Big black boxes have been synonymous with audio speakers in the past, but a new innovative material is paving the way for wall to wall speakers that are flat, lightweight and efficient. EMFi (Electro Mechanical Film) has the capability to sense the slightest of touches and change its thickness according to an external voltage to produce its own sounds. The high sensitivity and the ease of covering surfaces of different shape and flexure make EMFi material an appealing choice for many sensor and actuator applications. Today the EMFi material is used in many commercial applications such as keyboards, microphones in stringed musical instruments, small and large area sensors, and flat loudspeakers. Using EMFi sensors and actuators together with advanced control systems and amplifiers, the material is now being developed for use in the active control of sound (ACS), which until now has been commercially unattractive and only available in a few practical applications. EMFi Flat Panel Loudspeakers EMFi is a new, innovative elastic electret film first developed in the 1980s by Finnish inventor Kari Kirjavainen. His work has continued through VTT Chemical Technology since 1994, which has taken the EMFi material to new levels through continuing research and development. One such development, is the first EMFi flat loudspeakers, expected to be commercially available later in 2001. Developed by PanPhonics Ltd, the speakers incorporate thin, lightweight EMFi panel actuators. Sound is produced by the EMFi film vibrating in an air cavity between air penetrating stators made of porous plastic or fibre material. The film creates an electric field across the air cavity between the electrodes with no need for a separate bias voltage, producing sound pressure levels of above 100 dB. The aim is to produce ACS systems based on these flat loudspeakers covering a large, wall to wall area. Other EMFi Products EMFi has also been successfully implemented into sensor products, with keyboards and guitar microphones being the first EMFi-based sensor products on the market. A Finnish company, Screentec Ltd, has introduced vandal-proof keyboards and keypads for heavy duty applications using EMFi foil - the foil being protected by a steel or plastic plate several millimetres thick, figure 1. EMF Acoustics Ltd has manufactured EMFi-based microphones for different stringed instruments, such as acoustic guitars, bass guitars and violins, with the trademark of B-Band. The good acoustic match of EMFi to wood, produces the most natural sound, and has created many EMFi pick up enthusiasts. 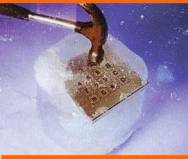 | Figure 1. A vandal-proof keypad made using EMFi technology. | When connected to a high impedance voltage amplifier or to a charge amplifier, signals from very weak phenomena can be measured both quantitatively and qualitatively e.g. raindrops and blasts of wind can be detected. The same sensors can detect the heartbeat and breath of a person standing or sitting on the sensor. The dynamics of the sensor are large. One layer can measure changes of pressure on its surface from 100 Nm-2 to 100 kNm-2 '. The upper limit is difficult to increase, because it relates to the inelastic compression of the film, while the lower detection limit depends on noise level and can be decreased by gluing, for example, 10 layers of EMFi material, one upon the other, will increase the sensitivity tenfold. EMFi Sensors EMFi sensors can be used where there is a need to monitor pressure or force changes, sound or movement. With this in mind VTT Chemical Technology together with EMFiTECH Ltd, a company that specialises in manufacturing sensors for customers and distributors and EMFi film for licensing partners have developed EMFi Floor, in which EMFi is installed under ordinary flooring. The EMFi generates an electric signal when exposed to a mechanical force such as footsteps, and although the entire EMFi sheet acts as a sensor, stationary objects such as furniture and appliances do not affect the signal and it does not set any limits for furnishing. The sensor signal is amplified and filtered by a preamplifier mounted inside a standard plug point on the wall, close to the EMFi floor sensors. A central control unit transfers the pre-processed information to a central control unit or directly via a portable phone system to an alarm unit in a nurse's pocket. Current applications of EMFi floors include patient monitoring at nursing and other care facilities. Future applications include normal guarding and surveillance applications in industrial or private buildings. What is EMFi Consisted of? The EMFi material is based on a polyolefin material manufactured in a continuous biaxial orientation process that stretches the film in two perpendicular directions (machine direction and the transverse direction). The structure of EMFi materials consists of flat voids separated by thin polyolefin layers. Typically thickness for HS01 type EMFi is 70 µm. The voids are made by compounding small particles, which