Introduction Much attention has been focused on the development of ceramic/metal nanocomposites because such materials offer outstanding mechanical and multifunctional properties [1,2]. Multifunctional ceramic/metal nanocomposites such as Al2O3/Ni nanocomposites exhibited unique mechanical properties and peculiar magnetic functions [3]. These cylinder or rectangular shaped 3-dimensional (3D) bulky nanocomposites have been fabricated by powder metallurgy processes. However, these kinds of materials have previously been developed by powder metallurgy process, and are difficult to machine as a consequence of the improved mechanical properties. The high machining costs for these materials therefore preclude widespread industrial application. Typically, 2-dimensional (2D) ceramic/metal nanocomposite film with fine microstructure displays unusual transport and magnetic properties depending on the metal content in the film. Film type ceramic/ metal nanocomposites can be applied to solar thermal collectors [4], electrodes of solid oxide fuel cells [5], remote sensors of applied stress [6], porous membranes [7], and ceramic-metal joint bonded materials [8]. However, it is difficult to fabricate nanocomposite-structured films with conventional powder process. In order to overcome shape and dimensional limitations of ceramic/metal nanocomposites, it is required to develop novel process of multi-dimensional ceramic/metal nanocomposites. Recently, many novel forming processes discussed begin with a monomer based aqueous suspension as a starting state. In these processes, it is important to control the particle interaction to synthesize a stable aqueous suspension. The monomer based aqueous suspension properties play a substantial role in determining the final properties of the specimen and the range of applications [9,10]. This stable suspension determines the properties of the final products with overcoming shape limitation. In the present study, the optimum aqueous monomer suspension conditions and process routes (casting and coating) for the fabrication of multi-dimensional (3D complex-shaped and 2D film) Al2O3/Ni nanocomposites are investigated. The relationship between the final specimen properties and the preparation conditions is investigated through systematic fabrication of 3D Al2O3/Ni nanocomposite under various conditions of suspension synthesis and reduction-sintering. Also, it is focused on the novel 2D spin coating process of stable Al2O3/NiO aqueous monomer suspensions, reduction of dispersed NiO on the film, and densification behaviors of 2D Al2O3/Ni nanocomposite films in the present study. Experimental The solution chemical route was selected to obtain Al2O3/NiO (for 5 vol% Ni) powder mixtures [3]. As a monomer and cross-linker of 3D casting and 2D coating, methacrylamide and N,N´,- methylenebisacrylamide (5 wt%, ratio 5:1) were dissolved in deionized water. Poly-acrylic acid (PAA) was added to this solution as a dispersant. A prepared Al2O3/NiO mixture was then added to that solution and ball milled for 24 h. Rheological measurements were performed on a rotational stress-controlled rheometer to estimate the relationship between rheology behavior and chemicals quantity. The reaction initiator