This article provides an end-of-life assessment of lithium-ion batteries, focusing on the recycling of an ever-growing amount of spent Li-Ion batteries in order to work toward a sustainable and circular approach to battery use and reuse.
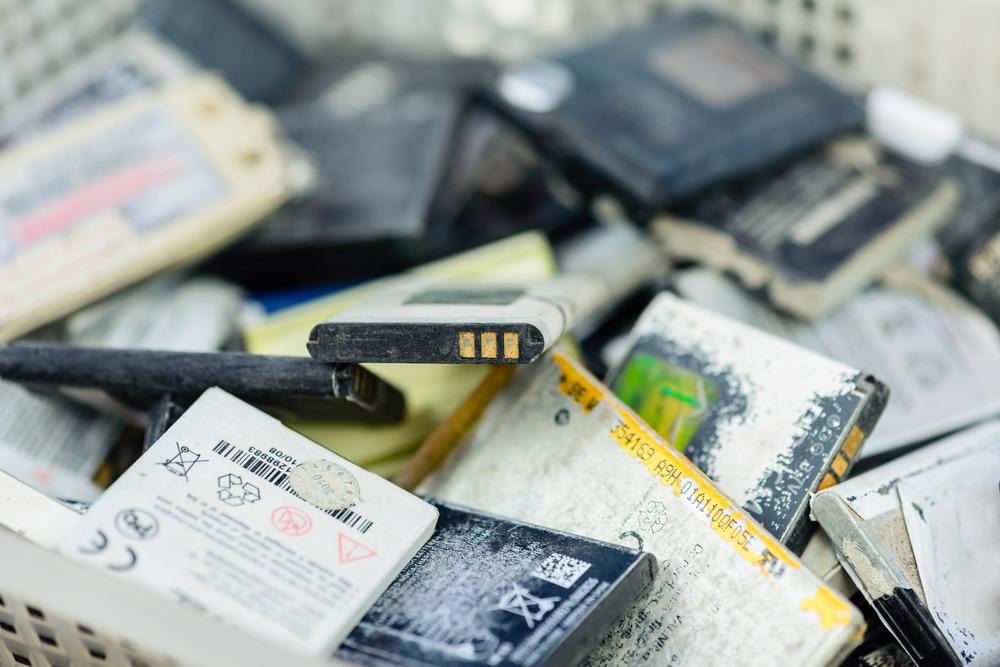
Image Credit: Vietnam stock photos/Shutterstock.com
Lithium-ion batteries (LIB) continue to gain popularity as a result of the growing demand for consumer electronics and the increasing adoption of electric vehicles and on-site energy storage solutions.
The increased use of LIBs poses severe challenges to the supply of raw materials needed for LIB manufacture. Some elements used in LIBs, such as lithium, cobalt, and graphite are scarce, are not currently mined in large quantities, or are mined in only a few countries whose trade policies could limit availability and impact prices.
The efficient recycling of the ever-growing quantity of spent LIBs can provide a pathway to lower the environmental impact of LIBs and to source sustainably high-value materials that can be used in producing new batteries.
After their successful commercialization 30 years ago, LIBs have become power sources of choice for portable electronic devices and one of the most promising solutions for energy storage in electric vehicles and stationary devices, such as Tesla's Powerwall. This widespread use in a multitude of industrial and domestic applications combined with the projected global demand for energy storage solutions, primarily driven by the growth of the electric vehicles market, has accelerated the need for an efficient recycling strategy more urgently than ever. This is especially important considering the scarcity of some raw materials used in LIBs.
LIB Types and Material Composition
A single LIB cell consists of a cathode, an anode, a separator that also contains the electrolyte, and robust housing. Many cells, interconnected in series, in parallel, or a combination of the two, are usually assembled into battery modules with the desired voltage and capacity. Depending on the requirements of the intended application, LIBs may vary in shape (consisting of cylindrical or pouch cells), size, capacity, and configuration. However, the most widely accepted classification of the LIB types is based on the cathode material.
