Introduction Developments of advanced biomaterials with high performances such as good mechanical properties, bioactivity and also biocompatibility are desired with urgent aging of the population not only in Japan, but also in Europe and USA. In addition, whether the quick bone formation on fracture associated with bone-thinning osteoporosis is achieved or not is also important on the medical application to maintain high quality of life (QOL) for the elderly. Also, the activities of bone cells like osteoblasts and osteoclasts are available for the performance of biomaterials. Bone cells like osteoblasts and osteoclasts need the rough surface as a cell scaffold to adhere on cell differentiation[1]. Therefore for high performance biomaterials special studies on porous structures and surface morphologies on the biomaterials are significantly important to achieve the early treatments for fast recovery. In case of metal implants like artificial joints, the surface treatments as a cell scaffold are important to improve the bioactivity from bone cells and also to obtain bioactivity like osteoconduction. Since metal itself has no bioactivity like osteoconduction, the coatings of bioactive ceramic materials, such as hydroxyapatite and calcium phosphates as a surface treatment are in general carried out on the metal implants like artificial joints to obtain the osteoconduction and surface roughness[2-5]. Hence, the useful and simple surface treatments for metal implants, especially titanium and its alloys, are desired in order to develop the advanced biomaterials with high performances. For some decades, various surface treatments such as sol-gel coating, ion-implantation, plasma spray and chemical treatments have been reported for metals by many researchers [2-8]. Since, however, these sol-gel coating, ion-implantation, plasma spray and chemical treatments need the complicated process and long term treatments, the developments of simple and fast surface treatments for metals are required. Herein, anodic oxidation treatments in phosphoric acid or calcium glycerophoshate solutions were carried out as a surface modification of titanium metals for artificial joints. The treatments of an anodic oxidation of titanium in acid solutions can lead to the synthesis of titanium oxides layer with nanoholes on titanium for the significantly short times. On anodic oxidations of titanium in acid solutions, furthermore, it is expected that phosphorus ions could be simultaneously doped into titanium oxide layers as well as the introduction of many unique nanoholes into titanium oxide layers. It is expected that the simultaneous doping of phosphorus ions into titanium oxide layer is effective for the formation of bone-like apatite and the activation of bone cell. In the present study, the microstructures of these titanium oxide layers prepared through anodic oxidation treatments were in detail investigated by X-ray diffraction (XRD), scanning electron microscopy (SEM), and transmission electron microscopy (TEM). In addition, the investigations of electric state of phosphorus ions in these titanium oxide layers prepared by anodic oxidation treatments were carried out by X-ray photoelectron spectroscopy (XPS). The main purpose is to clarify the effect of synthetic conditions of titanium on the microstructures of titanium oxide layer through anodic oxidations for the medical applications. Experimental Procedure As a starting material, titanium sheets (10×10×0.4 mm, Niraco Co.Ltd, Japan) were prepared. Titanium sheets were polished with various abrasive SiC papers and subsequently washed with the mixture of HF and HNO3 (=1:3) solution to remove the natural oxide layer on surface of titanium. The treatments of anodic oxidation was done for a titanium sheet in 0.25 M phosphoric acid or 0.06 M calcium glycerophoshate (C3H7CaO6P) as an electrode under dc voltage of 50 V to 350 V for 2 min at RT to 353 K. On the anodic oxidations, a titanium sheet was set as an anode and a carbon rod (diameter=5 mm, length= 50 mm, Toyo Carbon) was as a cathode. The anode and cathode were at a distance of 30 mm on anodic oxidation treatments. The products obtained by anodic oxidations in each electrode were washed with ethanol and dried at 323 K in an oven. The structural components for products obtained by anodic oxidation treatments were determined using XRD (RINT 2500, Rigaku) measurements. Microstructural features of products were observed by SEM (HITACHI, S-4500) with acceleration voltage of 15 kV. The detailed microstructure was carried out on products by TEM (JEOL, JEM2010-SP) with acceleration voltage of 200 kV. Evaluations of electric state of P2p for samples after anodic oxidation treatments were carried out by XPS measurements (XPS, JPS9010-MC, JOEL) and their