Reviewed by Louis CastelNov 22 2023
In the current health and fitness-conscious environment, there has been a notable transformation in clothing and wearables. People are willing to invest their resources to achieve a highly efficient, well-toned body that operates at elevated cardiac rates without posing risks to organs like the lungs.
This is translated in activities like hiking, running, and other sports that demand increased oxygen intake while preventing clothes from becoming heavier due to rain, snow, or wind on the outside, or excessive sweating on the inside.
This trend is observable on social media platforms where there is a growing interest in fitness-related content and education across all age groups.
Beyond fitness, breathable waterproof fabrics find diverse applications in professional attire, including clean rooms, military, firefighting, and farming wear. In the medical field, this technology can be incorporated into wearables such as surgical garments, dressings, and hygiene products. The applications of this technology are, therefore, extensive.
To meet these demands, fabric industries have enhanced their technology by offering lightweight, breathable fabrics that are also waterproof, enabling individuals to engage in physical activities more comfortably for extended periods (without needing to change their clothing).
These products include offerings from brands like Gore-Tex®, The North Face®, and Sympatex®, among others.
Among the various materials used in these wearables and textiles, perfluoroalkyl substances (PFAS) have been extensively employed. However, these substances pose environmental and health concerns, as they often accumulate in the environment and the human body.
Various organizations, including the United Nations,1 the Organization for Economic Co-operation and Development,2 Human Biomonitoring for Europe (HBM4EU),3 and the European Environment Agency,4 have raised alarms about PFAS pollutants; the presence of these pollutants has also been highlighted in the literature.5 This is worrisome for all communities and their detrimental effects are summarized in Figure 1.
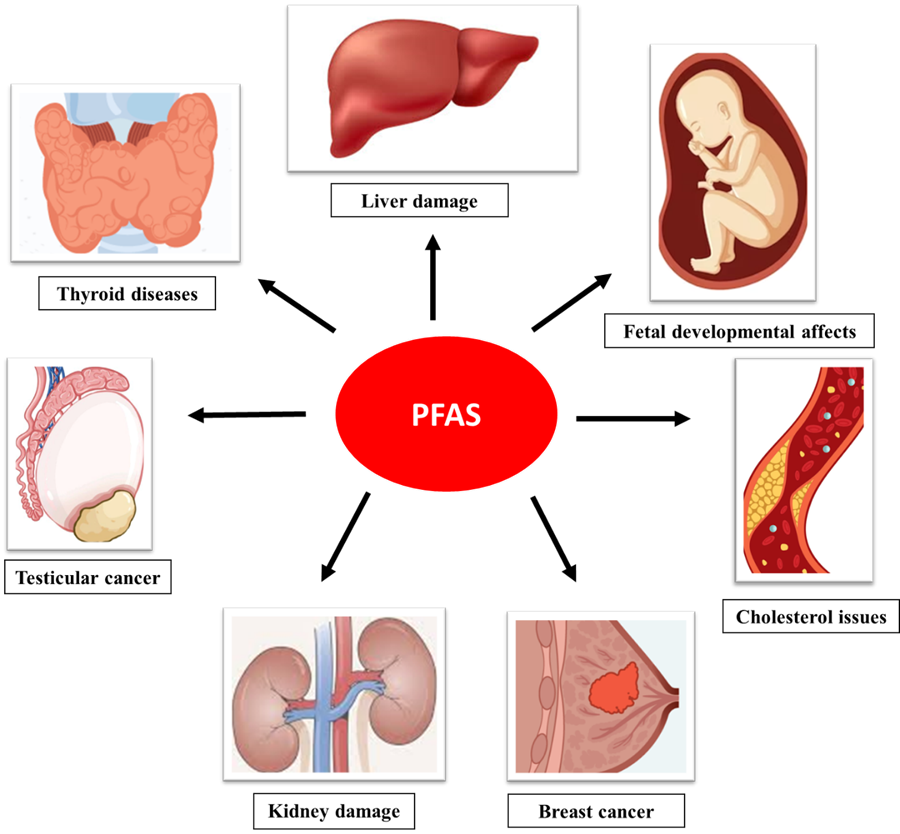
Figure 1. Effects of Perfluoroalkyl substances on the human body. 4,5 Image Credit: Inovenso
PFAS exists in numerous variants - over 5000 types are currently present. These can be categorized generally, as highlighted in Figure 2. These chemicals enter the environment and human body through multiple pathways, including production, use, and disposal.
