Introduction Fullerene-related materials such as carbon nanotubes have been the centre of extensive research [1]. The formation of nanotubular structures have also been found in several other systems such as: MoS2 [2], BxCyNz [3] and BN [4]. BN nanotubes are promising tubular structures for use in electronic devices because of the special semiconducting properties [5]. Different methods have been recently reported in the literature for synthesizing these BN nanostructure crystalline materials. These include techniques such as: plasma arc discharge [4], laser ablation [6] and catalytic decomposition [7]. Also, BN nanotubes have been obtained from a substitution reaction of carbon nanotubes at 1773 K [8]. These methods require either high power lasers or high temperature even sometimes subsequent annealing of the obtained compounds [9]. Ball milling techniques have also been used for this purpose. Thus, for example, room temperature ball milling of elemental boron in ammonia gas followed by annealing at a relatively low temperature has been used to produce BN nanotubes [10]. Multiple walled BN nanotubes and nanorods have recently been obtained using a mechanical alloying technique at room temperature [11]. However, the presence of these BN nanostructures were scarce and not frequently found in the ball milled powders. In this investigation, the effect of the container nature and the effects of some particular element additions to the milled powder mixture, on the BN nanorod production have been explored. Stainless steel and tungsten carbide containers have been used in the experimental ball mill arrangements. Also, additions of Si and Fe to the original mixture (boron powder and nitrogen gas), have been explored. Experimental Boron powder (99.8%) with particle sizes of approximately 1μ was ball milled at room temperature using a SPEX ball mill (8000D). High purity hydrogen was used as the milling atmosphere. Balls and containers (volume 270 ml.) of steel and tungsten carbide were used. Small amounts of sample were taken at specific milling times (3 and 8 h.), keeping the weight ratio of 30:1. Fe (99.9%) and Si (98.5%) were added to the boron powders (2 wt%), when the tungsten carbide container was used. The mechanically milled powders were characterized using X ray diffraction patterns and transmission electron microscopy. The X-ray experiments were carried out in a Siemens D-5000 instrument using CuKα radiation (Nickel filter) and the TEM observations in a Philips Tecnai F20 microscope. The TEM observations of the powder samples were obtained using holey carbon coated copper grids. Results and Discussion Experimental nanotubes and nanorods of BN obtained with this technique using steel balls and steel containers have been recently reported [11]. These types of nanotubes are illustrated in Figure 1a, where a HREM image of a BN nanotube is displayed. The measured interplanar distances obtained from this figure are: a=0.277 nm and c=0.333 nm, which correspond to the (100) and (002) lattice plane distances of the hexagonal structure (hcp) of the BN compound. Figure 1b shows another view of the HREM nanotube image. The empty space between the nanotube walls can clearly be seen. Figure 1c shows the Fast Fourier Transform (FFT) power spectrum obtained from the region which includes an appreciable number of nanotubes. Figure 2 shows the EDS spectrum obtained from the nanotube illustrated in Figure 1b. The spectrum shows the presence of copper, oxygen, iron and nitrogen. 