and catalyst were added immediately before casting and coating, where rectangular and complex shaped (bolt and nut) molds were used for 3D casting. Also, suspension was spin-coated on the polycrystalline Al2O3 substrate (10×10×2 mm) under conditions of 3000 rpm, 20 sec for 2D nanocomposites. Al2O3 substrates were ground (#100) for rough surface and polished (0.5 µm) for mirror surface. The drying process was performed in a relative humidity controlled chamber where RH was 90% and temperature was 30°C. A debinding step in air was 500°C. The fully debinded green specimens were reduced by hydrogen flow at 700°C for 1 h; then, it was densified in an argon atmosphere. A three-point bending test was used to measure fracture strength. Magnetic characteristics of the nanocomposites were measured using a SQUID magnetometer at 27ºC. The morphologies of multi-dimensional specimens were observed by field-emission scanning electron microscopy (FE-SEM). Results and Discussion Suspension Optimization As a solution chemical route, Al2O3/NiO mixture powder was successfully synthesized. In the aqueous suspension process, it is important to maintain good flow properties of the highly solid-loaded suspension. It is not possible to synthesis a stable highly solid-loaded aqueous suspension without the addition of a polymeric dispersant. To determine the most appropriate quantity of dispersant, leading to the best dispersion state, a 5 wt% monomer suspension with solid loading of 50 vol% Al2O3/NiO was prepared with different amounts of PAA (Figure 1). The results of these tests confirmed that the concentration of dispersant strongly influences the rheological behavior of the aqueous suspension. Below 1 wt% dispersant, the viscosity exceeds the available measurement range (dotted line), but decreased rapidly with increasing dispersant content up to 1.75 wt%. Further addition resulted in increased viscosity due to saturation of the particle surfaces with adsorbed PAA [9], which eliminates the dependence of the suspension rheology on the PAA concentration. 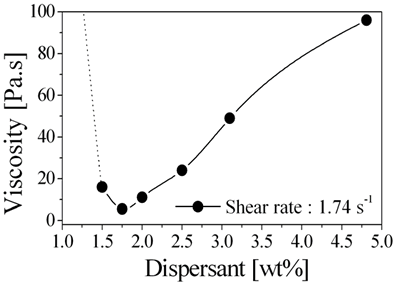 | Figure 1. Rheological curves for 5 wt% monomer and 50 vol% solid loaded Al2O3/NiO suspension prepared with different amount of dispersant. | Figure 2 shows the change in viscosity with solid loading of the Al2O3/NiO mixture for a monomer solution containing 1.75 wt% PAA and 5 wt% monomer. The viscosity increased slightly with solid loading up to 50 vol%, and further addition to 51.5 vol% resulted in a rapid increase in viscosity. From the analysis at a given quantity of Figure 1 and Figure 2, it is understood that concentration of dispersant and solid loading are strongly influenced by the rheological behavior of Al2O3/NiO suspension. Typically, a suspension of 1.75 wt% dispersant, 50 vol% solid loading was selected for further investigation of the multi-dimensional Al2O3/Ni nanocomposites. 