The component designer faces some difficult decisions when working with metal matrix composites (MMCs), due to the comparatively low volume of data on the processes available for joining these materials and, in particular, to the very sparse data on the performance of the joints. Despite the intense effort put into the development of high performance composites, relatively little work has been directed towards joining the materials. The ability to make economic and reliable joints in these materials will be an advantage in their commercial uptake, and without this capability, MMCs will be restricted to fewer applications. Assuming that a particular strength is required, there are generally a variety of MMCs available. At present, the available data do not cover the properties of joints in all materials, joined by all processes and, for most combinations, there is little or no information. Although some processes seem to work well with many MMCs (e.g friction welding), there is considerable evidence to suggest that this may not be the case for other processes. There are a number of methods available for joining MMCs, some being more successful than others, table 1. Three processes will be addressed in this article; tungsten inert gas (TIG) welding, friction welding and adhesive bonding. Table 1. Relative ratings for processes used for bonding MMC’s. | TIG | good | good | good | MIG+ | good | good | good | Resistance | fair | n/a | n/a | Laser | poor | poor | poor | Electron Beam | poor | poor | poor | Friction Welding | n/a | good | good | Diffusion Bonding | fair | fair | fair | MIAB* | n/a | fair | n/a | Flash Welding | n/a | good | good | Brazing | fair | fair | fair | Adhesives | good | good | good | + = metal inert gas welding, * = magnetically impelled arc butt welding Fusion Welding In general, arc fusion processes are economical and flexible. They are well established for joining conventional aluminium alloys, but there are particular problems which must be considered when joining aluminium based MMCs. Molten MMCs are viscous, and therefore mixing with conventional filler alloys is difficult. During solidification, in certain instances, a solidifying interface will reject reinforcing particles giving rise to heavily reinforced and unreinforced regions in a weld. The degree of particle clumping is also a function of particle size, cooling rate and gravitational effects and particle/matrix combinations. A final consideration is the reaction in Al/SiC MMCs between the aluminium matrix and silicon carbide reinforcing particles: 3SiC(S) + 4Al(I) --> Al4C3(S) + 3Si(S) This reaction is not reversible, and the aluminium carbide (Al4C3) forms as plates in the microstructure. The presence of the plates has two deleterious effects. Firstly, the material becomes extremely brittle, and secondly it becomes very prone to corrosion in the presence of water, leading to the release of acetylene gas. In extreme cases, this has led to the total disintegration of the weld within a few days. The formation of Al4C3 is accelerated at higher temperatures, and is more frequently reported in power beam welds, where the high energy density leads to higher pool temperatures. It is possible to use power beam processes, but care is required in the choice of welding parameters, and experience has shown that matrix composition is also an important variable in determining the risk of Al4C3 formation. Tungsten Inert Gas Welding The TIG process is widely used for welding unreinforced aluminium alloys and, although it is not the fastest process available, it is flexible, in that the deposition rate and heat input can be largely independent when a filler is used, and the process can be automated. A closer study of the process has been made at TWI, using 3.1 mm thick 2080/SiC and 2 mm thick 7475/SiC alloys. Welding was carried out both autogenously and using a filler wire addition. Melt runs in both alloys were characterised by a sooty surface appearance, which was also rougher in texture than would be expected for unreinforced aluminium alloys. Despite the visual appearance, the quality of the deposits, judged from macrosections, was good. No evidence for cracking, porosity, lack of fusion or massive segregation was found. A thin layer of particulate-free material was evident at all free surfaces, suggesting that the sooty deposit is a result of the breakdown of sic.
Manipulation of the molten pool was very difficult, due to the high viscosity of the molten MMC. Examination of the autogenously melted material by light microscopy showed no evidence for the formation of Al4C3 needles. Further examinations were conducted to evaluate the microstructures in greater detail. Particular attention was paid to investigating possible reactions between the SiC and molten aluminium matrix. A typical backscattered electron image, taken in a scanning electron microscope (SEM) from an autogenous weld in 2080/SiC material, showed that the solidification structure is closely related to the particle distribution. There is no evidence to suggest that the particles act as nucleation sites, but it is apparent that the interdendritic phase, rich in copper and magnesium, frequently lies adjacent to the SiC particles. The distribution of the phases strongly indicates that the SiC particles are rejected by the solidifying interface, and are surrounded by the last material to solidify. In the autogenous weld in 2080/SiC, there was again no evidence for the formation of Al4C3. Hardness tests showed a significant drop in hardness in the fused zone of the 2080/SiC, from 160 to 170 HV in the parent material to 140 to 145 HV in the fused zone. The 7475/SiC alloy showed no such drop, with values of 180 to 190 HV being observed across the joint. A number of welds were made in the 2080/SiC MMC. In order to overcome the problems of high melt viscosity in the autogenous welds, a 4047A filler was chosen because of its very high fluidity. However, it was apparent from preliminary trials that the molten 4047A (Al-Si) filler would not mix easily with the molten MMC. The best results were obtained using parameters which minimised dilution, examples are shown in figure 1. It is clear that some support for the pool is required from beneath, to prevent sagging, and back shielding is also necessary. In many respects, the operation is closer to brazing than welding, even though the MMC is molten during the joining operation. 