3D printing is reshaping aerospace, enabling lighter parts, faster production, and radical design shifts. Here's how leading companies are putting additive manufacturing into flight.
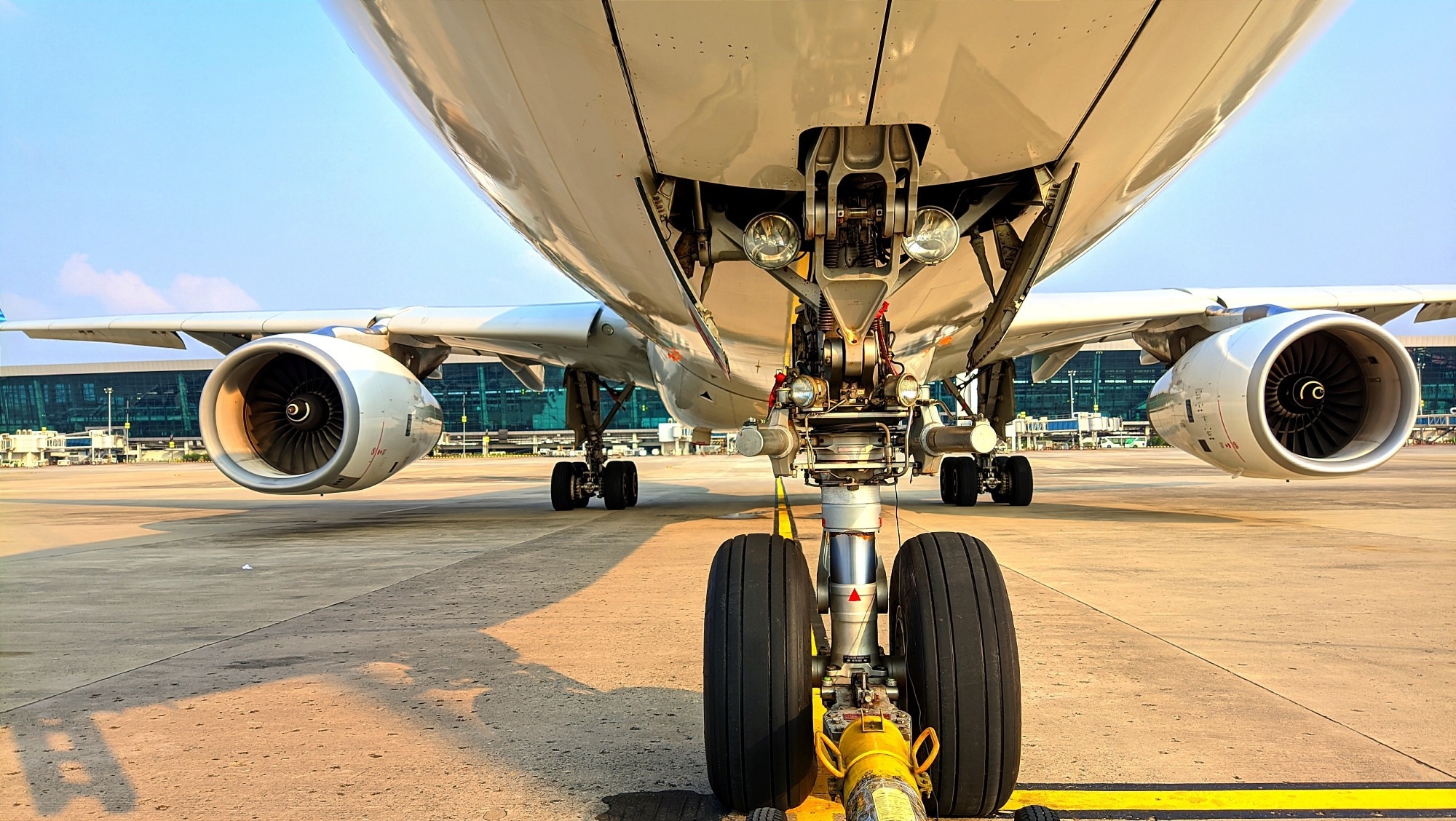
Image Credit: Sarmiko.id/Shutterstock.com
Sometimes referred to as additive manufacturing (AM), 3D printing is becoming prevalent in the aerospace industry. Because no dedicated tooling or molds are required, 3D printing dramatically reduces upfront costs and lead times for new designs. Engineers can tailor every part to exact specifications, producing small batches of highly customized components at a lower cost.1-2
What makes this approach so powerful is its flexibility. Manufacturers can iterate designs rapidly and produce bespoke or low-volume parts with minimal waste. In aerospace, where reducing weight can save fuel and customization is often key, that's a major advantage.
The environmental and economic benefits are hard to ignore. 3D printing drastically improves the so-called "buy-to-fly" ratio, a measure of how much raw material is needed to produce a flight-ready component. Traditional methods might use 20 kilograms of material to yield just one kilogram of the finished part. With additive manufacturing, that ratio can sometimes approach one-to-one.
