Introduction Cobalt catalysts are quite promising for oxidation–reduction processes. It is well known that the catalytic performance of supported cobalt depends upon the support properties and the nature of the surface species formed on the final catalysts [1-5]. Several studies have shown that cobalt supported mainly on aluminosilicates can display high activity for the selective catalytic hydrogenation of alkenes, aldehydes and ketenes. The effectiveness of Co/Al2O3 in the hydrogenation process depends strongly on the Co loading, the preparation conditions (e.g., calcinations temperature) and the preparation method [17-19]. The above factors determine the relative populations of the cobalt species formed on the alumina surface: Co(II) ions in CoAl2O4, small Co3O4 particles that interact strongly with Al2O3 SiO2, large Co3O4 particles and dispersed surface Co(II) ions in octahedral coordination. The latter Co(II) ions are likely the catalytically most active species for the hydrogenations process [17]. In contrast, Co3O4 particles catalyze the complete combustion of hydrocarbons by the O2 being in excess [25]. There is some debate concerning the activity of cobalt aluminosilicate. Yan and co-workers [24] and [27] proposed that the aluminate is inactive because the metal cation, Co(II), in tetrahedral coordination is shielded by the oxygen ions which hinder its contact with the gas reactants. On the other hand, Okazaki et al. [28] assigned SCR activity to the CoAl2O4 phase. However, these authors did not examine the possibility that additional dispersed forms of cobalt may be present on their catalysts. Catalytic hydrogenation of α,β-unsaturated aldehydes is an important step in the preparation of various fine chemical products. In this reaction the olefin double bond is preferentially reduced, both kinetics and thermodynamics are important considerations. This reduction occurs mainly for small aldehydes, while for larger molecules, steric restrictions imposed by the substituents may overcome the selectivity problem. [29]. In the presence of most of the conventional group VIII metal hydrogenation catalysts, α,β-unsaturated aldehydes are hydrogenated predominantly to saturated aldehydes by reduction of the C=C group or to saturated alcohols. [29] The aim of the present contribution is to study the effect of the amount of Cobalt of the samples obtained by Sol-Gel method on the activity and selectivity for the hydrogenation of crotonaldehyde. Experimental Procedure Catalysts Synthesis The silica-alumina support (SiO2: Al2O3 weigth ratio = 3:1), was prepared according to Sol-Gel technique. Required amounts of tetraethyl orthosilicate (TEOS 98% Aldrich Chemical Company, Inc.), aluminium tri-sec-butoxide (TSBA Aldrich Chemical Company, Inc.) were dissolved in anhydrous ethyl alcohol, (ET-OH, J.T. Baker S.A de C.V.). The mixture was stirred for 10 min and 28-30% w/w NH4OH was added for obtaining pH of 10. Finally water was added. The solution was aged until gel formation was accomplihshed. White opaque gels were obtained as products after drying at 70°C for 12 hours. The gels were then loaded with Co by the equilibrium deposition filtration, the conventional incipient wetness impregnation using cobalt nitrate [J. T. Baker] and calcinated