Mar 31 2008
Any child can tell you the difference between a good slippery dip and a bad one. They use the seat of their pants as a guide to friction, with the lowest friction offering the fastest ride and the greatest satisfaction.
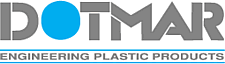
But while the fundamental equation involved may be similar, the science of the “Co-Efficient of Friction” (COF) is less obvious to many in industry for whom properly understanding a material’s slipperiness may be a vital design factor.
Knowing how to calculate COF properly is certainly essential in designing a host of materials handling and process equipment, ranging from liners for bins, trays and hoppers through to selecting the right materials for wear pads, slide bearings, support and guide wheels, conveyor rollers, tension rollers, sleeves for wheels and rollers, pulleys, cams, buffer blocks, scrapers, gear wheels, sprockets, seal rings, feed screws, starwheels and insulators.
In scientific terms, a material’s CoF is the ratio between the mass (weight) or applied load of a part and the force required to push/slide it over another surface. Force to slide = CoF x mass of part/applied load.
In the case of thermoplastics, the mating part is normally steel. The rankings below compare this "surface slipperiness" across a range of materials and are important when selecting products for use in dynamic applications.
One thing that is often ignored in assessing CoF value is the conditions under which the material will be operating. Factors such as temperature, load, speed, surface finish/roughness and counter material will affect the CoF value, sometimes quite significantly. Therefore, there is no one value of CoF for a material.
It is true that there are typical values (usually stated at room temperature and with the counter material being steel, with a surface finish of 0.8 mircons). These unqualified values can be useful where they are used to compare materials, as they are not an absolute value for a particular application under known conditions. But for a true value of CoF to be established, the conditions under which the material will be working needs to be specified – otherwise the number has little true value.
Major problems can arise when the market quotes CoF values without any such qualification, and the uninformed customer accepts these "raw" values and uses these numbers for engineering calculations.
Testing for true comparison
How do you test for a true comparison? There are various methods of testing the CoF of a material, but the most common (& accepted) method is a Pin-on-Disc test. This consists of a spinning metal disc (variable speed) with a typical surface finish of 0.8 microns, with a Pin (test specimen) that is pushed onto the spinning disc with a predetermined load. The force required to hold the pin still is the frictional force, which is then used to calculate the CoF under the test conditions.
These test conditions will vary, depending on the requirements of the test, and where the material is to be used (ie the application). It is obviously important to understand the CoF of a material where this directly relates to applications such as bushes, bearings & slide pads. The lower the CoF, the lower the force to move a part, the smoother the operation, the lower the wear of the components.
In Dotmar's field, thermoplastics, materials such as Ertalon and Ertalyte are typical materials that are used for bushes, bearings and slide pads. They are the best materials (technically and commercially) for high load, high speed applications, with temperatures less than 100 deg C.
Polystone PE is a typical materials used for wear strips, which is generally low to medium load and high speed application, with temperatures up to 60 deg C. Polystone PE also has very good abrasion resistance. (Abrasion is wear on a rough surface, where bearing type wear is wear on a smooth surface).
For high temperature applications, Advanced Engineering Plastic Products, such as PEEK & PPS are required, because they can handle the temperature, but are not necessarily lower in friction than standard engineering materials.
With a fundamental understanding of these materials’ CoF and physical attributes in service, engineers can break new ground in the design and performance of 21st Century process and materials handling equipment.