The Technetics Group is a renowned designer and manufacturer of sealing and component solutions such as sub-systems and assemblies. The company works closely with its customers, dealing with clean sheet designs that require specific sealing solutions in critical component applications.
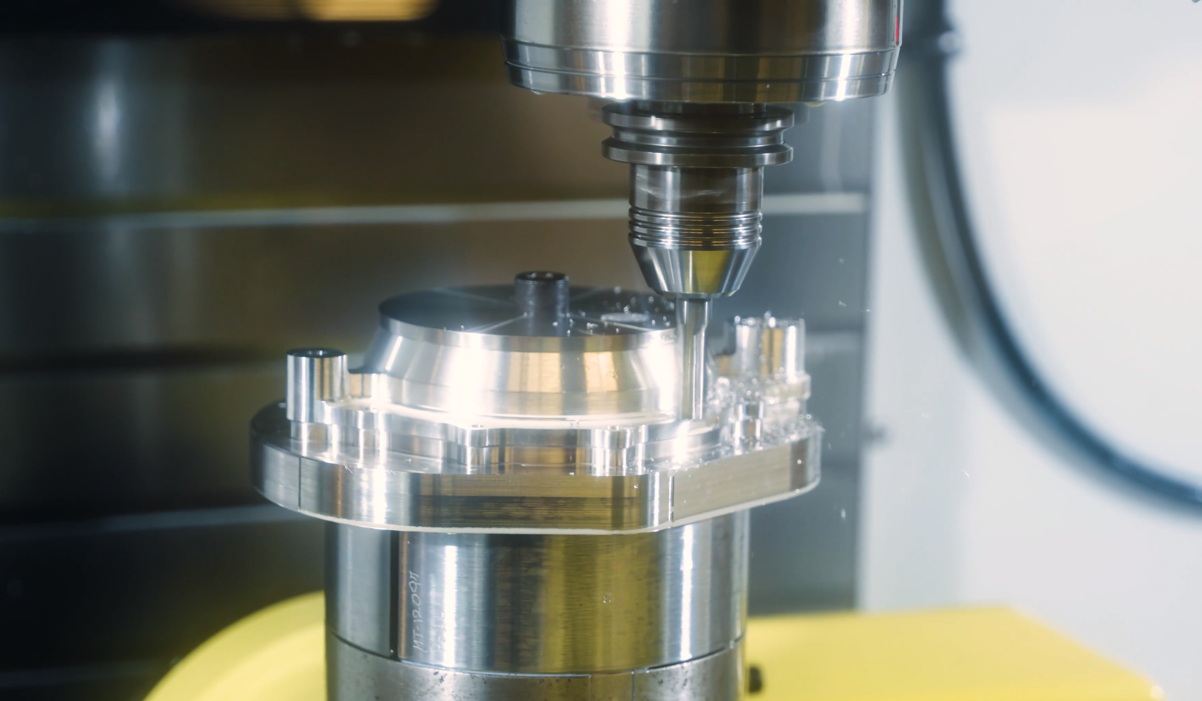
Image credit: Technetics Group
In this interview, Jason Riggs and Bob Jones of Technetics Group discuss the creation of mechanical seal solutions.
Could you please introduce yourselves and provide a quick overview of your roles at Technetics?
Jason Riggs: My name is Jason Riggs, and I support Technetics’ global aerospace product lines.
Technetics does things differently than its competitors, building close customer relationships over time. Our customers have learned that our process yields a robust sealing solution that works the first time, every time. Through those experiences, Technetics gains its customer’s trust, allowing us to confidently tell our customers that a robust solution is imminent.
Bob Jones: I am Bob Jones, General Sales manager with Technetics Group Chicago. I have over 20 years of experience in the field.
Our process starts with gathering the inputs needed to develop a preliminary seal design, compliance matrix, and project schedule. After collecting the design inputs, the first step is a preliminary design review with the customer. Technetics will present the initial seal design in a plan to validate the design requirements. The company uses a compliance matrix to identify the needs and how each will be validated while providing a plan to mitigate high-risk design requirements.
