Industrial plants tend to rely on oil to keep things running. Whether utilized as a fuel or lubricant, oil is the substance generally responsible for keeping industrial processes functioning in an efficient manner.
It is crucial that accurate and routine oil condition monitoring is carried out for most industrial applications, as degraded and contaminated oils can cause expensive equipment failures and slow down production.
Furthermore, good monitoring is vital for the safety of those working in industrial settings around systems and machinery deemed potentially hazardous.
Oil condition monitoring can be applied for early-warning systems, fault diagnosis, and data-driven maintenance scheduling.1 Friction, wear, and contamination from the buildup of particulates or overexposure to moisture are the leading causes of deterioration in oil condition.
Oil quality degradation can also impede mechanical performance properties, which means that parts are lubricated less effectively.
There are various methods when it comes to conducting oil condition monitoring. Some monitoring is carried out with offline analysis, whereby a sample of oil is processed in the laboratory. Other measurements can be conducted using sensors, viscometers, or spectrometers in-situ while offering real-time testing.2
To determine what testing methods are required for specific applications, it is important to pay consideration to whether the oil is safe and non-disruptive to the sample or whether continual processing monitoring is required.
Regardless of the method used, it is vital to have materials that can act as a reference standard. Reference standards are the chemicals used to assess process and product performance.
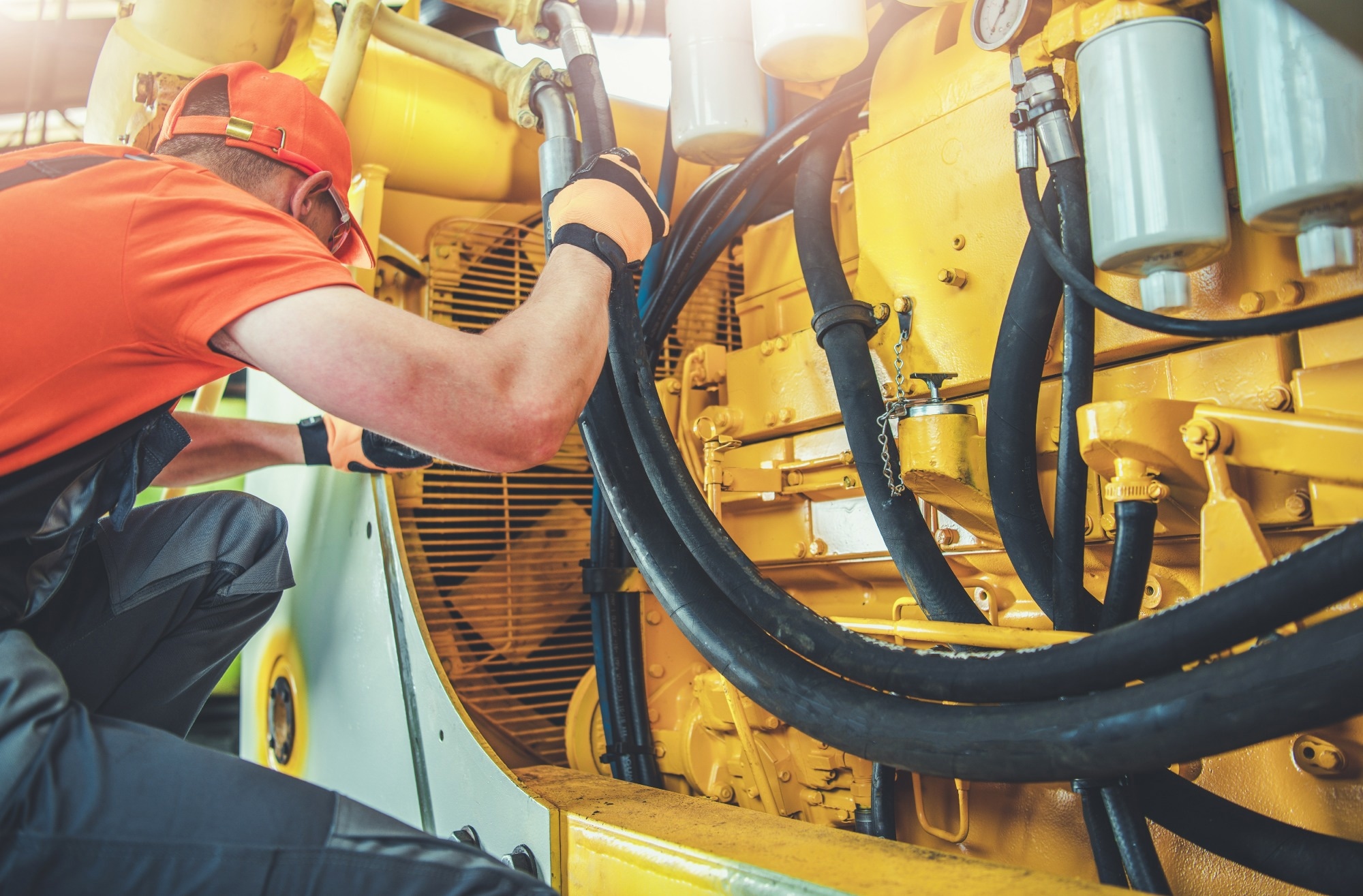
Image credit: LGC Standards
Applying Reference Standards
Reference materials for assessing soot levels in diesel by infrared spectroscopy would contain the concentration of soot already known in order to effectively evaluate the intensity and position of the features in the infrared spectrum.
