Thermomechanical analysis (TMA) is a thermal analysis technique that measures dimensional changes at a micrometer scale, such as deformation, in a material’s properties against time or temperature while applying a constant force (under non-oscillating stress).
Compression, tension, or flexure can all cause stress. The probe displacement measures changes in length caused by thermal expansion/shrinkage and softening.
How Does TMA Work?
A sample is kept in a TMA furnace, subjected to constant stress (tension, compression, or flexure) while its temperature is governed. Any sample deformation at a specific temperature can be identified.
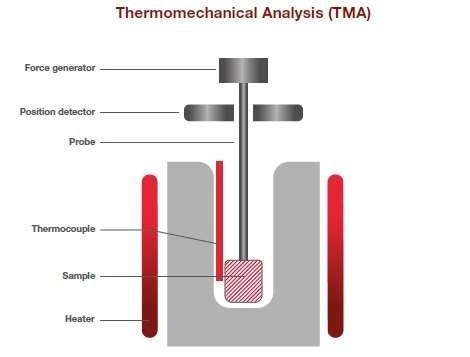
Image Credit: Hitachi High-Tech Analytical Science
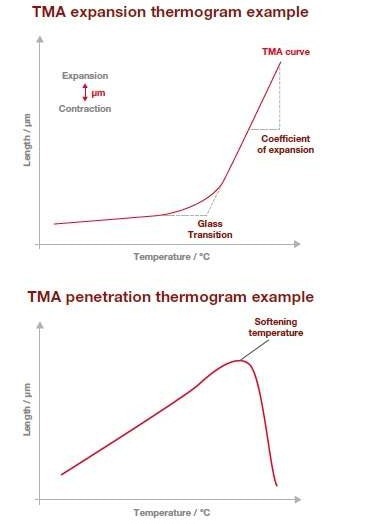
Image Credit: Hitachi High-Tech Analytical Science
The output traces shown above depict two types of measurements. The gradient of the curve just above the glass transition can be used to calculate the coefficient of expansion at the top. The bottom trace is a penetration measurement that can be used to ascertain the softening temperature of the polymer.
What Thermal Properties Does TMA Give Information About?
Softening, crystallization, anisotropy, solid–solid transitions, creep and stress relaxation, glass transition temperature (Tg), coefficient of thermal expansion (CTE), and compression modulus can all be measured using thermomechanical analysis. It can also be used to calculate Youngs modulus (ASTM E2769-16).
How to Interpret Results for a TMA to a Specific ASTM Method
ASTM E831-19 - the standard test method for linear thermal expansion of solid materials by thermomechanical analysis - will be used as an example. Using thermomechanical analysis techniques, this testing method identifies the technical coefficient of linear thermal expansion of solid materials.
This test approach is appropriate for solid materials that show adequate rigidity over the test temperature range to prevent indentation of the specimen by the sensing probe.
The TMA thermograms below show a classic example of a linear thermal expansion measurement, which is also called the coefficient of thermal expansion (CTE). For most polymers with an amorphous phase (i.e., exhibiting a glass transition), the expansion will be lower below the glass transition than after.
In this case, the slope of the linear part preceding the transition at 122.1 ºC is not as steep as the one following. This demonstrates that the expansion is greater at higher temperatures.
In this example, the CTE results also vary depending on the axis on which the measurement was executed. The CTE is calculated as μm/(m ·°C) by comparing the dimension change between two different temperatures in the linear thermal expansion region.
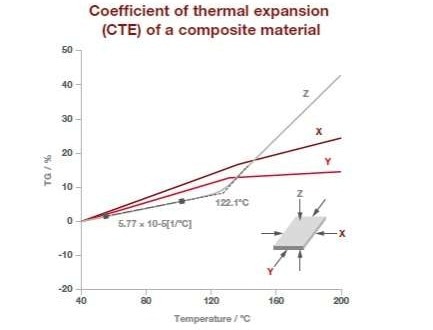
Image Credit: Hitachi High-Tech Analytical Science
What are the Advantages of Using TMA?
TMA can be used to predict how the final part will perform. For instance, by evaluating a material’s thermal expansion, users can determine whether it will be consistent with other materials or if they will delaminate. Users will also be able to determine how the material will respond to stress and whether its response will change with time or temperature.
TMA is primarily used to measure the thermal expansion of elastomers, adhesives and coatings, films and fibers, rubbers, and plastics, but it can also be used to evaluate the temperature expansion of metals and ceramics.
Hitachi’s Range of TMA Analyzers for Visibly Better Thermal Analysis
TMA instruments from Hitachi can measure sample expansion and shrinkage over a wide temperature range. In addition, the analyzers can quantify creep, stress-relaxation, heat shrinkage stress, stress-strain, and DMA.
Based on the temperature range users require, the TMA7100 (−170 ºC to 600 ºC) or TMA7300 (room temperature to 1500 ºC) will ensure that a material meets quality assurance and outgoing inspection specifications.
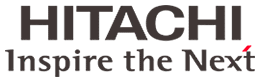
This information has been sourced, reviewed and adapted from materials provided by Hitachi High-Tech Analytical Science.
For more information on this source, please visit Hitachi High-Tech Analytical Science.