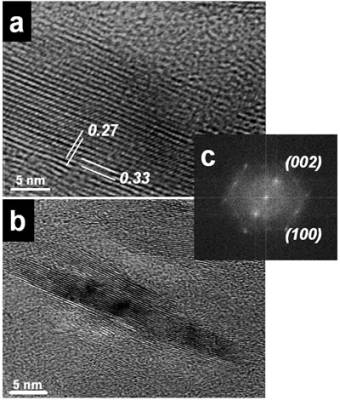 | Figure 1. HREM images and: electron diffraction pattern of nanotubes obtained from a mechanically alloying mixture in a stainless steel container. a) The measured distances correspond to the (100) and (002) lattice plane distances in the hcp structure of BN. b) This HREM images shows the empty space between the two multilayered walls of the BN nanotube. c) FFT power spectrum which correspond to these nanotubes images. | 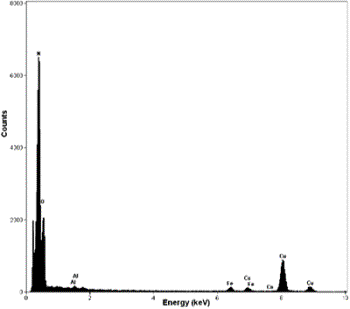 | Figure 2. X-ray compositional spectrum obtained from the nanotubes region illustrated in Figure 1. The spectrum shows the presence of oxygen, copper, iron and nitrogen. The iron presence is related with contamination from the steel balls and steel walls container. | The copper signal is produced by the specimen grid of observations; the oxygen is related with the environmental contamination of the milled powders after opening the container. Finally, the iron signal could be the result of the use of steel balls and steel containers. Subsequently, the same types of mechanical alloyed powders were obtained using tungsten carbide containers and similar tungsten carbide balls. Figure 3a shows a bright field image of an area from a powder specimen obtained with the tungsten carbide container. The initial powder mixture includes 2 at% of Si and also 2 at% of Fe. This image does not show high density of nanotubes. Thus for example, Figure 3b shows a HREM image with very small (few nanometer long) nanorods formation. The EDS spectrum from this region is illustrated in Figure 3c, where an appreciable amount of oxygen is clearly displayed. However, Figure 4a shows a region where the nanotubes presence is higher than the image illustrated in Figure 3a. Figure 4b shows the EDS spectrum from the region illustrated in Figure 4a. There are two main chemical differences with the results obtained from Figure 3a. The first difference is related with the appreciable reduction in the oxygen content and also with the increment in the Si content. The increment of silicon can be seen by measuring the relative intensities of the N and Si peaks. The iron content is similar in both spectra (Figures 3c and 4b). The presence of iron and the increment in silicon seems to have an appreciable effect on the nanorods production. Figures 5a shows typical nanorods of approximately 11 nm in wide and 100 nm long. 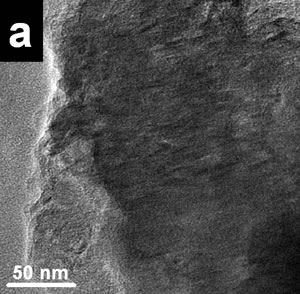 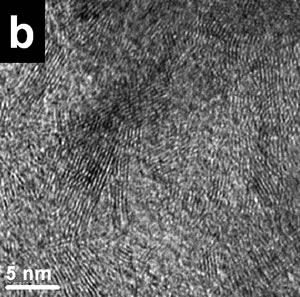 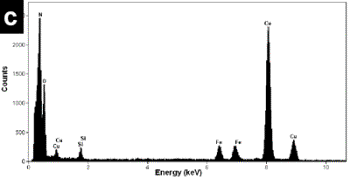 | Figure 3. a) Bright field images of a specimen region of the mechanical alloyed powders obtained with a tungsten carbide container b) HREM image from the region illustrated in Figure 2a. Small nanorods (few nanometers long) can be seen. c) the X-ray compositional spectrum shows iron, silicon and the appreciable amount of oxygen. | 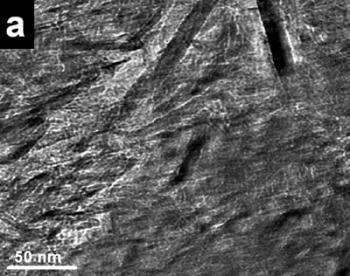 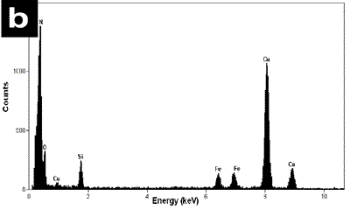 | Figure 4. a) Bright field images of a mechanical alloyed specimen obtained with the tungsten carbide container. A high density of nanorods can be seen in this image. b) The X-ray compositional spectrum shows similar amounts of iron than the spectrum in Figure 3, however there is a slight increment in the silicon contain and a reduction in the amount of oxygen. | Figure 5b shows the FFT power spectrum obtained from a region of Figure 5a. The interplanar distances are of the order of 0.333 nm which corresponds to the d[002] distance in the hcp structure of BN. The EDS spectrum illustrated in Figure 5c shows similar chemical characteristics to the above mentioned spectra. The observed specimens always show an increment in the nanotubes and nanorod production when the amount of silicon is increased and similar amounts of iron are used in the alloyed mixture. The best quality and the increment in the number the nanorods