Introduction The mechanical alloying by milling powder particles in a high-energy ball mill, where the starting materials are either pre-alloyed intermetallic compound powders or elemental ones has become a very promising process for synthesizing metastable alloys such as amorphous alloys and nanocrystals from solid precursors [1]. This method is called mechanical milling (MM). The first part of the work reported here deals with the formation of metastable states in Al-Ni system by MM method. Ni-Al alloys are of current interest as promising high-temperature structural materials due to its excellent properties such as high melting temperature, high specific strength, good oxidation and creep resistance [2]. However, the poor workability due to their brittleness at room temperature hinders a wider application of NiAl or Ni3Al. We expect these properties will be improved after MM process. The effect of MM process on characteristics of ordered Ni3Al phase such as magnetic permeability [3], far-order parameters, lattice constant [4] have been widely investigated. However, the characteristics and shaping of bulk samples from mechanically alloyed powders are not extensively studied. The second part of this work is focused on the preparation of bulk samples from mechanically alloyed powders. Experimental A starting material in this study was a powder mixture of Al3Ni2 (δ) and Al3Ni2 (ε). A planetary ball mill was used with the velocity of mill drum of 700 revolutions per minute. The powder mixture of selected composition was placed in a cylindrical stainless-steel container with stainless-steel balls under a vacuum atmosphere. The diameter of ball and container were 12 mm and 50 mm respectively. About 5 g of the powder mixture was used in each experiment. The ball-to-powder ratio was about 10:1. The powders of mechanically alloyed nanoparticles were obtained after the MM process. The structural evolution of the mechanically alloyed powders was examined by X-ray diffraction (XRD) with Siemens D5000 Diffractometer with CuKα radiation. Crystalline size of nanoparticles can be calculated by Hall-William formula: 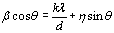 where θ, β, d, k and η, are diffraction angle, width of half maximum of the Bragg peaks, diameter of the nanocrystalline, Scheffer constant (0.9 …1) and strain, respectively. The microstructure of the powders obtained was observed by scanning electron microscopy (SEM) and high-resolution electron microscopy (HREM). The bulk samples were fabricated from the mechanically alloyed powders in two ways as follows: 1. The powders were pressed in a die of 10 mm diameter using a hydraulic pressing machine. The sinterability behavior was investigated from the sample sintered at 1000oC in vacuum. 2. The other method was hot pressing of the powders with the pressure of 90 MPa at 600oC for 60 min. Measurements of the hardness and densities of as-sintered samples were also carried out. Results and Discussion Mechanical Milling from Pre-alloyed Al-Ni Powders Figure 1 shows the XRD pattern of the initial pre-alloyed Ni-Al powders in which the diffraction peaks of Al3Ni (δ) and Al3Ni2 (ε) phases are indicated. After the powder mixture was milled for 40 h, the diffraction peaks are completely changed. The intensity of the Al3Ni phase peaks decreases rapidly and only the peaks belonging to centered-cubic systems of high space symmetry remain (Figure 1(b)). 