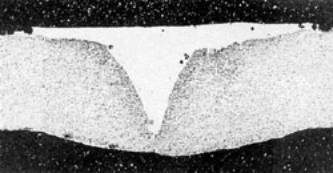 | Figure 1. Section through a TIG weld in 2080/SiC MMC, made with 4047A filler. | Light microscopy again showed no evidence for Al4C3 formation, but it was evident that some mixing of the filler and MMC had occurred close to the boundary between the pool of filler and the molten MMC. Examination of the microstructure in an SEM showed the formation of the Al-Si eutectic in the melted filler metal, and that this eutectic surrounded SiC particles close to the filler/MMC boundary. Traces of the Al-Si eutectic could be found up to 2 mm from particle/no particle boundary, and yet there was no evidence of significant redistribution of the reinforcement. At higher magnifications obtainable in the SEM, no Al4C3 was observed, but this is perhaps not unexpected, for two reasons. Firstly, the weld thermal cycle is not dissimilar to the autogenous welds, where no Al4C3 was formed. Secondly, one of the products of the reaction is pure silicon. As there is an abundance of pure silicon in the weld from the Al-Si eutectic, this would reduce the driving force for the reaction. This effect is utilised in the casting of Al-SiC products. As expected, the hardness in the 4047A region was much lower than that of the 7475/SiC, although it showed a significant increase after solution treatment and ageing. Parent material values were 160 HV, and the weld metal hardness was 90 HV as welded, increasing to 150 HV after a T6 heat treatment. Solid State Welding There is considerable experience of solid phase welding of aluminium (friction welding and diffusion bonding), and many studies have been made of the response of MMCs to these processes. Friction welding is suitable for joining MMCs, as there are no problems arising from the viscous weld pool, and no particle/matrix reaction is expected. Welding of a 45 mm diameter bar of 2618/SiC MMC was undertaken using rotary friction welding. There was little dependence of the weld appearance on process parameters, and a typical macrosection from one of the welds is shown in Figure 2. This shows quite clearly the extent of the plastic deformation around the bond line, and the weld flash formation. As is usually the case in aluminium alloys, the flash separates along the weld line outside the weld. More detailed examination of the microstructure close to the bond line showed no evidence of cracks, lack of bonding, oxide films or any other defect. However, individual SiC particles close to the bond line had clearly broken up to give a finer dispersion. Detailed examination of the bond line microstructure in an SEM showed no evidence for any reaction between the SiC and the matrix. 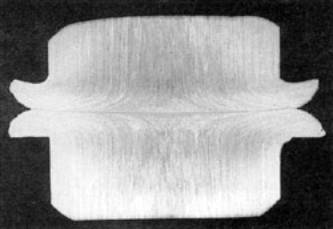 | Figure 2. Section through a rotary friction weld in 2618/SiC. | In the as-welded condition, a minimum hardness value of about 120 HV appeared about 5 mm either side of the weld, although the parent material hardness (160 HV) was almost recovered at the bond line. After an ageing treatment, very little change was seen, indicating that the structure was probably overaged by the welding process. However, a full solution treatment and ageing heat treatment led to full recovery of the parent material hardness, with no significant variation across the joint. Adhesive Bonding Adhesive bonding is a rapidly developing technology, with significant improvements being made continuously in the strength and durability of adhesive bonds, and the range of service environments in which such bonds can operate is being expanded. A wide range of adhesive types is now available, suitable for aluminium alloys, but preference in this work was given to those types with potential for higher temperature service. A major advantage of this technique is that bonds can be made at ambient temperature with curing temperatures below 200°C, thus minimising thermal damage to the aluminium matix. The potential for adhesive bonding of aluminium MMCs is demonstrated by work carried out on 2 mm Al-Li (8090) alloy sheet. It is well established that such alloys can be very active, and that some pretreatments are necessary to promote the most efficient bonding. Initial trials investigated the use of toughened acrylic and one part heat curing epoxy adhesives. For the toughened acrylic trials, three surface pretreatments were used: degreasing with trichlorothane, abrasion with 600 grit emery paper and degreasing, and abrasion in the presence of a bonding agent. For the one part heat curing epoxy trails, the same surface treatments were used, except that a more appropriate bonding agent was employed. In this case, abrasion took place while the specimen was immersed in the bonding agent, and so no degreasing was used. Trials were also undertaken using a structural nitrile phenolic film adhesive, with primer, and with a structural modified epoxy film adhesive, together with the same primer. Specimens made with both adhesives were cured for 1 hour at 177°C, under a pressure of 310 kN.m-2. All joints were made as single lap joints between strips of material of 100 by 25 mm, allowing a 15 mm overlap at the joint (ASTM D‑1002‑72). A constant adhesive thickness of 0.25 mm was maintained by the use of shims, and a modest pressure was applied during curing. The results of lap shear tests on bonds made with the toughened acrylic and two part heat cured epoxy were found to be very sensitive to surface pretreament, with best results obtained when using a bonding agent. Values of 17 M.N m-2 and 27 MN.m-2 average fracture stress were obtained in the toughened acrylic and epoxy bonded joints respectively. The use of nitride phenolic and epoxy film adhesives, with appropriate primers, gave mean fracture stress values of 2 and 21 MN m‑2. Although the results are very variable, it is considered that significant improvements are likely if surface pretreatments are optimised. All failures were cohesive, i.e. the fracture was contained entirely within the adhesive layer. Although relatively high strength bonds are achieved using adhesives, these high strengths do not necessarily equate to high durability. The long term stability and performance of these joints is still not known. Conclusion Work at TWI and other laboratories has demonstrated that particulate reinforced aluminium MMCs can be joined by a variety of processes, although many of the conventional processes which are well established for joining unreinforced aluminium alloys are presented with new challenges when joining MMCs. For the future, a better understanding of the SiC/Al reaction is required, in terms of compositional and process effects. Quality assurance (QA) and non-destructive testing (NDT) of joints in these materials are also issues which need to be addressed. There are insufficient data on the environmental performance of joints, and this information must be available before designers can feel comfortable with MMC alloys, and begin to exploit, more fully, the potential of these materials. |