Advances in engineering rely on the development of new materials. The materials must have improved properties, capable of being tailored to a specific application need, to fulfil the requirements of designers of the future. Ceramic fibres are playing a major part in enabling the development of new composite materials capable of withstanding the forces and temperatures exerted on components in industries as diverse as aerospace and sports goods. However, the currently available fibres have limitations or problems associated with their manufacture and use, and can be expensive. Commercial Fibre Production Several types of ceramic fibres are currently available for use in a variety of applications. These can be divided into two main categories. Oxide Fibres Mainly based on alumina, oxide fibres suffer from both grain growth problems, which destroy the fibre’s integrity, and phase change problems above 1100°C on the heating and cooling cycles. They are manufactured by three different techniques. Slurry spinning involves a dispersion of submicron crystalline ceramic particles, in an organic polymer or an alumina precursor polymer, being dry spun into a fibre. The sol-gel method produces microscopic gels by the spinning of viscous solutions of inorganic metal alkoxide polymers and silicon alkoxide, which are then heated to drive off any volatile materials to produce porous fibres with a non-uniform cross-section. Finally, single crystal fibres can be made from the film edge defined growth process, an expensive technique which produces alumina, and yttria-stabilised alumina filaments. Non-Oxide Fibres Two main fabrication methods are used to produce non-oxide fibres. A polymeric route involves the reduction and thermal rearrangement of organosilicon halides, which are then melt spun to a very fine fibre (7-14µm). Chemical vapour deposition (CVD) can also be used, whereby a fine carbon or tungsten filament is exposed to an organosilicon gas, leading to a chemical reaction and the production of a ceramic fibre. The CVD process also enables the coating of fibres, to give protection against reaction or to give modified properties, but this is an extra step in the production of the final fibre, and so adds the cost. Ceramic Fibre Usage A variety of composite materials benefit from incorporating ceramic fibres into the structure. Organic Matrix Composites Organic matrix composites are generally reinforced by either glass or carbon fibres, which increase stiffness and fatigue life, and decrease the dielectric constant, improving the compressive strength. Glass matrix composites have been developed for use in gas turbine or military applications. In general, these are either lithium or magnesium alumino-silicates reinforced by silicon carbide fibres, or glassy carbon systems made from phenolic resins, reinforced by various non-oxide fibres. Metal Matrix Composites Metal matrix composites are very popular materials due to their high stiffness, strength, temperature properties, fatigue life and creep resistance. The main drawback to using ceramic fibres in metal matrices is that the alloying elements react preferentially with the ceramic fibres, destroying their reinforcement integrity. To prevent this, the fibres would need to be coated with another material, which would act as an interface between the matrix and its reinforcing fibre. Ceramic Matrix Composites Ceramic matrix composites can also benefit from the use of ceramic reinforcing fibres, but again, reaction between the fibre and the body ceramic can cause degradation. Bicomponent Extrusion Bicomponent extrusion is a spinning technique to simultaneously extrude two different ceramic precursors through the same orifice by dry or melt spinning. This produces ceramic fibres with mainly a core and sheath component structure, although matrix-fibril and other arrangements of the components are possible. Bicomponent extrusion can be simply thought of as two spinning machines working one inside the other. Two sets of electric drive motors, gear boxes, drive shafts and pumps are required, and these are fed by twin reservoirs via capillary tubes using two sets of pressure transducers. However, a central temperature measurement system can be employed. The capillaries from the reservoirs feed into a central mixer head at an angle of 90° to each other, allowing the core precursor to feed directly to the core spinerette, whilst the sheath capillary divides via a cannula into two capillaries round either side of the core capillary. Following extrusion, the fibres can be cured using similar techniques to those employed to cure monolithic (single component) fibres, including heating, oxidation, radiation and chemical means. Production Variables The innovative production apparatus, has a maximum extrusion capability of one litre per hour from both the precursor reservoirs, giving a theoretical annual production capacity of 250kg of bicomponent fibre, an excellent rate for a laboratory scale machine. With industrial modifications, such as multiple extrusion nozzles and larger pumps, the process could produce the fibres at a phenomenal rate. Fibres with a 7-14 µm core and a 1-2 µm sheath can be produced at speeds of up to 200-300 metres per minute using the laboratory machine, figure 1. The final diameter and speed of extrusion are controlled by several factors: • The molecular weight of the initial polymer and the minimum level of solvent which allows filament formation. • The core/sheath spinerette ratio, and the ratio of the wall thickness of the core spinerette to the total diameter of the spinerette orifice. • The draw down ratio, or the reduction in diameter due to extrusion required to extract enough solvent to allow solid filament formation. • The uniformity of the polymer crystal size. • The length of the chamber, and the direction of gas flow. 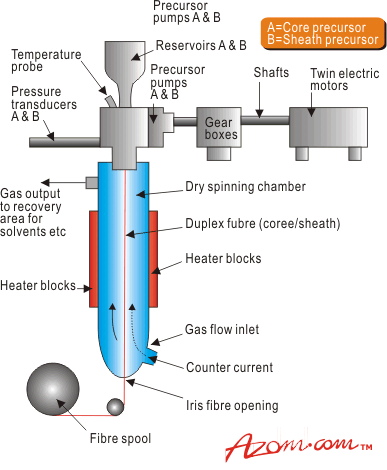 | Figure 1. Bicomponent extrusion using the monomeric precursors a and b. | The control of the pyrolysis regime is also of importance to the final product, and in particular the factors of time, temperature and atmospheric gases. Contained within the patents for the bicomponent extrusion process are methods to control stoichiometry, and to control pyrolysis speed to match extrusion output, allowing a continuous process, rather than the batch processes currently used. Advantages of Bicomponent Extrusion The bicomponent process, by generating ceramic fibres with a core-sheath structure, can eliminate many problems experienced when using monolithic ceramic fibres in composite materials. The sheath can act as an interfacial barrier, preventing reaction between the core and the metal matrix in metal matrix composites, for example, and allowing the production of a wide variety of systems, table 1. Other advantages include: • Reduced costs due to one-pass processing • Tailored properties for individual applications • Enhanced strength through lower oxygen content. Table 1. Metal and ceramic matrix composites incorporating ceramic fibres produced by the bicomponent extrusion process. | Silica/Al2O3 | C/BN | Al | SiC | TiB2 | Al/Ti | SiC | C | Mg | SiC | C | SiC | SiC | BN | Polymeric B-SiC | TiN | BN | C | Yttrium- Al2O3 | C/BN/PSZ | Al2O3 | SiC | BN | C | Present and Future Applications The market for ceramic fibres looks set to grow as the range of properties expands. They are already used, in metal matrix composites, in machine tools for improved wear resistance, in sports goods for their stiffness, and in jet engine components and automobile components to reduce the weight and improve fuel efficiency, and bicomponent types could be used to produce ceramic fibre reinforced diesel engine pistons by gravity die casting. Future applications of ceramic matrix composites are also numerous, and include reducing the weight and therefore the launch costs of satellites, heat shields for space planes, rocket engine components, advanced organic matrix composite tooling (removing the need for stainless steel moulds), high precision machine tools, body armour and military hardware applications, biomedical implants, and biomimetics. The uses for ceramic fibres are currently limited by the temperature at which they can operate, but this is expected to rise in the future as newly designed fibres such as the bicomponent types are exploited. Another area of research interest may be increasing the tensile strength from the current value of 3GNm-2 to 9GNm-2, although the theoretical maximum of 27GNm-2 is unlikely to be achieved! Other ceramic fibre formulations are also under consideration, with titanium silicide showing promise. |