Rotational moulding, or roto moulding, is the method of choice for producing many of the hollow plastic products that we use in everyday life and is in fact one of the fastest-growing sectors of the plastics industry over the last decade.
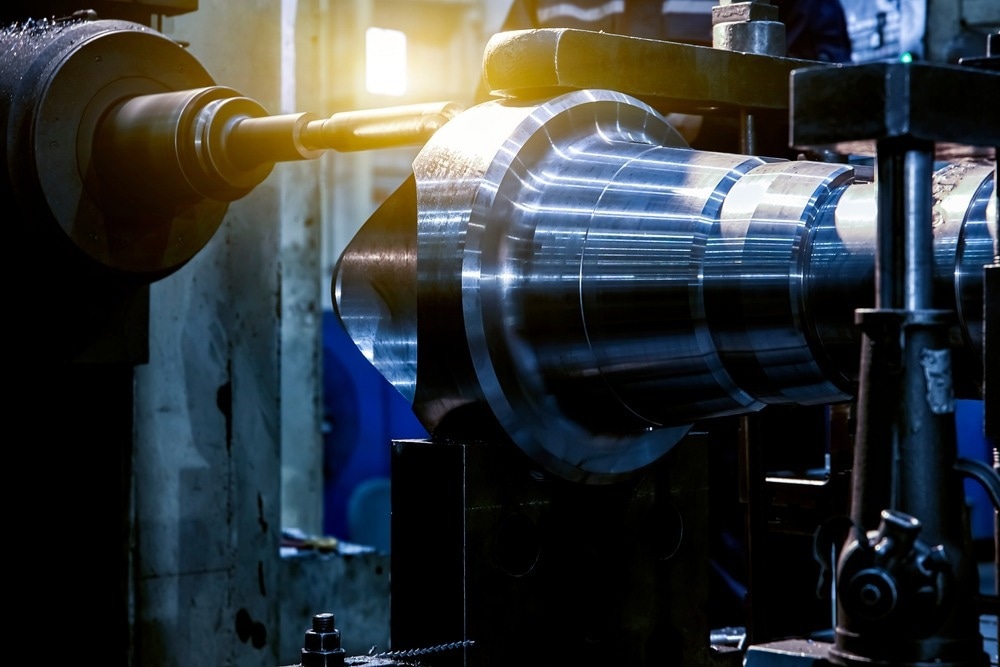
Image Credit: Jenson/Shutterstock.com
Unlike other processing methods the heating, melting, shaping, and cooling phases of rotational moulding happen after the polymer is placed in the mould, meaning no external pressure is required during forming.
The moulds themselves are generally made from cast aluminium, CNC machined aluminium, or steel, and can be relatively cheap when compared to moulds used in other methods such as injection or blow moulding.
The rotational moulding process is relatively simple but extremely versatile. Firstly, the mould cavity is loaded with a powdered polymer (which is discussed in the section below).
The oven is then heated to around 300°C (572°F), as the mould rotates on two axes to evenly distribute the polymer. The basic principle is that the powder particles (normally around 150-500 microns) will fuse together to create the continuous finished product. How the product eventually turns out is crucially based on the size of the powder particles.
Finally, the mould is cooled and the product is extracted for finishing. The cycle time of a basic roto moulding process can vary from 20 min to 1h, depending on the size and the complexity of the product.
Here, you can see how the Air Flow Oven Rotational Moulding Machine works:
Here you can see how works the Air Flow Oven of Rotational Molding Machine
Video Credit: Rotoline Rotomolding/Youtube.com
Typical Plastics Used and Products Produced
Various types of plastic polymers can be used in rotational moulding, depending on the desired end product.
A commonly used plastic is polyethylene (PE), as it is able to withstand elevated temperatures for prolonged periods of time and is fairly inexpensive. Furthermore, low-density PE is very flexible and resistant to fracturing.
The density ranges of PE that are used are as follows:
- Low-density PE - 915-929 kg/m3
- Medium-density PE - 930-939 kg/m3
- High-density PE - 940-965 kg/m3
Moulders also commonly use ethylene-butyl acrylate, as this material is crack resistant and strong at low temperatures. As with most thermoplastics, it has the added advantage of being easily recyclable.