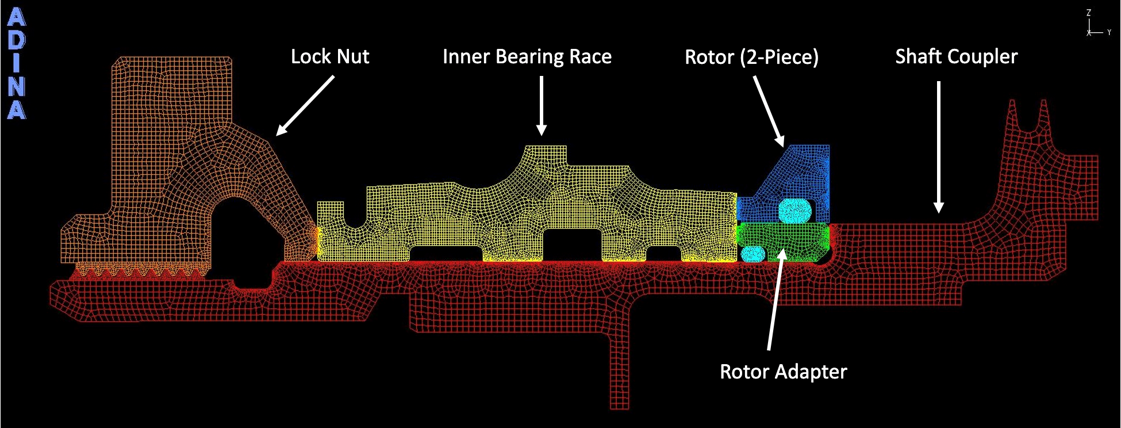
Image credit: Technetics Group
How do you typically oversee your projects, and how does the design review process begin?
Bob Jones: Technetics’ review of the schedule during the preliminary design review helps us allocate the resources we need to support the project. The initial design review starts with the analysis of the surrounding components. This includes the operating environments, materials, configuration, and assembly.
Technetics uses a unique FEA tool to review clamp loads and thermal effects on seal components, which we have found to be very helpful in analyzing coating and distortion effects. The company also looks at vibration and seal face loads while reviewing the surrounding components.
In some applications, we incorporate a secondary seal using metal bellows. Bellows provide a spring force to keep the sealing faces closed during shutdown. The design of the bellows includes stress and resonance analysis; in some cases, we test to validate some of the design requirements. We work with Technetics Daytona to design and produce the bellows. They have been manufacturing metal bellow seals since the 1950s.
What seal solutions does Technetics offer?
Bob Jones: Technetics Group Chicago offers contacting and non-contacting mechanical face seal designs. The non-contact or hydrodynamic face seal designs are often the best solution for high-speed applications with a low-pressure differential. This technology is often used to seal small main shaft bearing locations, gearboxes, and aero accessories.
Our hydrodynamic analysis includes a prediction of lift-off speed throughout the operating range, including high-altitude conditions. Technetics also offers different hydrodynamic designs that can be used to optimize lift-off, speed, form thickness and stiffness.
What are specific design features crucial to ensuring a good seal?
Bob Jones: A key element to the seal design would be rotor deflection. Technetics has designed face seals to maintain flatness and manage deflections and lubrication at the primary sealing faces; all three elements must work together.
Image credit: Technetics Group
The design analysis includes the unique FEA software, which provides a better understanding of the effects of flatness and deflections due to clamp load forces in the operating environment. Maintaining rotor flatness and optimizing face coating is a crucial element when it comes to effective hydrodynamic performance.
Does Technetics have a validation or testing process that ensures the integrity of your products?
Bob Jones: Yes, Technetics looks at the leakage and life of the seal. A small amount of lubrication film is required at the interface of a contacting seal to manage face temperature. This lubrication film helps cool the interface, eventually passing through it and resulting in a small amount of leakage.
Our design tool estimates the leakage rate and can predict the amount of heat generation at the interface, enabling us to estimate the seal life.
Once we have completed the prototyping phase and the production of parts is initiated, we will carry out a couple of critical tests in a production process to validate that we have adequately built parts.
The first is a face load test to validate the assembly process. We measure the face loading versus the drawing requirement, ensuring that it meets the specifications. We also carry out a vacuum or pressure check to validate the integrity of the secondary seal and the flatness of the primary sealing faces.
Why do customers approach Technetics for a solution when the previous vendor failed to solve the problem?
Bob Jones: Through our design analysis, we use four dynamic test rigs to validate some of the key elements of the design. We use the rigs to simulate the operating pressure speeds and temperature conditions to see what the seal will be exposed to throughout the duty cycle. We can measure leak rate, wear and face temperature and then compare the results to the analysis to validate a design. We can also determine the lift-off speeds for hydrodynamic face seals by measuring face temperature.
Image credit: Technetics Group
Technetics continues to invest in the resources and processes required to support the demanding requirements of the aerospace industry. Our robust quality system has resulted in an outstanding quality record with our major OEM customers. We have a fully integrated business system software designed specifically for the manufacturing environment. We continue to invest in our people to allow them to reach their full potential.
How long does it take to go from a design stack to hardware delivery?