at 600°C before characterization. Catalyst Characterization and Evaluation Surface Area BET specific surface area (SBET) of the supports and the catalyst was determined by N2 sorption at -196°C using a conventional all-glass vacuum apparatus equipped with an electronic manometer (MICROMERITICS ASAP 2010). X-ray Diffraction of Powder Spectra of support were obtained with an INEL EQUINOX, using Ni-filtred CuKα radiation at 30 kV and 20 mA. Hydrogen Chemisorption (TPD) Static H2 chemisorptions at 300°C on the reduced cobalt catalysts were used to determine the number of reduced surface cobalt metal atoms. Prior to H2 chemisorptions, the catalyst sample was reduced in H2 at 300°C for 1 h. Gas volumetric chemisorptions at 600°C was performed using the method described by Reuel and Bartholomew[20]. The experiment was performed using INSTRUMENTS QUANTACHROME CHAMBET-3000. Catalytic Activity Measurement Catalytic activity measurements were performed in a continuous flow fixed-bed micro reactor working under atmospheric pressure (Figure 1). The reaction mixture consisted of hydrogen and crotonaldehyde. The products from the reactor ware determined on line using a gas chromatograph PERKIN ELMER AUTOSYSTEM XI equipped with a thermal conductivity detector and a capillary column. Specimens of 50-250 mg of catalyst were used in these measurements. At the beginning, nitrogen was passed through the reactor and the catalytic bed was heated in two successive steps, first from room temperature to 300°C (10°C/min), remaining constant for 30 min, and then from 300 to 550°C (20°C/min), remaining also constant for 60 min. Then the reaction mixture was fed in the reactor, with a flow rate of 30-60 mL min-1 (STP) and catalytic tests were carried out in the temperature range 120–170°C. 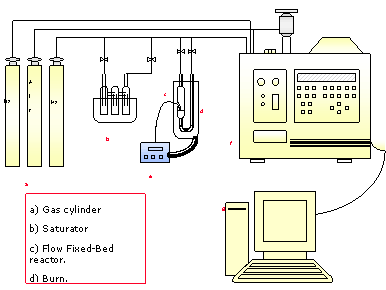 Figure 1. Continuous flow fixed-bed micro reactor working under atmospheric pressure Results and Discussion Samples Characterization of All the samples obtained by Sol-Gel method with 1, 3 and 5% cobalt, show isotherms of the type IV, characteristic of the mesopoures materials as show in Figures 2-4. 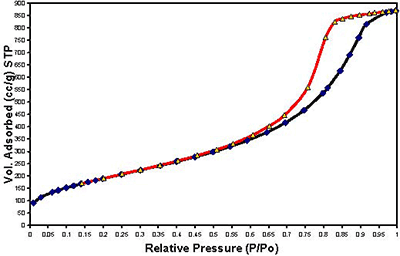 Figure 2. Adsorption-desorption Isotherms of sample M-6 with 1% of cobalt. 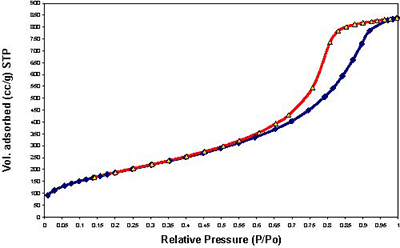 Figure 3. Adsorption-desorption isotherms of sample M-6 with 3% of Cobalt. 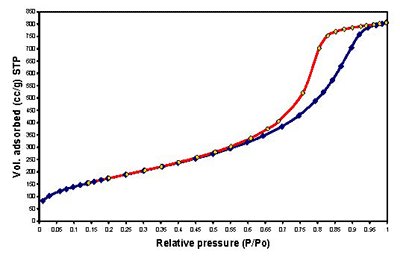 Figure 4. Adsorption-desorption isotherms of sample M-6 with 5% of Cobalt. All the synthesized solids possesed high BET surface areas. As expected, the calcined catalyst has lower BET surface area (SBET) than the supports and they show decreasing BET surface area with increasing Co loading (Table 1). This is most evident for the silica-alumina supported catalysts. These changes are suspected to be caused by plugging of support pores due to agglomeration of cobalt oxide. When the samples were calcined at different temperatures, their surface areas diminished (Table 2). Table 1. Surface areas of catalyst samples prepared by Sol-Gel method at 70°C. | M-6 1%Co | 676 | 1.34 | 74 | IV | MESOPORES | M-6 3%Co | 660 | 1.28 | 74 | IV | MESOPORES | M-6 5%Co | 617 | 1.23 | 75 | IV | MESOPORES | Table 2. Surface areas of support samples with catalyst at diferents temperatures after calcination. | 70 | 570 | 0.80 | 53 | IV | MESOPORES | 400 | 449 | 0.61 | 52 | IV | MESOPORES | 800 | 212 | 0.25 | 45 | IV | MESOPORES | All Samples obtained by Sol-Gel method and with 1, 3 and 5% Cobalt, respectively are amorphous (non-crystalline) as shown in Figure5. 