As opposed to conventional metal alloys, metal matrix composites (MMCs) possess inimitable physical, thermal, electrical, chemical, and mechanical properties that make them most suitable in today’s product-based manufacturing processes. With the need for continuous improvements in materials and manufacturing processes, MMCs continue to displace traditional materials and address recent advances and requirements in material science, aerospace manufacturing, automobile engineering, biomedical engineering, defense, and many other areas.
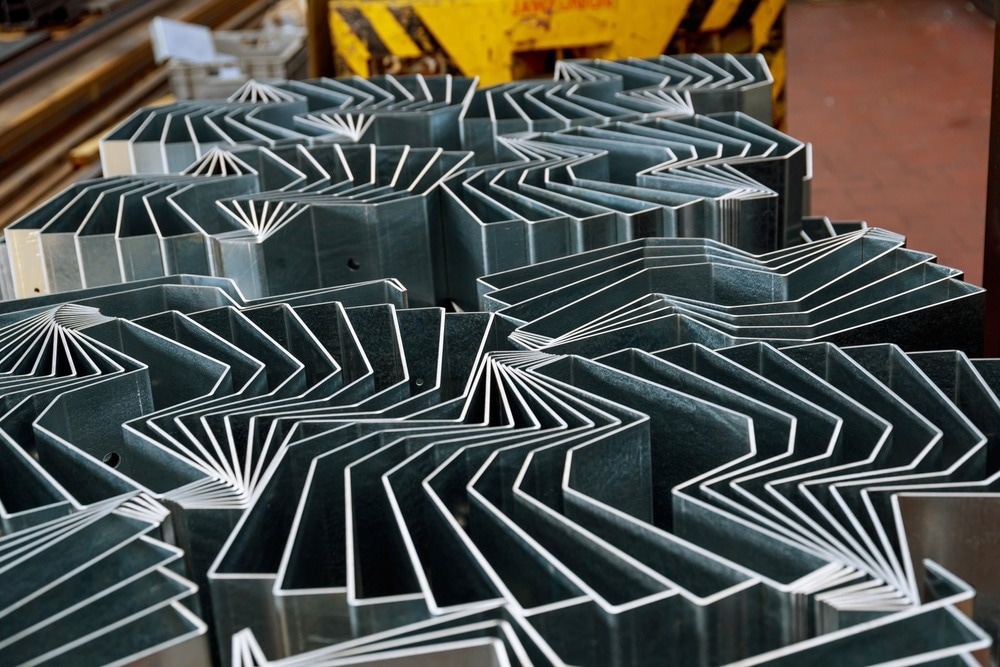
Image Credit: ZhakYaroslav/Shuttterstock.com
MMCs are a combination of foreign reinforcements dispersed in a metallic matrix. Depending on the intended properties of interest, the mount could be carbon materials, ceramics, or other metals. This distinct feature makes MMCs a better alternative to conventional materials in that the perceived property of the resulting composite can be modified for the intended purpose. The most popular metals include Cu, Ti, Mg, Al, and their respective alloys. However, the most widely researched MMCs are aluminum-based composites for their peculiar advantages.
Despite these advantages, limited expertise and high production costs have been a significant challenge to the commercialization and subsequent application of MMCs across different sectors. Recent studies and advancements have focused on improving the properties of these composites for specific purposes and optimizing the manufacturing processes. This article highlights recent studies and advances in the manufacturing and applications of MMCs.
Preparation Methods and Properties of MMCs
By studying and integrating the law of interfacial reaction between the reinforcement and the metal matrix, many researchers have developed various methods for preparing metal matrix composites. Solid-state and liquid-state techniques are the most common conventional manufacturing processes for MMCs, and each method has its advantages in terms of cost and the desired properties.
Solid-state fabrication techniques involve the processes of powder metallurgy, diffusion bonding, and friction stir processes. Powder metallurgy (PM) is the most common technique, and in general, solid-state fabrication processes are carried out below the melting point of the metal matrix.
In powder metallurgy, the metal matrix and the reinforcement materials are combined in the desired proportions, compressed into the desired shape, and allowed to bond in the solid-state by heating at a temperature just below the melting point of the materials in use.
In a study in the journal Materials Today: Proceedings, the authors investigated the fabrication of an Al-SiC metal matrix composite using a solid-state powder metallurgy technique to observe its mechanical properties. According to the researchers, the justification for this approach is based on the fact that powder metallurgy can produce MMCs with novel components and properties depending on the starting materials in use. Through the process of blending, compaction, and sinistering, the reinforcement materials were distributed homogenously in the metal matrix phase, and no byproduct was reported. The mechanical properties of interest, such as density, porosity, and hardness, were evaluated, and significant improvements were noted.
In another study in the Journal of Physics: Conference Series, the mechanical properties of metal matrix composites Al-Cu-Mg/SiCp fabricated using powder metallurgy were reported. After mixing the powders in the desired proportions, it was subjected to a hot-pressing process at 350oC followed by sinistering at 500oC for one hour. The final aging step lasted for 16 hours, after which the final composite material was subjected to various analyses to determine its physical and mechanical properties. The results, as reported, showed significant improvement in the hardness of the fabricated MMCs.