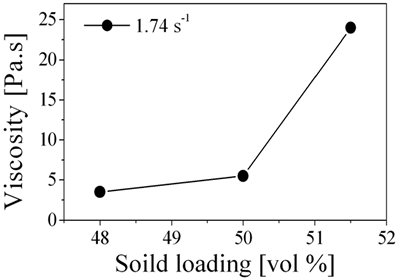 | Figure 2. Rheological behaviors of 5 wt% monomer and 1.75 wt% dispersant concentrated suspension with different solid loading. | Aqueous Suspension Casting Cast 3D specimens were fully dried and debound in a humidity controlled chamber. The debound Al2O3/NiO green body involves internal voids similar to those of porous materials because volume after burning out of polymerized chemicals remained as pores. This implies that the overall gas-solid reaction, reduction of NiO in the Al2O3/NiO mixture, can occur through these continuous pore channels [11]. The reduced green body comprised of Al2O3 and Ni phases with no reaction phases seen by XRD analysis. The relationship between fracture strength, relative density and sintering temperature of final rectangular products are shown in Figure 3. The fully densified Al2O3/5 vol% Ni nanocomposite shows enhanced fracture strength at 1500°C for 4 h. The maximum relative density and fracture strength reached 99.3% and 587 ± 50 MPa, respectively. Then, Al2O3 grain growth without densification and resultant strength degradation might occur at 1600°C. In this study, Al2O3/5 vol% Ni nanocomposite didn’t reveal superior mechanical properties due to the pressureless sintering. Although the differences in methods and conditions for mechanical testing make it difficult to set up an appropriate comparison, the present pressureless sintering result is much higher than that of reported conventional pressureless sintered pure Al2O3 results (294~393 MPa) [12], moreover, this value closely approximated other reported pressure-assisted sintering of pure Al2O3 value (605 MPa) [13]. 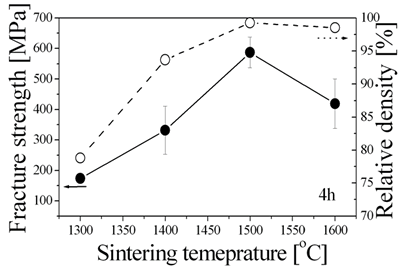 | Figure 3. Variation of fracture strength and relative density of 3D Al2O3/5 vol% Ni nanocomposite as a function of sintering temperature. | Figure 4 shows the complex shaped bolt and nut fabricated by this process. In the case of the model nut, the percent diametric shrinkage of sintering D/D0 reached 21.5% during the optimized sintering process (1500°C, 4 h). The advantage of the aqueous suspension casting process is that it allows for homogeneous density in 3D complex-shaped specimens. 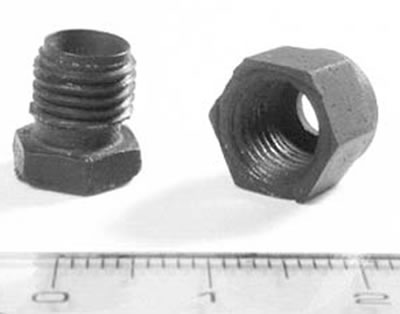 | Figure 4. The model made bolt and nut shaped 3D Al2O3/5 vol% Ni nanocomposite. | Dispersed Ni in 3D Al2O3/5 vol% Ni nanocomposites produced ferromagnetism in the final specimen, with a saturation magnetization of 50.9 emu/g. The coercive force, 3.3 kA/m, is approximately two orders of magnitude larger than that of pure Ni (70 A/m). Fine ferromagnetic Ni particles are known to exhibit high magnetic coercive force as a result of the characteristic magnetic domain structure. As the particle size of a magnetic material decreases, the magnetic structure changes from multi-domain to single-domain through reduction of the total energy of the system [14, 15]. Aqueous Suspension Coating Spin-coated 2D nanocomposite films were dried and debound in the same conditions of aqueous casting process. The stable suspension facilitated the homogeneous film formation resulting un-cracked green sheets after drying. It is explained that the shrinkage of horizontal plane with Al2O3 substrate didn’t occur in the humid drying process. This phenomenon could not be explained easily, because surface coating and the partial gelation of monomer proceeded simultaneously during the spin rotation (3000 rpm, 20 sec). Moreover, when a suspension is coated on substrate, evaporation of solvent increases the solid concentration of suspension at the liquid-vapor interface [16]. It is believed that the surface tension of the interface maintained a sound coated film structure without parallel shrinkage with substrate. Hydrogen reduced specimens were densified at the temperature range 1000 to 1500oC for 1 h. The cross-sectional SEM micrographs of Al2O3/Ni composites films and their plan images on rough substrates that were densified at (a) 1000, (b) 1100, (c) 1200, (d) 1300, and (e) 1400oC are shown in Figure 5. The microstructures were characterized by SEM using polished the cross-sectional surfaces that were thermally etched in argon atmosphere at 100oC lower than densification temperatures of each samples for 10 min. The morphology studies revealed that porous microstructure developments were strongly depending on densified temperatures. Grain growth of Al2O3 and Ni on the rough substrate observed from 1200oC. The rapid matrix grain and dispersed Ni growth occurred at 1400oC. Most of the Ni particles located in the triple junctions and grain boundaries of Al2O3 matrix in the 2D Al2O3/Ni nanocomposite. Also, microstructures of 2D Al2O3/Ni composites on mirror substrates similar to rough substrate cases. 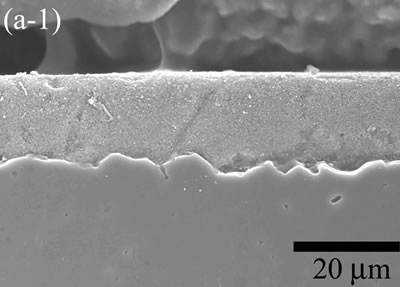 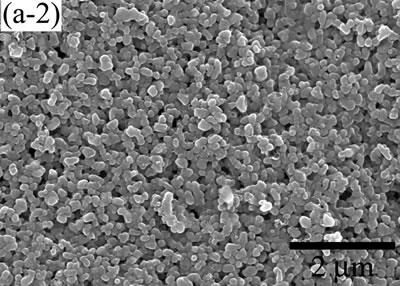 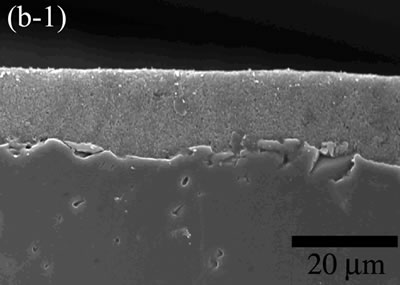 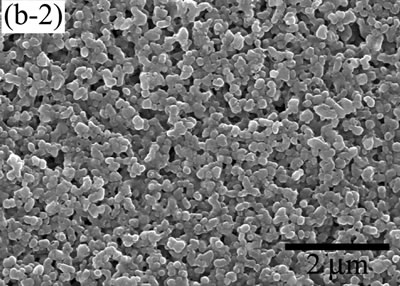 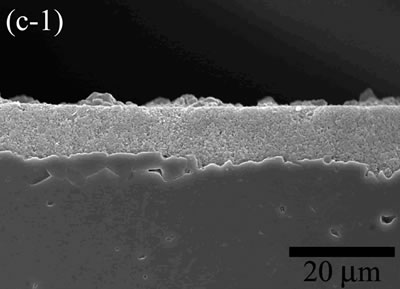  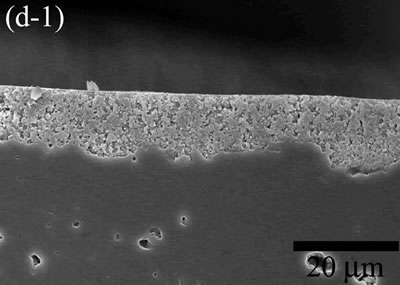 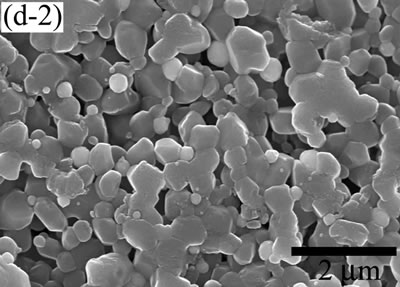 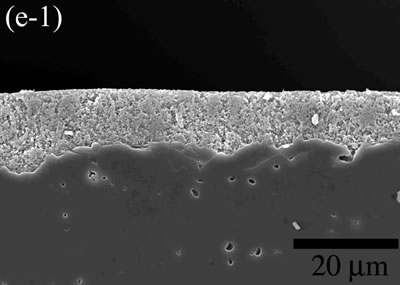 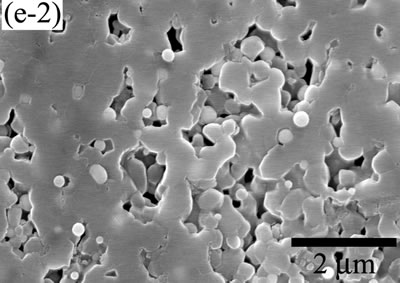 | Figure 5. The variation of cross-sectional and plan images of 2D Al2O3/5 vol% Ni nanocomposite, that were coated on rough substrate and densified at (a) 1000, (b) 1100, (c) 1200, (d) 1300, and (e) 1400oC. | The film thickness variations on both substrates depending on densification temperatures are shown in Figure 6. The initial film thicknesses depend on substrate roughness. It is believed that different surface tension between substrate and suspension decided green film thickness on given coating condition. The densifications of both conditions dominated at the temperature range from 1100 to 1200oC, and then thicknesses were saturated around 10 µm starting from 1300oC. From these results, it is understood that the combination of stable monomer-based Al2O3/NiO suspension coating and reduction-densification process have a great advantage to achieve the 2D porous ceramic/metal nanocomposite films. 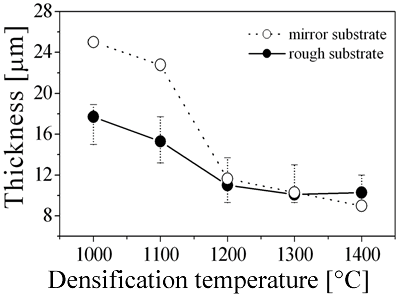 | Figure 6. The thickness variation of 2D Al2O3/5 vol% Ni nanocomposites as a function of densification temperature. | Conclusions As an approach to overcome shape and dimensional problems of general ceramic/metal nanocomposites, multi-dimensional Al2O3/Ni nanocomposites were suggested based on investigation of aqueous suspension process. The optimal aqueous suspension condition was found as follows: 1.75 wt% dispersant and 50 vol% solid loading. The density of the complex 3D Al2O3/Ni nanocomposite was 99.27% of the theoretical density, with bending strength of 586 MPa after sintering. The Ni particles in the Al2O3 matrix have revealed typical ferromagnetic behavior. Also, the porous structured 2D Al2O3/Ni nanocomposite were fabricated by aqueous monomer suspension coating process. The microstructural developments and film thickness were strongly dependent densified temperatures. With one-cycle duration of suspension, it would be possible to deposit 10 µm of 2D Al2O3/Ni nanocomposite. These results demonstrate that aqueous suspension process is a viable technique for the synthesis of multi-dimensional Al2O3/Ni nanocomposites with high strength and magnetic functionality. References 1. Y.