The reference material would be used to assess the performance of the spectrometer, which also includes checking the wavelength calibration. A range of reference standards could also be used for detector calibration as a function of sample concentration that could then be transferred when evaluating an unknown sample.
Another typical use of reference standards relates to assessing the levels of sulfur or wear metals in oil. These chemical contaminants can cause undesirable thickening of the oil. 3 Monitoring their concentration offers a good indication of the wear rate of mechanical components, facilitating pre-emptive maintenance of worn machinery.
The effects of water or moisture contamination can cause complicated issues which pose a real risk to equipment and operators.
The Crackle Test monitors the moisture content in oil as water can have an adverse effect on both machine parts and the oil that is used to lubricate them.4 For example, water can cause a chemical reaction with compounds in the oil and degrade the machine.
Industries
Oil testing is absolutely essential in industry; though different varieties of oil types, applications and performance requirements mean there is no universal approach.
Choosing the appropriate reference standard for oil condition monitoring is dependent on the type of test being performed – whether it be for the concentration of a specific contaminant or the viscosity of worn oil.2
For automotive and transportation applications, gasoline and similar standards are amongst the most important for oil condition monitoring. It is essential that the selected reference accurately reflects the composition of the 'real' samples. For instance, it may be necessary to choose high-temperature oil variants when monitoring oils in engines.
Aerospace and marine oil monitoring applications are faced with unique challenges due to environmental conditions being prone to severe and rapid change. Marine and aerospace applications are amongst the most stringently regulated, so it is crucial that oil monitoring is carried out to check for excess wear to prevent any safety issues.
Density, viscosity, and chemical contamination checks are important for fuel production companies. Fuel producers may also apply flashpoint analysis as a quality control measure. Standard references for flashpoint analysis are easily accessible as combustion temperature is related to the chemical composition of the fuel.
The oil, gas, and mining industries all use heavy industrial equipment in their applications, and the majority of this equipment is located in regions where access to maintenance is expensive.