A convergence of recent studies shows that solid-state powder metallurgy is one of the most widely used fabrication methods for high-performance aluminum MMCs. Relative to the liquid-state method with similar material components, MMCs fabricated using PM offer significantly improved mechanical, chemical, and physical properties. This advantage comes as a result of the reduction in the level of undesired interfacial interactions. However, PM techniques are costlier, which remains a significant challenge.
Liquid-state fabrication techniques involve casting and infiltration methods. This technique is carried out at higher temperatures, usually about the melting point of the metal matrix, because it has to take place in the molten state. There are various casting approaches.
Stir casting is the most popular and economical method for fabricating MMCs for industrial applications. In principle, the metal matrix is in the molten state, and the reinforcing materials are added with constant stirring to ensure the even dispersion of the material. This method is cost-effective, which explains its popularity. Unfortunately, it is sensitive to particle size and only allows for the dispersal of small-size reinforcements.
Infiltration, on the other hand, is a high-cost process involving transporting the reinforcement particles into the pores of the metal matrix through a gas or vacuum. This process allows for the formation of high-volume composites (up to 70% vol %) with near-net-shape. This method is expensive and requires an advanced fabrication setup, making it unsuitable for large-scale production.
In a study reported in the journal Materials (Basel), the authors reviewed the properties of AA 6061 Metal Matrix Composites fabricated using the stir casting method. Various reinforcements, including nanomaterials and metal alloys such as SiC, TiC, and B4C were used. In all of these studies, the authors reported a positive correlation between the mechanical and tribological properties of the composites and an increase in the reinforcement material.
Applications and Future Trends
The search to continuously develop materials with improved mechanical, physical, and chemical properties for various industrial applications is a subject of interest in contemporary times. MMCs are replacing conventional metal alloys because they can pre-determine their properties for specific applications. The most coveted properties of MMCs include their high-strength to weight ratio, density, durability, high tensile strength, improved wear resistance, hardness, and many others. These properties make MMCs highly valuable in marine engineering, defense, biomedical engineering, automobile, and aircraft manufacturing.
In the automobile industry, aluminum MMCs find practical applications in manufacturing lightweight brake calipers, piston pins, pistons, connecting rods, and other engine components. Across different sectors, aluminum MMCs are the most widely used, which explains their popularity.
The integration of nanoparticles or nanotubes in the fabrication of MMCs is yet to be fully explored and commercialized. So far, recent studies show that these categories of MMCs have the potential to substitute conventional materials, as has been seen in the use of carbon nanotubes in place of carbon fibers. To continuously improve the properties of MMCs and develop cost-effective and convenient fabrication methods, nanoparticles can play a significant role in that effect.
References and Further Readings
Sharma, A. K., Bhandari, R., & Pinca-Bretotean, C. (2021). A systematic overview of fabrication aspects and methods of aluminum metal matrix composites. Materials Today: Proceedings, 45, 4133–4138. doi:10.1016/j.matpr.2020.11.89
https://www.sciencedirect.com/science/article/pii/S2214785320395754
Jiju, K. B., Selvakumar, G., & Ram Prakash, S. (2020). Study on preparation of Al – SiC metal matrix composites using powder metallurgy technique and its mechanical properties. Materials Today: Proceedings. doi:10.1016/j.matpr.2020.04.001
https://www.researchgate.net/publication/341047376_Study_on_preparation_of_Al_-_SiC_metal_matrix_composites_using_powder_metallurgy_technique_and_its_mechanical_properties
Susula, A. B., Suguhartono, I. and Marpaung, M. A. (2019). Study on mechanical properties of Metal Matrix Composites (MMCs) Al-Cu-Mg/SiCp with Powder Metallurgy. Journal of Physics: Conference Series, 1402(4).
https://iopscience.iop.org/article/10.1088/1742-6596/1402/4/044109
Kareem, A., Qudeiri, J. A., Abdudeen, A., Ahammed, T., & Ziout, A. (2021). A Review on AA 6061 Metal Matrix Composites Produced by Stir Casting. Materials (Basel, Switzerland), 14(1), 175.
https://pubmed.ncbi.nlm.nih.gov/33401426/
Kumar Sharma, A., Bhandari, R., Aherwar, A., Rimašauskienė, R., & Pinca-Bretotean, C. (2020). A study of advancement in application opportunities of aluminum metal matrix composites. Materials Today: Proceedings. doi:10.1016/j.matpr.2020.02.516
https://www.sciencedirect.com/science/article/pii/S2214785320312712
Ayar, M. S., George, P. M., & Patel, R. R. (2021). Advanced research progresses in aluminium metal matrix composites: An overview. PROCEEDINGS OF THE 14TH ASIA-PACIFIC PHYSICS CONFERENCE. doi:10.1063/5.0036141
https://aip.scitation.org/doi/pdf/10.1063/5.0036141
Kim, D. Y., & Choi, H. J. (2020). Recent Developments towards Commercialization of Metal Matrix Composites. Materials (Basel, Switzerland), 13(12), 2828.
https://www.ncbi.nlm.nih.gov/pmc/articles/PMC7345546/
Disclaimer: The views expressed here are those of the author expressed in their private capacity and do not necessarily represent the views of AZoM.com Limited T/A AZoNetwork the owner and operator of this website. This disclaimer forms part of the Terms and conditions of use of this website.