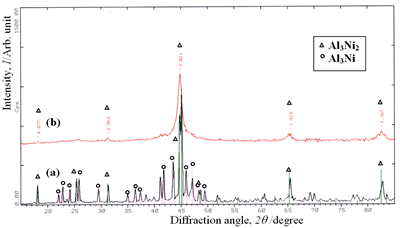 | Figure 1. XRD patterns of powders, MM processed for (a) 0 h and (b) 40 h. | The average grain size of the sample after 40 h milling calculated from the Hall-William formula based on the XRD pattern and from the SEM images was about 25 nm. As shown in Figures 2(a) and 2(b), the separation of clusters and exact calculation of grain size distribution by SEM images are difficult. A more precise grain distribution can be obtained from analysis of the HREM image shown in Figure 3. 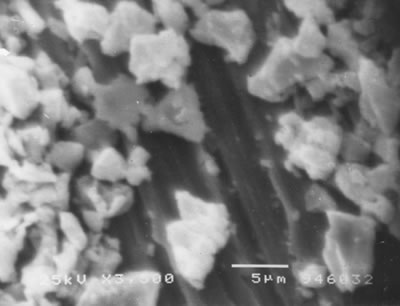 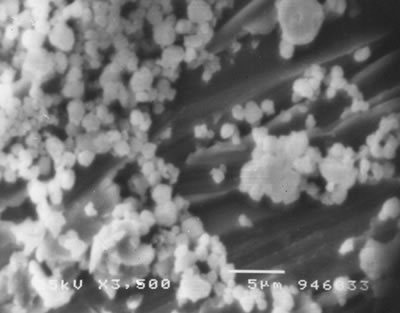 | Figure 2. SEM micrographs of Al-Ni powders, MM processed for (a) 0 h and (b) 40 h. | 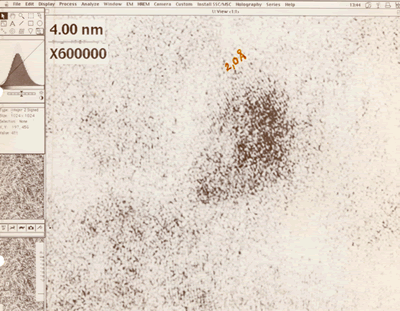 | Figure 3. HREM image of Ni-Al powders, MM processed for 40 h. | Consequently, the average grain size is found to be below 4 nm with narrow size distribution. With reference to the lattice parameters (a = 3.997Å and c = 4.118Å) of intermetallic Al3Ni2 reported by other authors [5], the powder obtained in this study consists of nanoparticles in the size range of tens of atoms. This proves the disappearance of “far-ordered” systems, and resulting in XRD patterns reflecting the presence of amorphous materials (Figure 1(b)). Based on these arguments, the phase transformation can be deduced as mechanical alloying of Al3Ni2 (δ) + Al3Ni (ε) powders for 40 h gives amorphous phase and nanocrystal Al3Ni2 (δ). Sinterability Behavior of Bulk Samples Fabricated from Pre-alloyed Al-Ni Powders after MM Process Table 1 shows the density and porosity of the bulk samples prepared by pressing and sintering powder mixture and mechanically alloyed powder (after MM process) at 1000oC. Table 2 presents the hardness and density of the bulk samples fabricated by hot pressing initial powders and those after the MM process. It can be deduced that the sinterability of powder after MM process is higher than the pre-alloyed powder mixture. Table 1. The density and porosity of the above mentioned bulk samples sintered at 1000oC. | 100 | 2.49 | 40 | 2.56 | 38 | 200 | 2.67 | 35.5 | 2.9 | 30 | 300 | 2.98 | 28 | 3.3 | 22 | 400 | Unforceable | 3.6 | 13.6 | 500 | 3.7 | 13 | 600 | 3.7 | 12.5 | Table 2. The hardness and density of the bulk samples sintered by hot-pressing. | hardness, MPa | 1980 | 3450 | porosity, % | 27 | 4.7 | Conclusion Mechanical milling by planetary ball mill was performed on the pre-alloyed Ni-Al system. The results obtained in this work are as follows: • Mechanical alloying Al3Ni2 (δ) and Al3Ni (ε) for 40 h gives amorphous phase and nanocrystal Al3Ni2 (δ). • The mechanical milling (MM) process for pre-alloyed powder mixture improves its sinterability. Acknowledgements The authors thank Prof. Goldberger, TU Dresden University, Germany, for experimental help in the sample preparation for HREM observation. References 1. N. V. Chi and T. Q. Lap, “Mechanical Alloying”, Vietnamese J. of Science and Technology, 36 (1998) 62. 2. U. D. Hanfen and G. Sauthoff, “The Effect of Martensite Transformation on the Mechanical Behavior of NiAl”, Intermetallic, 7 (1999) 501-510. 3. H. Bakker, G. F. Zhou and H. Yang, “Mechanical Driven Disorder and Phase Transformation in alloys”, Progress in Materials Science, 39 (1995) 159-241. 4. S. Gialanell, S. B. NewComb and R. W. Cahn, “Ordering and Disordering in Alloys”, Elsevier Applied Science, London, (1992) p. 67. 5. A. Taylor, “X-ray metallography” John Willey & Sons inc., New York - London, (1961) pp. 120-121. Contact Details |