No one likes handling unpleasant or dangerous materials, such as toxic herbicides, hospital infected laundry, or biohazard materials. Dust producing powders such as dyes and pigments particularly equally unpleasant. But at some point all these things have to be removed from their packaging which is why a new PVOH material is generating such a deal of interest. Environmental Polymers Group Plc (EPG) has recently developed a breakthrough proprietary technology that provides a family of biodegradable poly(vinyl alcohol) (PVOH)-based thermoplastics with outstanding versatility, processing and physical properties, containing no toxic additives. This has been achieved at lower cost than most other biodegradable plastics. These products represent a viable biodegradable alternative to present non degradable materials for a variety of applications. Poly(vinyl alcohol) Poly(vinyl alcohol) has been available since around 1924, when its synthesis via the saponification of poly(vinyl acetate) was first described by Herman and Haehnel. In the early years, the principal application for PVOH was in textile sizing. Today, much of the PVOH produced is used as a protective colloid in the manufacture of polymer emulsions. It is also found in many other applications, including the binding of pigments and fibres, dip coated articles, protective strippable coatings, the production of detergents and cleansing agents, adhesives, emulsion paints and solution cast film. All of these applications involve the use of the polymer in solution, since the thermal degradation characteristics of PVOH limit its ability to be used as a conventional thermoplastic. Unplasticised PVOH thermally degrades at temperatures of about 150°C, with the release of water and the formation of conjugated double bonds. As the crystalline melting point of PVOH ranges from 180°C to 240°C, its use as a thermoplastic, processable on conventional thermoplastic processing equipment, is limited unless it can be plasticised to such an extent that thermal dehydration is avoided. In practice, the amount of plasticiser necessary to achieve this is so high that many of the useful properties of PVOH are sacrificed. EPG Poly(vinyl alcohol) The novel process developed by EPG represents a highly significant technological advance. Expensive solution casting has previously been necessary to make high performance PVOH films. In contrast, the EPG extrusion technology produces materials with equivalent or greater multi dimensional strength to solution cast PVOH, but using an economical melt extrusion process that doesn't degrade the PVOH, and without the need for heavy plasticisation. The materials made by EPG have high tensile and tear strengths (superior to polyethylene and plasticised PVC). Table 1 shows some typical properties of EPG PVOH films compared with films made from various other polymers. The outstanding physical properties of the EPG films result from the high degree of crystallinity of the PVOH, which is typically 40-50%, and from the ability of adjacent molecules to hydrogen bond with each other. The representative space filled model structure of PVOH, shows the extensive hydrogen bonding capability of the PVOH molecules. Table 1. Typical properties of PVOH films compared to other traditional film materials. | | | | | | | Clarity (light transmitted) (%) | | 60-66 | 58-66 | 48-58 | 54-58 | Gloss (light reflected) (%) | | 81.5 | 60 | 79.5 | 22 | Water vapour Transmission In 24hrs, 30µm thick | A | 788 | 1340 | 148 | 21 | A=0% r.h, B=90% r.h, at 40°C | B | 1500-2000 | 1300-2000 | 120-180 | 35-180 | Tear strength (Elmendorf) (N.mm-1) | | 147-834 | 2-4 | 39-78 | 29-98 | Tensile strength (MN.m-2) | | 44-64 | 55-131 | 20-76 | 17-19 | Elongation at break (%) | | 150-400 | - | 5-250 | 50-600 | | Structure However, the structure of PVOH is far from ideal. PVOH is produced from the saponification of polyvinyl acetate and depending on the degree of saponification (i.e. the degree of hydrolysis of the PVOH), a variety of PVOH materials may be produced, ranging from partially hydrolysed to fully hydrolysed grades. Also, the majority of commercially available grades of PVOH are atactic and contain significant proportions of syndiotactic diads. The high levels of crystallinity in PVOH result from the relatively small size of the hydroxyl groups, which enable it to assume both d and 1 positions in an atactic chain within a single crystal lattice. Physical Properties The physical properties of PVOH, such as the strength, water solubility, gas permeability and thermal characteristics vary with the degree of crystallinity, which is heavily dependent on the degree of hydrolysis and the average molecular weight of the polymer. The actual amount of crystalline material present in compounded PVOH is further dependent on the amount of plasticiser and/or water incorporated into the compound, the production process (acid or base catalysed), the degree of hydrolysis and the molecular weight, figure 1. Partially hydrolysed grades contain residual acetate groups, which reduce the overall degree of crystallinity. This results in materials with lower strength and increased water solubility than the fully hydrolysed grades. The partially hydrolysed grades may be considered as copolymers, while those that are fully hydrolysed may be considered as homopolymers. 