPCC. (2018) Summary for Policymakers. Global Warming of 1.5 °C. An IPCC Special Report on the impacts of global warming of 1.5 °C above pre-industrial levels and related global greenhouse gas emission pathways, in the context of strengthening the global response to the threat of climate change, sustainable development, and efforts to eradicate poverty. Available at: https://www.ipcc.ch/
IPCC. (2021) Summary for Policymakers. Climate Change 2021: The Physical Science Basis. Contribution of Working Group I to the Sixth Assessment Report of the Intergovernmental Panel on Climate. Available at: https://www.ipcc.ch/report/ar6/wg1/downloads/report/IPCC_AR6_WGI_SPM.pdf
Skocek, J., M. Zajac and M. Ben Haha (2020) Carbon Capture and Utilization by Mineralization of Cement Pastes Derived from Recycled Concrete. Scientific Reports. Available at: https://doi.org/10.1038/s41598-020-62503-z.
von Greve-Dierfeld, S. et al. (2020) Understanding the Carbonation of Concrete with Supplementary Cementitious Materials: A Critical Review by RILEM TC 281-CCC. Materials and Structures. Available at: https://doi.org/10.1617/s11527-020-01558-w.
Disclaimer: The views expressed here are those of the author expressed in their private capacity and do not necessarily represent the views of AZoM.com Limited T/A AZoNetwork the owner and operator of this website. This disclaimer forms part of the Terms and conditions of use of this website.