Ultra-high molecular weight polyethylene (UHMWPE) has been the material of choice for the wear surface (against metallic or ceramic counterfaces) of total joint replacements for the past three decades. The life of these components is considered to be related to the wear performance of the UHMWPE used and the method of sterilisation. Sterilisation by Gamma Radiation Gamma irradiation has been the most common method of sterilisation but results in the formation of free-radicals, rendering the UHMWPE unstable. Oxygen can diffuse into the polymer over time, reacting with the free-radicals present and causing chain scission (a reduction in polymer molecular weight). This is accompanied by internal cross-linking reactions, with the overall result being a change in physical properties of the polymer resulting in a change in wear performance. Generally chain scission is considered to detrimental to wear performance whereas cross-linking is thought to be beneficial. A high wear rate results in a high generation of wear debris (figure 1). This enters the bone-joint interface and produces an inflammatory response. This has been linked to bone lysis which leads to loosening of the component itself (aseptic loosening). Revision surgery is normally the only option at this stage, but this is a costly and inconvenient operation. Methodologies are therefore required which can rapidly evaluate and compare any newly developed material processing or sterilisation technology. This would ensure early identification of the most effective processing and sterilisation combinations which would, in the long term, lead to a reduction in the requirement for revision surgery. 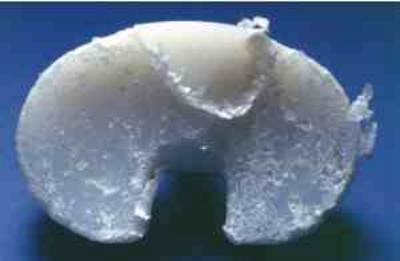 | Figure 1. Example of wear debris from an UHMWPE implant. | Accelerating Ageing to Date Despite the intensive focus on ageing methodologies for UHMWPE over the last few years there remains much debate over the most effective way of accelerated ageing this material to simulate both shelf and in-vivo ageing. Work is currently underway at The Queen’s University of Belfast to develop a widely acceptable methodology for the accelerated ageing of UHMWPE. Within the scope of this methodology polymer characterisation techniques are being proposed which, where possible, are based on existing standards and which have the potential to become widely adopted by industry. This work is funded by the UK Department of Trade and Industry. The oxidation of UHMWPE is in reality a complex sequence of various cascade reactions which is not fully understood. The main bone of contention concerns why maximum oxidation (region of embrittlement) often occurs 1-2 mm below the surface of UHMWPE components and not on the surface where exposure to oxidising species should be highest. Perhaps the most convincing explanation for the formation of subsurface maximum in oxidation comes from the work of Yeom et al. [1], who describe the cascade of events occurring at various depths within gamma irradiated UHMWPE. At the surface of the UHMWPE the O2 concentration is highest and most primary alkyl radicals (-CH2. .CH2-) and secondary alkyl radicals (-CH2-CH.-) produced by gamma irradiation will react to form peroxy radicals (-CH-O-O. or >CH-O-O., respectively). Other secondary alkyl radicals can combine to form crosslinks. A large concentration of peroxy radicals exist at the surface and these can combine to from ketones, a reaction which does not produce any further free radicals i.e. the end of the cascade. In the subsurface region, on the other hand, fewer peroxy radicals form, due to the lower O2 concentration in this region. Because these peroxy radicals will be further apart there will be a lesser tendency to react with each other and greater tendency to abstract H atoms from the polyethylene chains, thereby forming hydroperoxides and new free radicals. This initiates a cascade of reactions which forms carbonyl groups, chain scission and further free radicals. As oxygen diffuses into the UHMWPE, further reaction with the newly created free radicals can occur, eventually leading to higher levels of oxidation in this subsurface region compared with the surface. Deeper into the UHMWPE there will be less oxygen available for reaction so most of the radicals will combine to produce crosslinks. Accelerated Ageing Protocol An accelerated ageing test for the evaluation of gamma sterilisation on the performance of medical grade UHMWPE was originally proposed by Sun et al. [2] The recommended conditions for accelerated ageing were a heating rate of 0.6°C/min to 80°C for either 11 or 23 days. This was considered to be equivalent to 4 to 6 or 7 to 9 years of shelf ageing, respectively. Further work by Sun et al. [3] suggests that either a surface or subsurface peak in