The first commercial LIBs utilized lithium cobalt oxide (LiCoO2) as a cathode material, a graphite anode, and a conductive polymer as an electrolyte. While graphite remained the dominant anode material, the cathode composition went through significant changes. The LiCoO2 is relatively straightforward to produce and results in a stable discharge capacity of the battery.
However, the relatively high cost and environmental and safety issues concerning Co and Li mining led to the commercialization of alternative cathode materials. At present, the most widely used cathode materials include mixed oxides of Li, Ni, Co, Mn, and Al or lithium iron phosphate (LiFePO4). Many of these elements are classified as critical raw materials and emphasize the need to re-introduce end-of-life batteries and their components back into the economic cycle and reduce the need for primary raw materials.
Increased Global Production of LIBs Poses Environmental Challenges
The primary LIB manufacturing facilities are located in China, Japan, South Korea, and the United States. The three Asian countries are the major producers of LIB-specific components such as electrodes, separators, and electrolytes, and manufacture more than 80% of the global LIB supply.
Because environmental regulations concerning electronic waste and end-of-life LIBs, in particular, are not yet fully developed or implemented in most countries, the majority of these batteries currently end up in landfills, with a small fraction of the spent LIBs sent to the existing recycling facilities. Currently, the fraction of collected and recycled electronic waste in Europe is 42.5%, 11.4% in Asia, 9.4% in the Americas.
Besides, the variety of LIB sizes, configurations, and cell chemistries present a major challenge to current recycling methods as not all processes are economically viable for the recycling of any battery type.
Incentives for LIB Recycling
With more proactive regulations, an increasing supply of spent batteries, and innovations in recycling technologies, end-of-life batteries could supply a significant fraction of the materials needed for the manufacturing of new LIBs. Newly-developed regulations, such as the EU's Battery 2030+ roadmap, aim to define the responsibilities of battery manufacturers, users, and recyclers.
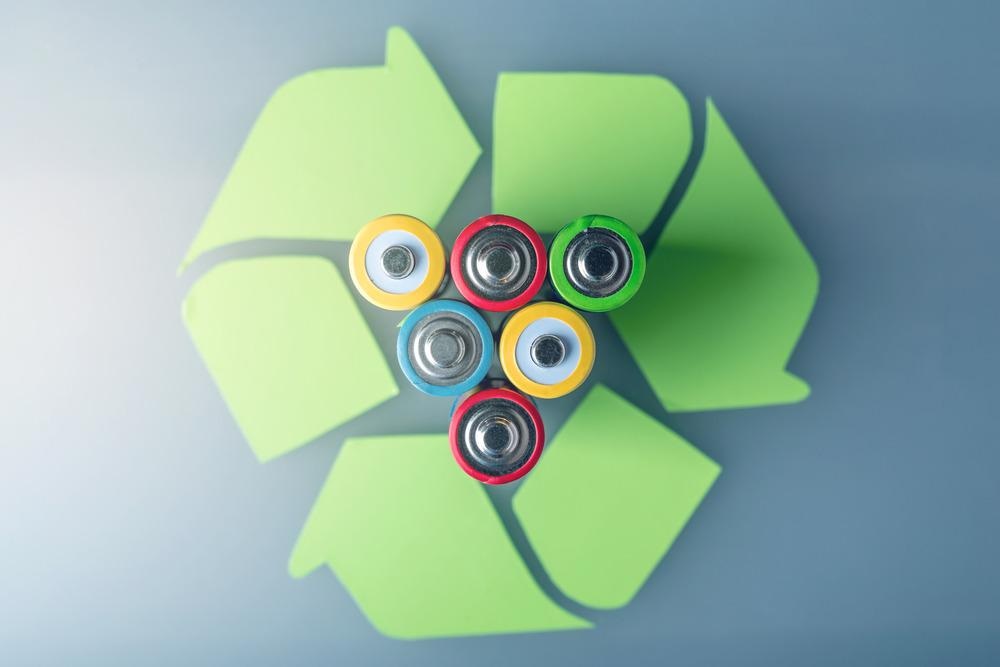
Image Credit: Artem Oleshko/Shutterstock.com
Battery manufacturers will be required to provide durability and performance data for their products and are responsible for the provenance of battery materials. These forthcoming regulations would effectively create “battery passports” which would allow end-users to identify the battery type and composition and to know where the materials come from, and their environmental impacts, so that the reuse and recycling of the LIBs can be monitored. The new rules also outline target efficiencies and material recovery rates for different recycling processes.