Due to their remarkable stability, they persist indefinitely in water sources, seas, and soil habitats, contaminating both animal and plant life.5 As they are non-degradable and cannot be naturally eliminated, they are commonly referred to as "forever chemicals."
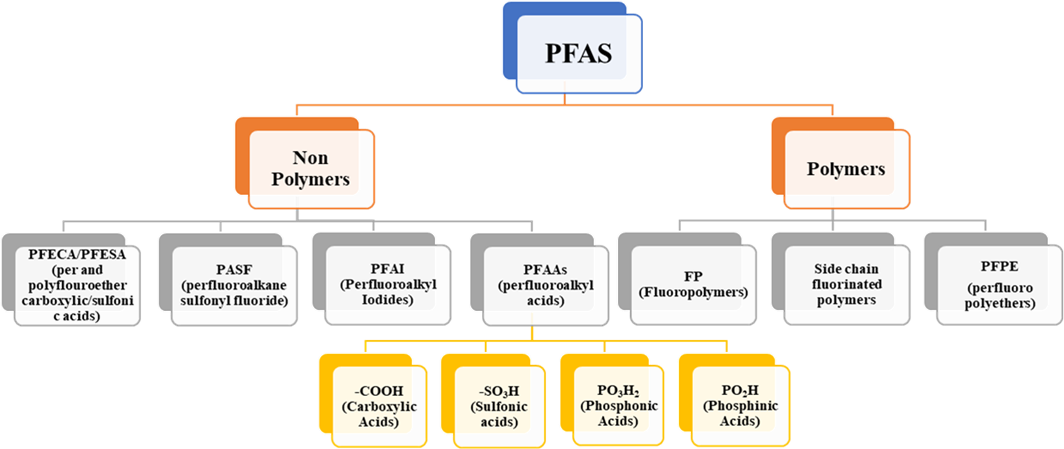
Figure 2. PFAS and their classifications. 5 Image Credit: Inovenso
This article provides a brief overview of fabric formation, the key factors involved, and one of the technologies employed in creating these fabrics.
Formation and Working Mechanics
Presently, three methods exist for creating a breathable, waterproof fabric: employing high-density woven fabrics, coated fabrics, and laminated fabrics. This article primarily concentrates on laminated fabrics as they can comprehensively provide both features compared to the initial two formation techniques.
Figure 1 provides an overview of fabric construction, illustrating the laminated three-layered scheme as an example of manufacturing breathable and waterproof fabric.
This comprises a layer of liner fabric in direct contact with the porous/fibrous membrane, acting as a barrier for larger molecules (vapors) while permitting smaller molecules (air) to pass through.
The liner fabric functions as an internal garment, enabling small-sized/aerated vapors to reach the membrane interface during physical exertion (sweating). The porous structure of the membrane then allows particles to penetrate based on size.
The third layer of waterproof fabric prevents external water vapors, such as rain, snow, or wind, from passing through while allowing internal vapors to permeate through and exit the fabric.
Crucial parameters considered in the creation of these fabrics include material hydrophilicity/hydrophobicity, permeability, porosity, mechanical strength, temperature resistance, and, lastly, the attachment/lamination of each layer to one another.
