Jun 20 2001
This article was updated on 4th Feb 2020 by Clare Kiernan.
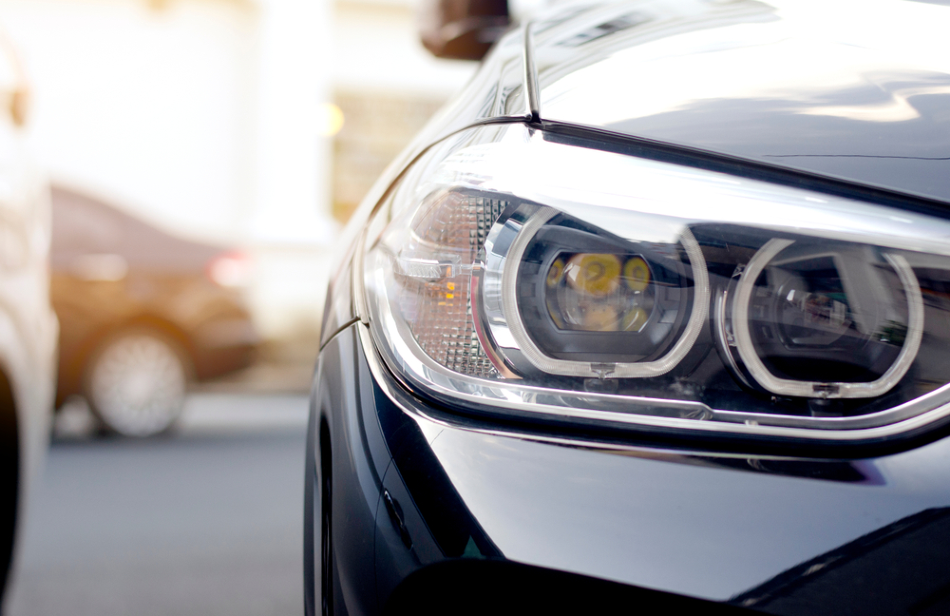
Image Credit: Nawin Kitpipatphinyo/Shutterstock.com
The automotive applications of titanium and its alloys follow logically from high strength, low density and, low modulus, and they have excellent resistance to corrosion and oxidation. Titanium is primarily used in internal combustion engine components, such as valves, valve spring, retainers, and connecting rods.
Springing is the principal application on vehicle bodies and exhausts capable of surviving a 100,000-mile warranty, wheels, high-strength fastenings and corrosion-resistant, damage-tolerant underpanels are also being evaluated.
The performance benefits of titanium in automotive applications have been established and widely reported over many years, demonstrating that titanium works. However, due to costs, the use of the metal has been limited to racing cars and a few top-of-the-range road models.
The titanium industry has attempted to meet the tough financial and life cycle targets set by the automotive industry in the past, and attention has concentrated on three areas:
- Development of lower cost alloys
- Exploration of low-cost manufacturing methods
- Where required, evaluation of treatments to enhance wear resistance.
Progress for the Titanium Industry
Positive progress has been made towards the cost-effective application of titanium in vehicles for the mass market. The leading applications are cold wound springs manufactured from low-cost beta alloy, and exhaust systems manufactured from commercially pure titanium.
These two classes of components are currently being manufactured for the automotive industry in titanium, using processes and tooling designed for manufacturing parts in steel.
Automotive suppliers and manufacturers look at the total system cost, and while the titanium industry aims to develop low-cost alloys, it is clear that cheaper titanium alone will not guarantee an automotive application, but a competitively priced titanium component will.
Therefore, there is a need to establish low-cost manufacturing methods for titanium parts. In working with automotive designers, the industry monitors the cost-benefit of using titanium, and remains abreast of all design and production developments, to reduce the cost and manufacturing challenges.
Requirements of the Automotive Industry
For automotive producers, style and performance remain key sales factors, but environmentally aware customers with increasingly educated social consciences want not only these, but also greater safety, minimum noise, maximum fuel economy, and the continued reduction of harmful emissions.
The pressure of legislation, typically the US Corporate Average Fuel Efficiency (CAFE), adds to market competition and growing customer demand - forcing design and material changes. As demand increases for more fuel-efficient and environmentally friendly cars, affordability is less of an issue. More improvements are being incorporated into engines, suspension, and bodywork.
Increases in the cost of fuel serve to hasten this process, which also allows for more to be spent on corrosion resistance, weight, and fuel-saving.
Table 1. Estimate of savings on fuel costs due to reduced weight in manufactured vehicles.
Type of vehicle |
$/car/kg of weight saved |
Mass production |
$2.20 |
CAFÉ limited |
$4.50-$7.70 |
Specialty and luxury |
$8.50+ |
Titanium Springs
Uniquely among engineering alloys, titanium possesses the strength, density, and modulus to make the ‘ideal’ spring for almost every application. Successful spring design means optimizing the saving of weight and space. Titanium springs are smaller and typically 60-70% lighter than steel equivalents. Several design concepts for cars, across a range of models, have space constraints that cannot be met using steel springs.