The implications of this technology are both environmental and financial: cutting weight from aircraft can translate to thousands of dollars in annual fuel savings per kilo removed, and significantly lower CO2 emissions over the component's lifecycle.
Techniques and Materials Driving AM
Aerospace-grade AM relies primarily on powder-bed fusion processes, selective laser sintering, selective laser melting (SLM), and electron beam melting (EBM). For larger components, engineers often turn to wire arc additive manufacturing, which deposits metal from a wire feed using a high-temperature arc.3
The materials are just as advanced as the methods. Titanium alloys like Ti-6Al-4V, commonly used in aerospace, offer excellent strength-to-weight ratios and can be printed to near-wrought properties.
Nickel-based superalloys such as Inconel 718 can withstand the extreme heat and stress of turbine engines, with printed versions demonstrating tensile strengths over 900 MPa. These material capabilities, coupled with the freedom to redesign parts for specific stresses and functions, make AM well-suited to aviation and spaceflight.3-4
Below are some leading aerospace companies that have brought AM parts from digital files to flight-certified hardware, outlining the technologies, materials, and components at the heart of each implementation.
GE Aerospace
Across the industry, several key players have already embraced this technology, not just for prototyping but for building certified components that are now flying on commercial aircraft and spacecraft.
GE Aerospace has been a frontrunner in the U.S. Its Additive Technology Center in Ohio brings together hundreds of engineers, designers, and materials scientists to produce parts using powder-bed fusion processes to turn CAD files into complex, near-net-shape parts that were previously impossible or expensive to make.5
One of its earliest 3D printing successes was a fuel nozzle tip for the CFM LEAP engine, previously made from 20 separate parts. Now, that nozzle is printed as a single piece: it's lighter, stronger, and more durable. The company's production facility in Alabama has since manufactured more than 21,000 of them.5
GE's latest engine, the GE9X, includes seven 3D-printed components and has already entered commercial service. These additively manufactured parts help the engine achieve a 10 % fuel-burn improvement compared to its predecessor. This isn't experimental. It's a major commercial program backed by over $ 100 million in investment, and it underscores the company's commitment to building lighter, more efficient engines using AM.5-6
Airbus
While GE focuses on next-generation jet engines, Airbus is pushing the technology into orbit. In collaboration with the European Space Agency, the company has developed the first miniaturized metal 3D printer designed for use aboard the International Space Station Columbus module.
Unlike powder-based systems, which are ill-suited to microgravity, this wire-fed printer uses a melting process that can operate safely in zero-g. It's compact (about the size of a washing machine) but capable of printing robust metal parts like brackets, connectors, and tools using high-temperature alloys.7
This system allows astronauts to manufacture critical parts on demand, reducing reliance on resupply missions and expanding options for repairs or upgrades. Looking further ahead, this kind of in-space manufacturing could play a key role in long-duration missions to the Moon or Mars.
Boeing
Back on Earth, Boeing is applying 3D printing across its operations, using it both for structural components and interior elements. For non-structural cabin interiors and composite tooling, Boeing employs Fused Deposition Modeling (FDM) using aerospace-grade polymers such as ULTEM™ 9085 and Nylon 12, which meet stringent flame, smoke, and toxicity standards.
These materials are printed on-demand to produce parts like seat-belt holders, overhead stowage latches, and custom assembly jigs, reducing tool lead times from months to days.7-8.
Boeing's defense and space divisions use laser-based metal printing techniques to produce engine brackets, hydraulic manifolds, and load-bearing structural parts. These printed components often replace complex assemblies with single-piece solutions, reducing potential failure points and improving corrosion resistance. With fewer suppliers, fewer parts, and faster turnaround times, the company also benefits from a leaner, more responsive supply chain.7
SpaceX
For SpaceX, additive manufacturing plays a substantial role, especially in propulsion. Through a strategic $8 million collaboration with metal-AM specialist Velo3D, the company has partnered with California-based Velo3D to develop and produce high-performance Sapphire printers for its Raptor engines.
The Saphire printers can produce a variety of highly intricate components from copper-based alloys like GRCop-42, including combustion chambers and turbopumps that can withstand extreme temperatures and pressures.9
The latest generation of SpaceX engines integrates internal cooling channels directly into the printed part, eliminating the need for external heat shields. It's a smarter, lighter solution that enhances thrust efficiency. Elon Musk has described the company's in-house printing capabilities as among the most advanced in the world. For a company that thrives on speed, AM is the perfect way to test, refine, and launch in record time.
Lockheed Martin
Meanwhile, Lockheed Martin is using 3D printing across its aviation and space programmes. The company has fabricated structural titanium parts for the F-35 and Falcon business jets using EBM techniques. On the space side, it has contributed dozens of 3D-printed components to NASA missions, including Juno and Orion.
The Orion is an obvious example of how printing can benefit aerospace machines. A 7-ft diameter Orion crew-vehicle bay cover, printed in Ti-6Al-4V, plus an Inconel pressure vent were used in Orion's December 2014 flight test. The printed aluminum antenna reflector for the Orion module reduced the weight from nearly 400 kilograms to just 40, without compromising structural integrity.10-11
Download your PDF copy now!
