Originally, typical matrices were the amorphous resins polyethersulphone (PES) and polyetherimide (PEI). However, it was soon recognised that solvent resistance was an important criterion for aerospace applications, and the emphasis of development shifted to semi crystalline polymers such as polyether ether ketone (PEEK) and polyphenylene sulphide (PPS) (table 1). These expensive materials are aimed at aerospace applications. There are also a limited number of pseudothermoplastics such as polyamide imide (PAI) and polyimides. These polymers, in contrast to normal thermoplastics, complete their polymerisation during processing, which includes a postcuring stage. Of the polymers for use at lower temperatures, PA, PBT/PET and PP have received most study. These materials offer a considerable span of use temperature, with prices ranging from commodity priced PP to more expensive engineering grade PA's. Table 1. Thermal data for some important engineering thermoplastics. | PP | -20 | 160-190 | 110 | PA | 50 | 220-270 | 170 | PES | 230 | - | 180 | PEI | 220 | - | 170 | PAI | 275 | - | 230 | PPS | 90 | 290-340 | 240 | PEEK | 145 | 350-390 | 250 | The continuous reinforcement used in ATC’s is supplied to the processor in a variety of forms. Apart from the basic strand, woven, knitted or braided fabrics may be used for impregnation. The continuous strand may alternatively be intermingled with fibres composed of the matrix polymer to form a drapable precursor for impregnation. In all cases however, it should be noted that the fibres may require special chemical treatment to their surface (sizing) to optimise the fibre/matrix interface. With high temperature polymers, the important fibres are carbon (AS-4, T-300), aramid (Kevlar-49, Twaron) and S or R-glass, with carbon most commonly found. Conversely, E-glass accounts for the greater part of all the lower temperature composites. Prepreg Forming Processes The available product forms fall into two groups classified as pre or post impregnated. In the former case the fibres are fully impregnated by the matrix in a separate step prior to part fabrication. With the latter, fibre and matrix are brought into close physical proximity without the fibres being fully wetted by the matrix. Full wetting only takes place during part fabrication. Pre impregnation may be achieved by melt or solution techniques. Melt Impregnation Process In the case of melt impregnation the fibre bundle is spread to aid melt penetration prior to entering a crosshead extruder and die which is normally designed to produce a thin flat tape or prepreg. The process, which is shown in figure 1, is capable of offering tape widths up to 300 mm with thicknesses from 0.125-0.5 mm. A typical carbon fibre prepreg with a thickness of 0.125mm will have a fibre volume fraction (FVF) around 60% and a single ply weight of 210g/m2. 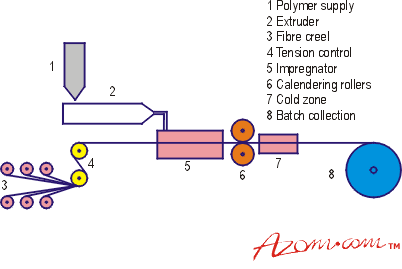 | Figure 1. Schematic of the melt impregnation process. | Alternatively, micronised polymer may be used in a fluidised bed process where the polymer particles are trapped within the fibre bundle by electrostatic charge. The coated fibres are then subjected to heat and pressure to complete the impregnation process. Because of the high viscosity of most thermoplastics, melt impregnation of fabrics has proved difficult and is normally restricted to narrow widths. Particular features of melt impregnated prepregs are that they are stiff and flex like spring steel, but have no tack. These characteristics can be useful in automated processing. Solution Impregnation Process In the case of solution impregnation, which is mainly used with amorphous polymers such as PEI, polymer concentration and temperature can be adjusted to give significantly lower viscosities than are available via melt impregnation. This gives the solution route an advantage for fabric impregnation. After passing through a bath of the polymer in solution, the material is passed through nip rollers which control the degree of solution uptake. The impregnated material then passes through a solvent evaporation/recovery unit as shown in Figure 2. Although the aim is to achieve total solvent removal, this in practice has proved difficult, with the result that care is necessary during fabrication to prevent the release of volatiles which can cause void formation. 