Nearly half of the world’s energy goes into heating and cooling our homes and workplaces. Researchers are looking to alloys as a promising alternative in making these processes more efficient.
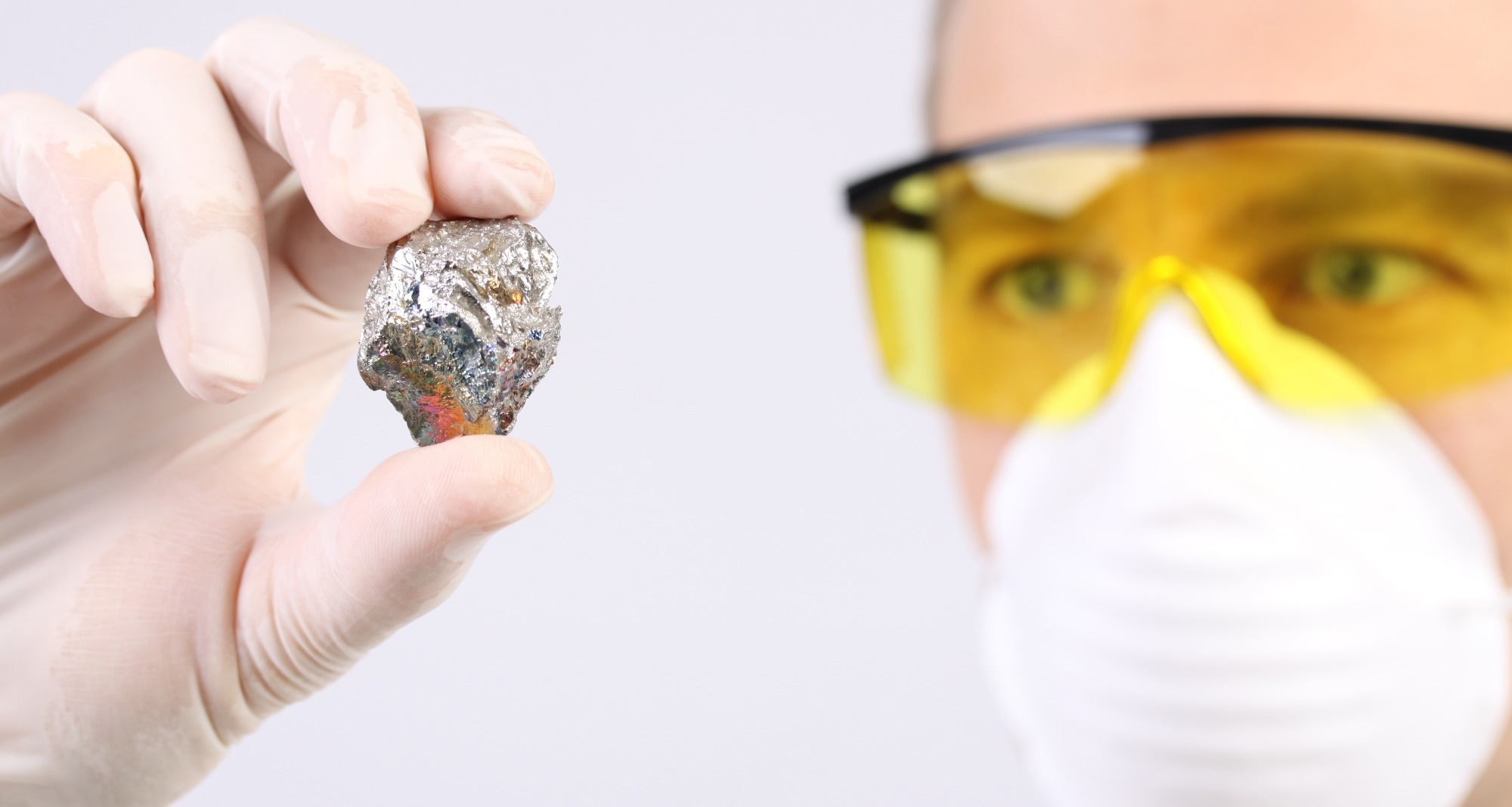
Image Credit: evka119/Shutterstock.com
Can the Thermal Properties of Shape Memory Alloys be adjusted for Heating and Cooling Applications?
Thermal parameters, especially thermal expansion, play a key role in the performance of shape memory alloys (SMAs) for heating and cooling applications. Finding ways to control the thermal expansion of SMAs more efficiently is necessary for real-world temperature regulation, and microstructure engineering is emerging as a popular approach.
Scientists have developed a model-based and experimental study for fine-tuning the coefficient of thermal expansion (CTE) of SMAs, which ensures their applicability for solid-state heating and cooling. A research study published in Acta Materialia demonstrated a predictive framework for designing and tailoring linear thermal expansion of polycrystalline martensitic SMAs using reorientation deformation.
The team applied Landau’s theory of first-order phase transitions to build thermodynamic models that predict how different SMA martensitic lattice structures expand with temperature. From these models, they calculated an intrinsic lattice-level thermal expansion CTE tensor and an extrinsic orientation distribution function. In combination, these values allowed them to create theoretical models linking the overall CTE tensor to the deformation caused by reorientation.
These theoretical models are key for designing deformation reorientation schemes, helping to map out the strain and deformation paths needed to achieve macroscopic unidirectional zero CTEs in SMAs.
The team tested their approach on 17 different SMAs, with experiments carried out on polycrystalline NiTi-based alloys. By applying reorientation deformation, they were able to adjust the CTE of NiTi from positive to zero and even to negative values.1 Fine-tuning these thermal properties is key for optimizing SMAs for use in heating and cooling technologies.