Limitations In A Layered Future
Despite its promise, there are still a few hurdles in place before additive manufacturing becomes widespread in aerospace.
Current machines are limited in size, meaning larger structures must still be built in sections. Production is relatively slow, with each part constructed layer by layer, and most printed components require post-processing before they're ready for use. And, while material options are growing, the number of certified aerospace-grade alloys remains limited.
Even so, it's clear that additive manufacturing is no longer just a tool for prototyping or non-critical parts. It's becoming essential to how complex systems are designed, built, and improved. Engineers are now designing parts that simply couldn't exist without it: Components with integrated sensors, custom cooling systems, or advanced lattice structures that offer strength and flexibility at a fraction of the weight.
The Next Phase Of 3D Printing
Looking ahead, the real excitement lies not just in making existing parts better, but in rethinking what parts can be. Visionaries at SpaceX and NASA are already exploring large-format off-world construction, using in situ resources to 3D print habitats and infrastructure on Mars. On Earth, the next wave of AM innovation will likely come from materials science, with nanocomposites, smart alloys, and printable electronics changing what can be made, and how.
As printers get faster, smarter, and more capable, additive manufacturing won't just support aerospace innovation. It will become one of its primary engines.
References and Further Studies
1. Karkun, M. S.; Dharmalingam, S., 3d Printing Technology in Aerospace Industry–a Review. International Journal of Aviation, Aeronautics, and Aerospace 2022, 9, 4. https://commons.erau.edu/ijaaa/vol9/iss2/4/
2. Khorasani, M.; Ghasemi, A.; Rolfe, B.; Gibson, I., Additive Manufacturing a Powerful Tool for the Aerospace Industry. Rapid prototyping journal 2022, 28, 87-100. https://www.emerald.com/insight/content/doi/10.1108/rpj-01-2021-0009/full/html
3. Kalender, M. et al. In Additive Manufacturing and 3d Printer Technology in Aerospace Industry, 2019 9th international conference on recent advances in space technologies (RAST), IEEE: 2019; pp 689-694. https://ieeexplore.ieee.org/abstract/document/8767881
4. Joshi, S. C.; Sheikh, A. A., 3d Printing in Aerospace and Its Long-Term Sustainability. Virtual and physical prototyping 2015, 10, 175-185. https://doi.org/10.1080/17452759.2015.1111519
5. Richards, F., Aerospace Today: Composites, 3d Printing, & a Shot of Espresso. Advanced Materials & Processes 2015, 173, 4-5. https://go.gale.com/ps/i.do?id=GALE%7CA414136047&sid=googleScholar&v=2.1&it=r&linkaccess=abs&issn=08827958&p=AONE&sw=w&cookieConsent=true&analyticsOptout=false&userGroupName=anon%7Ed8de4e1b&aty=open-web-entry
6. Tadjdeh, Y., 3d Printing Promises to Revolutionize Defense, Aerospace Industries. National Defense 2014, 98, 20-23. https://www.jstor.org/stable/27020306
7. Najmon, J. C.; Raeisi, S.; Tovar, A., Review of Additive Manufacturing Technologies and Applications in the Aerospace Industry. Additive manufacturing for the aerospace industry 2019, 7-31. https://www.sciencedirect.com/science/article/abs/pii/B9780128140628000029
8. Pelin, G.; Sonmez, M.; Pelin, C.-E., The Use of Additive Manufacturing Techniques in the Development of Polymeric Molds: A Review. Polymers 2024, 16, 1055. https://www.mdpi.com/2073-4360/16/8/1055
9. Ishfaq, K. et al. Opportunities and Challenges in Additive Manufacturing Used in Space Sector: A Comprehensive Review. Rapid Prototyping Journal 2022, 28, 2027-2042. https://www.emerald.com/insight/content/doi/10.1108/rpj-05-2022-0166/full/html
10. Williamson, M., Building a Rocket? Press' P'for Print...[3d Printing Space Exploration 3d]. Engineering & Technology 2015, 10, 40-43. https://ieeexplore.ieee.org/abstract/document/7098612
11. Fu, X.; Lin, Y.; Yue, X.-J.; XunMa; Hur, B.; Yue, X.-Z. In A Review of Additive Manufacturing (3d Printing) in Aerospace: Technology, Materials, Applications, and Challenges, Mobile Wireless Middleware, Operating Systems, and Applications: 10th International Conference on Mobile Wireless Middleware, Operating Systems and Applications (MOBILWARE 2021), Springer: 2022; pp 73-98. https://link.springer.com/chapter/10.1007/978-3-030-98671-1_6
Disclaimer: The views expressed here are those of the author expressed in their private capacity and do not necessarily represent the views of AZoM.com Limited T/A AZoNetwork the owner and operator of this website. This disclaimer forms part of the Terms and conditions of use of this website.