were obtained using the tungsten carbide containers. Small amounts of iron in the alloyed mixture obtained with the stainless steel containers give rise to a scarce presence of nanotubes and nanorods. However, increasing the amount of iron (wt 2%) with slight increments of silicon in the mixture and using the tungsten carbide containers increase the number of nanorods in the mechanical alloyed compound. This result is in agreement with the Chen et al. [10] results, who suggested that iron acts as a catalyst in the formation of nanotubes. Other investigations [12] have also show that the presence of metallic particles in the mixture tends to increase the number of obtained nanotubes. 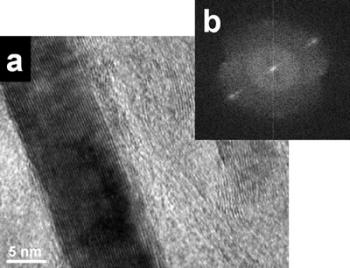  | Figure 5. a) HREM image of a typical nanorod of approximately 11 nm wide and 100 nm long. b) Powder spectrum obtained from the digitized image of figure 5a. c) X-ray compositional spectrum with similar characteristics of the spectra discussed in figures 3 and 4. | Conclusions Nanotubes and nanorods were obtained using mechanical alloying techniques. Different steel and tungsten carbide balls and containers were used in the experimental procedure. Also, two different elements (iron and silicon), were added to the initial boron-nitrogen mixture. The experimental results indicate that the presence of iron and silicon with the use tungsten carbide containers has an influence on the amount of nanotubes and nanorods obtained. Acknowledgements G. Rosas thank the UMSNH and CONACYT (38410-U) for financial support. References 1. S. Iijima, “Helical Microtubules of Graphitic Carbon”, Nature, 354 (1991) 56-58. 2. Y. Feldmann, E. Wasserman, D. Srolovitz and R. Tenne, “High-rate, gas-phase growth of MoS2 nested inorganic fullerenes and nanotubes”, Science, 267 (1995) 222-225. 3. Z. Weng-Sieh, K. Cherrey, N. G. Chopra, X. Blasé, Y. Miyamoto, A. Rubio, M. L. Cohen, S. G. Louie, A. Zettl and R. Gronsky, “Synthesis of BxCyNz nanotubules”, Phys. Rev. B, 51 (1995) 11229-11232. 4. N. G. Chopra, R. J. Luyken, K. Cherrey, V. H. Crespi, M. L. Cohen, S. G. Louis and A. Zettl, “Boron Nitride Nanotubes”, Science, 269 (1995) 966-967. 5. D. Golberg, Y. Bando, M. Mitote, K. Kurashima, T. Sato, N. Grobert, M. Reyes, H. Terrones and M. Terrones. “Preparation of aligned multi-walled BN and B/C/N nanotubular arrays and their characterization using HRTEM, EELS and energy-filtered TEM”, Physica. B, 323 (2002) 60-66. 6. D. Goldberg, Y. Bando, M. Eremets, K. Takemura and H. Yusa, “Nanotubes in boron nitride laser heated at high pressure”, Appl. Phys. Lett., 69 (1996) 2045-2047. 7. E. J. M. Hamilton, S. E. Dolan, C. M. Mann, H. O. Colijn, C. A. MacDonald and S. G. Shore, ‘‘Preparation of Amorphous Boron–Nitride and its Conversion to a Turbostratic”, Tubular Form,’’ Science, 260 (1993) 659-663. 8. W. Q. Han, Y. Bando, K. Kurashima and T. Sato, “Synthesis of boron nitride nanotubes from carbon nanotubes by a substitution reaction”, Appl. Phys. Lett., 73 (1998) 3085-3087. 9. X.P. Hao, D.L. Cui, X.G. Xu, M.Y. Yu, Y. J. Bai, Z.G. Liu and M.H. Jiang, “A novel synthetic route to prepare cubic BN nanorods”, Materials Research Bulletin, 37 (2002) 2085-2091. 10. Y. Chen, J. F. Gerald, J. S. Williams and P. Willis, “Mechanochemical Synthesis of Boron Nitride Nanotubes”, Materials Science Forum, 312-314 (1999) 173-178. 11. G. Rosas, J. Sistos, A. Ascencio, A. Medina and R. Pérez, “Múltiple-walled BN nanotubes obtained with a mechanical alloying technique”, Applied Phys. A, 80 (2005) 377-380. 12. C. H. Kiang, W. A. III Goddard, R. Beyers and D. S. Bethune, in Carbon Nanotubes edited by M. Endo, S. ilima and M. Dresselhaus (Oxford, Pergamon, 1996) pp. 47. Contact Details |