A Novel Ferro-elastic Alloy with Large Thermo-elastic Effect
In comparison to traditional fossil-fuel heating methods, pump-based solid-state heating using vapor compression (VC) is much more efficient, with lower operational costs and the recovery of industrial waste heat. In recent years, researchers have identified the first-order phase transition in SMAs as particularly well-suited for solid-state heat pumping.
A recent study proposed using solid-state heat pumping based on the large adiabatic temperature change caused by thermoelastic effects (or anhysteretic linear elastic deformation) in the martensitic phase of ferroelastic alloys.2
The researchers used raw Ti and Nb to prepare 200 g of Ti78Nb22 button samples. The team then used a two-step plastic deformation process, cold rolling and compression, to create a [100]-type texture from the Ti78Nb22 martensitic polycrystalline sample.
The experts measured the change in adiabatic temperature caused by the rapid release of about 700 MPa of compressive stress along the Rolling Direction of the sample. The small positive CTE at 298 K led to a small DTad of 2.2 ± 0.2 K. However, at around 473 K, the DTad was recorded to be around 5.2 ± 0.2 K.
The measured adiabatic temperature change of the elastic alloy in this experiment demonstrated a significant improvement over conventional metals and polymers used in thermal management systems.
Additionally, at temperatures of around 280-290 K, the material-level coefficient of performance (COP mat) was around 25.3, which is equivalent to a second law efficiency value of 88 %. At higher temperatures of around 455-470 K, the efficiency value rose to 95 %.
The experimental setup proved that [100]-textured Ti78Nb22 martensitic alloys with large DTad can be used to develop a highly energy-efficient pump for industrial solid-state heating.2
This eco-friendly material for solid-state heating will allow the pumps to reach Carnot efficiency values beyond the conventional limit of 50-70 %, and change the perception that thermos-elastic effects in SMAs and other alloys can’t be used for thermal systems.
Reverse Magneto-Caloric Effect in SMAs for Industrial Cooling Applications
SMAs are a highly viable eco-friendly option for industrial cooling applications thanks to their ability to exhibit a giant reverse magnetocaloric effect (MCE). During their first-order transformation, SMAs undergo a change in magnetic order as they shift from low-temperature martensite to ferromagnetic austenite, producing the inverse MCE.
While conventional MCE cools the material when the magnetic field is removed, SMAs display a unique cooling behaviour when a magnetic field is applied to the martensite phase, further stabilizing the austenite phase.
SMAs can be tailored with simple heat treatments and standard fabrication techniques, allowing researchers to fine-tune their lattice parameters and microstructure.
Experimental studies have shown that heat-treated SMAs deliver the most efficient magnetocaloric effect, achieving the greatest change in magnetization while minimizing elastic energy storage during phase transformation.3 These characteristics make such alloys well-suited for refrigeration and cooling technologies.
Download your PDF copy now!
Limitations and Novel Solutions
The use of thermos-elastic effects for solid-state heating and cooling applications is gaining popularity massively. However, the classic well-established linear coupled theory of thermos-elasticity used for alloys has a major limitation.
The theory, comprising two linear coupled partial differential equations, has been derived with the assumptions of small deformations in the alloys due to stress, limited temperature changes, and linear constitutive relationships.
In practice, however, when these conditions are not met, the classical model breaks down and new thermoelastic models are needed to describe the system accurately.4
For solid-state cooling, multiferroic alloys are often seen as the best option, but they also come with challenges. Fabrication tends to be costly and complex, and in use, the most significant challenge is minimizing the work done by applied stress to prevent rapid sample degradation.
Designing load cells that can deliver precise forces, while also integrating an efficient circulation platform to maintain temperature, remains a significant technical hurdle.
The development of an appropriate load cell to carry this out in application is a very difficult task, along with the integration of a circulation platform to the system for maintaining the required temperature without decreasing efficiency.5
Researchers are working to overcome these challenges, developing new thermoelastic theories and advanced heat treatment methods to tailor alloy microstructures for specific applications. These advances could make alloys a more practical choice in thermal management systems.
Further Reading
- Li, Q. et. al. (2021). Tailoring thermal expansion of shape memory alloys through designed reorientation deformation. Acta Materialia, 218, 117201. Available at: https://doi.org/10.1016/j.actamat.2021.117201
- Li, Q., Deng, Z. et al. (2025). Large thermoelastic effect in martensitic phase of ferroelastic alloys for high efficiency heat pumping. Nat Commun 16, 4511. Available at: https://doi.org/10.1038/s41467-025-59720-3
- Bruno, N. et. al. (2014). The effect of heat treatments on Ni43Mn42Co4Sn11 meta-magnetic shape memory alloys for magnetic refrigeration. Acta materialia. 74. 66-84. Available at: https://doi.org/10.1016/j.actamat.2014.03.020
- Zhang, H. et. al. (2021). Analysis of thermoelastic problems in isotropic solids undergoing large temperature changes based on novel models of thermoelasticity. International Journal of Heat and Mass Transfer. 177. 121576. Available at: https://doi.org/10.1016/j.ijheatmasstransfer.2021.121576
- Chauhan, A. et. al. (2015). A review and analysis of the elasto-caloric effect for solid-state refrigeration devices: Challenges and opportunities. MRS Energy & Sustainability, 2, E16. Available at: https://doi.org/10.1557/mre.2015.17
Disclaimer: The views expressed here are those of the author expressed in their private capacity and do not necessarily represent the views of AZoM.com Limited T/A AZoNetwork the owner and operator of this website. This disclaimer forms part of the Terms and conditions of use of this website.