Spring weight for a given load and spring rate is proportional to the product of the shear modulus and density of the alloy divided by the square of the allowable stress. Weight is minimized with titanium because of its low shear modulus and density combined with high allowable stress.
Simultaneously, spring deflection is inversely proportional to shear modulus and is therefore high for titanium. Consequently, fewer active coils are needed, which allows for a reduction in free height (by 50-80% of a comparable steel spring), with further weight reduction and a higher natural frequency.
Valve Springs
Valve springs represent an attractive entry point for titanium into the automotive engines for the mass market. The potential to reduce overall engine heights is beneficial when space is constrained. When combined with titanium valves and valve retainers, further savings are possible, as less spring power is required to prevent ‘valve bounce’ at high engine speeds.
Alternatively, titanium can be used without incurring a weight penalty to increase the spring load and permit a more rapid valve motion and greater rpm. The use of lower spring loads with lighter valves reduces the friction of the valve system that is typically about 20-25% of the total mechanical friction of the engine.
Lowering friction without compromise to engine power output gives improved engine efficiency, less noise, and reduced fuel consumption.
Estimated savings on fuel vary from 2% to 4% according to engine type. Greater levels of improvement are possible in engines with four valves per cylinder; where twice the number of moving parts and sliding faces generate a greater proportion of the overall engine friction.
Surface treatment to improve the wear resistance of titanium alloys is key to the success of the overall application in the valve train. Exhaust valves present a particular challenge to provide oxidation and creep resistance at high operating temperatures.
Suspension Springs
Titanium suspension springs provide an opportunity for savings of weight and space. A typical helical spring design in titanium, when compared to a steel version, will reduce the weight by upwards of 70% (4.12 kg to 1.36 kg in one example).
Rigorous schedules of on and off-road testing have been conducted. Although the mass market of private cars is a clear target for the wider use of titanium suspension springs, applications of comparable importance exist for public service vehicles and freight haulage.
Additional carrying space, reduction of weight, and saving of fuel may permit increasing payload or greater operating range and more revenue. A case study conducted in the US on a long haul freight vehicle showed a weight saving with titanium springs of 140 kg, for an additional outlay of £1000 (US$1316) on the cost of the truck. Turning the weight saved into cargo over a typical 600 trips produces added revenue of £8000 (US$10526) and a net annual return on investment of 20%.
The corrosion resistance of titanium alloys is also beneficial to service life for springs on equipment, even if it is only occasionally operated in aggressive conditions. Corrosion fatigue is the probable cause of the majority of steel suspension spring failures in motor vehicles.
Titanium Spring Materials
A wide range of titanium alloys is suitable for making springs. Good performance has been achieved with Ti-6Al-4V and other alpha-beta alloys, but much better results are obtained from the higher strength beta alloys, which are more easily drawn into wire and cold fabricated to form springs.
Of these, the Ti-4.5Fe-6.8Mo-1.5Al alloy (Timetal LCB) offers the best combination of desirable properties at an economical price. This was developed primarily for automotive springs and can be formulated at approximately 50% of the cost of typical existing beta alloys. Given sufficient production volume, its price should ultimately achieve the target for cost-effective use in automotive springs and other components.
Properties of Titanium Alloys
The strength, density, shear modulus, and relative weight of this alloy are compared with those of steel of similar tensile strength in Table 3. This table represents the optimum comparison for steel because it is not uncommon to apply an allowance for corrosion to the diameter of the steel spring, making it even heavier and bulkier. No such allowance is required for titanium, nor is there normally any need to apply paints or other protective coatings or anticorrosion treatments.
Table 2. Properties of Timetal versus Ti-6Al-4V.
Property |
Ti-6Al-4V Bar STA |
Timetal 10-2-3 |
Timetal LCB |
RT yield strength (N.mm-2) |
1100 |
1200 |
1350 |
RT UTS (N.mm-2) |
1185 |
1275 |
1420 |
Elongation (%) |
13 |
9 |
10 |
R of A (%) |
24 |
21 |
35 |
Density (g.cm-3) |
4.43 |
4.64 |
4.79 |
Tensile Modulus (103 N.mm-2) |
112 |
106 |
110 |
Fatigue endurance limit (N.mm-2) |
RT Smooth (kt=1) |
895 |
950 |
1000 |
RT Notched (kt=3) |
240 |
290 |
330 |
Beta alloys as a class offer designers many options to select a final combination of properties for specific applications. Consultation with the alloy producer and the spring manufacturer is recommended for the appropriate method of manufacture and finishing to be used.
Table 3. Properties of Timetal springs versus steel equivalents.
