Renovating a small diameter pipe is not a simple business. The pipes operated by the gas and water distribution companies that are found outside most of our homes are characterised by their small diameter and also by the large number of internal obstructions, restricting the ability to insert a liner. So-called `trenchless' systems for repairing underground pipelines are intended to minimise surface disruption by making use of existing pipe. These all have particular drawbacks. A novel pipeline renovation system about to enter service, which makes use of shape memory material technology and offers distinct advantages over current approaches, is of particular interest to engineers. Possible Solutions The purpose of the system is to deliver a close fit lining method for small diameter pipelines, typically between 8 and 20 cm, while at the same time minimising any requirement for excavation of the old pipe. In this way the utility company maximises the hydraulic capacity and structural integrity of its asset, while for the rest of us the impact of the installation operation is greatly reduced. Trenchless systems make use of the pipe already in the ground and only a limited number of excavations are made to gain access to the buried pipe to make new connections. The options for renovation are broadly classed as follows: • Slip Lining - a smaller diameter pipe is inserted inside the old pipe where a significant reduction in capacity can be tolerated, or where the possibility for pressure uplift can be implemented • Close Fit Lining - a polyethylene pipe is drawn through a die which reduces its diameter, allowing it to be inserted into a host pipe. On removal of the towing load the pipe undergoes elastic recovery towards its original diameter, achieving a close fit against the wall of the old pipe. Virtually unchanged flow capacity can be achieved • Bursting - the old pipe is used as a conduit to guide a bursting head which breaks it into fragments, pushes these into the soil and pulls a new pipe into the resulting void. A like for like replacement or even a larger diameter pipe can be installed by this method. Limitations of Existing Techniques In reviewing the techniques there are still situations where the available technology does not offer an optimum solution to the renovation engineer. Faced with the need to maintain the existing capacity of a pipeline without recourse to increased pressures or flow rates, he or she would opt for either a close fit lining solution or the bursting operation. Where there is underground congestion from nearby pipe lines serving other utilities, or incompatible soil which could cause significant ground disturbance, the engineer would not use a bursting system. In the case of small diameter pipelines the geometry of the old pipe would further rule out the option of a close fit liner. The reason for this is that old pipelines were fabricated without consideration for a fixture replacement of this type and as such many of the connections made to the pipeline, such as the service pipes which connect each of our houses, were made using screwed fittings which can protrude into the bore of the pipe. Also, over the years the ground around the pipes settles or moves and this causes the pipe to pipe joints to become deflected and offset, one of the reasons why leakage develops. The sum of these effects is that there are a number of obstructions in the bore of the pipe, and the smaller the diameter of the pipeline the bigger the relative protrusion might be. For example, a service connection might protrude 1cm into a pipe, this is 10% of the bore of a 10cm pipeline, but only 5% of a 20cm one. The use of close fit liner pipes is generally restricted to use on pipes of at least 20 to 25cm nominal bore, since the liner cannot be reduced in diameter by a sufficient margin in the smaller pipes to enable it to be inserted under the intrusions and subsequently achieve full elastic recovery to a close fit. Of secondary importance is that the old intrusions would then provide significant point loading on the liner which could easily lead to a stress induced failure within the expected lifetime of the installation. The Shape Memory Pipe Alternative The proposed solution involves the production of a cross linked polyethylene pipe (figure 1). In this case the cross linking of the polyethylene required to produce a shape memory is achieved by the addition of a peroxide chemical during the extrusion stage. Peroxide is mixed with polyethylene powder and extruded using the Engel process. The powder is converted to a melt under pressure in a piston engine. The pressure also forces the melt onto a mandrel whose dimensions correspond is the desired shape memory required. While the melt is pumped along the mandrel the peroxide breaks down to form radicals which remove hydrogen atoms and promote cross linking of the polymer chains. The length of the mandrel is set to ensure all the peroxide is consumed and something like 70 to 90% of the polyethylene mass has achieved cross linked status. 