Updated by Reginald Davey 03/03/2023
Acrylic resins include thermoset or thermoplastics obtained from methacrylic acid, acrylic acid, or other related compounds. These resins are extensively used in devices such as mobile telephones, television screens, furniture, as well as in domestic paints.
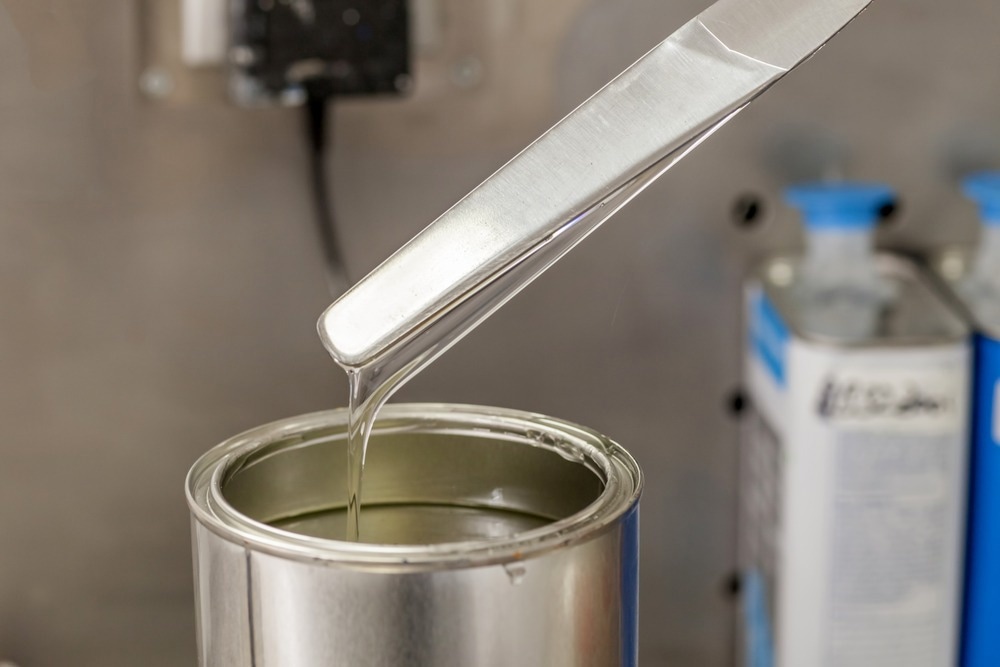
Image Credit: Aykut Erdogdu/Shutterstock.com
Acrylic resins are economical, effective, and transparent materials. At room temperature, these plastics are ductile and are derived from products such as acrylic acid obtained from polypropylene, which is a by-product of oil refining.
It can be seen, therefore, that acrylic resins are commercially important materials which are used in a multitude of applications in sectors such as the electronics industry and in several domestic products. Acrylic recyclability has become a key concern in several industries as they transition to a circular model of production.
An emulsified form of acrylic resin is polymethyl acrylate (PMA), which is used for textile finishes and lacquer and can be mixed with clay and adhesives to gloss paper. Polymethyl methacrylate (PMMA) is used to make hard plastics with a range of light-transmitting properties.
This article will explore acrylic resin, looking at properties, manufacturing processes, and will ask the question: is acrylic recyclable? Additionally, the article will explore the applications of recycled acrylic and acrylic resins.
Types of Acrylic Resin
Acrylic resins are a family of thermoplastic materials that are produced by the polymerization or co-polymerization of vinyl monomers. These materials incorporate nitrile or carbonyl groups. Several types of acrylic resin have been developed since the 19th century under various commercial trademarks.
Poly(methyl acrylate) (PMA)
A tough, flexible material softer than PMMA, with a low glass-transition temperature of around 10oC.
Molecular formula - (C5O2H8)n
Density - 1.18 g/cm3
Melting Point – 160°C (320°F)
IUPAC ID - Poly(methyl 2-methylpropenoate)
Poly (methyl methylacrylate) (PMMA)
A transparent thermoplastic, PMMA is also known as acrylic glass. Aside from its use as an acrylic resin, PMMA can be used as a shatter-proof, lightweight alternative to traditional glass. Harder than PMA.
Molecular Formula - (C4H6O2)n
Density - 1.22 g/cm3
Glass transition temperature – 6°C (43°F)
Chemical and Physical Properties of Acrylic Resins
Acrylics are transparent plastics and are therefore superior light transmitters. This optical clarity also means that they can be colored easily. It is possible to find these transparent thermoplastics in all shades, including fluorescents.
Acrylic resins have excellent surface luster. These materials are hard and have some impact resistance in spite of their low softening point. They also feature high scratch resistance and low moisture absorption properties.
Cleaning fluids and gasoline may damage acrylic; however, due to limited chemical resistance, household alkalies and non-oxidizing acids do not impact them.
One of the most commonly used acrylic resins is PMMA, and its wide range of properties are detailed below:
- PMMA features unique optical properties. It has high transparency of around 92% light transmission in the visible range from 380 to 780 nm. On an inner surface, the angle of total reflection is 41 to 42°, hence enabling its use in fiber optic filament, light conductors, etc.