The Economics of LIB Recycling
The economics of recycling mostly depends on the LIB chemistry, raw material prices on the market, and the processing cost, which is expected to decrease with the expansion of the recycling capacity. The variety and complexity of LIB chemistry impede to some extent the efforts to establish a streamlined recycling process suitable for all kinds of LIBs.
For example, the demand for higher energy density in EV batteries shifts battery development towards using cathodes with higher nickel content, while the desire to reduce battery costs favors lower-value lithium iron phosphate cathodes. Such diversity affects the value that can be extracted from end-of-life LIBs. The most value can be extracted from cathodes with high cobalt content. Such batteries are typically used in consumer electronics and account for a diminishing part of the spent LIBs.
Current State of LIB Recycling
There are more than fifty companies worldwide that process spent LIBs, with a recycling capacity of around 400 000 tons. The majority of the companies operate in China and South Korea, followed by the EU, Japan, Canada, and the USA. Improving the recycling technology of LIBs is a continuous effort and recycling is far from maturity today.
End-of-Life LIB Pre-Treatment Processes
Preparing LIBs for recycling involves two main processes - discharging and dismantling of the battery modules (including removal of major components, such as cables, frames, electronics, and others). After the battery dismantling, the components undergo mechanical processing and separation based on their different physical properties, including particle size, density, conductivity, magnetic properties, and others.
Batteries are discharged before dismantling to ensure the safety of the personnel and to eliminate the risk of electric shock and fire. Discharging can be performed by different methods like thermal treatment, salt-water-based baths, controlled discharging via an external circuit, or via cryogenic treatment using liquid nitrogen. The salt-water-based discharge is the most preferable method in the industrial environment as it is a sufficiently safe way to discharge and stabilize various types of high-energy-density cells.
Mechanical Pre-Treatment
Next, the spent LIBs are subjected to multi-stage mechanical pre-treatment that involves shredding, crushing, impact fragmentation, magnetic separation, flotation, and other processes. The purpose of this step is to disintegrate the batteries and separate particular components into different recycling streams.
A particular emphasis is placed on the separation of the metallic particles (casing, conductors) and the concentration of the so-called black mass, which is the mixture of cathode and anode active materials. The black mass is the most valuable LIB component and the mechanical pre-treatment is optimized for its maximum recovery and separation. Usually, an inert atmosphere (CO2 or nitrogen) is used during the crushing process.
Thermal Pre-Treatment
Thermal pre-treatment methods enable safe deactivation of the combustible components of the LIB electrolyte. At the same time, the battery is discharged, while the conductive carbon components and organic binder materials decompose (at temperatures above 600 °C).
Choosing an appropriate temperature range during that step facilitates the recovery of lithium and other metals further downstream. However, all plastic components and electrolytes are lost during the process. Alternatively, oxygen-free pyrolysis enables the transformation of the organic materials into lower molecular compounds and their recovery by recondensation.
Recycling Methods for High-Value LIB Components
Pyrometallurgy uses heating to convert metal oxides used in battery materials to metals or metal alloys. After the pretreatment, the battery materials are smelted in a reductive environment (either vacuum or inert gas atmosphere) to convert the metal oxides to a mixed metal alloy containing (depending on the battery composition) Co, Ni, Cu, Fe, and non-recyclable slag containing Li and Al.
Pyrometallurgical methods require simpler pretreatment methods (usually shredding or crushing) to prepare batteries for recycling and can accommodate LIBs of differing compositions, shapes, and sizes. Some pyrometallurgical methods can recycle Li, but overall these methods are most effective for extracting and recycling high-value metals such as Co.