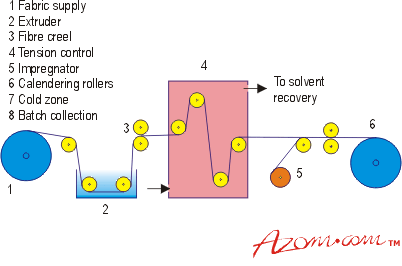 | Figure 2. Schematic of the solution imprenation process. | Post Impregnation Processes For post impregnation the matrix polymer may be used in the form of fibres, film or powder. In each case, the ease of processing depends on the degree of intimate physical contact achieved between the fibres and polymer during prepreg formation. With film stacking, which is primarily a laboratory technique, polymer film is interleaved with the reinforcement (usually fabric) prior to direct part fabrication. Prolonged consolidation at high pressure and temperature is necessary to achieve acceptable impregnation, which is rarely optimum. Powder Impregation Powder impregnation has been used to develop two distinctive forms of prepreg. In the first type, a fluidised bed technique is used to introduce polymer particles into the fibre bundle which is then passed through a crosshead extruder. This encapsulates the fibres and polymer powder within a thin sheath of the same polymer which prevents polymer loss during handling. The second type, makes use of tacky binders to retain the polymer powder after it has been introduced into the fibre bundle. This product can be draped in complex moulds but care is necessary during consolidation because the binder must be removed by volatilisation. However, the most important route for post impregnation involves commingling of matrix fibres with the reinforcement, which was developed by NASA. Commingling is accomplished by passing continuous filament reinforcement and matrix yarns through a turbulent jet of compressed air. A binder may be used to stabilise the mingled yarn. The attractions of the method are that the FVF can be closely controlled and high molecular weight polymers can be used to spin the matrix fibres, whereas lower molecular weight polymers are frequently used for melt impregnation. The importance of the post impregnated product forms is their ability to accept drape, which is a key factor in the fabrication of complex shapes, especially when deep draws are required. This is particularly the case with commingled yarns which lend themselves to braiding, knitting and weaving processes. Acceptable levels of impregnation can be achieved with the commingled route but relatively long cycle times are involved. Fabrication Processes The fabrication process for ATCs is dictated by the part shape and the form of prepreg used. Preimpregnated forms require nominal pressure for only a few seconds to yield a consolidated product. This makes them particularly suitable for high speed automated processing. However, their stiffness and lack of drape have limited their application to flat or simply contoured parts. On the other hand, the flexibility and drape of postimpregnated forms makes them the preferred materials for complex shape fabrication via compression moulding. In practice two routes are followed: 'direct from prepreg' or 'indirect via a semi finished intermediate'. Direct Forming This includes the routes used for producing semi finished sheet, rod and tube, i.e. tape laying, filament winding and pultrusion. Sheet can be made by manual lay up using a platen press but this is only economical for development quantities. Automation is following two paths: computer controlled sequential tape laying or the continuous lamination of a stack of appropriately oriented prepreg plies. Cincinnati Milacron have developed an TMC tape layer which continuously heats, compacts and cools tape as it is applied to a panel surface as shown in figure 3. Large sheets can be laid up with any required ply orientation sequence at deposition rates up to 45 kg/hr. This scale of operation is of interest to aerospace fabricators, but for volume markets continuous multi-ply lamination using a double belt press is the preferred route. This requires a supply of continuous off axis prepregs so that the reinforcing fibres can be oriented in the desired stress directions within the component. This can be achieved by continuous edge welding and slitting using equipment under development by Integrated Materials Technology. Here. the projected capacity of a combined off axis/lamination line producing 1220 mm wide E glass/PP sheet is estimated at 230-420 kg/hr depending on single ply thickness. 