- The vitreous transition temperature of PMMA is from 110 to 135 °C. It is an uncrystallized polymer and is rigid, hard, and brittle at ambient temperature, and has a low shock resistance
- PMMA is hygroscopic, and under extreme conditions, the absorbed water acts as a plasticizer that will change the material properties. It has a fairly limited creep
- At high critical stress in PMMA, crazing may occur. PMMA is considerably scratch-resistant and can be polished easily
- PMMA is odorless, tasteless, and can be used in contact with food
- The electrical properties can be impacted sharply by humidity absorption. Arcing resistance is high
- PMMA is combustible and burns without the production of a high amount of smoke. When molded, its retraction is less. Since its coefficient of linear expansion differs from that of metals and it has a very low elasticity, metal inserts should not be used in an injected PMMA component
- The maximum operating temperature is less than 80° C
- PMMA can be used for silk screening and vacuum-applied metallization
Another key acrylic resin is PMA and its properties are detailed below:
- PMA has a refractive index of 1.479
- PMA features good flexibility and adhesion
- It has an elongation of up to 750%
- Its tensile strength is 6.9MPa
- PMA is usually soluble in acetone, ethyl acetate, dichloroethane, xylene, etc.
- PMA cannot be dissolved in saturated hydrocarbons, ethanol, carbon tetrachloride, toluene, etc.
More from AZoM: How Can Polymer Strips Be Used to Clean Up Oil Spills?
Manufacturing Process of Acrylic Resins
Acrylate monomers (for example, methyl methacrylate) are made to react with a catalyst during the production of acrylic resins. Organic peroxide is a typical catalyst used in the manufacture of acrylic resins. Three forms of acrylic plastics are available, including elongated shapes such as tubes and rods, flat sheets, and powder.
A technique called suspension polymerization is used to make molding powders wherein the reaction occurs between tiny monomer droplets suspended in a solution of catalyst and water. Grains of polymer are formed that have a strictly controlled molecular weight suitable for extrusion or molding.
Bulk polymerization is used to form acrylic sheets. Here, the catalyst and the monomer are poured into a mold in which the reaction is taking place. There are two types of bulk polymerization, which are continuous and batch cell.
Batch cell processes are very common as they are simple and can be used to make sheets of thickness 0.06 to 6 inches and widths from 3 ft to several hundred feet. Rods and tubes can be produced using the batch cell method.
Continuous batch cell processes are rapid and involve less labor. It is possible to make thin acrylic plastic sheets with small widths using the batch cell method.
Applications of Acrylic Resins
Acrylic resin is used in a variety of applications, including:
- Used as the sole resin or an additive in solvent-based adhesives and water-borne coating systems
- Used as watch crystals, optical lenses, aircraft windshields, outdoor signs, and skylights
- PMMA can be cast to resemble marble. It is also used to make sinks, countertops, and other fixtures
- Useful in clothing, blankets, carpets made from acrylic fibers, adhesives, contact lenses, dentures, floor waxes, food preparation equipment, disposable diapers, sanitary napkins, and paints
- Acrylics can be used as a lens material. Also, they find applications in cameras, binoculars, and eyeglasses. They are also used in car headlights and stop lights. Acrylic plastics are used in dishes, lighting fixtures, carpets, floor waxes, piano keys, skylights, and beverage dispensers
Environmental Impacts of Acrylic Resin
The key cause of environmental problems due to acrylic plastics is that consumers do not dispose of them properly. Plastic usage has helped develop a large number of disposable products that have increased the amount of waste.
Nearly 25% of waste in landfills is comprised of plastics. Acrylics or most plastics degrade very slowly and enter the ocean and coastal ecosystems, posing a threat to birds and marine creatures as well as entering the food production chain.
Acrylic is obtained from fossil fuel and petroleum products that are not sustainable. It is possible to recycle certain forms of acrylic, but not all. In typical usage conditions, off-gassing of acrylic does not occur and environmentally it functions just like glass.
Many researchers are currently asking the question: is acrylic recyclable? Overcoming this key challenge associated with their use will significantly reduce the impact of these plastics, the products that include them, and the plastics industry as a whole.
Is Acrylic Recyclable?
Acrylic plastic is not easily recyclable. Among recycled plastics, it is considered a Group 7 plastic and mostly not collected for recycling.
It is possible to form large pieces into useful objects in cases where they have not suffered crazing, stress, or cracking. However, these are not readily biodegradable. Some are highly flammable and must be protected from combustion sources.
PMMA, the key type of acrylic, can be recycled in several ways. This normally involves subjecting the resin to pyrolysis. It is possible to recover the monomer from PMMA scrap by depolymerization. PMMA has been successfully depolymerized by contacting with molten lead, resulting in MMA with a purity of more than 98%.
From an environmental perspective, the use of lead is undesirable since it is very difficult to remove and cannot be reused. As a result, new recycling and reuse methods for acrylics are being devised.
Applications of Recycled Acrylic
Recycled acrylic PMMA sheets are used in the following applications:
- Construction: soundproof windows and doors, windows, mining masks, and telephone booths
- Medical: baby incubators, a specific variety of surgical medical devices
- Public goods: handicrafts, sanitary facilities, cosmetics, frames
- Surfaces of instrument panels and covers
- Lighting: fluorescent lamps, chandeliers, street lamp
- Signs, light boxes, signage, exhibition
- Transport: cars, trains, and other vehicles, doors, and windows
In Summary
Acrylic resins find widespread application in industries due to their good physical, thermal, and chemical properties. However, the question of their recyclability is a key topic of research currently, as these plastics have a deleterious impact on the environment. Novel technological solutions are needed to overcome this challenge.
More from AZoM: Restoring Old Art Works by Removing Deleterious Acrylic Resins Applied by other Restorers