oxidation can be achieved depending on the time period between gamma sterilisation and accelerated ageing. An alternative accelerated ageing method has been proposed by Sanford et al. [4] This involves use of a pressurised vessel. Using this technique, with a pressure of 5 atmospheres oxygen and temperature of 70°C, 5 to 10 years of shelf ageing could be simulated in as little as one week. The technique also produces the subsurface oxidation maximum which is often observed for shelf aged components. An ASTM standard for accelerated ageing of UHMWPE has recently been published (ASTM F2003-00). It incorporates both method A (21 days at 80°C in air) and method B (14 days at 70°C in 5 bar oxygen). However, interlaboratory studies have identified that, although materials can be ranked successfully by both these methods, there is poor interlaboratory reproducibility (especially for method B) [5]. Characterisation Techniques Oxidation Index by FTIR Oxidation is perhaps the most popular current method for assessing damage to UHMWPE following gamma sterilisation and ageing. Unfortunately, a wide range of differing techniques have been developed and therefore it is often difficult to compare results between various workers. The term ‘Oxidation Index’ is often used but an ASTM standard addressing the definition of this has only recently been drafted. It refers to comparison of the peak or peaks in the FTIR spectra in the region 1650-1850 cm-1 (corresponding to carbonyl C=O groups) and a reference peak which is independent of specimen degradation. Different workers have, in the past, used different reference peaks and, to complicate matters further, some workers choose to use peak areas and others peak heights. A ‘Round Robin’ investigation of oxidation index measurement protocol has recently been completed. Feedback from participating institutes would seem to indicate that reproducibility can be optimised by defining the Oxidation Index (OI) as the peak area at 1650-1850 cm-1 divided by the peak area at 1370 cm-1. This gives an overall relative uncertainty of 10-20% [6]. Density Determination Density depth profiles through UHMWPE are obtained using a density gradient column containing two liquids (e.g. water and ethanol) and essentially provide the same information with regard to extent of oxidation as FTIR. Density has been shown to correlate well with oxidation index [7]. The advantages of this method are that results are directly comparable between workers, capital outlay for equipment is low compared with FTIR and results are obtained relatively quickly. Other factors may also influence density, such as starting material and processing conditions. This is another technique where methods vary widely between workers making results difficult to compare. It is important to understand the balance that occurs between chain scission due to oxidation and internal crosslinking reactions in gamma sterilised UHMWPE. In terms of wear performance oxidation is considered to have a detrimental effect whereas crosslinking is considered beneficial [8]. The majority of methods for measurement of crosslink density have been modified from ASTM2765-90 or ASTM2765-95 (method C) and involve immersing samples in hot xylene. If crosslinking occurs within UHMWPE a 3-dimensional gel phase is formed. The non-crosslinked portion of the UHMWPE (the sol phase) can be dissolved in hot xylene, leaving the gel phase, from which the crosslink density can be determined. The main reason from modification of the ASTM standard is the need to use a small sample size to achieve adequate information on variation of crosslink density with depth into the sample. The drawback of using small samples is that, although the gel content can be measured with reasonable accuracy, errors may be high when determining the ‘swell ratio’ of the UHMWPE. A new series of round robins at ASTM F04 to quantify interlaboratory reproducibility of crosslinking measurements in UHMWPE are currently planned. The first study will compare the reproducibility of gravimetric and volumetric methods for measuring swell ratio in six UHMWPE materials that have been gamma irradiated in nitrogen. Mechanical Testing Kurtz et al.