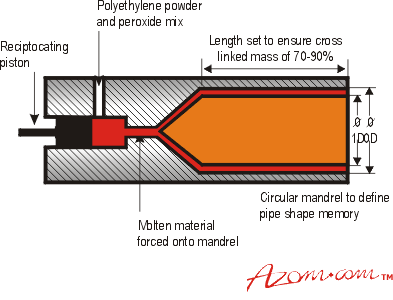 | Figure 1. The process by which shape memory pipes are manufactured. | Normally this pipe would then pass straight to a water bath where it would be cooled, with crystallisation taking place to form a high performance pipe. But for the lining application the material is deformed whilst still in the hot amorphous state so that it is reduced in diameter by over 25%. With the deformed pipe passing through a sleeve to prevent it returning to its original shape, heat is removed causing the material to crystallise, locking in the reduced diameter. In this way a pipe is made which is some 25% smaller than the diameter of the pipe which is to be lined, but which has a shape memory the same or slightly larger. The pipe can be treated as a normal polyethylene pipe in this state, it can be coiled in long lengths and if necessary can be stored for several years until it is required. Installation The application of shape memory material technology is an innovative step in itself, but so too is the method by which the pipe is installed (figure 2). On site, the old pipeline is prepared by making excavations at all points where a subsequent connection will need to be made after lining, typically each end of the section to be repaired and at intermediate points where a house service connection needs to be remade. The iron pipe is then broken out at the intermediate points and, following the insertion of a winch cable, the shape memory liner in its reduced form can be easily towed in. Because it is some 25% smaller than the bore of the old pipeline it is easily inserted, passing under the intrusions and through the offset joints described earlier. The next key step is the heating of the liner above the crystalline melting point, in this case 150°C, in order to allow the material to return to the original manufactured shape. 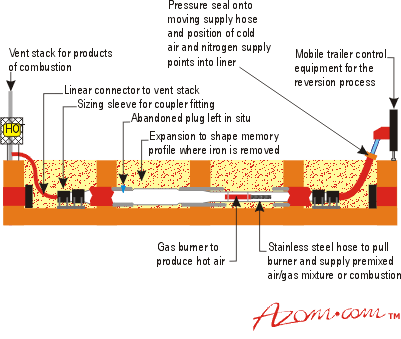 | Figure 2. The pipe repair operation utilising shape memory polyethylene pipe. | A number of systems for heating the liner were evaluated but due to the very short time available on site (typically about 1 hour is available to expand a loom length of liner) a technique has been developed in which a small gas burner is pulled through the inside of the plastic liner generating a large volume of hot air to heat the pipe. The volume of hot air generated is diluted with some cooler air blown through the pipe from one end, resulting in a larger volume of air flowing and giving up heat over a localised length. By progressively drawing the hot air tool through the pipe the entire liner can be heated, allowing it to expand by virtue of the shape memory, and then cooled. How it Works The sequence of expansion is best illustrated in the photographs, figure 3, with the liner shown in its reduced diameter immediately after insertion, then heated to its amorphous state where it actually goes transparent, and finally after cooling, in its original shape memory form. Where the liner is encased in the old pipe its ability to recover to its shape memory diameter is constrained and instead it stays as a close fit against the pipe surface. Where the liner is expanded, as shown in the broken out pipe section, it achieves its original shape, producing a pipe of known dimensions to which jointing systems can then be specified. Inside the old pipeline the material moulds itself around the remaining intrusions and across any offset pipe joints. Since crystallisation takes place after the material is shaped around intrusions, there is no stress on the liner. This, coupled with the fact that cross linked polyethylene produced using the peroxide process has exceptional stress crack resistant properties, will ensure that the pipe does not fail prematurely. Joining to the system after installation is straightforward using standard industry fittings such as polyethylene heat fusion fittings or mechanical connectors. 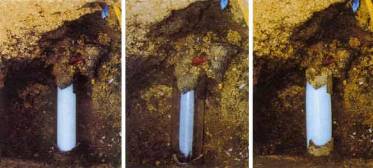 | Figure 3. (a) The liner in reduced diameter immediately after insertion. (b) The liner in amorphous state, shape memory activated. (c) After cooling and crystallisation, achieving a close fit to the original pipework. | The application of the technology will allow utility companies to reduce the impact of their operations on the general public, providing a more environmentally sensitive solution to the alternative which would have been a continuous open trench along the road. |