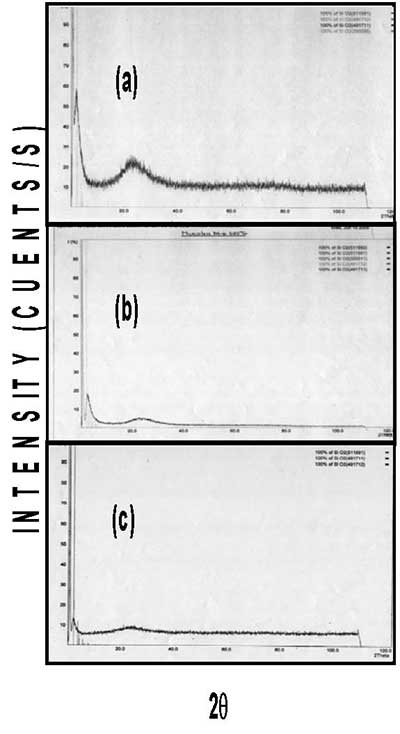 Figure 5. Catalyst Samples with (a) 1% cobalt (w/w), (b) 3% cobalt (w/w) and (c) 5% cobalt (w/w). The adsorption of hydrogen on M-6 containing different amounts of cobalt are shown in Figure 6. To determine the number of cobalt atoms interacting whit hydrogen, the area under the catalyst adsorption peak is divided by the area under the hydrogen standart curve. The distribution of the cobalt atoms on the support surface is then calculated by dividing the amount of cob atoms interacting by the total cobalt atoms present in the catalyst. 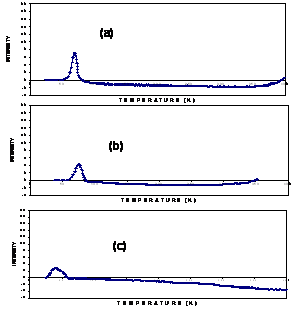 Figure 6. Absorption of H2 on the catalyst M-6 with (a) 1%, (b) 3% and (c) 5 % of cobalt w/w. The H2 chemisorption results corresponding to all catalyst samples are shown in Figure 7. It was found that the amount of adsorbed H2 increased untill the percentage of cobalt was 3% (w/w). It decreased with 5% effect of impregnated cobalt. This is due to a mass of the metal in the material. Since H2 chemisorption is a surface technique that the reduced Co metal surface atoms can be measured directly. However, based on the H2 chemisorption results in this present study, different percentages of cobalt exhibited different amounts of H2 chemisorbed on the catalyst samples. 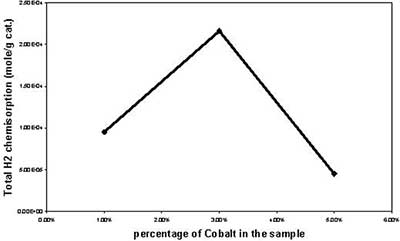 Figure 7. H2 chemisorption for Co/Al2O3.SiO2 catalysts with various percentages of cobalt used. In Table 3 the distribution of Cobalt impregnated on the surface of the catalyst is shown. A decrease in cobalt distribution percent is observed as the percentage of impregnated cobalt increased. This can be due to metal agglomeration in the material. Table 3. Distribution of cobalt in the support surface. | M-6 1%Co | 676 | 59 | M-6 3%Co | 660 | 59 | M-6 5%Co | 617 | 7 | Catalytic Behavior Table 4 contains the data for the crotonaldehyde conversion and selectivity to butiraldehyde achieved by the catalysts with 5% Co loading over the aluminosilicate support at reaction temperatures in the range 130–170°C. As can be seen the conversion of the crotonaldehyde increases with the temperature. Table 4. Crotonaldehyde conversions achieved over the catalysts with 5% Co loading and the support at reaction temperatures in the range 130–170°C. | 130 | 45.34 | 100 | 3.69 | 150 | 0.073 | 0.029 | 150 | 43.19 | 100 | 6.83 | 150 | 0.070 | 0.050 | 170 | 41.24 | 100 | 8.41 | 150 | 0.067 | 0.059 | However as it can be seen from Table 5 the conversions of crotonaldehyde determined by the catalyst with different amounts of sample used in the reaction loading showed significantly higher conversion with higher amount. Table 5. Conversions of crotonaldehyde into butiraldehyde achieved over the catalysts with different amounts of sample (50,150 and 250 mg) at reaction temperatures of 150°C. | M-6 5%Co | 259.15 | 100 | 3.14 | 50 | 0.42 | 0.139 | M-6 5%Co | 86.38 | 100 | 5.12 | 150 | 0.14 | 0.076 | M-6 5%Co | 51.83 | 100 | 31.27 | 250 | 0.08 | 0.277 | Conclusions The present research