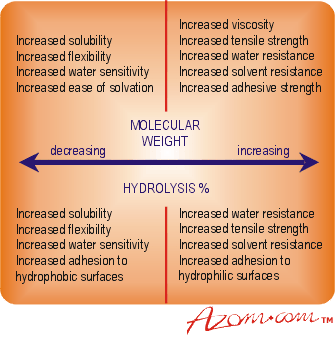 | Figure 1. The effect of molecular weight and hydrolysis level on the physical properties of PVOH. | Processing Exploitation of these remarkable properties has so far been limited, due to the difficulties in melt processing PVOH. In order to produce extruded articles with a high degree of ambient water resistance it is necessary to use fully hydrolysed grades of PVOH, and these materials are inherently more difficult to process than their partially hydrolysed counterparts due to their higher levels of crystallinity and consequent higher melting points. Temperatures of 210-220°C are needed to melt and process the polymer, which inevitably leads to thermal dehydration and eventually crosslinking. The technology developed at EPG allows the melt processing of fully hydrolysed PVOH. Plasticisers are incorporated into the polymer via a controlled process, followed by pelletisation of the compounded PVOH. The resulting pellets can then be processed on standard melt processing equipment to produce, for example, soluble PVOH hospital laundry bags. Water Resistance The water resistance of the compounded PVOH resulting from the patented EPG process is a distinct advantage over films made by the traditional solution casting process. It is normal to improve the ambient water resistance of films made using partially or fully hydrolysed PVOH by an annealing process, which increases the degree of crystallinity of the material. The resulting film products, while requiring a higher water temperature to go completely into solution, nevertheless still experience a deterioration in physical properties in contact with ambient water. In contrast, EPG PVOH films can be made to have excellent resistance to ambient water, without the need for annealing. In EPG's process the ‘wet out’ temperature (the water temperature at which a deterioration in physical properties is observed) can be effectively controlled, so that films of PVOH having excellent resistance to ambient water are now available. The fundamental chemical and physical phenomena responsible for this effect is the subject of a current research program. Biodegradability A biodegradable polymer does not generally sell simply because it is biodegradable, it must compete as a material on the basis of its own price/property characteristics, with biodegradability an added bonus. Given the above advantageous properties of the PVOH-based materials, potential markets fall into three main areas, depending upon the property to be exploited. • Applications which could make use of the controlled water solubility. These include hospital applications such as disposable infected laundry bags (which are already made from PVOH), biohazard bags, pathology sample bags, bedpans, urine bottle and vomit bowl inserts. The packaging of powders which are dust producing and are then further processed in the aqueous phase is another possibility. Examples are toxic herbicides, pesticides, dyes and pigments, where these materials are contained in a bag of cold water soluble PVOH, avoiding operator contact. • Applications making use of the barrier properties. PVOH materials can now act as a more effective replacement for the ethylene vinyl alcohol polymers currently used as oxygen barrier layers for food packaging. The resistance of PVOH to non polar organic solvents will also protect foodstuffs from secondary contamination by printing inks etc. Examples of potential food packaging uses are ketchup bottles (presently PP/EVOH/PP), and enhanced shelf life packaging. • Applications based on the biodegradability of the PVOH-based materials. A variety of applications are anticipated where the driving force is increasing pressures from environmental awareness issues, high landfill charges, legislation limiting use of landfills and non-degradable products, and the EEC Packaging and Landfill Directives. Such applications include film products made from hot water soluble PVOH, floating mulch films or transparent greenhouse/cloche films and silage wrap, pallet wrap, fertiliser bags, and general industrial and consumer packaging. Strict segregation would be necessary to prevent the biodegradable products being mixed with recyclable products such as polyethylene. A knowledge of the product origin, service life and end of life disposal method (for example dissolution in water, composting or incineration) is necessary for applications where the biodegradability of the PVOH is to be exploited. |