[6, 9, 10] have proposed a method for determining the biaxial tensile properties of UHMWPE using relatively small specimen sizes. The rational behind this is that standard uniaxial tensile tests do not adequately relate to properties affecting UHMWPE wear performance. During uniaxial plastic deformation the UHMWPE molecules orient parallel to the loading direction, resulting in ‘strain softening’ in the transverse direction. Wear, on the other hand, has been associated with localised deformations under multiaxial loading conditions. This technique consists of a ‘punch test’ which loads the polymer biaxially and has been found to result in up to 58% lower effective true stress values when compared to uniaxial loading conditions. The punch assembly can be fitted to a standard tensile testing machine and the relatively small sample size (6.4 mm dia. x 0.5 mm thick) offers the potential to depth profile the mechanical behaviour of UHMWPE and assess mechanical performance of retrieved UHMWPE from joint replacments. Material and Process Developments Bulk Processing Variables Ram extrusion and compression moulding are the two most common methods of consolidating UHMWPE resin particles. The resistance to oxidation of the processed material would seem to be influenced by two main factors, firstly the degree of consolidation and, secondly, whether calcium stearate is present in the UHMWPE resin. The results of Afflitto et al.[11] on resistance to oxidation have shown ram extruded UHMWPE to have inferior oxidation resistance to compression moulded UHMWPE following identical gamma sterilisation and accelerated ageing treatments. This was linked to higher consolidation of the compression moulded UHMWPE material. Duus et al.[12] have shown that consolidation and final UHMWPE properties are more dependant on the processing parameters employed than the actual processing route. They have shown that by careful selection of process parameters mechanical properties of UHMWPE can be optimised. Direct Moulded UHMWPE Net shape (or direct) compression moulding of UHMWPE is an alternative manufacturing process for components such as tibial bearings. Compared with bulk compression methods, no machining of the bearing surface is required. Both Gael et al. [13] and Ranard et al. [14] have observed that such components have an unusually high resistance to oxidation, following gamma irradiation and shelf ageing. Suggested causes for this were considered to be type of resin (1900H), absence of calcium stearate, temperature of consolidation and effects of machining of the bulk material. Free radicals are found to be present in these components after gamma irradiation and 3 months of shelf ageing, but following 17 months of shelf ageing the free radical concentration decreases significantly. This indicates that the material must have a very low oxygen permeability, since no oxidation occurs, even in the presence of free radicals [13]. Presumably the free radicals are consumed by internal crosslinking reactions. This may actually enhance wear resistance of the components. Crosslinking and Stabilisation Treatments Crosslinking has been shown to be an effective way of improving the wear resistance of UHMWPE as shown by hip simulator tests for both rough and smooth metallic counterfaces [15]. Crosslinking is achieved either by gamma or electron beam irradiation under inert conditions, followed by a heat treatment either above [16, 17] or below [15] the UHMWPE melting point. Thus free radicals are formed by irradiation and react when heated to produce crosslinks. Alternatively chemical crosslinking can be achieved by addition of a peroxide to the UHMWPE resin prior to moulding and irradiation. These techniques are also effective in improving the oxidation resistance of UHMWPE as free radicals, which are produced during the irradiation processes, are generally consumed by the crosslinking reactions and therefore unavailable for reaction with oxygen. Conclusions It is clear that accelerated ageing of UHMWPE can be achieved by a number of protocols, based on either elevated temperature alone, or elevated temperature combined with elevated pressure in oxygen. With regard to comparison of materials and sterilisation processes any of these techniques would seem appropriate if performance is to be ranked merely by oxidation resistance (measured by density change or oxidation index). Therefore either of the two methods proposed by the ASTM would be appropriate. It would seem sensible, however, to include a standard reference material as a control, to be sterilised and aged under identical conditions. Evidence in the literature suggests that care must be taken to ensure that test materials are always treated in a similar manner prior to and during accelerated ageing. If wear testing is to be conducted following accelerated ageing then ageing parameters need more careful control. Wear performance may be effected by the location of the oxidation maximum (i.e. whether on the surface or subsurface). In this case accelerated ageing needs to be capable of producing the same oxidation depth profile as observed for shelf ageing. This is difficult because the exact depth profile for shelf ageing of a new material or process is unknown. Accelerating ageing protocol will need to be based on well characterised materials where data for