To delay the wear resistance, coating methods have evolved significantly in recent decades as a result of the tribological needs of thermally spray coatings for wear-resistant tasks.
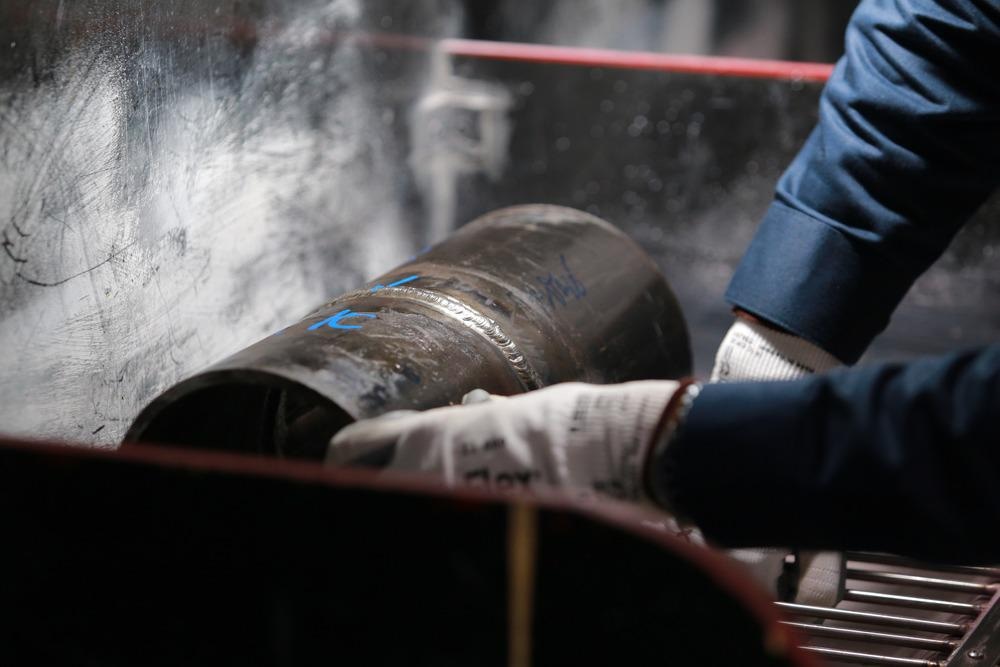
Image Credit: Thitipan Noreesuwan/Shutterstock.com
Introduction
The expectations of specific performances and lifespans of mechanical parts are growing all the time. The mechanical parts are destined to undergo various hectic wear and temperature fluctuations throughout their lifespan, and scientists are constantly looking to increase the life span of parts.
This is where advanced materials such as composites come in. To delay wear resistance, coating methods have evolved significantly in recent decades as a result of the tribological needs of thermally spray coatings for wear resistant tasks.
Thermal spraying is one of the most efficient coating deposition processes for improving wear and corrosion resistance. It is a technique that works with practically any substance and can create coatings with depths varying from a few micrometers to several mm.
The distinct characteristic properties such as thermal stability, high wettability of NiCrBSi-WC, high temperature wear resistance, and corrosion resistance deposits have made them a popular choice among the different alloy systems available.
Material Composition and Properties
At high temperatures, the NiCrBSi alloy exhibits unique properties, such as the capacity to absorb additional elements, the development of coherent and ordered strengthening phases, and microstructure stability.
Si and B are primarily responsible for wetting and lowering the melting point of NiCrBSi, Cr is utilized to increase the alloy's oxidation and corrosion resistance, while C, B, and Fe all contribute to the alloy's hardness and wear resistance.
Boride and carbide crystals are formed when the concentration of B is high enough. As a result, the NiCrBSi alloy is reinforced even further.
The characteristics of NiCrBSi, on the other hand, are unique. The contents of the elements cannot be changed indefinitely to improve the alloy.
The introduction of a ceramic particle to a NiCrBSi coating to improve its hardness and wear resistance is a suitable technique. Tungsten carbide (WC) is a crucial reinforcing agent for development of high wear resistant coatings. WC particles with a high melting temperature and exceptional hardness offer enough support for the NiCrBSi alloy matrix in harsh corrosive conditions.
Usage in Industry
As stated earlier, coating is done on parts undergoing high friction and temperature fluctuations. Rollers as well as other equipment with NiCrBSi coatings that are utilized in demanding industries like hot strip mills are subjected to a great deal of wear.
These are also used in Aerospace Applications on the bearings used in turbofan/turbo shafts engines; these bearings hold the shaft to which compressor and turbine blades are attached, and they undergo extreme temperatures and high friction. Moreover, its uses are also found in piston engines on the piston head, as it undergoes high temperatures and needs to tackle high wear and tear.
Limitations
Technological advancements is thermal spraying including the technologies of flame spraying (FS), plasma spraying (PS), and high velocity oxy fuel (HVOF) spraying are often utilized for NiCrBSi coatings.
Thermally applied NiCrBSi coatings, on the other hand, often have low to moderate adherence to the substrate and are porous.
The strength and fatigue resistance of plasma-sprayed coatings are affected by a wide number of imperfections, such as porosity and un-melted particles.
Meanwhile, with NiCrBSi coatings, the amorphous phase is always present, which arises from the rapid cooling of molten particles during accumulation, which reduces the volume sections of hard phases, lowering toughness and corrosion resistance.