Jason Riggs: It depends on how well-defined the application is, the type of seal we will be utilizing, and the complexity of the design.
In general, project turnaround could be as quick as three months, but typically, it is a year, sometimes even longer. It depends on how well-defined the application is and how tight the design specification is. In reality, this ends up being a collaborative effort with our customers. So the project timeline is a function of the inputs we receive from our customers.
Do you provide detailed analysis to show compliance with design requirements?
Bob Jones: We provide a complete design review, including an initial design review to the customer that eventually evolves into a more critical design review and a final design review presentation.
The design review document also serves as a living document, which we amend as the product evolves and things change, or we learn that would apply to the design. You could pick it up ten years from now when you have the complete history of what happened with the particular seal design.
How do you handle the costs associated with the design analysis, design reviews, and so on?
Jason Riggs: We typically quote those deliverables as non-recurring engineering charges. In some cases, we are asked to perform qualification testing. That will typically involve a combination of in-house costs plus expenses from outside vendors and test houses, depending on the scope of work. We usually quote these types of activities as non-recurring engineering charges.
What solutions does Technetics have for high-vibration environments?
Jason Riggs: Technetics Chicago has quite a bit of experience in high-vibe and shock environments. We often use bellows or a spring to keep the seal nose in contact with the mating ring or a rotor for contacting face seals. Other applications can leverage our hydrodynamic lift-off technology, which works very well in high-vibration environments, mainly due to the higher film stiffness and thickness that our proprietary hydrodynamic seal designs provide.
How much manufacturing does Technetics complete in-house?
Bob Jones: Technetics does most of its key processes in-house, including lapping and manufacturing many components. We make the housing and the mating rings in-house.
The company does use subcontractors for o-rings, springs and washers, but it does control many of the critical manufacturing processes that go into making its product.
About Jason Riggs 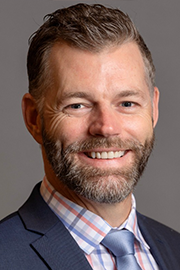
Jason Riggs is the Director of Strategy for Technetics, responsible for driving organic and inorganic growth strategies. He’s an aerospace industry veteran with over 25 years of experience in strategy, business development, and engineering for various engineered product companies. Jason is an Arizona native and Arizona State University graduate with a Mechanical Engineering degree and an MBA.
About Bob Jones
Bob Jones has worked in the aerospace industry for more than 40 years in various roles, including customer support, project management and new business development. He has been the liaison between the customer and our engineering team to facilitate the design and production of custom engineering sealing solutions for rotating shafts. He enjoys the challenge of helping customers solve demanding sealing applications while supporting the project schedule.
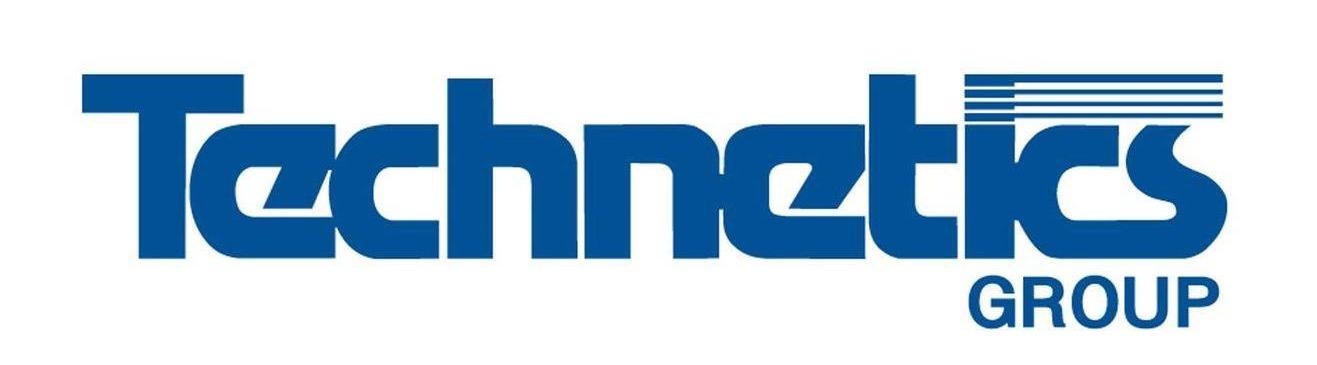
This information has been sourced, reviewed and adapted from materials provided by Technetics Group.
For more information on this source, please visit Technetics Group
Disclaimer: The views expressed here are those of the interviewee and do not necessarily represent the views of AZoM.com Limited (T/A) AZoNetwork, the owner and operator of this website. This disclaimer forms part of the Terms and Conditions of use of this website.