-H. Choa, T. Nakayama, T. Sekino and K. Niihara, “Fabrication of Nano-Sized Metal Dispersed Magnesia Based Composites and Related Mechanical and Magnetic Properties”, J. Kor. Ceram. Soc., 5 (1999) 395-399. 2. R. Z. Chen and W. H. Tuan, “Pressureless Sintering of Al2O3/ Ni Nanocomposite”, J. Eur. Ceram. Soc., 19 (1999) 463-468. 3. T. Sekino, and K. Niihara, “Microstructural Characteristics and Mechanical Properties for Al2O3/Metal Nanocomposites”, NanoStr. Mater., 6 (1995) 663-666. 4. F. Kadirgan, E. Wackelgard and M. Söhmen, “Electro Chemical Characterization of Al2O3-Ni Thin Film Selective Surface on Aluminium”, Turk. J. Chem., 23 (1999) 381-391. 5. S.-W. Kim, B.-H. Lee, Y.-B. Son and H.-S. Song, “Preparation of Elecrtolyte Thin Film on NiO-YSZ Porous Substrate for Solid Oxide Fuel Cell by Elctrophoretic Deposition (I)”, J. Kor. Ceram. Soc., 36 (1999) 521-532. 6. M. Awano, M. Sando and K. Niihara, “Synthesis of Nanocomposite Ceramics for Magnetic Remote Sensing and Actuating” Key Eng. Mater., 161-163 (1999) 485-488. 7. P. Aranda and J. M. Garcia, “Porous Membranes for Preparation of Magnetic Nanostructure”, J. Magn. & Magn. Mater., 249 (2002) 214-219. 8. B. H. Rabin, R. L. Williamson, H. A. Bruck, X.-L. Wang, T. R. Watkins, Y.-Z. Feng and D. R. Clarke, “Residual Strains in an Al2O3-Ni Joint Bonded with a Conposite Interlayer: Experimental Measurements and FEM Analyses”, J. Am. Ceram. Soc., 81 (1998) 1541-1549. 9. R. Gilissen, J. P. Erauw, A. Smolders, E. Vanswijgenhoven and J. Luyten, “Gelcasting, a Near Net Shape Technique”, Maters. & Design, 21 (2000) 251-257. 10. R. Laucournet, C. Pagnoux, T. Chartier and J. F. Baumard, “Coagulation Method of Aqueous Concentrated Alumina Suspensions by Thermal Decomposition of Hydroxyaluminum Diacetate”, J. Am. Ceram. Soc., 83 (2000) 2661-2667. 11. B.-S. Kim, T. Sekino, T. Nakayama, M. Wada, J.-S. Lee and K. Niihara, “Pulse Electric Current Sintering of Alumina/Nickel Nanocomposites”, Mater. Resea. Innov., 7 (2003) 57-62. 12. G. V. Samsonov, “The Oxide Handbook”, IFI/Plenum Data Com., New York, (1982) pp. 190. 13. R. M. German, “Sintering Theory and Practice”, John Wiley & Sons, New York, (1996) pp. 314. 14. A. YE. Yermakov, O. A. Ivanov, YA. S. Shur, R. M. Grechishkin and G. V. Ivanova, “Magnetic Properties of Monocrystalline Powders of Nickel”, Phys. Met. Metall., 33 (1972) 99-104. 15. R. Kamel and A. Reffat, “On The Effect of Lattice Disorders on The Reversible Magnetization Process in Pure Nickel”, Solid State Commu., 8 (1970) 821-823. 16. R. M. van Hardeveld, P. L. J. Gunter, L. J. van Ijzendoorn, W. Wieldraaijer, E. W. Kuipers and J. W. Niemantsverdriet, “Deposition of Salts from Solution on Flat Substrates by Spin-Coating: Theory, Quantification and Application to Model Catalysts”, Appl. Surfa. Scien., 84 (1995) 339-346. Contact Details |