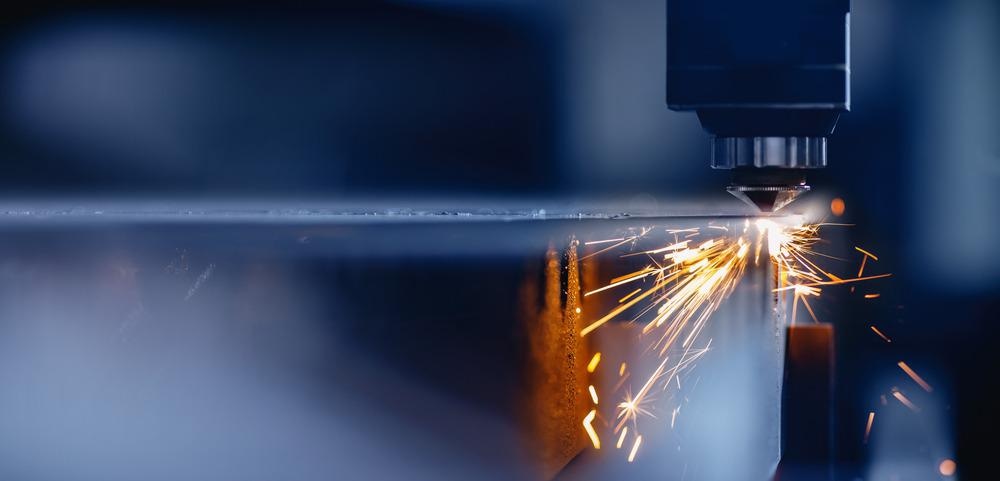
Image Credit: Parilov/Shutterstock.com
The assessment of tensile and flexural properties is difficult due to the strength of the intermolecular forces linking different faces between the accumulations and substrate.
Latest Research
The influence of short-term laser and focused heat treatment on mechanical characteristics of NiCrBSi-WC and NiCrBSi coatings is investigated in this work. Furthermore, the impact of existing distinct interface chemistry and topology on bonding strength of the substrate was studied and linked to the material characteristics of NiCrBSi-WC coatings and NiCrBSi coatings.
The major results found were as follows:
- During laser treatment, unsteady intermetallic forms found in the NiCrBSi-WC and AW NiCrBSi formations were transitioned into stable forms via metastable eutectic conversion.
- The process followed by the primary heat treatment resulted in an escalation of residual stress as the weight percentage of WC decreased.
- By re-crystallizing the residual ϒ-Ni coarsened phase and transforming higher-order destabilizing phases into lower order phases, the short duration heat treatment greatly enhanced the hardness of NiCrBSi-WC and NiCrBSi coatings.
- The secondary treatment significantly boosted the tensile and flexural strength of NiCrBSi-WC and NiCrBSi deposits, owing to the removal of microstructural flaws and the decrease of residual stress.
Benefits to Industry
Since this method increases the survivability of materials, it can be used in all those various high-performance parts which are currently limited in reaching their maximum potential due to the high wear and tear and thermodynamic stresses.
These include turbine blades in a turbo jet engine, temperature adjustment of combustion chamber in a piston engine so that the piston head does not melt, and similarly all other applications where temperature is the restricting factor.
Limitations of Current Study
Some obvious drawbacks or limitations of laser treatment includes dissolving of WC particles in a molten Ni-based matrix, which increases the porosity and reduces the hardness of the alloy.
Future work
In order to omit the few drawbacks of the current method, the following methods should be studied and applied: parameters optimization, substrate preheating, formation of gradient coatings, addition of rare-earth elements and other compounds.
References:
Chen, C., Du, C., Pan, Q., & Chen, Q. (2021). Effect of Post-Heat Treatment on the Microstructure and Mechanical Properties of Laser-Deposited WxC + Ni-Based Composite Thin Walls. Journal of Materials Engineering and Performance, 30(1), 423-433. https://link.springer.com/article/10.1007/s11665-020-05346-z
Deenadayalan, K., Murali, V., Elayaperumal, A., & Arulvel, S. (2021). Effective role of short time furnace heat treatment and laser treatment on the residual stress and mechanical properties of NiCrBSi-WC weldments produced using plasma transferred arc welding. Journal of Materials Research and technology, 15, 3492-3513. https://www.sciencedirect.com/science/article/pii/S2238785421011029
Sha, J., Chen, L.-y., Liu, Y.-T., Yao, Z.-J., Lu, S., & Wang, Z.-X. (2020). Phase Transformation-Induced Improvement in Hardness and High-Temperature Wear Resistance of Plasma-Sprayed and Remelted NiCrBSi-WC Coatings. Metals, 10(1688), 1-15. https://www.researchgate.net/publication/347821619_Phase_Transformation-Induced_Improvement_in_Hardness_and_High-Temperature_Wear_Resistance_of_Plasma-Sprayed_and_Remelted_NiCrBSiWC_Coatings
Škamat, J., Cernašejus, O., Zhetessova, G., Nikonova, T., & Zharkevich, O. (2021). Effect of Laser Processing Parameters on Microstructure,Hardness and Tribology of NiCrCoFeCBSi-WC Coatings. Materials(14), 1-15. https://www.mdpi.com/1996-1944/14/20/6034
Yao, S. H. (2014). Tribological behaviour of NiCrBSi–WC(Co) coatings. Materials Research Innovations , 18(2), 12-18. https://www.tandfonline.com/doi/abs/10.1179/1432891714Z.000000000436
Disclaimer: The views expressed here are those of the author expressed in their private capacity and do not necessarily represent the views of AZoM.com Limited T/A AZoNetwork the owner and operator of this website. This disclaimer forms part of the Terms and conditions of use of this website.