function as rupture nuclei and form closed lens like cavities to the film during the biaxial orientation. A permanent electric charge is injected into the material during the manufacturing process in order to form an electret material capable of interacting with its environment. Thin metal electrodes, which are made by vacuum evaporation to both surfaces of the film, complete the EMFi structure. How Do They Work? Normally polymer electret films are corona charged with voltages ranging from 5-10 kV. In the case of solid films (without air voids) it is only possible to charge the surface of the film. The surface voltage is controllably raised to, say, 500 V. In the case of voided electret films such as EMFi the charges can also locate permanently at the polymer/gas interfaces inside the film. To charge a voided film it is necessary to use higher corona voltage to create electrical discharges inside the voided material. Our present assumption is that the discharge inside the material forms charge densities on the polymer/gas interfaces inside the voided film equivalent to the charges on the outer surface. To use the charged voided film as a sensor or an actuator, that changes its thickness according to an external voltage signal, it is necessary to provide metal electrodes on both surfaces of the film. The voided internal structure makes the film soft and elastic in the thickness direction. This means that the voids expand and contract in relation to the orientation of the film. The excellent sensor and actuator operations of EMFi are based on the fact that reduction in the thickness of the film caused by an external force takes place in the gas voids and these are much softer than the polymer layers. The direct piezoelectric transducer coefficient d33 that describes the sensor sensitivity of the electret material is very high compared to solid piezoelectric polymers such as polyvinyl difluoride (PVDF) (about 20 pico Coulombs per Newton). The transducer coefficient for EMFi is 170 pC/N for the HSO1 type. This higher value equates to increased sensitivity. The actuator operation is reciprocal to the sensor operation. This means that the thickness change corresponding to a 1 V change in voltage is 170 pm (picometers) for HSO1 film. The principles of sensor and actuator operations are explained with schematic drawings, figure 2. 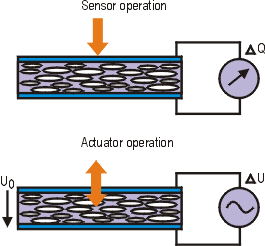 | Figure 2. Sensor operation vs. actuator operation in EMFi materials. | The HSO1 EMFi can easily be subjected to +/- 500 V driving signal without causing damage to the film. This equates to about +/- 85 nm of change in its thickness. However, the sound radiation capability of a single layer of EMFi is low. By stacking several film layers on top of each other the sound radiation can be increased, and the amplitude increase seems to be nearly linear. But, even with 20 layers the sound level at a distance of one metre from the radiating surface, is not more than 70 dB at 250 Hz and 90 dB at 1000 Hz, if the total distortion is less than 1%. The human ear can respond to sounds if they are in the audible frequency range of 20 to 20,000 Hz, being particularly sensitive to frequencies between 500 Hz and 4000 Hz. EMFi For Sound Control A new challenge is the use of EMFi in the active control of sound (ACS). ACS has been a promising method for noise control (active noise control, ANC) and other applications such as active absorption and active sound transmission, but the lack of good actuators for anti-sound production has made it difficult to control sound actively. Two European Union financed research and development projects (FACTS and SMARTACUS), as well as several other smaller ones, have been focused on the use of EMFi sensors and actuator panel elements for active noise control. So far the EMFi-based active noise control has been applied to ventilation ducts, with newer applications including the sound transmission loss increase of panels for the noise control in transportation systems and building elements. The Future For the future we are looking to concentrate our research and develop the EMFi material so it can withstand higher temperatures. At the moment, EMFi material with the highest sensitivity is suitable for operation at normal room temperature, at which the electrical properties or static charges inside the material are stable. However, EMFiTECH Ltd has developed a pre-aging process to stabilise EMFi sensors for continuous use at 60°C. The real challenge for us to is to develop the EMFi material to withstand temperatures of up to 100°C, which is a requirement of many industrial applications. New polymer materials that can easily withstand such temperatures and maintain their static charge are already available. High temperature resistive materials tend to be more rigid and their strain capacity is typically smaller. Ongoing and future research projects will deal with this problem and with the help of new prominent materials the high temperature voided electret material will soon see the daylight. |