Property |
Steel |
Timetal LCB |
Allowable Stress (N.mm-2) |
1000 |
1000 |
Shear Modulus (103 N.mm-2) |
80 |
43 |
Density (g.cm-3) |
7.82 |
4.78 |
Relative weight |
100 |
33 |
Timetal LCB spring wire can be supplied hot rolled, or hot rolled and cold drawn, (normally up to 20% cold reduction), or hot rolled and solution treated. LCB can be either cold wound or hot wound at 700-760 °C. If hot wound, springs would be fan air-cooled and aged. Cold wound springs may pass directly for aging, typically at 510-540 °C for up to two hours.
Finishing of springs manufactured by either method can be blasted and pickled followed by shot peening, typically to 16-18A intensity.
Production Economics
The manufacturing methods for LCB springs enable production costs and production rates to be achieved which are similar to steel springs. Employing standard steel spring making equipment, standard dry coatings for cold coiling, with similar aging (tempering) furnaces, temperatures and times.
Here, capital costs for re-equipment normally associated with the implementation of new materials and technologies can be negated, and production rates equivalent to those for steel springs have been achieved.
Titanium Exhaust Systems
In the US, environmental agencies require guaranteed corrosion resistance on exhaust systems above 100,000 miles. Titanium easily achieves this and surpasses the stainless steel (409) systems. A typical expansion box and tailpipe in 409 steel weighed 10 kg, compared to a re-design made from titanium, which reduced this to 3.2 kg.
Pure titanium sheet and tube are the preferred commercial materials for silencers and pipework. By selecting the thinnest gauges of materials consistent with the engineering and acoustic requirements of the exhaust system improves both weight and cost.
Titanium may not be suitable for the entire system, and in practice will most probably be limited to components where the metal temperature does not exceed 400 °C for sustained periods. US units coupled immediately behind the catalytic converter continue to perform well.
The use of titanium lugs welded to the pipe likely proves to be the most effective way to attach the exhaust to the chassis, (via rubber isolators), but other methods are being tested.
Suitability of Titanium Alloys
Material conforming to ASTM Grade 2, (e.g. Timetal 50A) offers the optimum for cost, availability, fabricability, weldability, and mechanical properties. Grade 45A is slightly less strong and more ductile than 50A and may be required where extensive forming is part of the manufacturing process e.g. lock seaming (Table 4).
Table 4. Properties of commercially pure titanium Timetal 45A and 50A.
Grade |
45A |
50A (ASTM 2) |
Proof Stress min (N.mm-2) |
200 |
275 |
UTS min (N.mm-2) |
290 |
345 |
Elongation min (%) |
23 |
20 |
RA min (%) |
40 |
35 |
Hardness (Hv) |
140-170 |
160-200 |
Tensile modulus (103 N.mm-2) |
103 |
103 |
Torsion modulus (103 N.mm-2) |
45 |
45 |
Density (g.cm-3) |
4.51 |
4.51 |
Thermal expansion (10-6 °C) |
8.9 |
8.9 |
Thermal conductivity (W.m-1.°C-1) |
21.6 |
21.6 |
Specific heat (J.kg-1.°C-1) |
519 |
519 |
Both alloys are fully weldable, require no intermediate or post-forming heat treatment, and are available in wide sheet coil. These alloys are also used to manufacture low-cost continuously welded tubes.
Titanium Production Allowances
Commercially pure titanium is cold formable, and sheet and tube can be shaped readily at room temperature using techniques and equipment suitable for steel. Attention to three points of detail ensures trouble-free production:
- The ductility of titanium is generally less than that of steel. More generous bend radii may be required or Timetal 45A used to meet essential tight bending and seaming requirements.
- The modulus of elasticity of titanium is about half that of steel and therefore it will spring back after forming. Compensation for this is made by slight over-forming.
- Titanium tends to gall against unlubricated forming tools. Clean, properly lubricated tooling presents no difficulty.
Both lock seaming and resistance welding are suitable to close the expansion box, and autogenous TIG is suitable to seal the ends and pipe joints with a torch trailing shield to the external surface of the box end joints. Argon shielding is not required for resistance welding.
Production Economics
In the US, a leading exhaust system manufacturer, Arvin, successfully rolled and seam welded a run of titanium boxes at one of its plants. This was done with no cost penalty compared with steel production. The company has also found that no extra costs apply when bending titanium tubes through plants that are currently producing steel components.
Summary
Practices made possible by cold hearth melting, enable ‘ingot’ for strip production to be cast as slab and then hot-rolled directly to coil; which is the feedstock for final cold reduction to strip. Timet is well-equipped for strip production and finishing, and with the combined Sendzimir mill and continuous vacuum annealing line, it is a long-established low-cost producer of both strip and tube.
Rolling of commercially pure titanium is an uncomplicated process, with high yield and excellent reproducibility. Additional capacity to accommodate a substantial growth of demand in one product sector; e.g. strip for exhaust manufacture; almost certainly exists outside the titanium industry with companies that supply automotive steels.
Titanium will likely become a part of the normal delivery program of these companies, who will seek to retain their share of the market as titanium gains a more significant place in mass-market vehicles.