Volkswagen Electric Car Battery Recycling Plant
Video Credit: YOUCAR/Youtube.com
Hydrometallurgical methods use aqueous solutions to extract and separate metals from LIBs. The pretreated battery materials (with Al and Cu conductors previously removed) are most often subjected to extraction with H2SO4 and H2O2, although HCl, HNO3, and organic acids including citric and oxalic acids can also be used. Once metals have been extracted into solution, they are precipitated selectively as salts using pH titration or extracted using organic solvents containing dialkyl phosphates or phosphinates.
At present, hydro- and pyrometallurgical approaches dominate the recycling of metals from cathode materials. The global trend is to shift most of the recycling operations towards using hydrometallurgical approaches, owing to their ability to recover larger amounts of battery components and reach very high purities of metal salts.
Future Developments for the Recycling of Next-Generation LIBs
An important concept that can facilitate the development of an efficient circular battery economy is the so-called design for recycling. This concept is focused on considering the eventual recycling treatment of the battery cells during the initial design stage of the battery. Such an approach would enable fully automated battery disassembly and minimize pre-treatment costs.
Streamlined battery designs that allow facile disassembly would also make the direct recycling methods much more effective. Currently, the direct recycling methods involve the reuse of end-of-life LIBs from electric vehicles in stationary applications. Such an approach requires battery type classification and determination of the charge state and the residual capacity of the recycled batteries.
By using standardized cell designs and specific battery chemistries, the regeneration of the batteries would be possible via exposing cathode material to moieties with high lithium content and repacking it into new battery cells.
In addition, the use of novel methods, such as high-voltage treatment or the use of supercritical CO2, would permit more effective material separation. This, in turn, would improve the recycling efficiency of carbon material (such as graphite and carbon black used in the anodes) and electrolytes. Supercritical liquid media extraction has already demonstrated relatively good recovery rates for both electrolytes and binders.
The rapid development of efficient and sustainable recycling processes is the only option to re-introduce end-of-life batteries and their components into the economic cycle and reduce the need for primary raw materials.
References and Further Reading
Bird, R., et al. (2022) The Regulatory Environment for Lithium-Ion Battery Recycling. ACS Energy Letters, 7(2), 736-740. Available at: https://pubs.acs.org/doi/10.1021/acsenergylett.1c02724
Baum, Z. J., et al. (2022) Lithium-Ion Battery Recycling─Overview of Techniques and Trends. ACS Energy Letters, 7 (2), 712-719. Available at: https://pubs.acs.org/doi/10.1021/acsenergylett.1c02602
Neumann, J., et al. (2022) Recycling of Lithium-Ion Batteries—Current State of the Art, Circular Economy, and Next Generation Recycling. Adv. Energy Mater. 2102917. Available at: https://onlinelibrary.wiley.com/doi/10.1002/aenm.202102917
Windisch-Kern, S., et al. (2022) Recycling chains for lithium-ion batteries: A critical examination of current challenges, opportunities and process dependencies. Waste Management, 138, 125-139. Available at: https://www.sciencedirect.com/science/article/pii/S0956053X21006267?via%3Dihub
Hu, Qiushi and Xu, Linghong (2021) An overview on Lithium-ion batteries recycling processes. Journal of Physics: Conference Series, 1885. Available at: https://iopscience.iop.org/article/10.1088/1742-6596/1885/3/032031
Miao, Y., et al. (2022) An overview of global power lithium-ion batteries and associated critical metal recycling. Journal of Hazardous Materials, 145, 127900. Available at: https://www.sciencedirect.com/science/article/pii/S0304389421028697?via%3Dihub
Disclaimer: The views expressed here are those of the author expressed in their private capacity and do not necessarily represent the views of AZoM.com Limited T/A AZoNetwork the owner and operator of this website. This disclaimer forms part of the Terms and conditions of use of this website.