The exposure of materials to external load at high temperatures results in gradual plastic deformation, known as creep behavior.
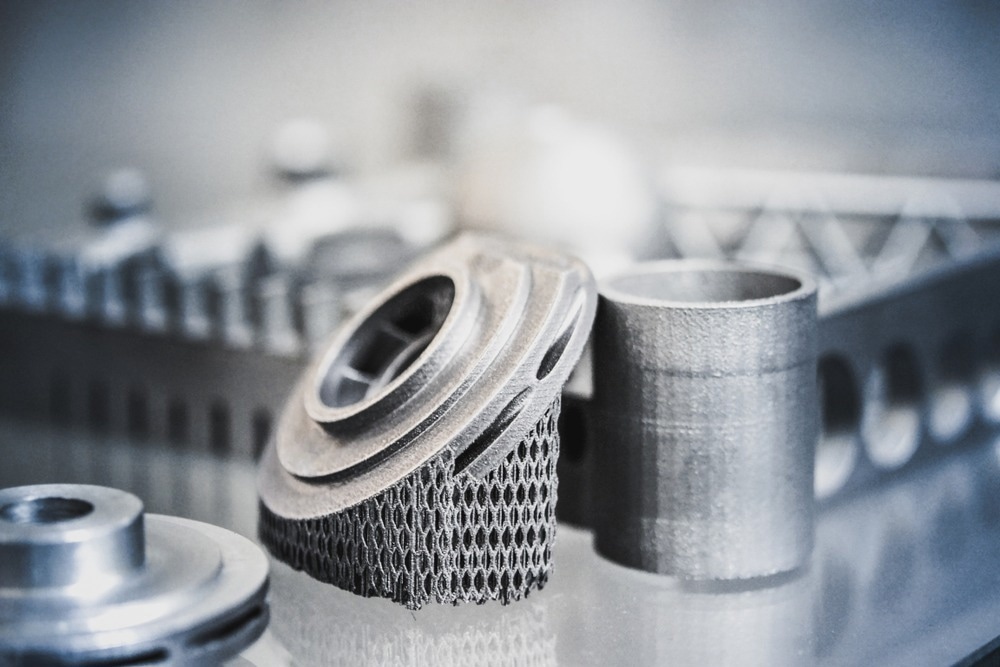
Image Credit: MarinaGrigorivna/ShutterStock.com
Creeps are characterized as time-dependent permanent deformations that occur under constant stress at elevated temperatures. The material composition determines the onset of creep. For example, steel experiences significant creep at temperatures approaching its melting point. Testing for creep behavior typically involves subjecting the material to a fixed load at a high temperature and recording the strain variation over time.
Creep Formation Process
Creep deformation involves a competition between work hardening (dislocation generation due to strain) and recovery (dislocation annihilation) until an equilibrium between the two is attained. Dislocations lead to the formation of voids on grain boundaries or within the crystal structure, which can travel throughout the material, resulting in a permanent deformation called creep.
The process of creep formation involves three stages: primary, secondary, and tertiary. The primary (or transient) stage starts instantaneously upon the application of load, during which work hardening dominates until the recovery rate gradually increases. The material experiences high creep resistance during this stage.
Upon reaching the equilibrium, the creep formation rate remains constant for an extended period, termed the secondary/stationary creep stage. Engineers use the creep rate during this stage as a crucial parameter for part design.
The tertiary stage involves the formation of cracks, voids, and grain-boundary separation due to an increased creep rate, ultimately leading to creep failure or rupture of the material.
Industrial Impact of Creep in High-Temperature Materials
In contrast to the conventional creep characterization performed under constant temperature and stress conditions, materials employed in industrial applications are exposed to varying loading and temperature conditions. Creep deformation, microstructural evolution, and final fracture in such materials are, therefore, significantly influenced by other phenomena like creep-buckling and creep fatigue.
The service life of high-temperature components in boilers and superheaters is determined by their creep behavior. Besides elevated temperatures, creep onset can be induced by fuel-ash corrosion or erosion of the component wall, leading to premature creep failures. Creep behavior, therefore, acts as a critical limitation in high-temperature design, with the secondary stage of creep development providing permissible stress values for the high-temperature materials.
The deformation rate at the stationary stage defines the creep strength of a material. The materials used in high-temperature applications should have high corrosion resistance, oxidation resistance, and creep strength. Creep strength is enhanced by solid solution hardening, precipitation, and dislocations. This requires lower stacking fault energy and diffusion coefficients while having higher elastic moduli, which can be achieved by incorporating suitable elements in superalloys, such as adding tungsten in Ni-based allows.