showed a dependence of the characteristics and catalytic properties during crotonaldehyde hydrogenation on percentage of cobalt in the samples. The study revealed that the hydrogenation is selective towards the double link because butiraldehyde was obtained. These catalysts exhibited the highest activity during crotonaldehyde hydrogenation when one works with larger quantities of sample. The steric impediment plays a very important role for this type of materials because of the low efficiency of these materials. Acknowledgements We gratefully acknowledge to the Universidad de Guanajuato (U de G), the Universidad Autonoma Metropolitana (UAM-I) and CONACYTfor its invaluable support through to this project. References 1. R.J. Farrauto and C.H. Bartholomew, Fundamental of Industrial Catalytic Processes, Blackie Academic & Professional, London (1997), pp. 640–644. 2. J. Spivey and J. Butt, Catal. Today 11 (1992), p. 465. 3. R.L. Chin and D.M. Hercules, J. Phys. Chem. 86 (1982), p. 360. 4. M.J. Dees, T. Shido, Y. Iwasawa and V. Ponec, J. Catal. 124 (1990), p. 530. 5. L. Guczi, T. Hoffer, Z. Zsoldos, S. Zyode, G. Maire and F. Garin, J. Phys. Chem. 95 (1991), p. 802 6. R.D. Jones and C.H. Bartholomew, Appl. Catal. A 39 (1998), p. 77. 7. R. Bechara, D. Balloy and D. Vanhove, Appl. Catal. A 207 (2001), p. 343. 8. L.F. Liotta, G. Pantaleo, A. Macaluso, G. Di Carlo and G. Deganello, Appl. Catal. A 245 (2003), p. 167. 9. J. Zhang, J. Chen, J. Ren, Y. Li and Y. Sun, Fuel 82 (2003), p. 581. 10. L.F. Liotta, G. Pantaleo, G. Di Carlo, G. Marcì and G. Deganello, Appl. Catal. B 52 (2004), p. 1. A. Kogelbauer, J.G. Goodwin Jr. and R.J. Oukaci, J. Catal. 160 (1996), p. 125. 11. Y.L. Zhang, D.G. Wei, S. Hammache and J.G. Goodwin Jr., J. Catal. 188 (1999), p. 281. 12. F. Rohr, O.A. Lindvag, A. Holmen and E.A. Blekkan, Catal. Today 58 (2000), p. 247. 13. P.A. Chernavskii, G.A. Pankina and V.V. Lunin, Catal. Lett. 66 (2000), p. 121. A. Martínez-Hernández and G.A. Fuentes, Appl. Catal. B 57 (2005), p. 167. 14. Fritz and V. Pitchon, Appl. Catal. B 13 (1997), p. 1. 15. R. Burch, J.P. Breen and F.C. Meunier, Appl. Catal. B 39 (2002), p. 283. 16. Y. Kintaichi, H. Hamada, M. Tabata, T. Yoshinari, M. Sasaki and T. Ito, Catal. Lett. 6 (1990), p. 239 17. H. Hamada, Y. Kintaichi, M. Sasaki, T. Ito and M. Tabata, Appl. Catal. 75 (1991), p. L1. 18. H. Hamada, Y. Kintaichi, M. Sasaki, T. Ito and T. Yoshinari, Appl. Catal. A 88 (1992), p. L1. 19. H. Hamada, Y. Kintaichi, M. Sasaki, M. Tabata, T. Ito and T. Yoshinari, Catal. Today 17 (1993), p. 111. 20. H. Hamada, Catal. Today 22 (1994), p. 21. 21. H. Hamada, Y. Kintaichi, M. Inaba, M. Tabata, T. Yoshinari and H. Tsuchida, Catal. Today 29 (1996), p. 53. 22. J. Yan, M.C. Kung, W.M.H. Sachtler and H.H. Kung, J. Catal. 172 (1997), p. 178. 23. N. Okazaki, Y. Katoh, Y. Shiina, A. Tada and M. Iwamoto, Chem. Lett. 26 (1997), p. 889. 24. M. Inaba, Y. Kintaichi, M. Haneda and H. Hamada, Catal. Lett. 39 (1996), p. 269. 25. M.C. Kung, K.A. Bethke, J. Yan, J.-H. Lee and H.H. Kung, Appl. Surf. Sci. 121/122 (1997), p. 261. 26. N. Okazaki, S. Tsuda, Y. Shiina, A. Tada and M. Iwamoto, Chem. Lett. 27 (1998), p. 429. 27. P. Reyes, M. Aguirre, G. Pecchi AND J.L.G. Fierro, Bol. Soc. Chil. Quím. v.45 n.1 Concepción mar. 2000. Contact Details |