One of the benefits of oil condition monitoring is that scheduling of maintenance work can be planned for when it is needed rather than being integrated into a calendar routine. For example, mining sites are dependent on heavy-duty drilling, blasting, and transportation equipment.
On an isolated site, equipment failure can be disastrous as well as expensive, and repairs can be time- and labor-intensive, leading to delays across the entire operation. In applications like these, oil condition monitoring is vital to properly track and maintain the condition of key pieces of equipment and make sure that they are functioning properly.5
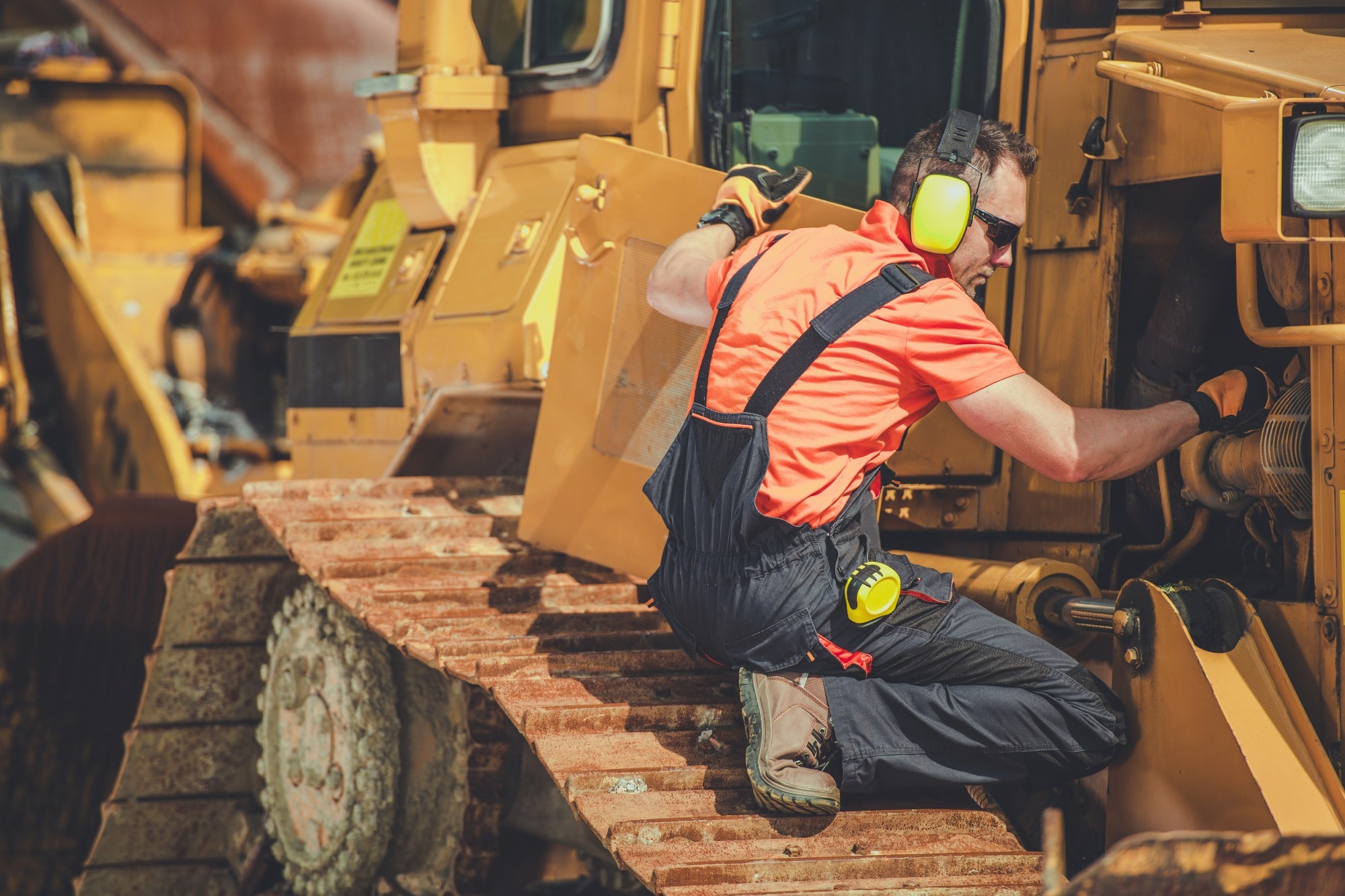
Image credit: LGC Standards
LGC Standards
To achieve operational savings with oil condition monitoring, LGC Standards are of great help. With a comprehensive catalog of reference materials for fuels and lubricants that meet the highest quality standards, LGC Standards can offer all that is essential when it comes to oil condition monitoring.
As an industry leader for more than 30 years, LGC Standards has extensive experience when it comes to producing reference materials for petrochemical and industrial applications.
Alongside their extensive inventory of reference materials, LGC Standards also offers custom solutions and consulting to help customers find the right solution for oil condition monitoring applications to achieve the right results.
References
- Wakiru, J. M., Pintelon, L., Muchiri, P. N., & Chemweno, P. K. (2019). A review on lubricant condition monitoring information analysis for maintenance decision support. Mechanical Systems and Signal Processing, 118, 108–132. https://doi.org/10.1016/j.ymssp.2018.08.039
- Mujahid, A., & Dickert, F. L. (2012). Monitoring automotive oil degradation: analytical tools and onboard sensing technologies. Anal Bioanal Chem, 404, 1197–1209. https://doi.org/10.1007/s00216-012-6186-1
- Introduction ICP-Optical Emission Spectroscopy Analysis of Wear Metals and Additive Package Elements in New and Used Oil Using the Optima 8300 ICP-OES with Flat Plate Plasma Technology. (n.d.). Retrieved June 14, 2022, from https://www.perkinelmer.com/
- Noria Corporation. (2019, June 27). Monitor Water-In-Oil with the Visual Crackle Test. Machinerylubrication.com; Noria Corporation. https://www.machinerylubrication.com/Read/301/visual-crackle-oil-test
- Mining & Construction - Fluid Life. (2022, February 10). Fluid Life. https://www.fluidlife.com/industries-served/mining-and-construction/
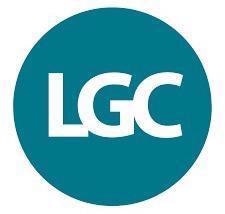
This information has been sourced, reviewed and adapted from materials provided by LGC Limited.
For more information on this source, please visit LGC Limited.