Grain-boundary sliding (the relative movement of adjacent grains or crystals as a unit) is responsible for creep deformation. Thus, a greater grain-boundary area allows easier creep deformation. Creep failure occurs when there is no significant deformation of the grains along the boundary. Creep strength can thus be improved by increasing the grain size, a method commonly employed in the design of austenitic stainless steel and carbon steel.
Modeling and Testing Creep Behavior
Testing the creep behavior of high-temperature materials is crucial for understanding their relationship with stress and temperature. This allows the engineers to design parts for high-temperature applications. Creep deformation tests can be conducted by subjecting a metal to a constant load and temperature. Alternatively, for brittle materials, compressive creep tests can be performed under prolonged loads and elevated temperatures.
High-temperature structural steels are commonly used in structural engineering applications due to their low specific heat, high thermal conductivity, and fire resistance. However, the fire-resistant properties of high-temperature steels can be significantly compromised by creep behavior during fire incidents.
The steep increase in creep strain with increasing temperatures and stress levels resulting from prolonged exposure to fire reduces their stiffness and strength. Thus, the creep strength of different types of industrial steels is determined by conducting tensile tests. This helps establish structure size, weight, seismic response, and quantity of steel required per unit building area.
The development of hypersonic vehicles, such as airplanes, spacecraft, and missiles, relies on high-temperature materials such as titanium, Inconel, ceramic composites, and complex alloys. A comprehensive understanding of these materials’ properties, structures, stability, and failure mechanisms is required for overall device integration.
Hence, advanced modeling and simulation tools that can be integrated with multiple systems are required to study the creep behavior of high-temperature materials and determine their thermo-mechanical properties and failure mechanisms.
Recent Advances
A recent study published in the Journal of Constructional Steel Research investigated the high-temperature and post-creep response of structural steels. The authors conducted creep tests in the 300 to 800 °C temperature range, using stress levels in the 0.4‐1.1 yield strength range. They compared the effects on high-strength steel Q460GJ and plain steel Q345B. The results showed that the densely connected network (DenseNet) model effectively predicted creep response in structural steels at various stress and temperature levels.
In another study in the Transactions of Nonferrous Metals Society of China, researchers used induction skull melting to reinforce titanium matrix composites with (TiB + TiC) and (TiB + TiC + Y2O3). They performed the creep test at 120−160 MPa and 650 °C and characterized the microstructure evolution using scanning electron microscopy (SEM), X-Ray diffractometry (XRD), and transmission electron microscopy (TEM). The findings show that the two composites have a basket-weave microstructure and that the composite with Y2O3 showed a lower steady-state creep rate under the same creep condition.
Several other techniques have recently emerged for testing the creep strength of high-temperature materials to evaluate their performance in real application environments. These include inductively coupled plasma, in situ XRD, small angle neutron scattering, quantitative metallography, and high-temperature digital image correlation.
Recent technological advancements have also seen the exploration of machine learning and artificial intelligence (AI) for rapid modeling and testing of creep behavior in high-temperature materials.
More from AZoM: Using High-Temperature Materials for Energy Technology and Mobility
References and Further Reading
1. Zhang., J. (2021). Creep modeling and first-principles investigation of high-temperature alloys. [Online] KTH Royal Institute of Technology Available at: https://www.diva-portal.org/smash/get/diva2:1529816/FULLTEXT01.pdf (Accessed on February 8, 2024)
2. National Academies. (2023). High-Temperature Materials Systems. National Academies. doi.org/10.17226/26849
3. Li, G.-Q., Wang, X.-X., Zhang, C., Cai, W.-Y. (2020). Creep behavior and model of high-strength steels over 500 MPa at elevated temperatures. Journal of Constructional Steel Research. doi.org/10.1016/j.jcsr.2020.105989
4. The National Board of Boiler and Pressure Vessel Inspectors. (2019). Creep and Creep Failures. [Online] The National Board of Boiler and Pressure Vessel Inspectors. Available at: https://www.nationalboard.org/Index.aspx?pageID=181
5. Gariboldi, E., Spigarelli, S. (2019). Creep and High-Temperature Deformation of Metals and Alloys. Metals. doi.org/10.3390/met9101087
6. Zhenli, Wu., Lingzhi, Li., Renjun, Wu., Zhoudao, Lu. (2022). Determination of high-temperature creep and post-creep response of structural steels. Journal of Constructional Steel Research. doi.org/10.1016/j.jcsr.2022.107287
7. Li-juan XU., et al. (2023). Creep behavior and microstructure evolution of titanium matrix composites reinforced with TiB, TiC and Y2O3. Trans. Nonferrous Met. Soc. doi.org/10.1016/S1003-6326(22)66120-X
Disclaimer: The views expressed here are those of the author expressed in their private capacity and do not necessarily represent the views of AZoM.com Limited T/A AZoNetwork the owner and operator of this website. This disclaimer forms part of the Terms and conditions of use of this website.