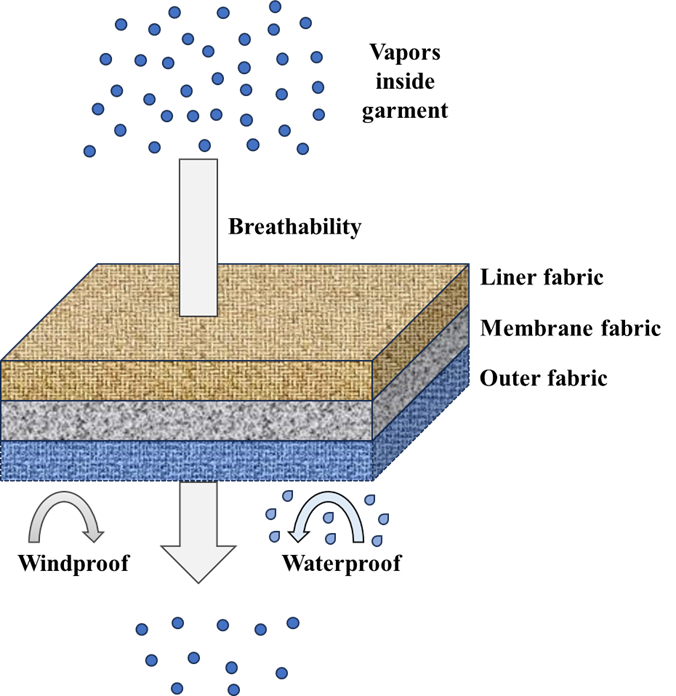
Figure 3. Scheme of a three-layered, breathable, waterproof fabric. Image Credit: Inovenso
Breathability
Breathability in fabrics refers to the fabric's capacity for water vapors to effectively permeate through via diffusion, thereby facilitating cooling through evaporation.6
Enhanced breathability means increased perspiration allowed from the skin to the fabric's exterior, preventing moisture buildup inside and ensuring wearer comfort.
Breathability can be gauged using the moisture vapor transmission rate, which indicates the rate at which vapors can permeate through a square meter of fabric in 24 hours, providing a value in g/m2/day.
The fabric's application suitability is determined by its breathability rating. For instance, a low breathability level of 5000 g/m2/day may be appropriate for fishing, but mountaineering necessitates a minimum of 20000 g/m2/day (signifying a very high breathability level requirement).
Waterproofness
The waterproofness of a fabric refers to its ability to prevent the infiltration of water. This implies that the fabric should possess sufficient porosity to repel water in the form of droplets or bulk while allowing the passage of water vapors.6
Waterproofness is quantified in terms of hydrostatic pressure, measured in millimeters. The waterproof ratings also specify the fabric's application. For instance, fabrics with ratings up to 10000 mm can withstand light rain, average snow, and pressure. Fabrics with values surpassing 20000 mm can endure extreme rain, snow, and high pressure.
Electrospinning for Nanofibrous Membranes
Conventional membrane materials like polytetrafluoroethylene (PTFE) and thermoplastic polyurethane (TPU), when produced through a laminated approach, exhibit certain drawbacks in comparison to each other. These include cost and recycling concerns for PTFE and non-porosity, resulting in low water permeability and discomfort for TPU. Simultaneously achieving protective capability and comfort is challenging due to their inverse relationship.7
To address the limitations of these methods, electrospinning has introduced a novel approach to creating nanofibrous and porous membranes with enhanced efficiency, optimized nanostructures, and reduced weight.
The technique is straightforward, as it involves the application of high voltage from a charged spinneret with a polymeric solution that deposits the polymer directly onto a substrate, such as liner fabric.
With advanced electrospinning systems, large-scale continuous production of membranes laminated with fabrics is feasible, exemplified by Inovenso Ltd.'s SS series.8
Recent research has focused on enhancing membrane properties, including improving both vapor transmission and hydrostatic pressure (while avoiding environmentally hazardous fluorine-based materials), and enhancing the producibility of highly hydrophobic resistant membranes.