shelf ageing exists. It is a matter of not only simulating the oxidation of the UHMWPE, but also the level of internal crosslinking, since both are understood to effect wear performance. Further work is ongoing in this area to establish factors which control the depth of maximum oxidation and the balance between oxidation and crosslinking for accelerated ageing compared with shelf ageing. In terms of characterisation protocols both density and oxidation index are measurement techniques where standardisation of methodologies are gradually being adopted. Standardisation of the measurement technique for crosslink density still needs attention. It would seem important to adopt a technique which is capable of assessing the variation in crosslink density with depth into the sample. 1. Yeom, B., Yu, Y.-J., McKellop, H.A. and Salovey, R., Profile of oxidation in irradiated polyethylene. Journal of Polymer Science: Part A: Polymer Chemistry, 1998. 36: p. 329-339. 2. Sun, D.C., Stark, C. and Dumbleton, J.H., Development of an accelerated aging method for evaluation of long term irradiation effects on UHMWPE, in ACS Symposium Series, Irradiation of Polymers. 1996, American Chemical Society. p. 340-349. 3. Sun, D.C., Schmidig, G., Stark, C. and Dumbleton, J.H. A Simple Accelerated Ageing Method for Long Term Post-Radiation Effects in UHMWPE Implants. in 42nd Annual Meeting, Orthopaedic Research Society. 1996. Atlanta, Georgia, Feb 19-22,p. 493. 4. Sanford, W.M. and Saum, K.A. Accelerated oxidative ageing testing of UHMWPE. in 41st Annual Meeting, Orthopaedic Research Society. 1995. Orlando, Florida,13-16 February, p. 119-20. 5. Kurtz, S.M., Muratoglu, O., Mounib, L., et al. Interinstitutional reproducibility of standard accelerated ageing methods for UHMWPE. in 46th Annual Meeting of the Orthopaedic Research Society. 2000. Orlando, FL, USA, March 12-15. 6. Kurtz, S.M., Muratoglu, O., Mounib, L., et al. Confirmed interlaboratory studies of a standard method for determining the oxidation index of UHMWPE. in 31st International Biomaterials Symposium. 1999. Providence, RI, USA, April 28-May 2,p. 46. 7. Furman, B.D., Lelas, J., Walsh, H., et al. Kinetics, Chemistry and Calibration of UHMWPE Accelerated Aging Methods. in 24th Annual Meeting of the Society for Biomaterials. 1998. San Diego, CA: Socitey for Biomaterials, April 22-26,p. 154. 8. Essner, A., Polineni, V.K., Wang, A., Stark, C. and Dumbleton, J.H. The Effect of Femoral Head Surface Roughness and Crosslinking on the Wear of UHMWPE Acetabular Inserts. in 24th Annual Meeting of the Society for Biomaterials. 1998. San Diego, CA, April 22-26,p. 4. 9. Kurtz, S.M., Foulds, J.R., Jewett, C.W., Srivastav, S. and Edidin, A.A., Validation of a small punch testing technique to characterise the mechanical behaviour of UHMWPE. Biomaterials, 1997. 18(24): p. 1659-1663. 10. Kurtz, S.M., Rimnac, C.M., Pruitt, L.A., Jewett, C.W., Goldberg, V. and Edidin, A.A., The relationship between clinical performance and large deformation mechanical behaviour of retrieved UHMWPE tibial inserts. Biomaterials, 2000. 21: p. 283-291. 11. Afflitto, R.M., Poggie, R.A., Cohen, R.C. and Averill, R.G. Comparison of the oxidation resistance of three different types of polyethylene. in 24th Annual Meeting of the Society for Biomaterials. 1998. San Diego, CA, April 22-26,p. 157. 12. Duus, L.C., Santner, T.J., Williams, B.J. and Li, S. Controlling the physical properties of molded UHMWPE through predictable interaction between processing variables. in 24th Annual Meeting of the Society for Biomaterials. 1998. San Diego, CA, April 22-26,p. 152. 13. Gsell, R. and Lin, S. Improved resistance to oxidative degradation of 1900H net-shape compression molded components. in 24th Annual Meeting of the Society for Biomaterials. 1998. San Diego, CA, April 22-26,p. 123. 14. Ranard, G., Higgins, J. and Schroeder, D. Density and thermal analysis of molded and machined UHMWPE tibial bearings. in 24th Annual Meeting of the Society for Biomaterials. 1998. San Diego, CA, April 22-26,p. 497. 15. Essner, A., Polineni, V.K., Wang, A., Stark, C. and Dumbleton, J.H. Effect of femoral head surface roughness and crosslinking on the wear of UHMWPE acetabular inserts. in 24th Annual Meeting of the Society for Biomaterials. 1998. San Diego, CA, April 22-26,p. 4. 16. Shen, F.-W., McKellop, H. and Salvey, R. Improving the resistance to wear and oxidation of acetabular cups of UHMWPE by gamma radiation crosslinking and remelting. in 24th Annual Meeting of the Society for Biomaterials. 1998. San Diego, CA, April 22-26,p. 3. 17. Bragdon, C.R., O'Connor, D.O., Muratoglu, O.K., et al. A new polyethylene with undetectable wear at 12 million cycles. in 24th Annual Meeting of the Society for Biomaterials. 1998. San Diego, CA, April 22-26,p. 2. |