More from AZoM: Thermal Analysis Methods Applied to Polyethylene
The other plastics that are typically used in rotational moulding are listed below:
- Nylon
- Plastisols
- Polycarbonate
- Elastomers
- Ethylene vinyl acetate
- Polyurethane
- Polyvinyl chloride
- Polypropylene
Polypropylene, although a plastic that is widely used, is not the preferred choice of many moulders. The reason is that at close to room temperature this material becomes brittle, thus giving manufacturers very little time to mould the product.
Many everyday products are produced using the rotational moulding method, as are more bespoke creations. Some examples are given below:
- Manhole inspection chambers
- Rainwater tanks and diesel fuel tanks
- Children’s playhouses, slides, climbing frames, toys and leisure crafts
- Traffic cones
- Dinghies, canoes and kayaks
- Pallets, garden planters, and water butts
- Complex medical products
- Domestic oil storage tank and oil recovery bank
- Steering wheels
Advantages of Rotational Moulding
Rotational moulding is a very effective moulding method that allows manufacturers not only to produce extremely durable products with minimum design constraints but also to produce them at comparatively low costs in an environmentally-friendly manner. Furthermore, large products can be easily manufactured in an economic manner with very little material wasted.
Rotational moulding is quick to set up, thereby making it possible for small batch production to meet unpredictable demand. It helps to minimize stock holding and potential redundancy of stock making it overall comparatively cheap compared to fabricating, fibre glass, injection, vacuum or blow moulding methods.
The versatility of rotational moulding is also one of its major assets. It enables products to be created without polymer weld lines, with multiple layers and a variety of styles, colours and surface finishes. Roto moulding can accommodate not just inserts but also logos, recesses, spouts, bosses, and many more features to fulfil the demanding design and engineering requirements. Additionally, different types of products can be moulded together on a single machine using this method.
Apart from the above, it has the following advantages:
- Stress-free products
- Weather-resistant end products
- Fast manufacturing times
- Even wall thickness and leak-proof reliability
- High impact resistance and good load-bearing properties
Companies Involved in Rotational Moulding
The following are the major companies involved in rotational moulding:
- Etills ltd located in Cambridgeshire, UK creates a wide range of products using rotational moulding
- Rotadyne, located in New South Wales, Australia, has been a leader in the field of plastic rotational moulding since 1973. Their services include product design and development, tooling, laser trimming, assembly, foam filling, elaborate quality controls, and mould-in graphics
- Rotational Mouldings Ltd is one of the leading manufacturers of rotationally moulded products in the UK and Europe. They serve a wide variety of industry sectors including offshore buoyancy, traffic management, water treatment, construction, street furniture, agricultural, toys, playground equipment, sewage treatment, medical and hygiene
- Amber Plastics is a roto moulding manufacturer and supplier located in Derbyshire, UK. Their products include complete finished products including bins, boxes, water carriers, planters and street furniture, and sub-assemblies or components of larger products.
- JFC are manufacturers of rotationally moulded products up to 2.5 m in length. They are located in Cheshire, UK
- Rototek is a high-quality trade rotational moulder company located in Nottinghamshire, UK.
- Corilla Plastics is a rotational moulder company located in Mid Glamorgan, UK
Applications of Rotational Moulding
Rotational moulding finds applications in the following sectors:
- Automotive industry
- Agricultural industry
- Furniture industry
- General industry such as lighting solutions, namely, ovoids, bollards, double cones, lamp covers, spheres, and cubes
- Packaging industry such as stackable containers, pallets, and tanks
- Sports and leisure industry
- Water treatment industry
- Marina offshore buoyancy and marine safety equipment industries- e.g. navigation aids, mooring and marker buoys, boom floats, SOLAS-approved lifebuoys, fuel tanks, and net floats
- Construction industry
Disclaimer: The views expressed here are those of the author expressed in their private capacity and do not necessarily represent the views of AZoM.com Limited T/A AZoNetwork the owner and operator of this website. This disclaimer forms part of the Terms and conditions of use of this website.