depth profiles of P2p XPS spectra were measured with the etching treatments in Ar for 1 to 120 min. Results and Discussion Samples obtained by anodic oxidation treatments showed gray colored surface after anodic oxidation treatments in 0.25 M phosphoric acid or 0.06 M calcium glycerophoshate with an applied dc voltage of 350 V for 2 min. The samples obtained by anodic oxidation treatments under these synthetic conditions had unique porous structures with unidirectional pores of a few hundred nm in diameter, that is, nanoholes. The surface morphologies of these nanoholes were observed in detail by SEM. Figure 1 shows the results of SEM observations of titanium samples after anodic oxidation treatments in 0.25 M phosphoric acid and calcium glycerophoshate solutions with 350 V for 2 min. Samples prepared by anodic oxidation treatments in phosphoric acid showed many nanoholes with a diameter of several hundreds nm. However, samples prepared by anodic oxidation treatments in calcium glycerophoshate solution possessed many nanoholes with more uniform pore sizes and round morphologies, compared to those of samples by anodic oxidation treatments in phosphoric acid. The number and morphology of nanoholes were dependent on the type of electrode solution on anodic oxidations. Furthermore, from SEM observations of cross section of samples (not shown here), the thickness of oxidation layer was approximately 5 to 10 μm in thickness for samples prepared by anodic oxidation treatments in both phosphoric acid and calcium glycerophoshate solutions with 350 V for 2 min. 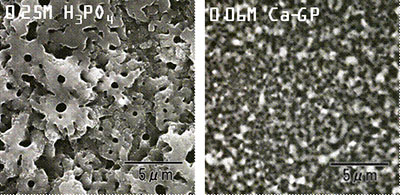 (A) (B) Figure 1. Results of SEM observations of titanium samples after anodic oxidation treatments in (A) 0.25 M phosphoric acid and (B) calcium glycerophoshate solutions (Ca-GP) with 350 V for 2 min. Figure 2 shows XRD results for samples prepared by anodic oxidation treatments in 0.25 M phosphoric acid and 0.06 M calcium glycerophoshate with 350 V for 2 min. XRD patterns of surface layers obtained by anodic oxidation at 350 V showed broad peak between 2θ=20° and 2θ=30°, identified as an anatase phase, although the crystallinity of these oxidation layers was strongly dependent on the solutions of the anodic oxidation treatments. In case of anodic oxidation treatments in calcium glycerophoshate solution, samples showed anatase phase with higher crystallinities compared to that of samples by anodic oxidation treatments in phosphoric acid. More detailed observations of microstructures of samples were carried out by TEM. The results of TEM observation (not shown here) showed that these oxide layers consisted of fine grain sizes of 20-50 nm in diameter for samples prepared by anodic oxidation treatments in phosphoric acid and calcium glycerophoshate solutions. There was no large difference in grain size of titanium oxides between samples prepared by anodic oxidations both in phosphoric acid and calcium glycerophoshate solutions, although different crystallinities of titanium oxide layers are possessed for samples prepared in phosphoric acid and calcium glycerophoshate solutions. 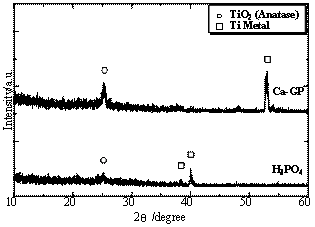 Figure 2. XRD results for samples prepared by anodic oxidation treatments in 0.25 M phosphoric acid and 0.06 M calcium glycerophoshate (Ca-GP) with 350 V for 2 min. Thus, the size, morphology and volume of nanoholes could be controlled with the synthetic conditions on the anodic oxidation treatments, such as the types of electrodes, concentration of phosphoric acid solution, temperature of acid solution, dc voltage[9, 10]. XPS profiles of P2p for the oxide layer prepared by the anodic oxidation treatments in phosphoric acid and calcium glycerophoshate solutions were measured with the Ar etching for 1 to 120 min. XPS profiles with etching time are shown in Figure 3. XPS results revealed that phosphorus ions were doped in the titanium oxide layer of samples prepared by the anodic oxidation in both phosphoric acid and calcium glycerophoshate solutions. In case of samples prepared by anodic oxidation in phosphoric acid solution, especially, the phosphorus ions at the surface of the oxide layer would exist as P5+ state, while phosphorus ions inside of the layer was P3+ state. On the contrary, in case of samples prepared by anodic oxidation treatments in calcium glycerophoshate solution, the depth profiles of P5+ and P3+ were different from those in phosphoric acid solution. Both P5+ and P3+ were equally doped into the titanium oxide layers by anodic oxidation in phosphoric acid solution. According to results in Figure 3, the phosphorus ions profile of XPS was diminished after the etching for 60 min for titanium oxide layers by anodic oxidations in calcium glycerophoshate solutions, whereas the profiles of phosphorus ions were still confirmed after the etching for 120 min for titanium oxide layers by anodic oxidations in phosphoric acid solutions. Thus, the phosphorus ions in the titanium oxide layers by anodic oxidations in calcium glycerophoshate solutions were not deeply doped, compared to ones by anodic oxidation in phosphoric acid. One reason in these different profiles of depths in phosphorus ions was thought to be attributed to the concentration of phosphoric acid and calcium glycerophoshate solutions, in which the phosphoric acid solution was four times as concentrated as calcium glycerophoshate solution on the anodic oxidation treatments. 