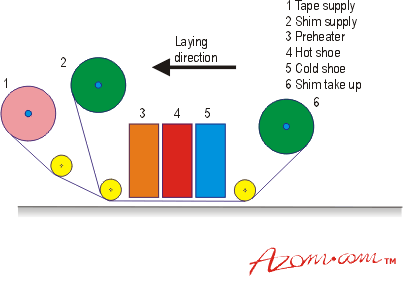 | Figure 3. Schematic of thermoplastic tape-layer (Cincinnati-Milacron type). | Tube Formation Tube formation uses the same basic filament winding equipment developed for thermoset systems with the addition of a focussed heat source. The prepreg tape or tow is heated just before being wound on the mandrel, which can also be heated to aid consolidation. The pressure required for consolidation is applied by maintaining adequate winding tension and can be augmented by a following pressure roller. There are several advantages of ATC filament winding which deserve mention. First, non geodesic winding patterns are possible because of the rapid solidification of the matrix after tape deposition. Second, post forming of the wound tube allows the designer to conceive monolithic hollow structures which can include concave surfaces and finally, because no autoclave is required for curing, there is no practical limit to the size of thermoplastic filament wound structures. Rod Formation The pultrusion of ATC rod is at an early stage of development. Most use has been made of melt impregnated tow or tape but die design is critical. Gradual heating is necessary as the prepreg cross section adjusts through a compliant die which provides a constant pressure for consolidation. Post impregnated prepregs are not generally suitable for pultrusion because they require excessively long times for melting, shaping and consolidation. Indirect Forming Pre consolidated sheet is the main feed stock for the rapid thermoforming of ATCs. If semiconsolidated feed stock is used, longer cycle times are required. With semi-crystalline polymers, cooling rates must be carefully controlled to yield the correct morphology which influences physical properties such as toughness and solvent resistance. There are four different thermoforming techniques: hydro or rubber, diaphragm, stretch and roll forming. Hydroforming In hydro forming, (figure 4a), a heavy rubber membrane, pressurised by hydraulic fluid, shapes the preheated blank against the mould face. With rubber forming, the membrane is replaced by a solid block of rubber. Both processes are suitable for rapid forming of relatively simple parts. Cycle times of a few minutes can be achieved. 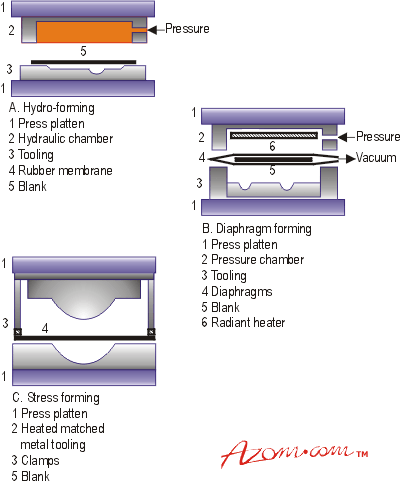 | Figure 4. Schematic of the indirect forming process. | Diaphragm Forming Diaphragm forming is suitable for more complex parts (figure 4b). The key feature of this process is the placement of the ATC blank between two stretchable diaphragms of superplastic aluminium or polyimide film. The blank is not edge clamped and may advantageously consist of semi consolidated sheet. During gradual shaping under heat and pressure interlaminar slip allows the inextensible continuous filament plies to accommodate complex curvature without fibre buckling or breakage. Here cycle times can range from 20-100 mins. Stretch Forming Conversely, stretch forming intentionally clamps the edges of the blank so that shaping takes place under tension (see Figure 4c). With impregnated fabrics or prepregs based on discontinuous aligned fibres, this method allows rapid forming with minimum fibre buckling. Cycle times are similar to hydro or rubber forming. Finally, roll forming can be used to produce linear profiles such as hat or Z sections. Here, pre heated consolidated sheet is passed through sets of shaping and cooling rollers which bend the sheet to the required form. The process is highly productive with rates up to 10 m/min being claimed, but high precision in sheet thickness is required. |