This involves regulating parameters such as processing (voltage, deposition distance, injection flow rate, spinneret diameter), environmental (relative humidity, temperature), and solution (viscosity, conductivity, surface tension). This enables a balance between breathability and waterproofing capabilities.7
Material Types
In recent years, various materials, including polyurethanes (PU), polyacrylonitrile (PAN), polyvinylidene fluoride (PVDF), polyether sulfone (PES), polyimide (PI), polypropylene (PP), polymethyl methacrylate (PMMA), and Nylon 6, have been explored to create optimal waterproof and breathable fabric materials.
Each of these polymers possesses unique capabilities that contribute to fabric formation. They are either combined among themselves or with other agents like carbon nanotubes (CNTs), silicon dioxide (SiO2), and functional fluorine.7
Products
Combining the materials with optimized electrospinning parameters results in products like Futurelight© by The North Face®.9 This product utilizes PU elastic microporous membranes and was introduced in 2019 as a waterproof breathable fabric for high-exertion activities such as climbing.
The brand has achieved a PFC-free final product and employs treated recycled fabrics, making it more environmentally friendly. Other waterproof, breathable fabric brands include DryVent®, eVent®, GORE-TEX®, Polartec®-Neoshell®, and others.
Applications
Waterproof and breathable fabrics are commonly used in various applications, including but not limited to:
- Outdoor gear, such as hats, gloves, umbrellas, dry suits, tents, etc.
- Construction materials, like roofing materials, due to their lower weight, water resistance, UV resistance, and acoustic insulation.
- Medical applications, such as hygiene products, pillow covers, bed covers, surgical garments, wound dressings, and others.
- Agricultural uses, like tree shelters, packaging for product transportation, and more.
- Professional purposes, such as protective military wear, functional heavy-duty wear, cleanroom clothing, firefighter gear, farmer clothing, and others.
- Sportswear items like jackets, trousers, raincoats, swimwear, rainwear, skiwear, footwear, trekking shoes, camping boots, and others.
Future Directions
This article highlights the different applications of waterproof, breathable fabrics. Considerable effort can be directed toward achieving an optimal fabric level by selecting appropriate material types, particularly polymers that strike the right balance between breathability and waterproofness while ensuring comfort for extended wear.
The choice of material is crucial, especially given the industry's shift towards PFC-free products to minimize environmental impact.
Fabric formation plays a key role in emerging technologies, with electrospinning leading the way in producing high-precision, optimally porous nanofibers at a high production rate.
This flexible technique allows for the incorporation and direct deposition of novel fibers with multifunctionalities, such as the liner fabric. Another advantage of this technology lies in the reduced post-processing required to attain a final and finished product form.
References and Further Reading
- UNEP/POPS/POPRC.14/6 (Meeting report)
- https://www.oecd.org/chemicalsafety/portal-perfluorinated-chemicals/
- https://www.hbm4eu.eu/hbm4eu-substances/per-polyfluorinated-compounds/
- https://www.eea.europa.eu/publications/emerging-chemical-risks-in-europe/emerging-chemical-risks-in-europe
- Brennan, N. M., Evans, A. T., Fritz, M. K., Peak, S. A., & von Holst, H. E. (2021). Trends in the regulation of per-and polyfluoroalkyl substances (PFAS): a scoping review. International journal of environmental research and public health, 18(20), 10900.
- McCullough, E. A., Kwon, M., & Shim, H. (2003). A comparison of standard methods for measuring water vapour permeability of fabrics. Measurement Science and Technology, 14(8), 1402.
- Sheng, J., Zhao, J., Yu, X., Liu, L., Yu, J., & Ding, B. (2019). Electrospun nanofibers for waterproof and breathable clothing. In Electrospinning: Nanofabrication and applications (pp. 543-570). William Andrew Publishing.
- https://www.inovenso.com/
- https://www.thenorthface.co.uk/
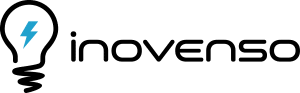
This information has been sourced, reviewed, and adapted from materials provided by Inovenso.
For more information on this source, please visit Inovenso.