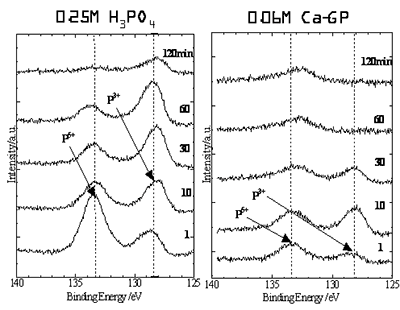 Figure 3. XPS profiles of P2p for the oxide layer prepared by the anodic oxidation treatments in phosphoric acid and calcium glycerophoshate solutions (Ca-GP) with the Ar etching for 1 to 120 min. These results suggest that many unique nanoholes were successfully generated in titanium oxide layers and simultaneously phosphorus ions were doped into titanium oxide layers through the anodic oxidation treatments in phosphoric acid or calcium glycerophoshate solutions, leading to the simple and fast treatments as a surface modification of titanium for medical usages. The bioactivity of these materials obtained in this study is now under investigation using SBF immersion tests. Conclusions Here, anodic oxidation treatments in phosphoric acid or calcium glycerophoshate solutions were carried out for the surface modification for titanium metals of artificial joints. SEM observations indicated the thickness of oxidation layer of approximately 5 to 10 μm in thickness for samples prepared by anodic oxidation treatments in both solutions with 350 V for 2 min. Samples prepared by anodic oxidation treatments in phosphoric acid showed many nanoholes with a diameter of several hundreds nm, whereas samples prepared by anodic oxidation treatments in calcium glycerophoshate solution possessed many nanoholes with more uniform pore sizes and round morphologies. These oxide layers consisted of fine grain sizes of 20-50 nm in diameter for both samples prepared by anodic oxidation treatments in phosphoric acid and calcium glycerophoshate solutions. From XPS results, phosphorus ions were doped in the titanium oxide layer of samples both prepared by the anodic oxidation in phosphoric acid and calcium glycerophoshate solutions. These rough surface containing with nanoholes and doping of phosphorous ions are expected to be useful as a cell scaffold to adhere on cell differentiation, leading to the achievement of bioactivity of titanium through the surface modification of titanium oxides by anodic oxidation treatments. Acknowledgements The authors wish to thank NSERC, Canada for financial support for this work. References 1. B. Kasemo, “Biomaterial and Inplant Surfaces: A Surface Science Approach”, The Intern. J of Oral & Maxxillofacials Implants, 3 (1988)247-259. 2. J. L. Delplanancke and R. Winand, “Galvanotic Anodization of Titanium-I, Structures and Compositions of the Anodic Films”, Electrochimica.Acta, 11 (1988)1539-1549. 3. J. Pouilleau, D. Devillers, F. Garrido, S. Durand-Vidal and E. Mahe, “Structure and Composiotion of Passive Titanium Oxide Films”, Mater. Sci., and Eng., B47 (1997) 235-243. 4. J. P. Schreckenbach, G. Mark, F. Schlottig, M. Textor and N.D. Spencer, “Characterization of Anodic Spark-Converted Titanium Surfaces for Biomedical Applications”, J. Mater. Sci., Maters. in Med., 10 (1999) 453-457. A. Cigada, M. Cabrini, and P. Pedeferri, “Increasing of the Corrosion Resistance of the Ti6Al4V Alloy by High Thickness Anodic Oxidation”, J. Mater. Sci., Maters. in Med., 3 (1992) 408-412. 5. Nakahira, K. Sakamoto, S. Yamaguchi, M. Kaneno, S. Takeda and M. Okazaki, “Novel Synthesis Method of Hydroxyapatite Whiskers by Hydrolysis of Alpha-Tricalcium Phosphate in Mixtures of H2O and Organic Solvent”, J. Am. Ceram. Soc., 82 (1999)2029-32. 6. Nakahira and K. Eguchi, “Evaluation of Microstructure and Some Properties of Hydroxyapatite/Ti Composites”, J. Ceramic Processing Res., 2 (2001) 1-7. 7. Nakahira, F. Nishimura, S. Kato, M. Iwata and S. Takeda, “Green Fabrication of Porous Ceramics using an Aqueous Electrophoretic Deposition Process”, J. Am. Ceram. Soc., 86 (2003) 1230-32. 8. K. Konishi, T. Kubo and A. Nakahira, “Characterization and Some Properties of TiO2 on Ti surface by Anodization in Acid Solution”, Water, Steam and Aqueous Solutions for Electric Power, Advances in Sci. and Tech., Maruzen, Tokyo, 2005, pp.390-394. A. Nakahira, T.Konishi, K. Yokota, T. Honma, N. Umesaki, H. Aritani and K. Tanaka, “Synthesis and Characterization of TiO2 Doped with P Ions by Anodic Oxidation of Titanium in Acid Solution”, J. Ceram. Soc. of Japan, 114 (2006) 46-50. Contact Details |